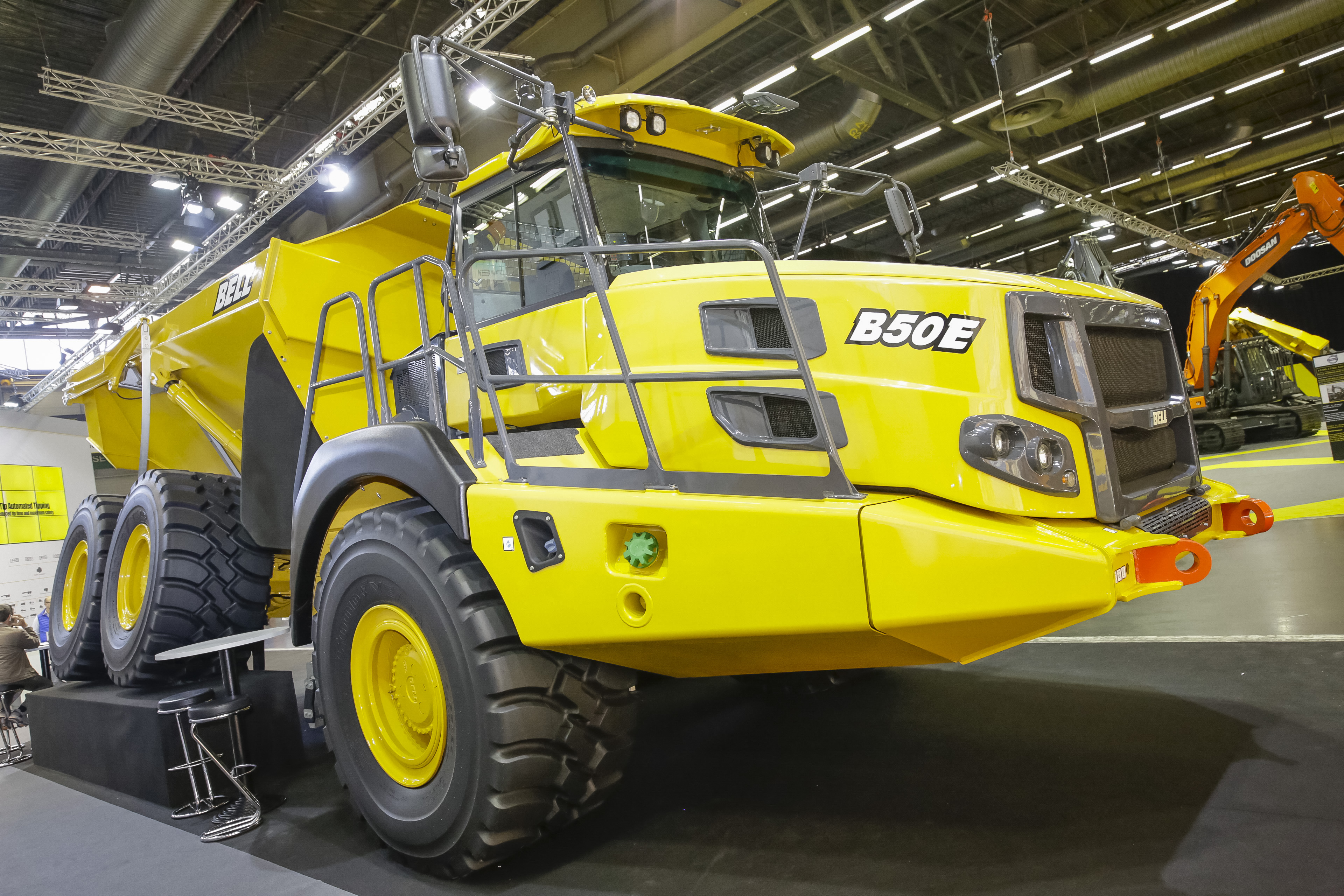
Customers of one leading dump truck manufacturer are set to receive replacement parts in ultra-quick time thanks to the opening of a new European logistics centre, while another is targeting growth thanks to renewed investment following their big money acquisition. Guy Woodford reports.
Marc Schürmann, Bell’s Europe managing director, said the new facility in Alsfeld, central Germany, will be 12,000m², compared to the current 7,000m² facility on an adjacent site.
“It’s on the cusp of two north, south, east and west autobahn crosses in Germany. The location almost right in the centre of Germany. It’s an hour’s drive from Frankfurt, so we can have a parts pick up late afternoon, get it on the plane at night, and deliver it to the customer or dealer the very next morning.
“With the changes to the E-Series, we bought additional property and aim to do a green field development of a new facility that will be ultra-modern and have all the latest technology. From that facility we hope to deliver 24 hours a day.”
Bell’s final assembly facility for the Northern Hemisphere is also only one hour’s drive from Alsfeld in Eisenach – near the former East German border.
Schürmann also said that Bell was planning to bring a 60tonne E-Series ADT onto the market by the end of next year, following the launch later in 2015 of its 50 tonne payload B50E model – a prototype of which was exhibited at
“The B50E offers a five per cent improvement on fuel efficiency than our other ADTs, due to the latest engine technology on the model. We also focus on every component to give us the best weight to performance benefit, which sets us apart from many of our competitors. We are not bound to use the in-house engine, transmission or axles.
We can go out and find the best trucking application. “We are quite proud that we do not have a diesel particulate filter in our [B50E engine] solution. It’s costly and causes a lot of headache for the operators and owners. It does burn fuel because the ADT only hauls in one direction, and it might not generate the temperatures to clean it out.”
Schürmann said Bell expect the B50E to sell well in the UK, and the firm is looking to increase its overall range sales in the large Scandinavian quarrying sector, as well as in high growth potential territories such as North Africa, Turkey and Russia.
Terex Trucks is set to benefit significantly from new thinking and investment in its production processes, dealership networks, and customer support capability.
The Motherwell, Scotlandheadquartered articulated and rigid truck manufacturer has been “refreshed” by its €123.5 million acquisition last year by Volvo Construction Equipment (
Speaking at INTERMAT about some of the key post acquisition changes, Wyant said: “We’ve had audits by the Volvo Group on our factories to see what we can do to improve their productivity; how can we learn from what the Volvo Group does. If you look at the [machine] design side, those same methodologies are being brought into place.”
Wyant explained that the ‘Volvo Production System’ being applied to Terex Trucks looked at everything from material flow in the workshop, to different techniques for welding and assembly, among other things.
“It’s inspiring the teams to look at the way they do things, and then challenging the norm to make the right improvements,” said Wyant. “The refreshing news for the people in Motherwell is that the company is investing.”
Wyant, who joined Terex Trucks on 1 January this year after nearly three years as Volvo Construction Equipment’s global road program manager based in Brussels, Belgium, said that through taking advantage of Volvo CE’s existing dealer footprint and structure, Terex Trucks was also now starting to “fill some of the white spaces” it had in that area.
As an example of the ongoing development of its dealership networks, Wyant said that Terex Trucks had signed up two new North American dealers on the first day of the exhibition. The company also planned to finalise the appointment of one new African and a new Eastern Europe-based dealer at INTERMAT.
Of the company’s aftermarket capabilities, Wyant added: “We’ve got a full field team that’s dedicated to keeping our customers’ machines running. We’ve improved parts stocking and what we do with our warehouses, and also improved the way we’re tracking machine availability.”
ADTs from Terex Trucks range from the 25tonne payload TA250 to the 38tonne payload TA400, with its 331kW engine and 23.3m³ heaped capacity. The off-highway RDTs range from the 41tonne payload TR45 to the 91tonne payload TR100. Representing the Terex Trucks line-up at INTERMAT was the TA300 and TA400 ADTs and theTR60 RDT.
Rated payload capacities for the new models are 32.7, 38, and 41tonnes respectively, with all models replacing their B Series predecessors. The new 745C’s 1.5tonne capacity increase, compared with the 740B’s capacity, is said to combine with its faster cycle times for significant production gains.
The new 740C EJ ejector model, which combines the 745C’s tractor with a horizontaldischarge body, provides added versatility and safety in certain operations. The 740C EJ can unload material to uniform depths while travelling at speed, potentially reducing the need for on-site spreading equipment, and can discharge the load with added stability in soft underfoot conditions, on side slopes and grades, and in environments where overhead obstructions are present.
The 735C’s Cat C15 ACERT engine can draw on 337kW of power, and the C18 ACERT engine in the 740C EJ and 745C has 381kW of power at its disposal.
Articulated trucks designed for sale in higher regulated territories are equipped with the Cat Clean Emissions Module (CEM). This aftertreatment system includes a diesel particulate filter that is said to be able to automatically regenerate (remove accumulated soot) without operator intervention or work cycle disruption. The fully integrated Cat CEM also includes a selective catalytic reduction system and diesel exhaust fluid (DEF) tank, with the DEF tank being easily accessed from ground level.
The new Cat CX38 High Density Power Shift transmission used in the C Series trucks has nine forward speeds, two reverse speeds, and a number of electronic features that enhance overall performance and productivity. As the new C Series trucks, with permanent six-wheel drive, encounter changing terrain and underfoot conditions, the Automatic Traction Control (ATC) feature adjusts the level of engagement for the clutch locks in the inter-axle differential and in the three axle differentials.
The system makes these adjustments while the machine is moving and does not require operator intervention. ATC maintains optimum traction for steady production, relieves the operator of manually engaging the system, saves fuel by proportionally applying the locks based on operating conditions, and does not hinder tight-manoeuvre steering.
Retarding control for the C Series models can now be set to fully automatic, in addition to manual control. In automatic mode, the machine manages retarding through a combination of engine brake, gear selection, and service-brake application without operator intervention. The automatic system is available for both forward and reverse operations, and the manual system provides two levels of engagement for more experienced operators.
Cat Connect PAYLOAD technologies for the 735C, 740C EJ, and 745C help customers optimise operations and improve overall job site efficiency. With Cat Production Measurement as an option, operators can measure and deliver accurate payloads with confidence to boost productivity, lower costs and prevent the potential for overload damage. When used with Cat Connect LINK technologies, PAYLOAD data can be accessed through the online VisionLink user interface.