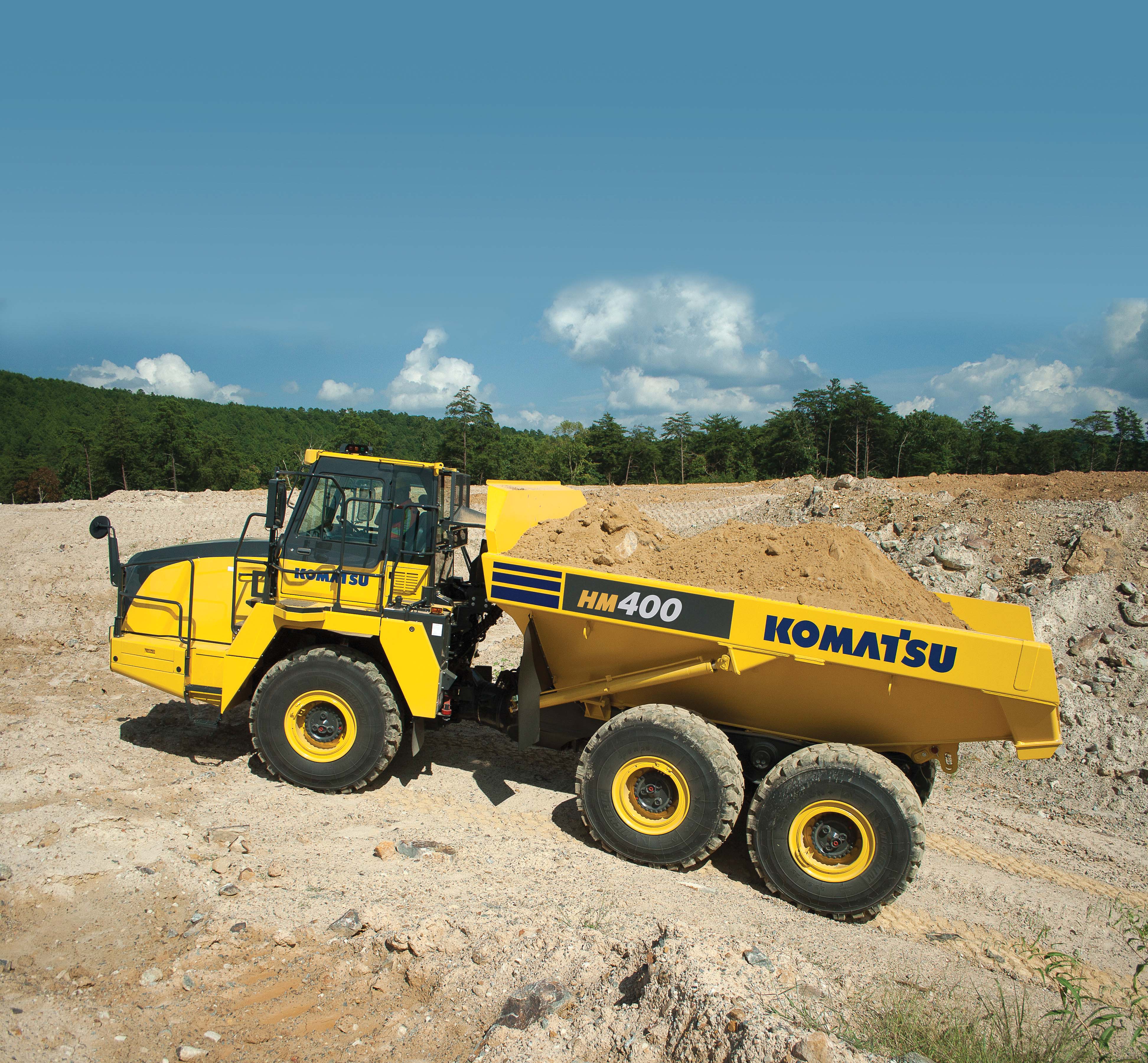
RSSA rare bird, thought to be close to extinction, is being given a chance of survival by global cement giant Cemex.
The company’s team at Dove Holes Quarry, near Buxton, County Derbyshire, central England, in partnership with the RSPB nature conservation charity, has created a five-hectare flower-rich meadow that provides seeds such as sorrel for the Twite, a bird similar to sparrows but smaller. They feed their young entirely on seed, and have declined because of a lack of such food.
Today, it is thought that there are fewer than 100 breeding pairs in England, and a tiny population in Dove Holes Quarry nest in fissures, long narrow cracks, in the quarry face.
As the teams seek a future for the birds, a long-term working relationship between
An eight-year £11 million (€15 million/US$17 million) contract sees Finning and Cemex working together with Caterpillar and Cat Finance to deliver a whole-site solution, incorporating the latest equipment, technology and quarry management expertise.
The new approach, the vision of Cemex vice president Lex Russell, is designed to deliver long-term shareholder value from the biggest Cemex quarry site in the UK.
He believes the model is a first for Cemex and the industry as a whole, saying: “It breaks a traditional mould and allows us to move the business forward with a clear competitive edge.
“We saw a real opportunity to develop a solution that delivers numerous benefits, including £1.4 million (€1.96 million/$2 million) of fuel savings. By undertaking a true partnership with Finning and Cat Finance, two businesses that we have worked with for many years, we are able to realise existing asset value, whilst developing a highly productive mobile fleet solution.”
The new managed solution was 18 months in the making, starting with an extensive analysis of the operation at Dove Holes by experts from the Finning Managed Solutions team and Caterpillar.
By combining the latest Caterpillar technology with the on-the-ground experience of the Cemex site team, Finning was able to develop a managed solution that would deliver key improvements, including a 15% increase in production and a 10% reduction in machine operating hours, in addition to practical changes to the layout of the site. A key part of the delivery of these improvements is the ongoing performance management and optimisation of new and used equipment on site that will see the overall fleet reduced in size by 6%. Even before a new fleet, including seven Cat 775G off-highway trucks was brought to site, Finning supported the transition phase with four Cat 775Ds from its own fleet, which were delivered to site six months before the new equipment arrived.
“It was important throughout the whole process that Cemex were able to maintain productivity levels and that the site was fully supported. We recognised that the ageing fleet on site would not be able to boost productivity as required, so to minimise the risk of major component failure, we made the units available, guaranteeing uptime and fleet support” says Mick Knight, business development manager for Finning Managed Solutions. With the new fleet delivered to site, Finning will be providing a fully managed solution for all of the equipment on site, including a rolling fleet replacement package that will enable the replacement of existing assets as they reach the end of their optimum life cycles.
Using the latest communications technology, fitted to new and existing equipment, the whole fleet will be monitored by Finsight engineers. This team will liaise with on site Finning engineers that form part of the Cemex team, to manage the preventative maintenance and repair programme of all Cat and competitor machinery, ensuring contractual uptime targets and efficiency gains are achieved. The Finsight team also provides Cemex with daily reports on productivity levels and machine performance, including cycle times, payloads, fuel usage and operator performance.
Neil Farmer, aggregates director at Doves Hole, says the quarry probably dates back to Roman times but historically it can be traced back to the 1650s when a census was taken, and at present it has reserves of over 300 million tonnes.
With the new fleet now fully operational, the site is set to process 4.5 million tonnes/year. Meanwhile, Caterpillar says its new 735C, 740C EJ (ejector model), and 745C ADTs build on the proven performance, reliability and durability of their B Series predecessors with significant new features. These include engines that meet US EPA Tier 4 Final/EU Stage IV emissions standards; new transmissions with expanded electronic control; automatic traction control; automatic retarder control; hill assist and waiting brake systems; and an optional payload weighing system, “all aimed at delivering lower costs per tonne by reducing cycle times, saving fuel, and easing the operator’s work load.” Rated payload capacities for the new models are 32.7tonnes, 38tonnes and 41tonnes respectively, with all models replacing their B Series predecessors.
Cat Connect PAYLOAD technologies for the 735C, 740C EJ, and 745C are said to help customers optimise operations and improve overall jobsite efficiency. (See also Equipment Focus, Weighing). In another development,
It has a maximum payload of 40tonnes and a body capacity (heaped) of 24m³ while the loading height is only 3.164mm, which enables easy and quick loading, says Komatsu. Additionally, the two single-staged body lift cylinders provide a 70° dump angle and selectable working modes allow the operator to choose between Economy and Power modes to tailor machine performance to the application or to work conditions.
The HM400-5 is powered by a Komatsu SAA6D140E-7 engine that is EU Stage IV emissions certified and with a net 353kW. By integrating Selective Catalyst Reduction (SCR), the engine further reduces NOx emissions using AdBlue, an additive which helps to converts harmful NOx from the machine’s exhaust into harmless nitrogen and steam. It also uses an advanced electronic control system to manage the airflow rate, fuel injection, combustion parameters, and after-treatment functions to optimise performance, reduce emissions, and provide advanced diagnostic capability.
“The result is lower fuel consumption with no loss of performance,” says Komatsu. “Komatsu continues to use a Komatsu Variable Geometry Turbocharger (KVGT) and an Exhaust Gas Recirculation (EGR) valve for more precise temperature and air management control as well as longer component life.”
An integrated payload meter is available as an option on the HM400-5, displaying the weight of loaded material on a LCD monitor for the truck operator, and indicating payload information to the loader operator via external display lamps.
The HM400-5 is equipped with the latest KOMTRAX remote monitoring technology with data access via the web or by KOMTRAX Mobile on a smart phone. In addition to providing data such as fuel levels, operating hours, location, cautions, and maintenance alerts, it was further enhanced to also monitor AdBlue levels and Komatsu Diesel Particulate Filter (KDPF) regeneration, and to provide fuel theft alerts.
Russia’s frigid Far East was the destination for four 91tonne TR100 rigid haulers from
Having secured the order for four TR100s, the biggest challenge for Terex Trucks was to deliver the machines.
When completed, the equipment was disassembled into kit form at the Motherwell factory and packed into crates for shipping to the Russian port of St Petersburg to start an 8,920km journey across Russia.
The kits were taken by rail for over 1,610km to Chelyabinsk and then onto Ust-Kut where they were transferred onto a fleet of special on-highway trucks (each hauler needed four trucks to transport) and taken a further 805km to ALROSA’s Udachny Mine.
Workshop facilities allowed the haulers to be reassembled and driven 300km along forest ice roads to the mine site, a journey that took four days.
Another mining project near the port of Plymouth, southern England, and repeat business wins, have seen C A Blackwell buying 12 new ADTs from
Four Bell B50Ds, the largest ADT available on the market, are joined by similar numbers of B30Es and B40Ds, bringing the number of Bell ADTs in the fleet to 39.
“It’s great that construction projects around the UK appear to be gaining impetus once more, making it a good time for us to invest in the latest ADT equipment from Bell, with the titan that is the B50D being no exception,” says David Lancashire, plant manager at C A Blackwell, who points to machine performance and cost-effiency being central to Blackwell’s continuing choice of Bell machines.
The ADTs also use Fleetm@ tic, which enables plant managers to monitor the efficiency of each machine, helping to streamline operations and maximise returns. The system, with its satellite coverage, creates automated production reports and efficiency alerts.
“We’ve relied on Bell to provide us with payload information for our ADTs for many years, and with this recent purchase, will continue to do so,” says Lancashire.
ContiTech/Volvo CE heavy-duty bushing
With heavy transportation loads and uneven terrain, components in construction vehicles have to withstand the most extreme conditions.
For several years, Volvo CE has been using elastomer bushings in this type of construction vehicle as the connecting element between the hydraulic spring strut and axle. Volvo CE approached ContiTech Vibration Control in order to substantially reduce maintenance work on this component. ContiTech Vibration Control acted as an engineering partner and assisted Volvo CE in developing a bushing with a much longer life than the component used to date.
“Our engineers faced a particular challenge in terms of the material,” says Dr Stefan Narberhaus, head of industry development at ContiTech Vibration Control.