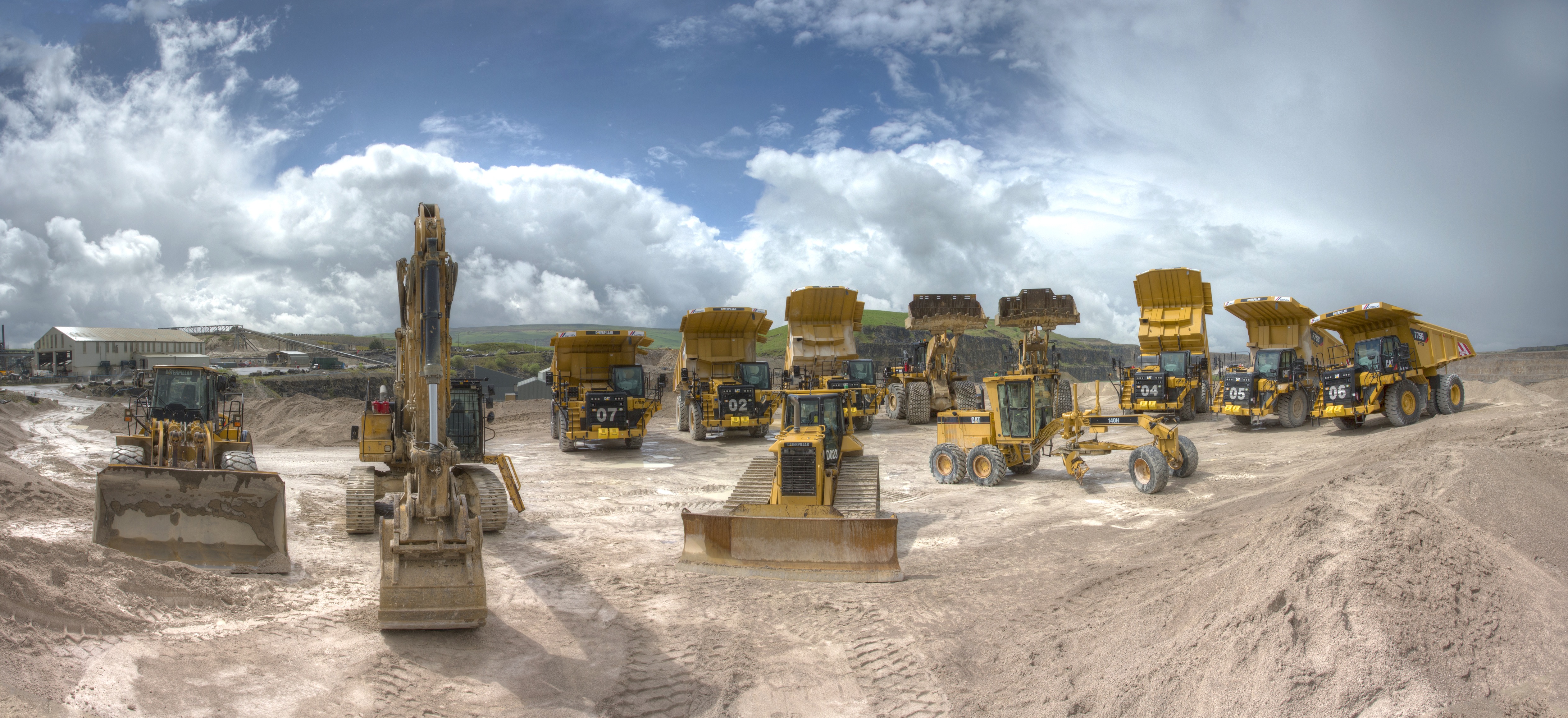
The eight-year contract will see Finning and Cemex staff work hand in hand to deliver numerous efficiency gains that will lead to a £1.4 million (€1.75 million) fuel saving over the contract period. Key improvements will include a 15% increase in production and a 10% reduction in machine operating hours, even though the fleet size has been reduced by 6%.
Supported by the newly-formed Managed Solutions team at Finning, the deal includes the complete performance management and optimisation of new and used equipment onsite. To support the contract seven new Cat 775G off highway trucks, complete with the latest technology have recently been delivered to site. The transition to the new fleet has also been supported by equipment currently owned by Finning.
In total, four Cat 775Ds were brought into the site in December 2013 as part of the deal, six months before the new fleet arrived. This ensured Cemex minimised the risk of major component failure on its aging fleet, increasing availability and boosting productivity, with guaranteed fleet support from Finning.
In addition to the new trucks, Finning will provide a total solution to support the equipment currently on site, ranging from full repair and maintenance to preventive maintenance. A rolling fleet replacement package will also enable the replacement of the existing assets as they reach the end of their optimum lifecycles.
As part of the Finning Managed Solution, specialists from the team and Caterpillar have worked with Cemex to analyse the workflow of the site, helping the team to optimise the performance of the overall quarrying operation. Highlights from this process include operational changes to the layout of the primary stocking area and haul roads using advanced
To ensure efficiency gains are achieved by these changes the fleet will be monitored by a dedicated Contract Manager, supported by the Finsight engineering team.
Together they will provide daily reports on productivity levels and machine performance, including cycle times, payloads, fuel usage and operator performance. With the Cemex operators already benefitting from the Eco-DriveTM training programme, further familiarisation and advanced training will also be made available.
This will ensure the Cemex team onsite will be running one of the UK’s most fuel efficient and productive quarry operations.
Commenting on the new venture with Finning, Cemex vice president, Lex Russell said: “With this project we saw a real opportunity to deliver longer term value to our shareholders with a solution that is set to deliver numerous benefits, including £1.4 million of fuel savings. By undertaking a true partnership with Finning and Cat Financial, two businesses that we have worked with for many years, we are able to realise existing asset value, whilst developing a highly productive mobile fleet solution.
“This model is a first for Cemex and the industry as a whole, it breaks a traditional mould and allows us to move the business forward with a clear competitive edge.”
The Finning team has developed a strategic partnership with Cemex over a number of years, sharing best practice across the business, leading up to the Dove Holes project.
Adds Neil Farmer, Aggregates Director for Dove Holes: “With this project we wanted to really push the boundaries when it came to site efficiency and performance, with a fresh set of eyes analysing the overall operation and not just the equipment. With Finning you not only get their experts, you also get access to the global experience of Caterpillar, which is invaluable. We have left no stone unturned in this process and by committing to a long-term contract with Finning, we are able to challenge them to enhance performance throughout the contract period.
“Every penny saved in every part of the process really counts in this current climate and with room to increase production built into the solution, we know we can take advantage of any upturn in the market.”
As part of the deal Finning is also committed to achieving machine uptime levels and daily reporting. This will be supported by a dedicated engineer onsite, who’s also available to support the non-Cat equipment.
Mick Knight, Business Development Manager for Finning Managed Solutions said:
“This is the first time a major site in the UK has taken such a collaborative long term approach to optimising performance with Finning, Caterpillar and Cat Financial.
Having started the process in December 2012, we have been able to manage the transition to the new setup using our customer support fleet, whilst also increasing availability and upping productivity, which is excellent.
“With the new upgraded fleet in place, the real work starts now. Through every part of the contract the Cemex team will be supported by Finning, from shared health and safety best practice, all the way down to the management of ground engaging tools. As the project moves forward we will be collecting invaluable data, capitalising on the telemetry and remote monitoring that is now available to us. Cemex’s business will be given a distinct advantage when it comes to delivering higher levels of profitability to the bottom line.”
With the new fleet now fully operational, the site is set to process 4.5 million tonnes/year/.