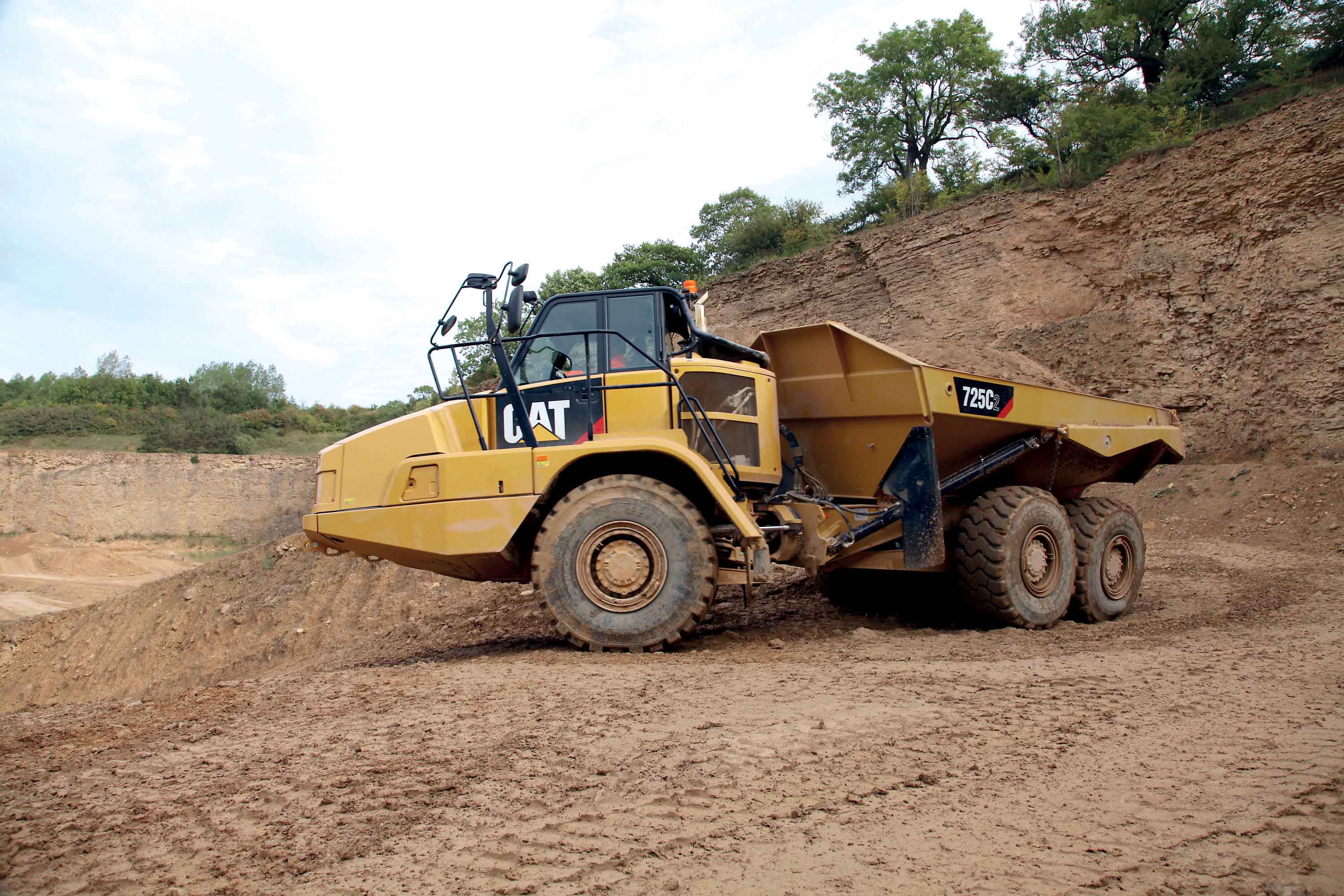
Tough machines are required for tough jobs, and for hauling equipment used for a variety of arduous tasks, this is certainly true.
Whether moving rocks, clay or earth, these rugged machines are in constant use, meaning that productivity is a key factor for owners.
In Wareham, county Dorset, southern England, near Purbeck’s Jurassic Coast, a fleet of
At
The Doreys site is operated by local family company Andrews Plant Hire and Haulage, which runs a fleet of nine Terex Trucks machines: a TA30 ADT and eight TA300s, working at six different local clay quarries.
Five machines are removing huge volumes of sandstone and bad clay excavated by the diggers, and then hauling it to another part of the site to be mostly used as backfill to restore an adjacent quarry, from which the clay has already been removed.
The trucks at the quarry each make 50-60 deliveries a day of overburden to the restoration point, adding up to between 500,000-750,000m³ of overburden and restoration materials/ year out of a total of 1.5 million m³ for all Andrews’ clients.
A few years from now, Doreys will be restored to its former rural calm, the 35m gash in the earth once again grassy farmland.
“Terex Trucks are perfect for our application. The wider-thanaverage tyres on the machines allow the wheels to float over the top of the surface, instead of just spinning and jumping when the ground is very wet,” says Peter Andrews, company owner.
In Wales, Hogan Aggregates has added two TA300 articulated haulers to its existing Terex Trucks fleet, helping to increase fuel efficiency and productivity at the company’s Coedana granite quarry, on the island of Anglesey, Wales.
The 28tonne capacity TA300s join other Terex Trucks in the quarry, and the new units will work ten-hour days, hauling blasted rock from the quarry face and transporting finished product to stockpiles around the site. Built in Terex Trucks’ Motherwell factory in Scotland, the TA300 articulated hauler, powered by
Meanwhile, Burgh Plant Hire from South Africa is the first customer to place an order for the new
Burgh Plant Hire, a longstanding customer, placed an order for three Volvo A60H articulated haulers.
Stanley van der Burgh, CEO and owner of Burgh Plant Hire, and Roger O’Callaghan, CEO of
Martin Lundstedt, CEO of the Volvo Group; Martin Weissburg, president of Volvo CE; Tomas Kuta, president of Volvo CE sales region EMEA, and Carl Zietsman, operations manager at Burgh Plant Hire, were also present.
Van der Burgh already owns at fleet of more than 100 Volvo machines for his company’s mining operations, the majority of them articulated haulers. The Volvo A60H is said to offer an impressive 40% higher payload than the company’s previous largest articulated hauler, the A40G.
Engines in all three models are available that meet or are equivalent to world emission standards: US EPA Tier 2/EU Stage II, Tier 3/Stage IIIA, or Tier 4 Final/Stage IV.
A diesel particulate filter and selective catalytic reduction system provide exhaust aftertreatment for Tier 4 Final/Stage IV models.
“The spacious two-person cab features a multi adjustable air suspension seat for the operator; a full size, forward facing seat for the trainer; tilting/telescopic steering wheel, and convenient wrap- around dash. A multipurpose colour display provides pertinent operating information, as well as the feed from the rearview camera when activated,” says Caterpillar.
Introduced as a concept in 2013, the B60D is said to have has proven itself as a solution capable of moving large volumes of material in all weather conditions, in a market segment that was previously only contested by rigid trucks.
The 60tonne B60E is the next generation, a 4x4 with full articulation steering and oscillation joint, which keeps all four wheels on the ground and fully utilises the traction available, meaning it has more off-road capability than any other conventional rigid truck.
“With its four-wheel drive and ability, through the incorporation of an independent front and rear chassis, to keep its wheels on the ground, the B60E is ideal for a number of specific applications,” says Nick Learoyd, managing director of Bell Equipment.
“The tighter turning circle of the B60E and its ability to negotiate steeper ramps are also significant advantages over its rigid truck counterparts.”
Advanced Bell ADT technology, with the original B50E front chassis now powered by a EU4/ Tier 4 Final certified 430kW Mercedes-Benz/
Two new Doosan DA30 30onne ADTs have been hired with drivers from Total Plant Hire, based in Manchester, north-west England, for work on the new Mersey Gateway Bridge across the River Mersey, Liverpool.
The specially-shaped body and sloping frame on the DA30 offers a low centre of gravity and perfect weight distribution. Combined with the free-swinging tandem, the DA30 offers low ground bearing pressure.
“We purchased the new