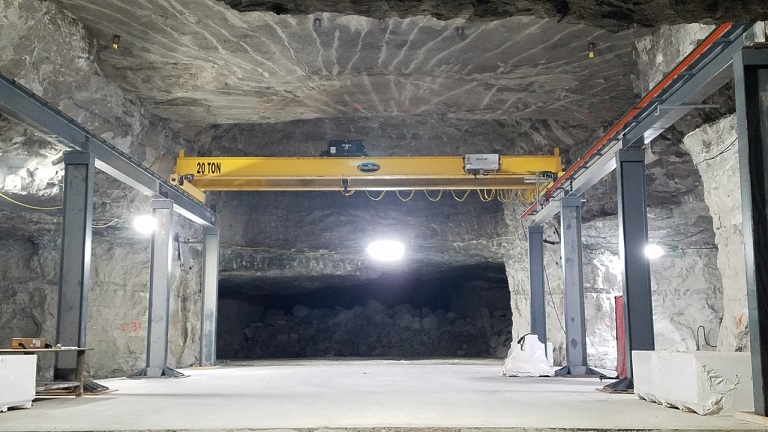
The crane and hoist – sold by Harriman Material Handling – was installed by CraneWerks 400 ft beneath the surface at US Gypsum Shoals Mine.
CraneWerks is a distributor for R&M components, which builds cranes that are sold through distributors across the US.
The top running double girder crane is being used to assemble and maintain equipment for the mine underground. It spans 35 ft and travels on a 62 ft long runway.
During the case study, challenges were encountered on the surface and below ground.
For example, the shaft used to get equipment into the mine was much smaller than most of the machinery used below. A 35 ft bridge beam was too long to go down the shaft in one piece.
US Gypsum says: “Being underground is its own challenge. Everything from pouring concrete to lifting the beams is difficult because you don’t have access to a lot of the equipment you would normally think of using. It’s constant problem solving.”
CraneWerks designed a bridge that was built in two pieces so it could fit down the narrow mine shaft before it was welded together at the bottom.
The crane provides a lifting solution on a daily basis, raising mobile equipment components, weighing approximately 10 tonnes around the area. US Gypsum explains that loads are normally large pieces of fabricated steel components of a larger machine.
“We have trained around ten people on how to use the crane. About four or five of them use it on a daily basis,” US Gypsum adds.
A top running crane was chosen because it offers the same hook height as a single girder crane, which would require a higher ceiling.
The height available is described within the case study as important because the hoist and trolley ride on top of the bridge girders rather than being suspended beneath the bridge girder. This gives the best hook height of any overhead bridge crane option, giving users the maximum amount of lift (distance that the hook can be raised above the floor below) available.
“We needed a crane capable of moving large pieces around for assembly of equipment in the mine, and the results suggest we found a solution,” US Gypsum continues. “We could have acquired a few telehandlers that had the necessary weight capacities, but the EOT (electric overhead travelling) crane was the preferred option.”
The crane has been installed at the south end of the mine. The plan is to relocate the site’s maintenance facility to this location in the future.