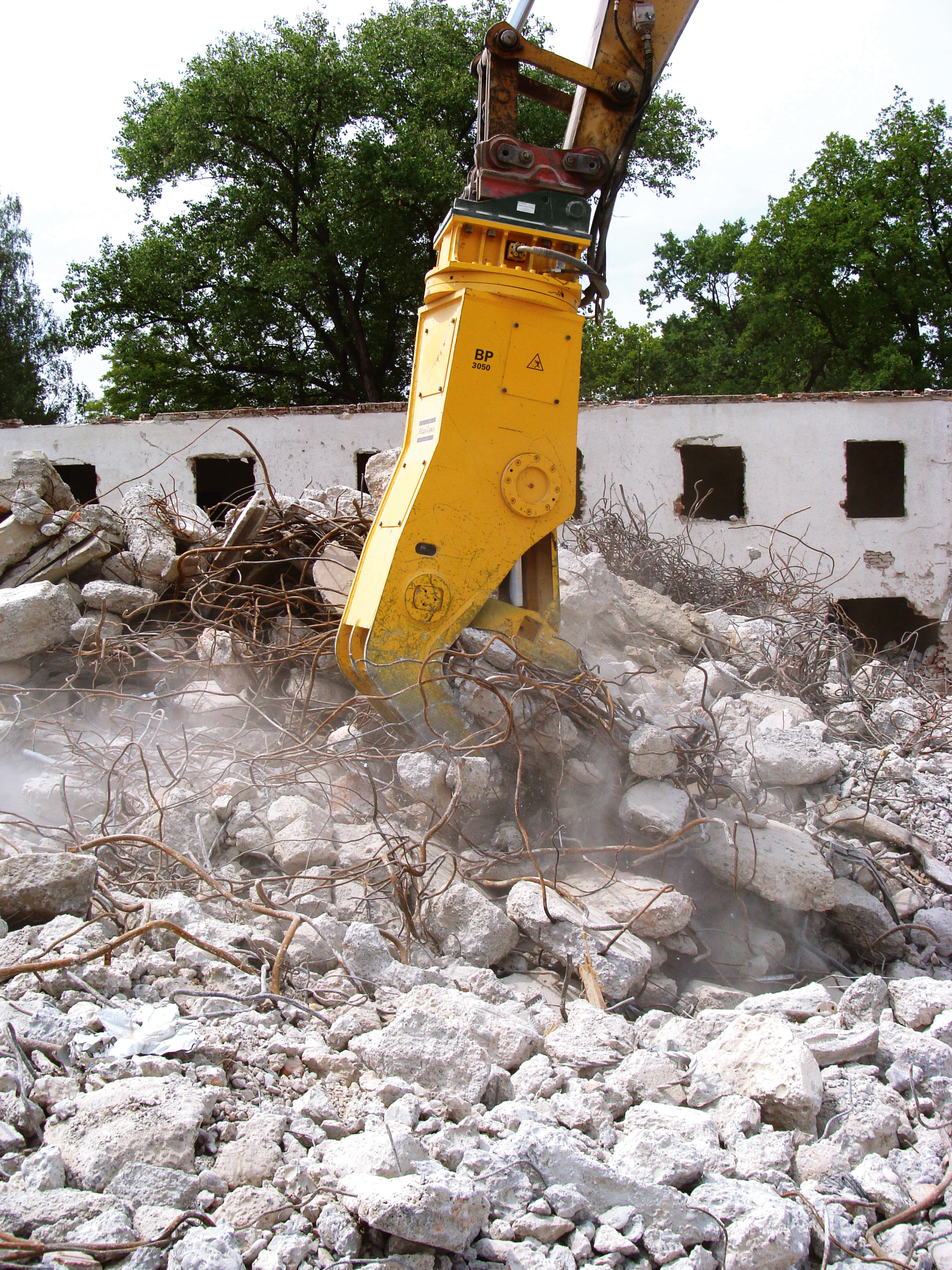
Recycling old concrete has never been easier or more cost-effective as Patrick Smith reports
Recycling is now a common method of utilising the rubble produced when structures made of concrete are demolished or renovated.
Rather than truck the old material to landfill sites, advances in equipment over the years coupled with greater environmental awareness, more environmental laws, and the desire to keep construction costs down, has made recycling an attractive proposition.
Indeed, a considerable amount of recycled/secondary aggregate was used in the construction of the Olympic Park in London.
According to reports, an initial estimate of concrete use on the Olympic Park indicated a requirement for 500,000m³ of ready-mixed concrete and an equivalent aggregate requirement of 1million tonnes.
In a report on the procurement and use of sustainable concrete on the Olympic Park, Kirsten Henson, a director of KLH Sustainability (sustainability advisor to main contractor CLM), says: “Concrete has a high environmental impact and therefore improving the sustainability of the concrete was a key focus for the Olympic Delivery Authority (ODA).
The combination of a tight construction programme, the importance of a reliable supply and the opportunity to maximise the sustainability credentials, led to the procurement of a single ready-mix concrete batching plant to provide concrete to all projects on the Park.
“The ODA worked with the concrete supplier and engaged with the supply chain to develop sustainable concrete mixes. This resulted in the use of approximately 170,000tonnes (almost 22%) of recycled and secondary aggregate, a saving of approximately 30,000tonnes (24%) of embodied carbon and elimination of over 70,000 road vehicle movements.”
Apart from the ‘green’ benefits, reusing concrete from a demolition project offers considerable savings in the cost of transporting it to the landfill and eliminates the cost of disposal.
Major crushing and screening equipment manufacturers now offer machines to handle concrete aggregate collected from (or processed at) demolition sites.
Recycling of concrete pavement is a relatively simple process involving breaking, removing and crushing concrete into a material with a specified size and quality, and there are few, if any, restrictions on the types of concrete pavements that can be recycled. Metals such as rebar can be removed with magnets and other sorting equipment supplied with or part of the machine.
Large plants can crush concrete and asphalt rubble at more than 600tonnes/hour, while compact, self-contained mini-crushers are available to fit into small areas.
Crusher attachments from companies such as Italian company
Recycled concrete can be reused as an aggregate in new concrete (usually combined with a virgin aggregate) although it is more commonly used as aggregate in a sub-base layer.
In a report, the
“In construction the readiness to recycle differs remarkably in Europe. In Austria, Denmark, Germany and the Netherlands a recycling quota of more than 70% was stated. However, potentials are still available in the remaining European states.
“Altogether approximately two-thirds of the waste is produced in the fields of construction, demolition, mining and extraction of stones and earths. This waste consists predominantly of mineral waste.
“The fields of application of recycled building materials are wide-ranging. So far recycled building materials have been used in the construction of roads, road foundations and sports grounds, for noise protection walls, earth banks and in landscape construction. They are also increasingly used as aggregates in the concrete and stone production.”
It notes that the success story in the field of quality-assured recycling of building materials shows a high marketability of these products as compared to natural stones in many European countries such as Austria, Germany, Italy, the Netherlands, Czech Republic and Switzerland. “This is proved by their rising acceptance and demand by clients and authorities,” says EQAR.