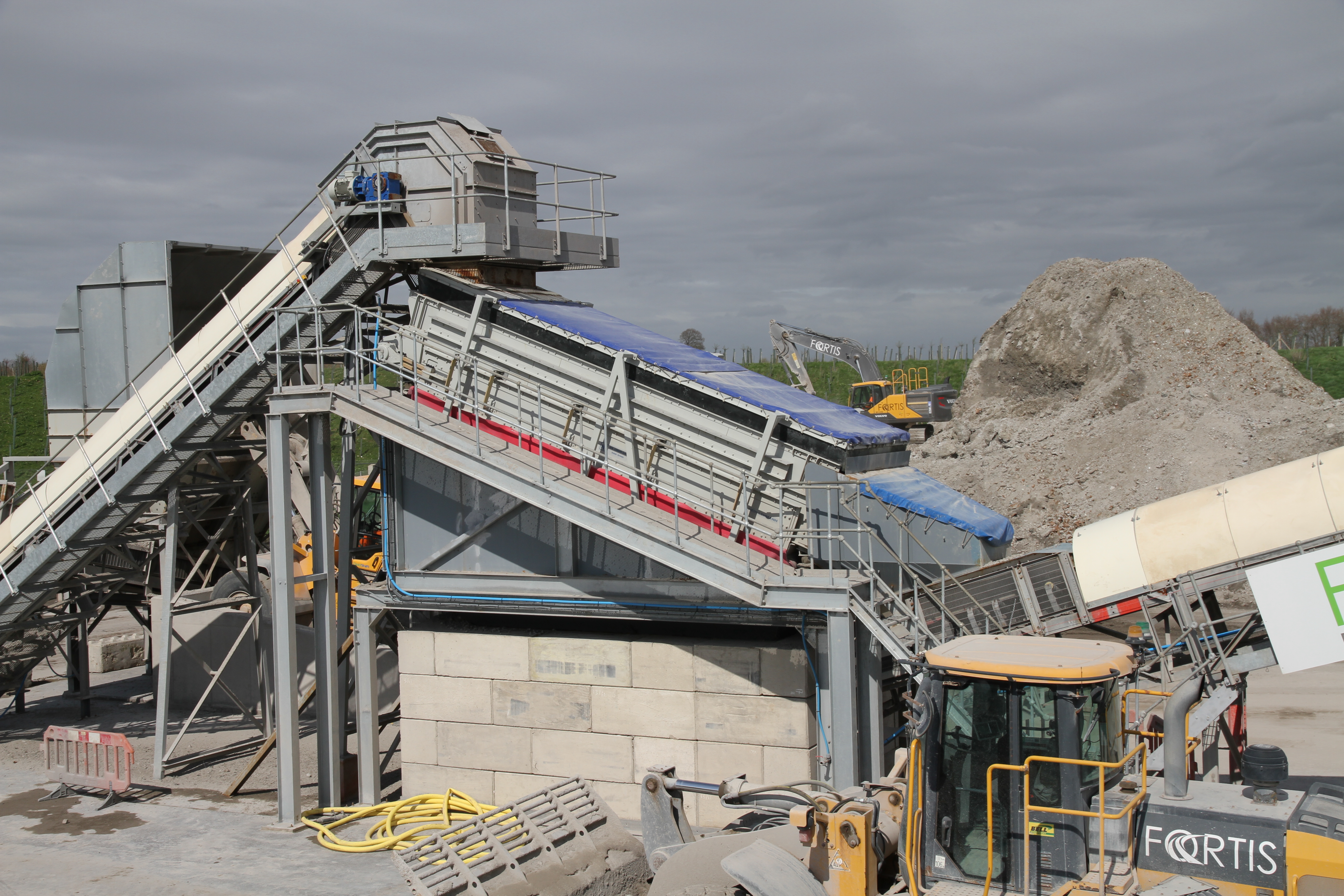
The facility currently processes 120,000tonnes of IBA (incinerator bottom ash) from energy from waste facilities each year, transforming the ash into a sustainable recycled aggregate which is used in construction projects.
Fortis resourced the project internally, undertaking extensive research within the European materials separation technology markets prior to the investment.
It was critical to ensure that the investment would significantly increase metallic extraction rates and improve processing efficiencies, while enhancing the engineering properties of the final IBA aggregate products.
A series of trials were carried out using different screening and separation solutions from the UK and Europe. After a lengthy evaluation process, Tema (Machinery) was selected to carry out further detailed trials at the A303 IBA facility using its mobile version of the Liwell screener.
The Fortis team was subsequently invited to the Liwell factory in Germany to negotiate and agree final specifications.
Supplied by Tema (Machinery), which is based at Woodford Halse, near Daventry, county Northamptonshire, England, the Liwell 2m x 6m double deck Flip Flow screening machine (model LF2.0-5.76/18DD) was the installed at the Fortis site.
The investment in the Liwell Flip Flow Screener followed extensive on site testing with the Hein Lehmann test facility with the design and build contract awarded to European Active Projects of Southampton, southern England.
The Liwell screen is said to be the first ever Flip Flow screen, and was invented by Hein Lehmann some 45 years ago. The Liwell principle ensures the mat is subject to at least 50gs acceleration, yet the screen itself is under very little stress, in fact just over 2g when operating.
“We are continually looking at new ways of developing our processes to improve our metallic recovery rates and overall processing efficiencies,” says Terry Moore, general operations manager, Fortis IBA.
“We produce high-quality IBA aggregates and the introduction of the Liwell screen has refined our processes further.
“Successfully separating smaller IBA fractions improves recovery rates and reduces maintenance and downtime. We are delighted with the performance of the Liwell screen and are achieving the anticipated improvements in recovery and efficiency.”
Hein Lehmann and Tema (Machinery) are sister companies within the wider Steinhaus Group of companies, and Temad look after the interests of Hein Lehmann and the Liwell screen along with Siebtechnik in the UK and Ireland.