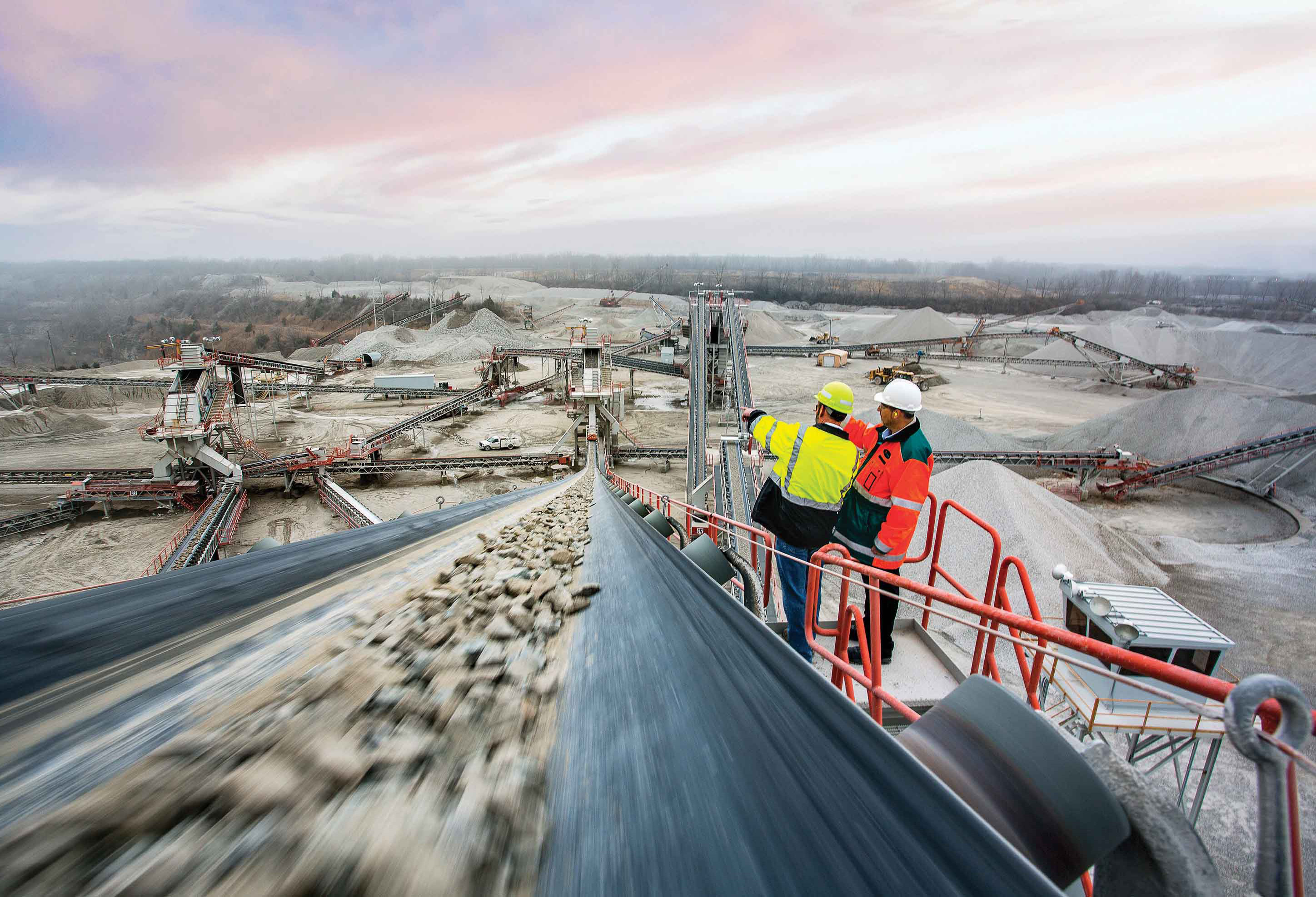
At bauma 2016 in Munich, many leading crushing and screening OEMs were due to unveil new models or showcase proven existing solutions. Patrick Smith and Guy Woodford look at some of the best.
There will be some big screen stars at the
Oliver Donnelly, the Northern Ireland-headquartered crushing and screening giant’s product manager, said the Warrior 1400XE showed the company’s response to customer demand, alongside its commitment to embracing a more environmentally aware approach to innovation.
“This latest development utilises a combination of highly efficient electrical components and clever design to deliver the lowest possible cost for every tonne of material processed through the machine,” he continued. “While we are excited about the low running costs, we are proud to have produced a machine where customers will also quickly see dramatic savings in the costs associated with maintenance and servicing. Versatility has definitely not been compromised.”
The Warrior 1400XE has been designed to meet the needs of customers for whom electricity is a preferred power source and opens up the possibility to run the machine indoors. It can be powered by electricity generated by other Powerscreen models (such as the Premiertrak 600 jaw crusher). The Warrior 1400XE builds on the success of the standard Warrior 1400X model with its single shaft, high amplitude 3.6m x 1.25m screenbox and the chassis riser option giving excellent stockpiling capacity. It also has several important service and maintenance features including the Powerscreen ‘Stay-Clean’ system under the feeder and a jack-up screen system allowing easy access for screen media changes. Depending on feed material, the output capacity for the model is up to an impressive 500tonnes/hour.
The crucial advantage of the Warrior 1400XE is the variety of power options available. It can be self-powered with its own 72kVA generator, or be connected to a mains electricity supply for even further reductions in cost of ownership. For customers who understand the advantages of a packaged solution, the Warrior 1400XE can also be powered from an electric drive crusher with a barely noticeable effect on the crusher fuel consumption. This has the added benefit of eliminating the engine maintenance on the Warrior. Similarly in regions of the world where there is a need to operate in high altitude or in high ambient temperatures, the Warrior 1400XE can be powered as part of a machine train from a single gen-set which can be oversized to handle any de-rating caused by the operating environment.
Powerscreen stress there are many other scenarios where the Warrior 1400XE can be seen as the right solution. For example, the Warrior 1400XE is more suited to running indoors than a conventional diesel-hydraulic machine. The machine’s extremely low noise levels will also be advantageous in many circumstances.
Meanwhile,
The specially adapted BIVITEC technology from Austrian development partner Binder + Co, in combination with the large screening surfaces of the double screening unit (2 x 6,000mm x 1,900mm) and a broad area of application in the recycling of various waste materials, is said to guarantee the processing of materials difficult to screen that have high basic moisture llevels, or in the production of large volumes of standard mineral products up to 600tonnes/hour.
“By providing different versions of the double screening it is possible to process, for example, minimum grain sizes of < 2mm efficiently,” says Keestrack. “If the linings in the upperdeck circular vibratory screen are changed, the unit can also be directly deployed behind a crusher or for the processing of hot materials such as slag or substances containing tar.”
The transport weight of the unit is 45.4tonnes (B x H during transport: 3.2m x 3.6m) including the 12m³ feed hopper, overband magnet (option) and two side belts. According to Keestrack, the rapid on-site set-up times make even shorter-term constructionsite deployments of the machine worthwhile.
A number of new cone and impact crusher solutions on show at bauma 2016 are likely to catch the eye of customers looking for highly efficient and productive models.
Many will be keen to see what Finnish crushing and screening giant Metso has to offer at the big Munich exhibition.
The company’s renewed mobile Lokotrack LT1213S impactor plant; the popular Lokotrack LT96 jaw plant; the maintenance-friendly threedeck PREMIER ES303 horizontal screen; new stationary plant solutions; truck lining solutions and proven pumps, are part of the company’s exhibit.
“Bauma offers us a great possibility to present the
With the goal of helping customers reach their lowest sustainable cost structure, Metso’s new Life Cycle Services (LCS) packages are tailored to the aggregates industry.
The LCS offering is designed to support Metso equipment and wear and spare parts in order to ensure the most profitable operations in aggregates production.
“We have built our new Aggregates Life Cycle Services offering so that our customers can easily select the solution they need to best meet their business goals,” says Giuseppe Campanelli, vice president of Metso’s Life Cycle Services business unit.
“This includes providing new ways of buying, maintaining and operating equipment. “Though we have had LCS aggregates contracts in certain regional markets, the new packages have been structured so that they are easier to understand and customise as needed, making them more accessible to the rest of our global client base. Metso successfully supports the mining sector with the LCS concept, and we believe there is a good demand for it in the aggregates customer segment as well. With this new offering, our customers are able to streamline their operations and further reduce the total cost of ownership.”
The bauma 2016 global première of
The cone crusher, driven by a powerful and low-consumption diesel-electric drive, enables operation with an external power supply, and it has a maximum feed capacity of up to 470tonnes/hour.
Equipped with the innovative CFS (Continuous Feed System), which ensures a productive crusher feed, the MCO 11 PRO is also ideally suited for operation in inter-linked combinations of plants.
Kleemann says the plant can be transported in one piece and can be quickly put into operation thanks to hydraulic machine components.
Terex Finlay’s new I-140 direct drive 1,270mm x 1,240mm horizontal impact crusher offers variable speed for production in recycling, mining and quarrying applications.
A significant engineering approach being introduced in this model, which will be on show in Munich, is the material flow through the plant. The flow of material has been significantly improved by increasing the width of components as the material moves through the machine, says Terex Finlay.
The I-140’s robust and proven
Material from the integrated pre-screen can be diverted to a stockpile via the optional bypass conveyor, or it may join the crushed product on the main belt. The standard hopper capacity is 6m³.
“The introduction of the
“The enhanced material flow process of the plant represents a significant change to our engineering ethos and in due course will be extended to encompass our range of impact crushers.”
A fully hydraulic apron setting assist provides convenient and efficient adjustment of the aprons while an optional under crusher vibratory plate feeder with wear resistant liners aids material discharge flow. Remaining with impact crushers,
“Although the new machine shortens the traditional process chain it can produce a final product with even higher quality,” says SBM.
“Secondary and tertiary crushing of natural stones for the recycling and asphalt industry are the main application areas of this intelligent SMR crushing system impressing clients with both performance and perfect process results.”
With a crusher width of 700mm, material with a feed size of up to 200mm can be fed to the crusher.
SBM says this innovation saves one crushing step due to the fact that the fine impact crusher SMR can process the material directly after the primary crushing step, for example a jaw crusher.
The cubic grain form required for further processing is produced in the desired grain size at a percentage of more than 90% high-value aggregates in the final product.
This is achieved by a frequency converter for constant rotor speeds that can be readjusted easily and quickly. With a drive performance of 160kW maximum, the sturdy power package offers a maximum average crushing capacity of 150tonnes/hour.
“Until now high-grade chippings, for example asphalt surfaces, have been produced by using an impact mill and an additional cone crusher, which always meant a product with an inadequate cubicity. Just by itself the new SMR is capable of processing every cheap, inferior grain size material to refined chippings thus contributing to achieve especially economic and high-quality final processing,” says SBM.
MB Crusher’s newly upgraded and renovated third generation BF units were being officially launched at bauma 2016. The models were set to be on display and working in the Munich event’s demo area. The new state-of-the-art BF units follow the hugely successful first two generation units.
Designed for all excavators, the new generation BF crusher buckets are now said to be even more compact with better balance in the collection phase.
The crusher’s mouth has been further expanded, increasing the crushing surface and, consequently, the productivity. With the dust suppression system, the iron separator and low noise impact, the BF units can be easily used in any construction site, even in residential areas and within total compliance with environmental regulations.
MB Crusher claims its buckets are the only ones in the world that do not need drainage, while also, the north-east Italy-based company says, ensuring higher productivity compared to countless imitations of the original BF unit. MB’s crushing power exceeds 110m3/hour, thanks to an exclusive power enhancer which enables the crushing of the toughest materials including basalt and granite. The BF units are also said to deliver a high quality, competitively priced product, in compliance with the high-quality, standards required for waste material reuse.
A further new product from
Ideal for natural material selection, pre- and post-crushing, the new screening bucket MB-LS170 is said to reduce crushing time by up to 60%, while still ensuring a high-quality end product.
The MB-LS170 has many application areas, such as the primary selection of waste material, demolition, excavation filling and the reclaiming of rocky ground, pebble selection, beach cleaning and all other instances where thinner pieces are needed. The new MB-LS 170 is said to be a “real jewel of mechanics”, lightweight (around 0.45tonnes), compact (dimensions 1420 x 1380mm x H=875) with a loading capacity of 0.50m3.
MB Crusher says it is the only manufacturer in the world able to offer a complete range of 18 crushing and screening buckets - for excavators, wheeled loaders, skid steer loaders and backhoes - from 2.8tonnes to over 70tonnes with a 24-month warranty.