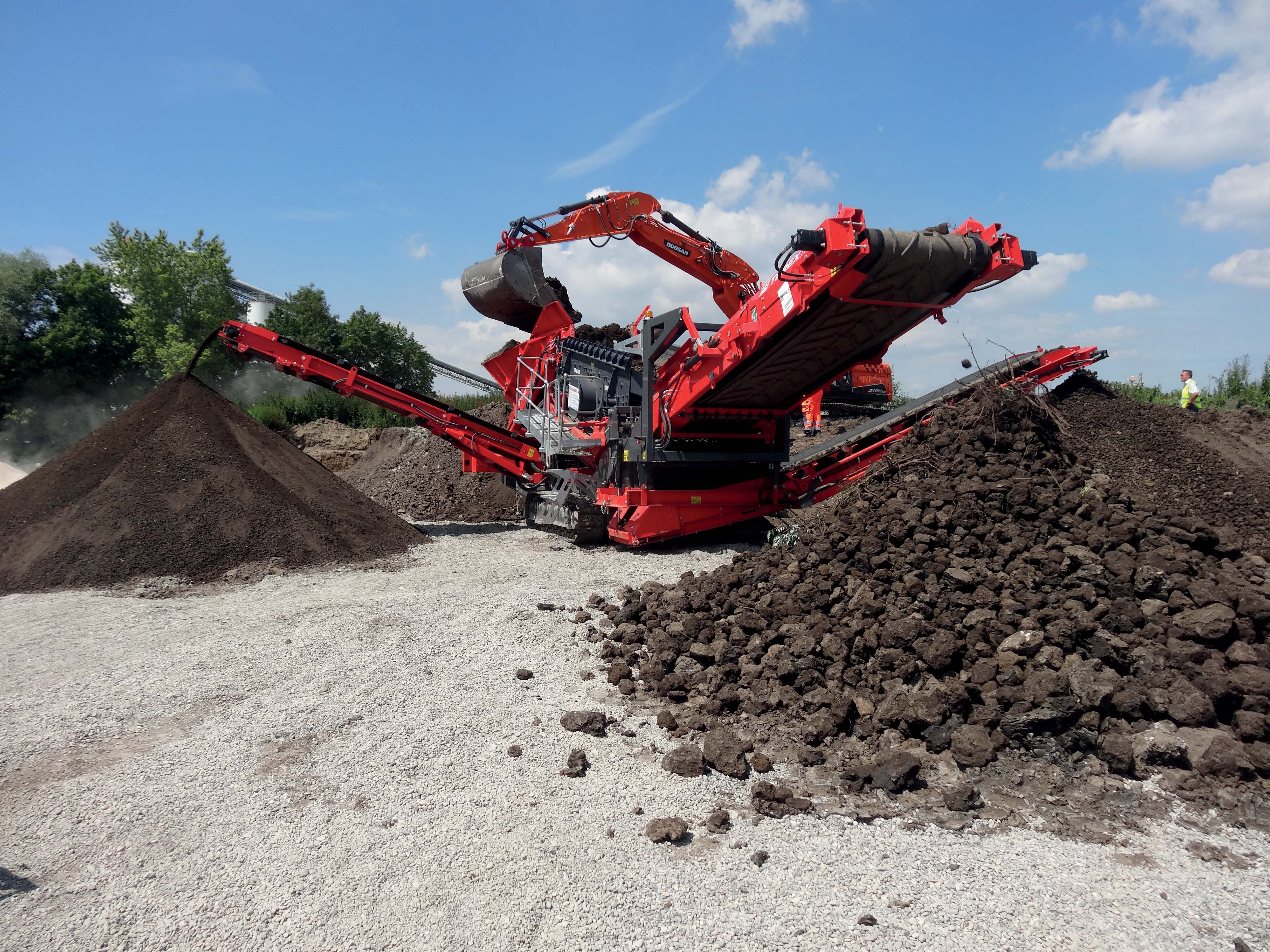
Two leading crushing and screening OEMs have been showcasing new models to European customers, while another is doing great business in South Korea. Guy Woodford reports.
Stars of the show at the 28-29 May 2015 showpiece were the Premiertrak 600 jaw crusher, which received its global launch and featured the firm’s new telematics software, and the Chieftain 2200 screen, previewed for the first time in Europe ahead of its launch later this year.
Other new Powerscreen models on show at the
The productivity requirements of customers coupled with high expectations are said to have fuelled the development of the Powerscreen Premiertrak 600 jaw crusher and its two possible configurations: diesel-hydraulic and diesel-electric. Both versions are designed and constructed to deliver maximum production and performance with minimum downtime and running costs. The diesel-electric machine can be powered directly from an on-site source which further reduces operation costs.
“The Premiertrak 600 is the first diesel-electric drive crusher that we’ve introduced into our range,” says Oliver Donnelly, Powerscreen product manager. “We have some other exciting development activities underway which will deliver products that complement the Premiertrak 600 and broaden our customer offering. Our focus is to increase efficiency, reduce the environmental impact, and ultimately deliver a lower cost of ownership to the end user.”
The move towards all-electric driven crushers is also becoming a necessity to meet tough new quarrying environmental legislation in some regions, including parts of Scandinavia.
“For example, our Swedish dealer commented that for a lot of new quarry permissions one of the stipulations is that the mobile crushing models should be electrically driven,” says Donnelly.
At the heart of the Premiertrak 600 crusher is a 1200mm x 820mm robustly built, modern jaw chamber with many user-friendly features including a fully hydraulic CSS range of 75mm-200mm and a reversing system to quickly clear blockages for increased uptime. The aggressive stroke and high inertia flywheels are said to offer high production rates and excellent reduction ratios. For speed and safety purposes, the Premiertrak 600 crusher can be fully set-up from ground level due to its hydraulic folding and locking hopper system, in combination with the hydraulically lowering product conveyor. Like all other products in Powerscreen’s mobile jaw crushing range, the Premiertrak 600 has an array of options which are said to be configurable for all application types.
Donnelly adds: “We went to great lengths on the jaw chamber to make sure we’d oversized bearings and all the critical components, so that we’re out there a hundred per cent confident we can put the machine into the hardest of applications, the hardest of stones in any quarry, and the performance and productivity will be there.”
Donnelly says that the Premiertrak 600 had a strong prelaunch order book, and was very well suited to the needs of customers in markets such as Europe, the US, Canada, South Africa, and Australia, and he’s also expecting it to appeal to Latin American customers.
The Powerscreen Chieftain 2200 screen is the first in the Chieftain range to feature two screenboxes and is said to deliver great performance, including meeting the tightest aggregate specs.
“Our Chieftain 1400 has a four-bearing drive system on the screenbox, whereas typically the rest of the range operates on a two-bearing drive system. Some time ago market feedback suggested there’s a significant market for a bigger screenbox utilising the four-bearing drive system. We said ‘Okay, we can go and do that’. But as the conversations developed we said, ‘Why don’t we evolve the concept to have two screenboxes on one chassis with the four-bearing drive system, which could be designed in such a way to make it easily convertible from a four-bearing to a two-bearing system?’ That’s what we’ve done and conversion capability is patent pending,” explains Donnelly. “This means that customers are getting the best of both: they have the four-bearing drive system but can easily convert to the two-bearing drive system. And because there are two screenboxes, they can have a combination of both. For example, a two-bearing system could be on the first screenbox for productivity, and the four-bearing system on the other could deliver efficiency and a high specification product. It gives a lot of flexibility to cover a great breadth of applications.”
Donnelly says that the Chieftain 2200 screen impressively offers up to 20% more productivity than the comparable Chieftain 2100X, which has an up to 600tonnes/hour capability. It’s also available in two-deck or three-deck form.
Opportunities provided by the demand for enhanced plant automation, the production of fine materials and artificial sand manufacturing, have seen
Sandvik Construction (Sandvik) stationary crushing equipment is said to be engineered for maximum productivity, offering advanced customer focused solutions for any material size reduction. In addition an extended offering includes such items as wear parts, extended warranty and retrofits, with a focus on customers’ productivity and profitability. These are all enhanced by Sandvik’s comprehensive knowledge of customers’ raw materials, supported by an in-house laboratory, with a full-scale test plant, which enables Sandvik to deliver plant-crusher optimisation audits at the customers’ own site. Recently this customer focused approach is said to have been warmly embraced by two South Korean companies, who have both used Sandvik crushing equipment in rather unusual applications.
In recent years some of South Korea’s leading aggregates producers have started to invest in Sandvik crushing equipment. One such company is Wooryung, which is using a recently acquired CH430 cone crusher to produce a 30mm product from a -150mm feed material. The CH430 is located at the company’s site at YoungWol, in KangWon province, with the crushed limestone being supplied to a steel company after desulphurisation. The use of the CH430 is seen as a way of using the best equipment to produce an end product of the highest quality. Due to Wooryung’s customer’s requirement it was decided that if the best possible product was to be produced then the very best cone crushers should be used.
Sandvik cone crushers, such as the CH430, combine high capacity operation with high reduction efficiency. With hydraulically adjusted CSS and automatic wear compensation, a choice of different crushing chambers and eccentric throws, plus many other high performance features, helps to ensure each model is versatile, user-friendly and highly productive. All Sandvik cone crushers are optimised by 3D CAD and Finite Element Analysis (FEA). Each model is tested ‘virtually’ for stress, strain, shock, deformation, thermal loading, vibration and noise under a wide range of load conditions, with the end result being exceptional reliability.
Sandvik VSI crushers have been developed for the tertiary and quarternary crushing of abrasive rocks, with the design of the working principle of these innovative crushers encouraging material to break along natural cleavage planes, thus producing stress-free, cubical shaped products. This means that the VSIs’ development ensures that product shape and size are consistent, but the innovative nature of the design also produces reduced power consumption, increased capacities, reduced maintenance costs, and vitally, requires fewer maintenance services.
Introduced in 2002, Sandvik’s line of autogenous crushers, of which the CV229 is one of the more recent developments, utilises a rock lined rotor to accelerate material. This is then impacted in a highly energised rock lined crushing chamber and it impacts with material falling through the biflow system. The crushers incorporate the Sandvik Hurricane rotor, which became a major breakthrough in VSI autogenous rotor design due to its decreased vibration levels and wear part design, which results in increased crusher bearing life combined with reduced maintenance. Standard Sandvik VSI crushers are fitted with a timed trapped two key system, which ensures the safety of maintenance personnel combined with electrical isolation. Also supplied and fitted as standard, are a vibration detection switch and a pre-start alarm siren.
These features have been particularly useful to one such South Korean company as a shortage of sand in its natural form has presented Bokwang with the opportunity to use its existing aggregates to help satisfy the needs of the Korean construction industry. This is achieved through not only being able to supply a manufactured sand product, but also by being able to improve on the naturally occurring sand. How this is accomplished is due to manufactured sand possessing significant benefits over the naturally occurring form, as it originates directly from high quality virgin rock, and thus contains very few, if any, contaminants that are found in naturally occurring sand.
There are also significant advantages to be gained from the cubical shape of the end product produced during manufacture, which further provides advantages during cement manufacture, and benefits the construction industry as a whole. Hence the Sandvik CV229 is now proving its qualities by producing sand from aggregate with Bokwang using the VSI at its site in KwangJoo, KyungGi province. The -35mm aggregate is fed into the CV229 to produce a finished product of -5mm, which is then used as sand.
Among the models on show, and making its German event debut, was the new J-1170AS primary mobile jaw crusher. The model’s 1100mm x 700mm jaw chamber is said to provide excellent material reduction and product sizing in the processing of blasted quarry rock and ore material. The jaw chamber is also available with optional hydraulic release, an excellent feature when crushing construction and demolition debris. The hydraulic release option has an automatic overload protection system to prevent damage by uncrushable items in the feed material.
The machine is powered by either a Tier 4F
Hydrostatic transmission of the jaw chamber offers operators reversible operation in the event of a blockage. The hydrostatic system also provides variable chamber speed to suit given applications. The crusher features hydraulic assist Chamber CSS (Closed Side Setting) adjustment, and can be changed in a matter of minutes.
The machine has a heavy-duty variable speed vibrating grizzly feeder (VGF) with integrated pre-screen, providing an aggressive action to separate fines material efficiently. The variable speed VGF ensures continuous choke feeding of the crushing chamber for optimal productivity. Material from the pre-screen can be diverted to a stock pile via the onboard bypass conveyor, or join the crushed product on the main belt.
The J-1170AS’s large 9.6m³ hopper has hydraulically folding sides and an innovative hydraulic self-locking mechanism to provide efficient and faster machine set up and tear down times.
The new Terex Finlay I-140 direct drive 1270mm x 1240mm horizontal impact crusher gives operators high levels of fuel efficiency and production in both recycling and quarrying applications. The robust and proven Terex chamber gives excellent reduction ratios and high consistency of product shape.
Fitted with Terex Finlay’s new crusher telematics solution and due to hit the market in Q1 2016, the machine features an independent aggressive hydraulic pre-screen with 9mm throw and 1,000rpm screen speed.
Powered by a Tier 4F/Stage IV Scania DC13 373kW or Tier 3/Stage IIIA Caterpillar C15 403kW engine, the ease of material through the machine is said to have been greatly improved on comparable models. Each component is said to increase in width as the material moves through the machine.
Fully hydraulic assisted apron setting features makes adjustment of the aprons convenient and efficient, while a heavy-duty vibrating feeder (VGF) with integral pre-screen removes dirt and fines and seizes bypass material for reprocessing.
Furthermore, an optional under crusher vibratory plate feeder with wear resistant liners aids material discharge flow.
The efficient direct drive crusher chamber on the I-140 is supplied with a four-bar rotor as standard.
Meanwhile, the new Terex Finlay 873 Spaleck is said to be the ultimate in mobile screening and separation technology. This new product offering is said to be the result of a joint partnership between Terex Finlay, among the largest firms for mobile tracked processing equipment and Spaleck, the claimed market leaders in static recycling screening technology.
At the heart of the mobile model is the two deck German designed and constructed high performance screenbox. The novel stepped top deck design combined with state of the art flip flow technology on the bottom deck is said to catapult the Finlay 873 Spaleck into a class of its own. Its processing capabilities and application flexibility is claimed to make the machine the only all-in-one mobile solution for processing difficult waste, recycling, slag, C&D, shredded metal, wood, compost, mulch, ores, coal and soil.
Even large-grained material can be screened on a screening machine with a Flip-Flow screen deck. The screening desk with 3D screen segments, which is positioned above the Flip Flow screen deck to form a cascade, protects and reduces the stress on the Flip Flow screen mats. Their service life is increased and optimal screening results are said to be guaranteed.
The 3D screen segments with maximum open screen area can be changed quickly and simply thanks to the modular construction. The screen mats of the 3D Flip Flow screen are fastened without screws and have no edges that could cause difficulties. This means that the screen mats can be changed quickly and there is an optimal product flow on the screen mats.
During the Germany customer and dealers event held 25-26 June 2015, Christoph Karrer, owner and CEO of Bau, Terex Finlay’s south Germany dealership, said: “Germany is a good market for sales, and Terex Finlay provides good products for us. The smaller mobile crushing and screening model is in the biggest demand here.”
MB Crusher’s new bucket
MB-LS140 was conceived in MB Crusher’s R&D department, which the company says “listens daily to customer suggestions and designs equipment that meets the needs of each individual site”.
Entirely designed in Italy in the MB Crusher factory in Fara Vicentino, Vicenza, the new MB-LS 140 is suitable for skid steer loaders from 2.6tonnes.
Said to be a “real jewel of mechanics”, the model is lightweight, coming in around 0.45tonnes, compact, and has a loading capacity of 0.5m³.