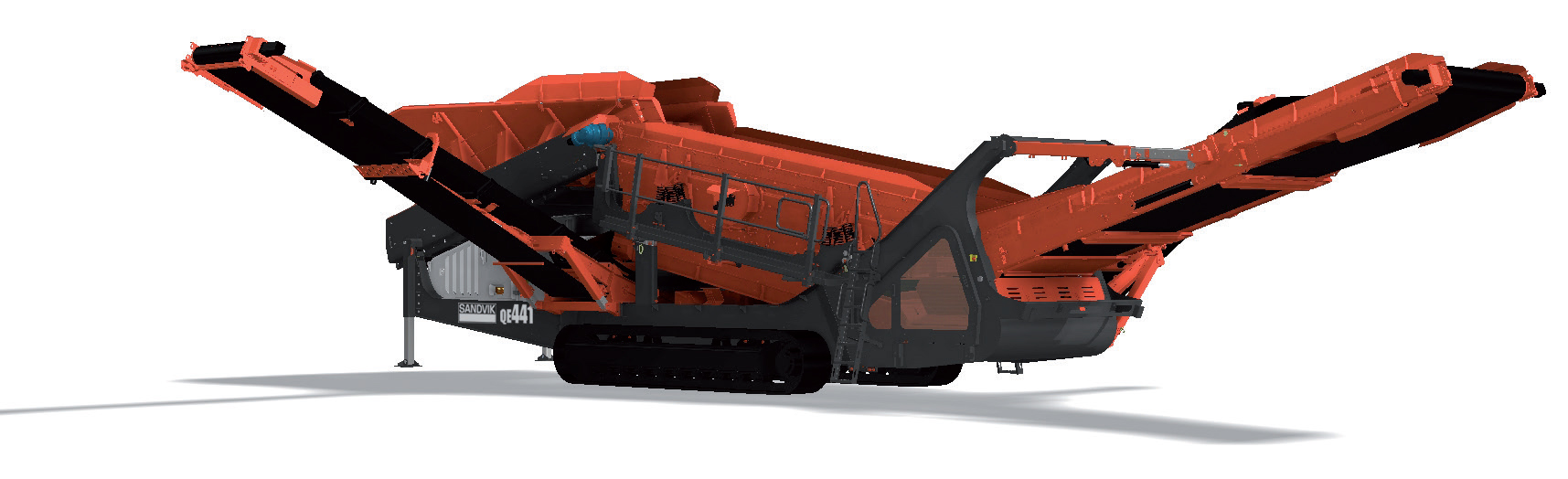
Lots of new crushing and screening solutions, including dual-powered models, from leading international manufacturers have come onto the market in the first few months of 2015. Guy Woodford looks at some of them.
Crushing and screening equipment offering high efficiency, versatility and productivity is always going to attract strong interest from quarry-based customers. And the new QA335 Doublescreen from
Based around a 4 x 1.5m Doublescreen, the QA335 includes many claimed class leading features for ease of operation and high levels of efficiency. These include a user-friendly electrical control system with sequential start up, hydraulic screen separation to aid screen media changes, and a fuel-efficient 74.5kW engine. The QA335 has been designed with wraparound walkways to provide operators with a safe working platform for service and maintenance, with their hydraulic operation enabling quick set-up times. The model also features radio control for ease of on-site manoeuvrability, and an oil cooler fitted as standard.
The innovative Doublescreen technology is said by Sandvik to be one of the most adaptable and flexible screening solutions available on the market today. It consists of two highvelocity screen boxes featuring independent screen drives with the ability to adjust the working angle of each screen independently to suit the exact requirements of your application. This is said to offer users greater adjustability, increased accuracy and higher screening efficiency, making it ideal for producing tight specification products without compromising on production.
Sandvik’s flagship QE440 scalper has been refreshed with the QE441, the latest addition to the brand’s premium range of scalping screens.
Key refinements to the QE441 include updates to the screenbox, screen drive and screen media, said by the Swedish firm to increase uptime, performance and versatility.
Other improvements include upgrades to the apron plate feeder, wear resistant hopper and radio remote controls, all of which are fitted as standard. To improve the experience for operators, the model now includes Sandvik’s easy to use control system and user interface with sequential start, whilst two-speed tracking will help to reduce travel time between job sites. The QE441 is said to offer increased plant durability and operator comfort, without sacrificing on performance.
The QE441 can accept even the most robust of infeed material and is now even better suited to large quarrying, mining and recycling applications. It can also work as a stand-alone unit feeding a primary crusher. Some of the outstanding features of this latest addition to the Sandvik range of mobile screens include a next generation 1-Series scalper; claimed class leading total scalping area of 5.5 x 1.75m / 5 x 1.75m allowing for high rates of production; the capability of being fed by large crushers, yet precise enough to produce accurate aggregates, and tough enough to recycle mixed materials; and a model designed for efficient fuel economy and low operating costs.
Due to their special nature, vertical shaft impactors (VSI) – machines typically used for shaping or final stage crushing – tend to follow a maintenance schedule of their own. To help plant operators tackle this problem,
Thanks to the longer lifetime and clever composition of wear parts, the Orange Rotor is said to require far less maintenance. It also includes several wear part options, which means that its service schedule can be easily aligned with the service intervals of the other crushers. This reduces the number of annual service shutdowns needed and translates to more production and, crucially, more profit. The increased wear life is said by Metso to be the sum of several factors. The Finnish company has made significant improvements to the material used in the wear parts, and the main frame of the rotor is better protected against wear, which reduces the need for expensive weld repairs. Furthermore, the rotor features several interchangeable wear parts. For example, the tips of the Orange Rotor consist of three parts that are easily interchangeable without bolts and nuts. As the middle part wears, it can be changed out with the top part in a matter of minutes.
In real-life quarry testing, Metso claims tip life increased by 30–50%, cavity wear plates lasted 20–30% longer, and the lifetime of the top and bottom wear plates was as much as 30–40% longer. The new Orange Rotor is said to not only enable longer service intervals, it is also much easier to maintain. Metso’s goal was to simplify the composition by leaving out all unnecessary bits and pieces and eliminating as many huck and bolt fastenings as possible. Thanks to this and a new fitting solution, the new rotor enables the changing of the wear parts in claimed record short time. The rotor consists of 25% fewer components, which helps customers to keep their stock more manageable.
The number of parts that can be changed through the innovative service door of the Barmac VSI has been increased. This is said by Metso to generate big savings, as basic maintenance can be performed through the door on the side of the machine without having to lift the roof off. This means that all related structures, such as conveyors, can remain attached to the machine during maintenance, saving even more time and effort.
These product introductions mean that the Northern Irelandheadquartered firm can now offer operators a full mobile crushing and screening train that can be powered from mains electric and has the flexibility to run selfpowered if required.
The mains electric connection or onboard genset powerpack power options on the J-1175 jaw crusher are said to present operators with significant power, servicing and maintenance cost savings in direct comparison to a diesel/hydraulic powered plant. The plant incorporates the robust Terex JW42 high performance electrically driven single toggle jaw chamber and a heavy duty VGF feeder to give optimum production in quarrying, mining, demolition and recycling applications. Additional benefits include rapid setup time, ease of maintenance, high reduction ratio, high output capacity and advanced electronic control system.
The jaw chamber is hydrostatically driven which offers operators reversible operation for clearing blockages that may be experienced in demolition and recycling applications.
The hydrostatic system also provides variable chamber speed to suit given applications. Chamber CSS (Closed Side Setting) adjustment is fully hydraulic, and can be changed in a matter of minutes.
The dual-powered
The C-1540 can be fitted with an optional patented pre-screen module which allows fines materials to bypass prior to being fed to the crushing chamber, offering better wear rates in the crushing chamber. These fines materials can also be prepared separately and discharged via the optional onboard side conveyor. The model’s large hopper/ feeder has an automated metal detection and purge system to protect the cone and reduce downtime by removing metal contaminants via the purge chute.
The Terex Finlay 694+ dualpowered inclined screen uses two 37kW IE2 electric motors as standard, which are suitable for most regions. However, an IE3 setup can be configured to suit particular regions such as the US. The intuitive and user-friendly electrical and hydraulic system allows the customer to switch between diesel and electric mode at the flick of a switch. The primary operation and controls of the machine remain the same regardless of the selected power.
The 694+ features a large 6.1m x 1.525m triple deck inclined screen giving a total screening area of 28m², ensuring efficient screening and high capacity.
Commenting on the company’s line-up at Intermat, Colin Clements, Powerscreen’s brand leader, said: “This machine demonstrates how we can meet the needs of the aggregates and recycling segments not just in France but across the world. We look forward to meeting with customers and discussing the features and benefits of our entire equipment range in Paris in April.”
The Warrior 600 is the latest addition to the Warrior mobile screening product family - said by Powerscreen to be the widest range in the market, with six machines of varying size to meet a variety of customer requirements. Ease of transport is only one of many eye-catching features on the Warrior 600 model. The mobile screen is highly versatile with its claimed ground-breaking simple conversion from 3-Way Split mode to 2-Way Split mode, able to be completed in minutes. It has been specifically designed for operators for whom versatility, manoeuvrability and transportation are of key importance.
A highly aggressive screenbox capable of 6G of force is another impressive feature of the Warrior 600. The high-strength, high-amplitude, two-bearing screenbox is said to allow easy handling and separation of large items from material fines in recycling tasks, such as soils from tree stumps and logs, fines and rock from overburden and blasted rock. User benefits include a rapid setup time and ease of operation aided by hydraulic folding side conveyors, rigid feed hopper sides and two-speed tracks.
In the US, visitors to AGG1 in Baltimore, Maryland, 17-19 March 2015 got a first look at
Also introduced at the AGG1 show was the J45R, which allows operators to produce a crushed and screened final product with one machine. Like the J45, the J45R boasts a 4.51m x 2.14m hopper with close to 6.8m³ capacity. The model’s 1.52m x 3.04m screenbox features McCloskey ‘High Energy’ technology, with adjustable speed. Rugged and versatile, both models are said to have undergone rigorous field-testing to ensure the reliability required for the toughest projects around the globe.
Anaconda’s new UK distribution
Paul Donnelly and Aaron McVeigh of RK 6, and Ben McQuaid of Matpro Machinery, have spent many years in the industry and are said by Anaconda to be highly regarded for their hard work, support and product knowledge when it comes to providing the right equipment for each application.
Anaconda provides a range of mobile crushing, screening and conveyor equipment enabling both distributors to offer solutions to the waste, demolition and the extractive industries. RK 6 will operate in the South of the UK, including South Wales, Matpro in Scotland and the North of England with existing Anaconda distributor, CDP Plant Ltd of Chesterfield, in Central England and the North of Wales.