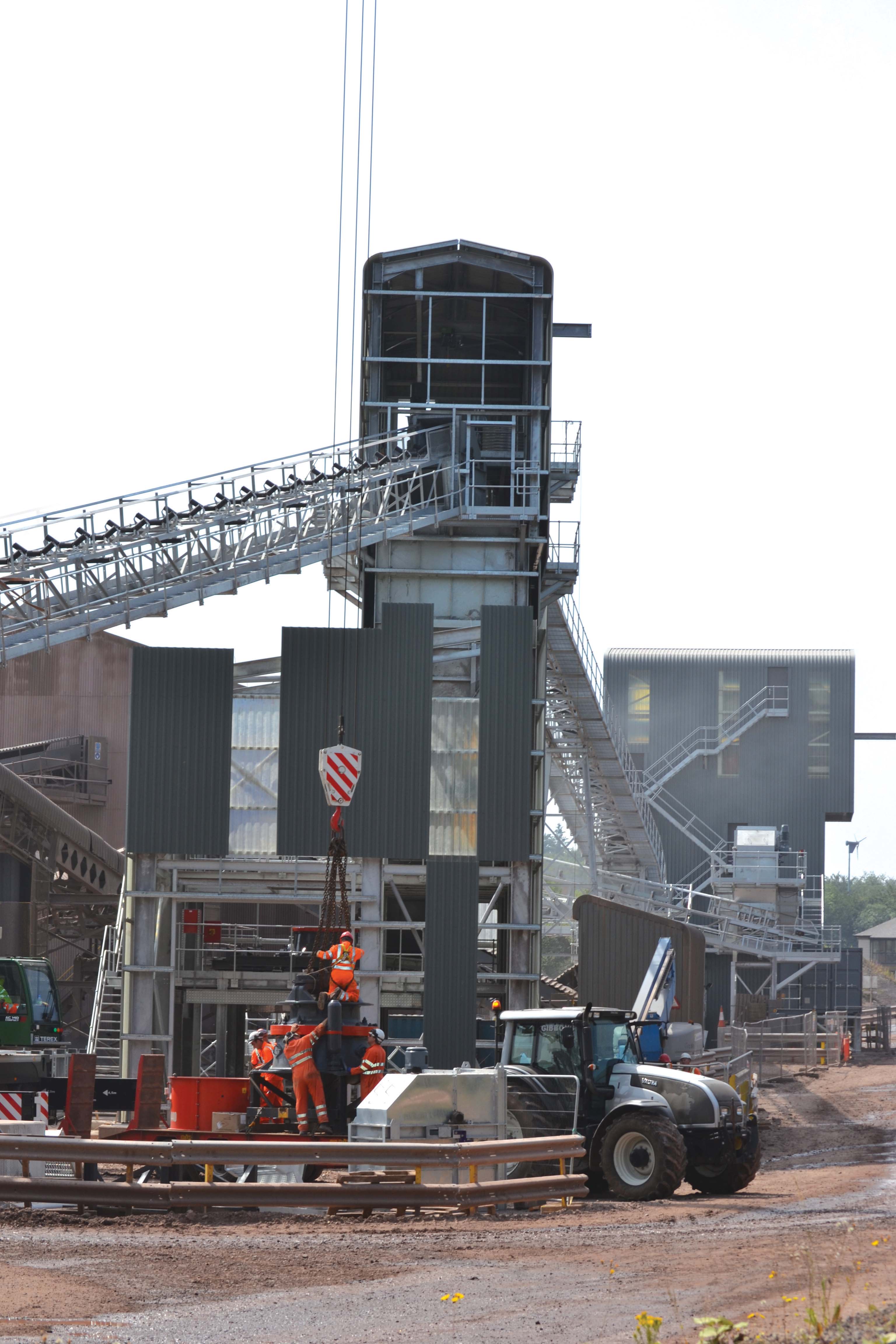
A new 20m high secondary aggregate production plant belonging to UK company Wainwright & Co is estimated to be 60% more productive than the equipment it replaces.
The county Somerset, south-west England-based company’s Moons Hill Quarry has seen £3.5 million (€4.4 million) of investment in the plant, replacing some of the equipment that has been in use since 1963. The crushing and screening equipment is all manufactured by
Independent company John
“Wainwright’s has maintained its market share through the expansion of the company’s core capabilities, major inward investment and the professionalism of our extremely experienced staff,” says Peter Barkwill, managing director.
“This pervades the company at all levels, and ultimately the quality of our major asset, the basalt upon which the company was founded.”
For over 100 years Wainwright has been extracting the basalt from Moons Hill Quarry, the only source of surface course quality aggregate within the Somerset and surrounding region. The aggregate is a hard stone basalt (Andesite) with a minimum PSV of 57.
Extracted aggregate passes through an extensive crushing and screening process, enabling the production of single sized and blended aggregate. As well as being used extensively for surface dressing throughout the south of England, the processed material has many other applications, including the production of asphalt or concrete, sub-base, a specialist dust for horse arenas as well as a non-calcareous aggregate for water courses.
To capitalise on the basalt’s excellent properties, in 2001 Wainwright established a road surfacing division, Wainwright Surfacing, which in 2003 formed another company, Mendip Contracting in partnership with
To develop quarry faces for the production of the aggregate it has, in certain areas, been necessary to excavate and strip between 20-30m of the weathered rock from the surface. This and the high quality basalt are removed by blasting, which is planned using laser mapping for logging the drill holes.
After analysing all the available data, the drill pattern is agreed and drill holes are placed in a precise pattern to ensure the maximum amount of stone is blasted in the most efficient manner. This ensures the aggregate is of a size that is able to pass through the crushing plant without further processing.
After blasting, the broken stone is normally loaded into dump trucks by face loading shovels and delivered to the crushing plant, which varies considerably in design and layout.
Typically the stone is discharged into a dump hopper, and then drawn from the hopper by an apron feeder with chain curtains controlling the flow of rock. From the apron feeder the stone falls onto a vibrating grizzly.
The under-sized stone falls onto a conveyor belt and the oversize passes into the primary crusher. Crushed stone falls from the crusher onto a conveyor belt which is parallel to a belt carrying the undersize from the grizzly running from the base of the primary crusher house to the new scalping plant.
This consists of a new scalping screen which is fed by extended conveyors from the existing primary crushing station. New scalping conveyors and a radial conveyor allow two sizes of scalpings to be stocked and blended. Dependant on quality and weather conditions, the scalping screen and conveyor arrangement allows scalpings to be recovered and fed into the secondary surge bin.
Recovered oversize scalpings and -200mm crushed rock from the primary crusher are discharged into a surge bin, prior to secondary crushing.
Here it passes through the new
The tertiary crushing station consists of a new Sandvik CH440 Hydrocone, and an existing Sandvik H3800 Hydrocone that was refurbished by Sandvik and then relocated from the old processing plant.
The tertiary crushed material is conveyed to the main screen house where it is passed over three linear motion screens which are fitted with polyurethane decks. These screen decks are set up to produce aggregates: dust, 5mm, 6mm, 10mm, 14mm, 20mm and rejects.
All the Sandvik crushers are based on the principle of hydraulic adjustment of the closed side setting (CSS) and ASRi (intelligent Automated Setting Regulation) is fitted to all machines. Sandvik’s ASRi is also fitted to both tertiary crushers and is said to optimise the efficiency and operation of the Hydrocone crushers by automatically adapting the crusher to variations in feed conditions.
By continuously measuring and compensating for crusher liner wear the ASRi allows Wainwright to fully utilise crusher liners, thus scheduling liner replacements to coincide with planned maintenance. The ASRi also assists in keeping the crusher choke fed, maximising rock-on-rock crushing, which helps to optimise the quality of the final product.
“In order to comply with local planning, the new plant now possesses minimal visual impact, with low noise and low emissions from all the Sandvik equipment proving to be vitally important given the proximity of the plant to both a main road and a local village,” says Peter Barkwill.
“Community relations are very important to us, and hence the benefits cannot be overestimated.”