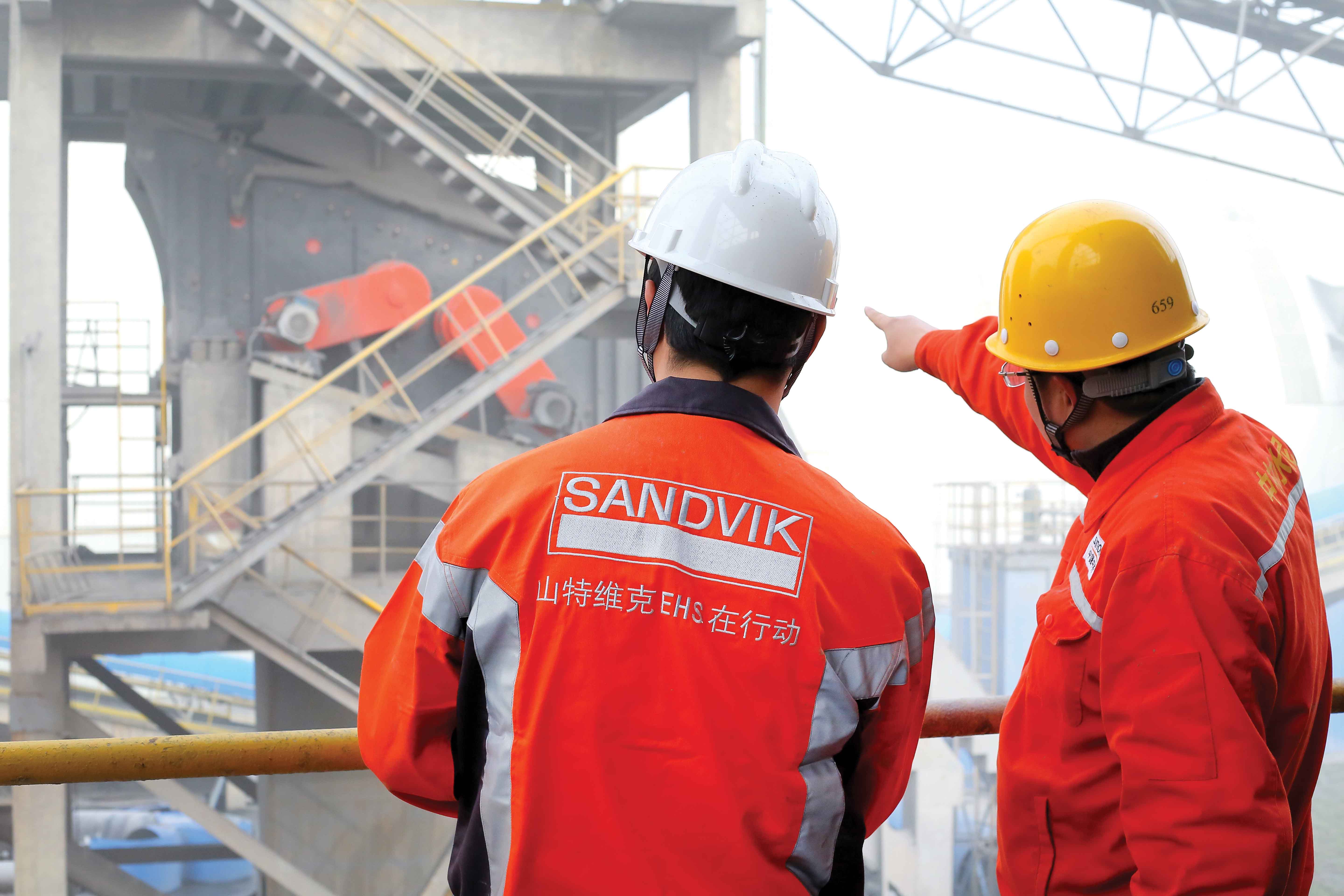
A Chinese company’s investment in a Sandvik Construction aggregate production model fleet is fulfilling its ambitious production and efficiency goals. Guy Woodford reports
In 2012
Established in November 2003, Sinoma Cement is a wholly-owned subsidiary of Sinoma Co. Ltd, an H-share listed company on the Hong Kong stock Exchange. Affiliated to the Sinoma Group, a central enterprise directly managed by SASAC, Sinoma Cement is among the first group of AAA grade credit enterprises in China’s building materials industry. Additionally, it is one of the 12 large cement groups which are directly supported by the government.
In 2007 the company created Sinoma (Anhui) Cement (Sinoma Cement) as a wholly-owned subsidiary. With registered capital of 600 million yuan (US$100 million) and total assets of 2 billion yuan ($315 million), the relatively new enterprise possesses extensive operations of over 660,000m². It now employs over 600 people and is considered the largest producer of cement clinker in the central Anhui region of eastern China. Its main products include cement, cement auxiliary materials, limestone powder, concrete products and cement products. The company has also enlarged its businesses into other fields, such as commercial concrete, admixture and aggregate.
The extensive production of clinker cement is facilitated through three production lines, each with a daily output of 4,500tonnes, with a total annual production of 5.4 million tonnes. In addition over 5 million tonnes of aggregates, in a variety of sizes, are produced annually. Thanks to the company’s own specialised wharf located at Lake Chao, 3.8 million tonnes of a variety of aggregates and other materials are shipped each year to the Yangtze River delta, and then supplied to customers at various locations.
Aggregate production began in February 2012, with the company keen to see production ramped up to 5 million tonnes annually. This would involve producing a variety of sizes for use in both cement manufacturing and for sale to the construction industry. The plan was to construct three aggregate production lines, with two being fully operational and the third being used depending on specific market conditions.
When Sinoma Cement set about ramping up its aggregate manufacturing the company established very high standards, both for its own operations and from the equipment it wished to use. In order to achieve these objectives, world-class equipment was not considered to be enough. The designated supplier of the aggregate plants would have to supply not only the plant, but also aftermarket support, proactive servicing, and plant design. The latter had to be able to deliver the production required, and had to deliver low energy consumption, environmental protection, operator training, as well as incorporate efficient transportation and stockpiling.
As would be expected from such an important player within the Chinese cement business, Sinoma Cement went about its search for a supplier that met its high standards methodically. Over the period of a year the company met with various manufacturers of aggregate plant, inspecting various facilities, and meeting with technical, service, aftermarket and planning experts.
Following this extensive and intensive process the final contract for all elements of the new aggregate plants was awarded to Sandvik in China. This resulted in an order being placed for Sandvik to supply all the equipment, plan the processes, and support the equipment for two aggregate production lines. This comprised of two SV1562 Grizzly Feeders, two CJ613 Jaw Crushers, two CI225 Impact Crushers, two SC3062 Circular Vibrating Screens and two SC3063 Circular Vibrating Screens. With this plant installed and commissioned, Sinoma Cement is now able to produce five aggregate products consisting of: 31.5-16mm, 16-10mm, 10-5mm, 5-3mm and 3-0mm.
As well as being able to provide badly needed accurately sized aggregates for the construction industry, Sinoma Cement is also using the materials produced by its aggregate plants for its cement manufacturing. As the material for both aggregates and cement are being produced from the same quarry, the blasted rock is quite often of a large size, being around 1m diameter. This necessitated the use of a primary jaw crusher that would be able to accept a large feed size, but at the same time be able to reduce the fed rock prior to being fed into a secondary crusher. The CJ613 Jaw Crusher has proved to be the ideal choice. As with all Sandvik jaw crushers, the CJ613 is of a single toggle design, with a deep, symmetrical crushing chamber and easy setting adjustment. It has a large feed opening for its size and an ideal nip angle, giving smooth material flow, high reduction efficiency and high capacity.
Behind the simple design are many advanced features that ensure easy operation and maintenance, long life and a low cost per tonne. The CJ613 has been purpose-built for tough quarrying applications due to its heavy-duty design, and built on proven technology to offer the highest possible reliability in relation to price and performance.
Secondary crushing is then provided by the CI225 Impact Crushers, which have proved ideal for producing the next stage with the ideal shape, essential in catering for the demanding requirements of the market. The CI225 has been developed for the secondary crushing of non-abrasive rocks in aggregate production, although its attributes has seen it used extensively in the recycling industry, crushing a variety of materials including reinforced concrete. It is designed on a simple working principle that encourages material to break along its natural cleavage planes, thereby producing excellent, stress-free, cubical-shaped products.
FEEDERS
2 x Sandvik SV1562 Grizzly Feeders
CRUSHERS
2 x Sandvik CJ613 Jaw Crushers 2x Sandvik CI225 Impact Crushers
SCREENS
2x Sandvik SC3062 Circular Vibrating Screens 2x SC3063 Circular Vibrating Screens
Following on from the crushing process the material is then sent for screening to produce the finished fractions. This is undertaken by two SC3062 and two SC3063 Circular Vibrating Screens. Sandvik’s SC screens can be used on a variety of screening applications, but being of a more robust construction they allow the feeding of a more coarse feed material size. Maximum versatility is said to be ensured due to their choice of screening media, with acceleration up to 4.5G possible on certain applications, ensuring maximum screening efficiency.
Following screening and stockpiling, the finished aggregates are then distributed across the Anhui area. This is accomplished due to highly efficient local waterway transport. This enables the material to be sent exactly where it is needed, being used on commercial concrete mixing plants in the major cities around Lake Chao and the lower-andmiddle sections of the Yangtze River.
The saying “effective tools to do good work” is well known in China. Although Sinoma Cement is said to be very pleased to have selected what it considers to be highly effective and productive tools. Furthermore, through evaluating and investigating the choices available to it, Sinoma Cement is said to now boast a highly reliable, efficient and low cost operation, supported and maintained by expert Sandvik personnel. Due to the professional and practical solutions delivered by Sandvik and its equipment, the Swedish company will also now be supplying equipment for Sinoma Cement’s green mining operation.