A Haver & Boecker company, MAJOR’s European operation (MAJOR Europe) is based in Battice, Belgium. The company currently sells its product range directly to customers in Germany, France, Belgium, Switzerland, Austria, Slovenia and Croatia. While working to increase its direct dealership reach in Germany and France, MAJOR is supported by dealer-led sales in the UK, Finland, Sweden, Netherlands, and Turkey.
Manufactured in Canada, Flex-Mat high-vibration wire screen media – available in TENSIONED and MODULAR form and in D, S, DD (impact resistance), L (sand screening), and T (fine screening) series variants - is seen by MAJOR as a key product range for European customers.
Flex-Mat TENSIONED allows wires, bonded to lime-green polyurethane strips, to vibrate independently from hook to hook for faster material stratification. The screen media is available in a side-tensioned or end-tensioned configuration.
Flex-Mat MODULAR comprises direct switch-and-replace polyurethane modular panels said to provide substantially more open area than traditional panels, increasing the throughput of spec material.
Unlike imitation self-cleaning screens, MAJOR designs Flex-Mat to fit all decks, from scalping to finishing screening. It features up to a claimed 40% more screen capacity than traditional woven wire and a claimed up to 50% more than traditional polyurethane and rubber panels.
As of late October 2019, over 1,000 Flex-Mat applications had been carried out on quarrying, mining and construction job sites in Europe since 2015 – 30,000-plus globally. A further 100-150 plant assessments have also been conducted in Europe over the past four years.
During a visit to MAJOR’s European HQ in autumn 2019, Aggregates Business learnt that plans are in place to begin producing the Flex-Mat product range in Europe within the next two years. MAJOR’s Woven Screen product range for European customers is currently made in Battice.
MAJOR’s original Battice workshop, excluding office space surface, was 1500m². The firm expanded the workshop surface up to 3700m² in 2016 by adding a new 2200m² facility. The company is in the process of extending the automation of its wire weaving machines in North America and Europe.
Globally, around 60% of MAJOR’s customers are in the aggregates sector; with 30% in mining and 10% in the recycling industry.
Speaking to Aggregates Business, Lars Bräunling, MAJOR Europe director of product technology, talked about why MAJOR, a company with a proud 130-year plus history, needed to operate differently in Europe, and not simply mirror its successful North American business set-up.
“We have a homogenous dealer-led approach to market in North America, where you can largely operate in one language and customer product needs are pretty consistent. In Europe, company type and size, produced product standards and how the products are made varies a great deal. Then there are 15-20 countries featuring many different languages that we are targeting sales-wise.”
Matej Grm, MAJOR Europe sales manager, said the diversity of the European market means that MAJOR Europe needs to have a particularly strong focus on localised customer service, both in assessing and installing the best product solution and subsequent aftersales support.
“We are in the process of building a ‘tool kit’ to allow our dealers to serve our customers even better,” added Bräunling.
MAJOR’s research and development (R&D) focus is on wire screen media products delivering continuous improvement, better performance, and longer wear life. New products must also be capable of more varied applications.
The R&D focus ties in with MAJOR’s corporate philosophy, which it refers to as ‘the MAJOR way’. It includes the company’s emphasis on advanced technology, screening know-how, and business operation – helping drive materials-producer profitability.
In November 2019, MAJOR introduced the Flex-Mat Sensor, a valuable and easy-to-operate vibration data-measurement tool users can utilise to review results and fine-tune their screen machine without shutting down equipment. The app-controlled vibration analysis sensor enables readings of screen-box vibrations within seconds and generates a report that can be sent or reviewed.
The operator connects the single sensor to the Flex-Mat Sensor app on their phone before placing the sensor on one corner of the machine. The user continues to move the sensor to each corner of the machine until finished. Once the measurement process is completed, the information will be delivered to the phone in the time it takes to climb down from the machine. Alternative systems may not provide the data until the following day. Machine information is stored locally for ease of use and viewing in areas with cellular limitations. Once a signal is available, the information uploads to MAJOR’s cloud service where it is viewable from a web browser. Historical equipment performance data is also viewable through the cloud.
The sensor measures g-force, stroke, rpm and orbit, including lateral movement — a measurement not offered by many vibration analysis systems. Producers can use the data to monitor and fine-tune screen-box performance as well as make parameter decisions with minimal guesswork.
Bräunling told Aggregates Business that at CONEXPO-CON/AGG 2020 (10-14 March 2020) MAJOR will unveil a new innovative screen media solution improving “product integration”.
Opting for a fully electric combination of Keestrack’s track-mounted R6e impact crusher and three-deck C6e classifier as part of a comprehensive modernisation of its processing technology is set to save Paekivitoodete Tehas (PT) nearly €100,000 a year in energy-related operating cost at the company’s flagship quarry near Estonia’s capital city, Tallinn.
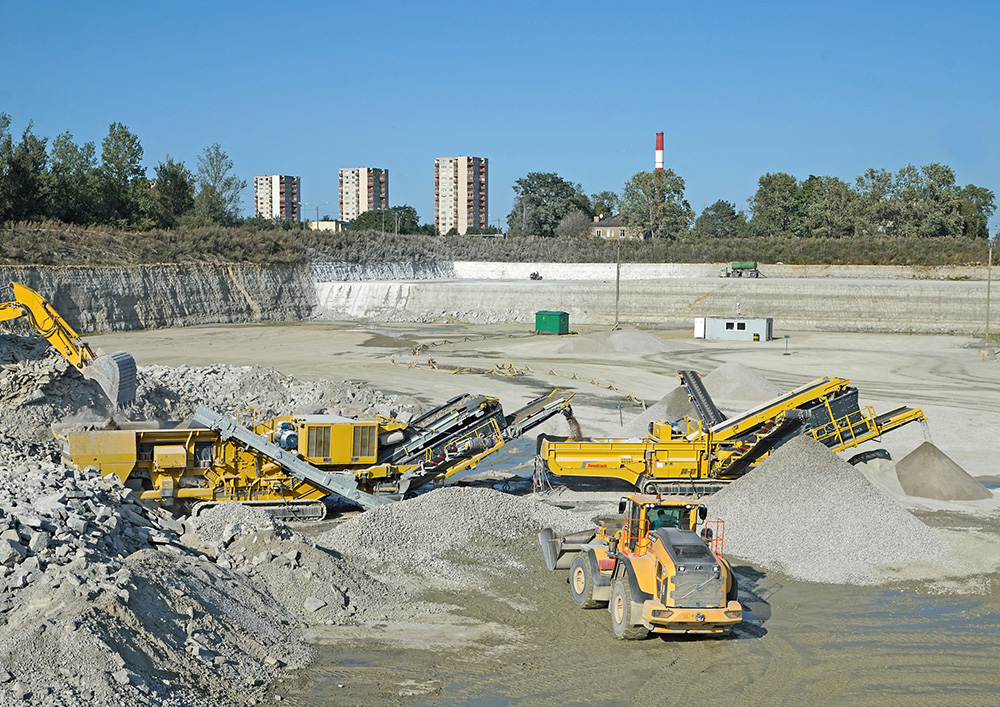
The impressive saving forecast by PT and Keestrack was made after the R6e and C6e began operating at PT’s Väo Quarry in June 2019. Connected to the grid, the new plant set-up cuts PT’s cost per final product tonne to €0.42, compared to the calculated total of €0.58 per tonne of the same machine duo’s annual diesel-electric powered operation (approx. 600,000 tonnes a year).
The reduction of pollutant emissions on site through all-electric crushing and classifying is also significant, with around 400 tonnes per year of climate-damaging CO2 avoided.
Since the installation of the R6e and C6e, the three-man working teams (excavator-wheeled loader-all-electric plants operator) have also been reaching their daily production target of 3,000 tonnes in one long or two short shifts, bringing further significant savings compared to the previous three-shift pattern, requiring 15 PT personnel.
The modernisation of the PT quarries’ set-up cost just under €1mn, with 35% of funding being provided by the Estonian Environmental Investment Centre (EIC) using EU regional funding. The significance of the project was demonstrated by the presence of numerous high-ranking representatives from politics and business at the new all-electric plant configuration start-up.
PT has now also become part of the international Keestrack network. As of 1 September 2019, the company officially took over as the Belgian crushing and screening equipment maker’s new sales and service supplier in Estonia and neighbouring Latvia.
Offering up to 400 tonnes of material per hour and four defined, final end products, the R6e and C6e in fully electric grid operation is said to have impressed PT management with their high efficiency and low environmental impact, while still offering the full flexibility of the diesel-electric hybrid drive.
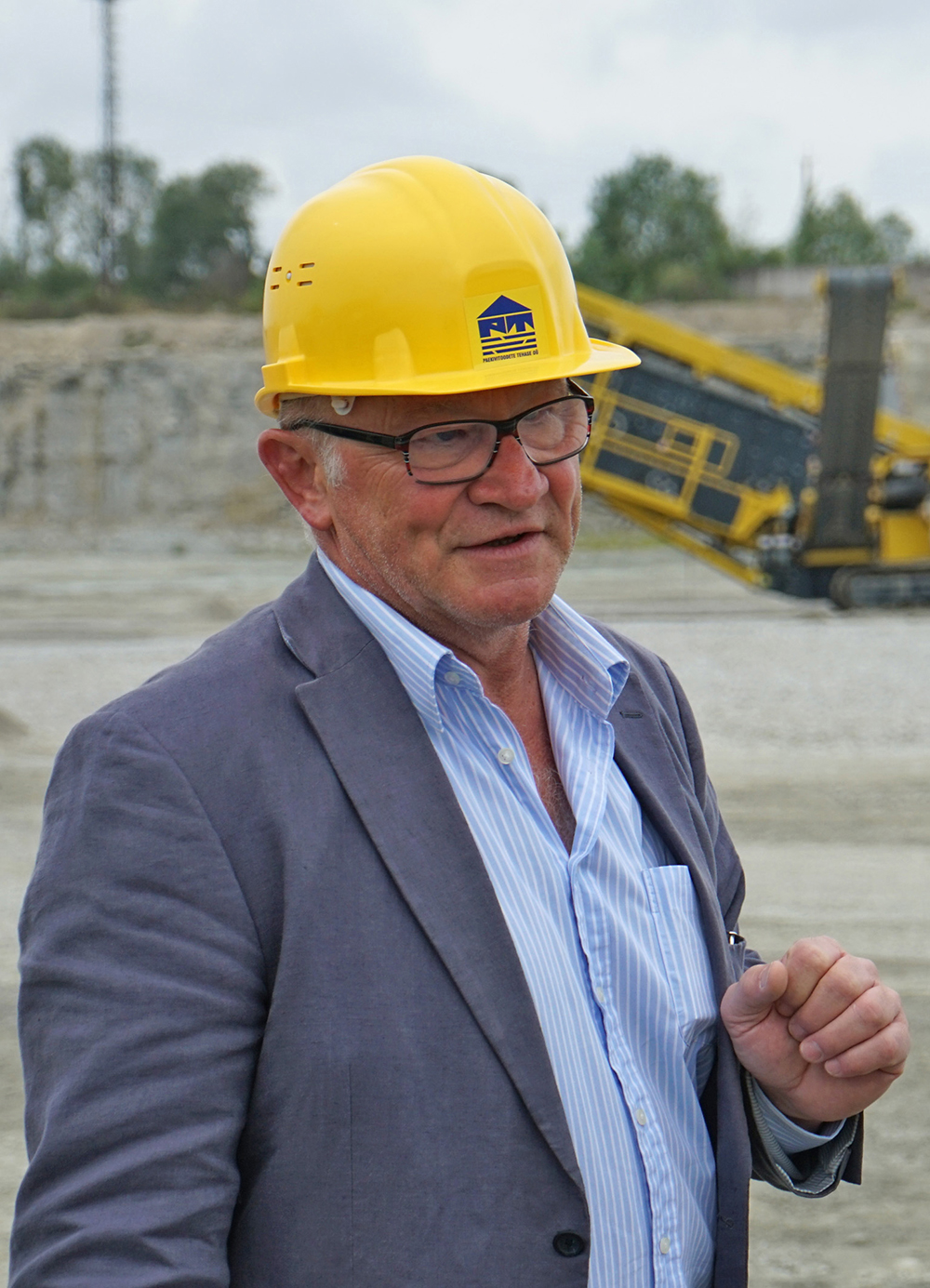
Since 1959, Paekivitoodete Tehas – ‘Limestone Factory’ in English – has supplied high-quality mineral and aggregates for the Estonian road and construction industry. Since 1989 the former state-owned enterprise has been gradually transformed into a private company and developed into one of Estonia’s leading construction materials suppliers, under the leadership of the long-standing director, today’s chairman of the board and majority shareholder, Vladimir Libman.
Today, up to 20% of the Estonian annual demand for crushed aggregates comes from PT’s Väo and Maardu quarries, with their combined extraction quantity of around 750,000 tonnes of material per year. Together with washed sand and gravel from mining residual masses with high contents of fines or clay and marl impurities and the company’s recycling activities, PT’s total production amounts to around 1.2 million tonnes per year.
On the Baltic coast, high-quality limestone is found close to the surface in 5-6-metre widths. In the past, PT has responded to the rapid growth of aggregates demand with three decentralised stationary processing units (totalling 400 tonnes per hour), whose raw materials, intermediate and end products had to be extensively hauled by rigid trucks. This low efficiency operation became problematic as the mining zone with its dust and noise emissions moved ever closer to the rapidly expanding Tallinn residential district of Lasnamäe, and its 120,000 inhabitants.
To minimise the impact of its quarrying activities, due to the fact that mineral reserves are expected to last for the next seven years, the company will rely on low-emission technologies wherever possible on its 176-hectare Väo quarry site. Instead of blasting, 95% of the stone is quarried by hydraulic hammer – further relief has been achieved through investment in modern low-emission and low-noise machinery and equipment.
Correspondingly, the comprehensive modernisation of the processing technology, along with an optimisation of the production processes has focussed especially on the protection of residents and a general reduction of the environmental impact. To replace the existing installations, a mobile processing line for the production directly in the mining zone was favoured for the main Väo quarry site as well as for temporary operations in the smaller Maardu quarry (150,000 tonnes per year), 10kms away.
The entire PT processing modernisation project was supervised by Johann Prüwasser, CEO of Keestrack Engineering, the Austrian design and development branch within the Keestrack Group.
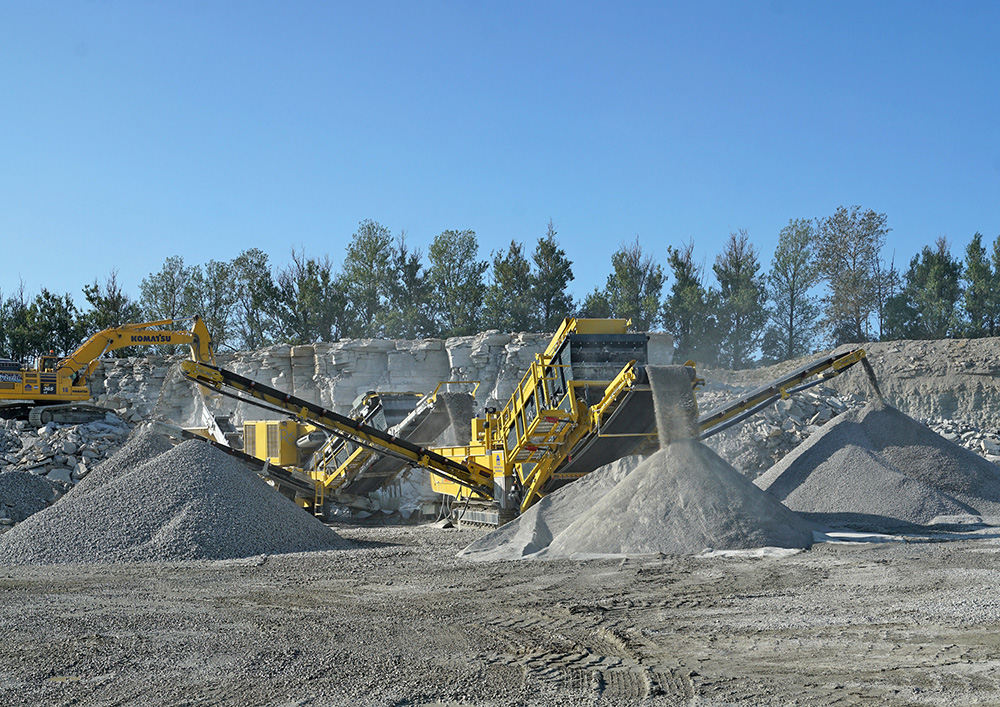
“Like all other suppliers, we found PT’s required high throughput of 375 tonnes per hour from 0/800mm to 0/63mm and the optimal distribution of the end products 0/4mm, 4/16mm, 16/32mm and 32/63mm a real challenge, given the high-quality but very tough raw material. However, we were able to exactly match the crushing characteristics of the heavy impact crusher in the R6e to the material, especially with regards to the necessary high rotor speed.
“With double-deck hanging screen and oversize recirculation, we now achieve high feeding quantities of 250 tonnes per hour of -32mm material to the connected C6e and deliver a good 30% 4/16mm main end product as requested by the customer,” explains Prüwasser. “We were able to realise the customer’s intended all-electric operation in the Väo quarry with all the advantages of our proven track-mounted technology,” he adds.
Two 200-metre cables from the specially installed 400V transformer station on the quarry floor now feed the Keestrack R6e and the downstream C6e classifier, directly connected to the crusher via power supply and communication cable for data exchange between the plant controls.
Powerful electric motors for the crusher drive (250kW) and the pump units of the central plant hydraulics (R6e: 90kW, C6e: 45kW), as well as electric belt drives and ancillary units, enable complete emission-free operation. If the plant combination has to be relocated in the course of the extraction process, both plants simply disconnect from the grid and follow the excavator on their own, using their on-board diesel/generator units. The independent diesel-electric drive also ensures economic temporary operation in Maardu quarry, which is additionally aided by the combined 95-tonne transport-friendly weight of the Keestrack plant combination (R6e: approx. 62 tonnes, C6e: around 32 tonnes).
Major development for Euroquartz
Euroquartz, based in Hermalle-sous-Argenteau, near Liège, Belgium, produces around 60,000 tonnes of building material products each year, with just over 50% for export customers in Europe or further afield.
In early 2019, the company identified a lack of consistent quality in every other truckload of variously sized quartz, silica, marble or limestone products processed through its Mogensen SN1544 four-deck sieving machine.
The company turned to screening wire system manufacturer MAJOR Europe, a leading manufacturer of high-performance screen media and a long-term supplier of solutions for some of Euroquartz’s other screening machines, for a solution. This led in May 2019 to MAJOR Europe installing its Flex-Mat high-vibrating wire screens on two of the Mogensen SN1544 unit’s four decks.
Eddy Depraetere, Euroquartz’s chief technology officer, said the introduction of Flex-Mat wire screens is expected to reduce the Mogensen SN1544’s production cost by 30%, with the company set to fit Flex-Mat to the machine’s two other screen decks.
When Aggregates Business visited Euroquartz in late October 2019, Depraetere said that the firm had processed 1500 tonnes of material with the Mogensen SN1544 without any problem.
“We are now able to produce a better quality product, while saving a lot of time and money through reduced maintenance. Before, we were losing one to one and a half hours of production time every time we had a problem with material throughput, such as plugging” said Depraetere.
“We initially installed the Flex-Mat on two decks of the Mogensen unit as we wanted to compare its performance against the screen media that came with the machine. The difference the Flex-Mat has made is really big.”
The successful introduction of Flex-Mat on the Mogensen SN1544 could not have been better timed as demand for Euroquartz’s product range is growing year on year. The company’s six-hectare manufacturing and storage site has been operational for more than 10 years.
“We have a wide client base. Our biggest export market is other European countries, but we also sell our products to customers in South America, China and Thailand. We also sell our sand products to the Saudi Arabians!”