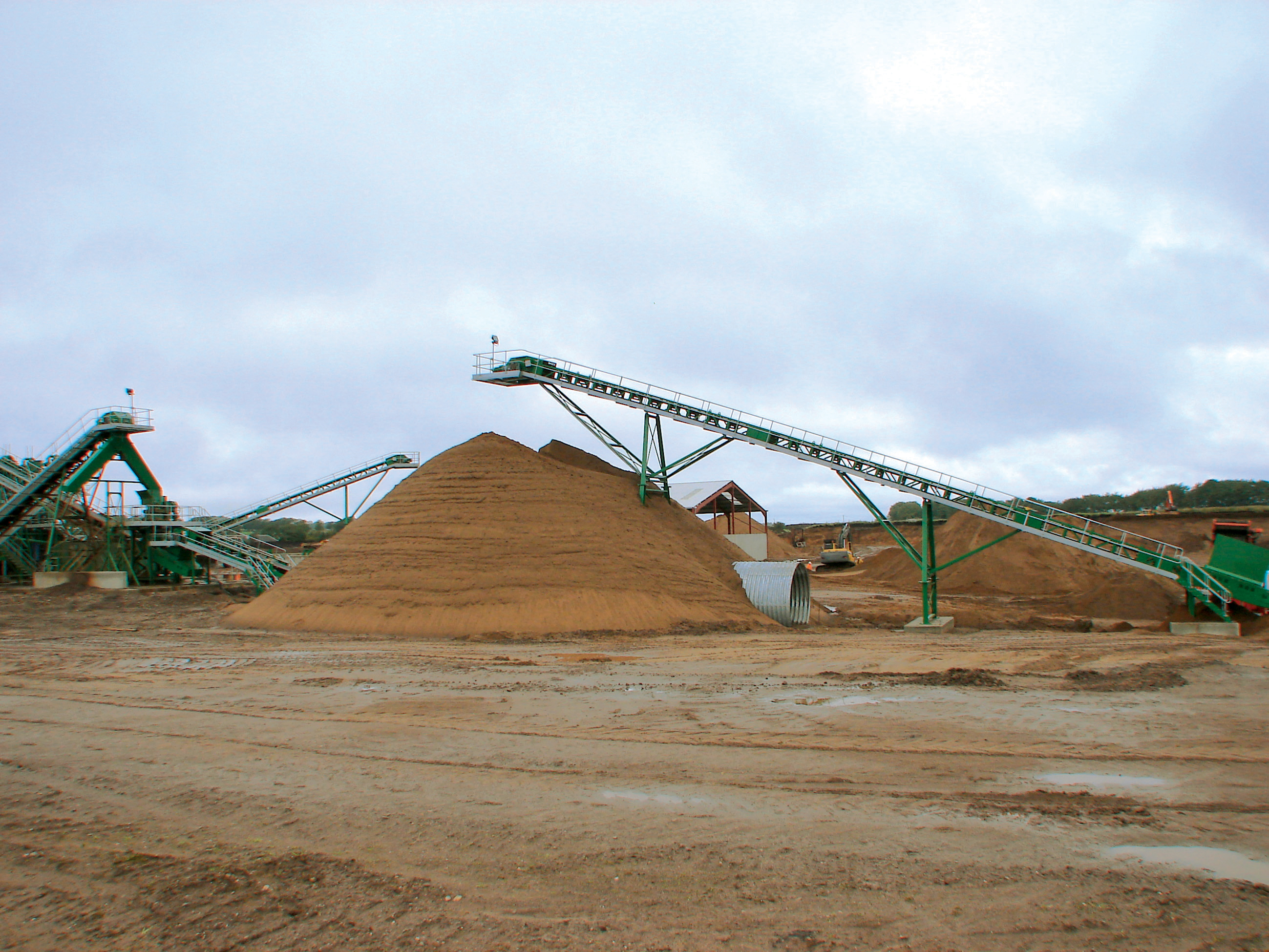
Latest washing equipment is helping to reduce water and power demand while producing cleaner aggregates and higher quality recycled material
Whether quarries are trying to improve the cleanliness of their aggregates, sell difficult deposits or move into recycled aggregates, washing is growing in popularity. Today's washing equipment has reached new peaks with water recycling and low power use and can be as sophisticated or simple as the user requires. Some of the latest models are also challenging the concept of washing equipment as fixed items of plant.
Recent installation of a lignite removal plant at
Lignite in itself can be a very useful commodity being a soft brown fuel, the characteristics of which put it somewhere between coal and peat. In Greece over 50% of electricity comes from lignite fuelled power plants. In Germany deposits of lignite are concentrated around the Cologne area and stocks are believed to be over 50billion tonnes. These are currently being exploited and generate some 25% of the electricity produced by Germany.
However, when lignite is present in deposits of sand and gravel it presents a significant problem as it compromises the final quality of the sand and aggregate products. In seeking to process this material effectively the specification of a system that is tried and tested in the effective removal of this lignite material is key.
The CDE plant at Snabe Quarry has been custom built to specifically tackle the individual characteristics of the feed material at the site. The plant's performance is measured by a set of pre-defined production requirements including final levels of lignite in the sand and aggregate products.
The plant currently in operation at Snabe Quarry has a capacity of 480tph and is producing two commercial sand products - a concrete sand and a building sand - as well as a 5-10mm and 10-20mm aggregate product. The plant includes a wide range of equipment from the CDE portfolio including its Prograde screens, numerous feed, stockpile and transfer conveyors in various configurations and its CFCU system for the washing of the lignite contaminated sand product.
"Every lignite removal plant is entirely unique" explained CDE technical manager Dermot Murphy. "The plant has to be constructed around the specifics of the project - most significantly the required capacity, level of lignite contamination and the desired final product specification." Since this CDE plant was fully commissioned at Snabe Quarry it has exceeded the requirements as detailed in the extensive performance guarantees drafted by Tarmac. Firstly, and most significantly, lignite being effectively removed - final lignite content was required by the performance guarantees to be 0.05% by mass. This is being comfortably beaten with Tarmac reporting levels of 0.03% by mass from the regular testing that they undertake on the final products.
Recycled benefits
Water reduction
Canada-based WS Tyler claims that its new Hydro-Clean can clean contaminated material from aggregate effectively but uses 75% less water than conventional log washers. Conveyor fed, the machine uses high-pressure water jets on a rotary washing head operating in close range to the material to remove contaminants as small as 63 microns deep within its surface. The turbulence in the drum creates additional scrubbing and abrasive forces that break down agglomerates and clean stubborn material to offer a 400tonne per hour capacity.While washing is improving the quality of natural material, washing also appears to be helping the recycling market generate new business."It does appear that the aggregate recycling business is busy - maybe because this material is a percentage cheaper than virgin aggregate,"
"There are a number of government incentives that are helping to drive demand for clean recycled aggregates - contracts like those of the 2012 Olympics projects require a proportion of the aggregate supplied to be from recycled sources.
"It seems that the recycling operators are cash rich generally. They start out in demolition and then move into recycling before expanding into complimentary areas like concrete. The customers are different from larger, more established quarry customers - the recycling people are relying on a few machines so when something goes wrong, they want a fast fix and good service.
"For the first investment many use turn-key or semi turn-key solutions to move into washing so the plants are not always fitted with the highest spec pumps and other elements. But once they understand the business better and have experience of operating plants, they are more demanding on specification.
Development
"I do not expect there to be many further technological developments in the washing sector in the next few years - the log washers, conveyors, screens etc are all standard. These units already offer good energy efficiency and high levels of water recycling. Nonetheless, it is interesting how the sites and customers in this sector develop - they are real innovators and good at looking for new business opportunities so they are likely to be the main driver of further development."
Kanter believes that changes in the sector will be driven by the end user. "The more challenging aggregate specification means that companies in Western Europe are investing in washing equipment to help meet the more technical demands," he added. "There is more demand for smaller machines and for simpler technology, especially in emerging markets." The drive towards smaller machines can already be seen with the launch of CDE's M2500 mobile washing plant and the debut of
Sound sand improvement
UK-based Potgate Quarry near Ripon, Yorkshire is benefitting from improved operation following installation of a modern hydro cyclone sand treatment unit. Quarry owner Lightwater Quarries had noticed that the existing screw/bucket dewatering unit was losing fine sand to the settling lagoons and worked with Finedoor to find a solution.
Finedoor worked with its sand processing and water treatment partner Sotres SA in France to install a new unit to recover 100% passing 150 micron during the Christmas shut down. The new system is capable of producing up to 80tonnes per hour and features a galvanised dewatering screen unit which is supplying a single grade of sand. Finedoor also supplied a Warman pump specifically supplied 'one size up' to minimise wear.
Initial grading taken after a few days after commissioning reflected excellent results, with tests on the waste water indicating nothing passing 75 micron was entering the lagoons.