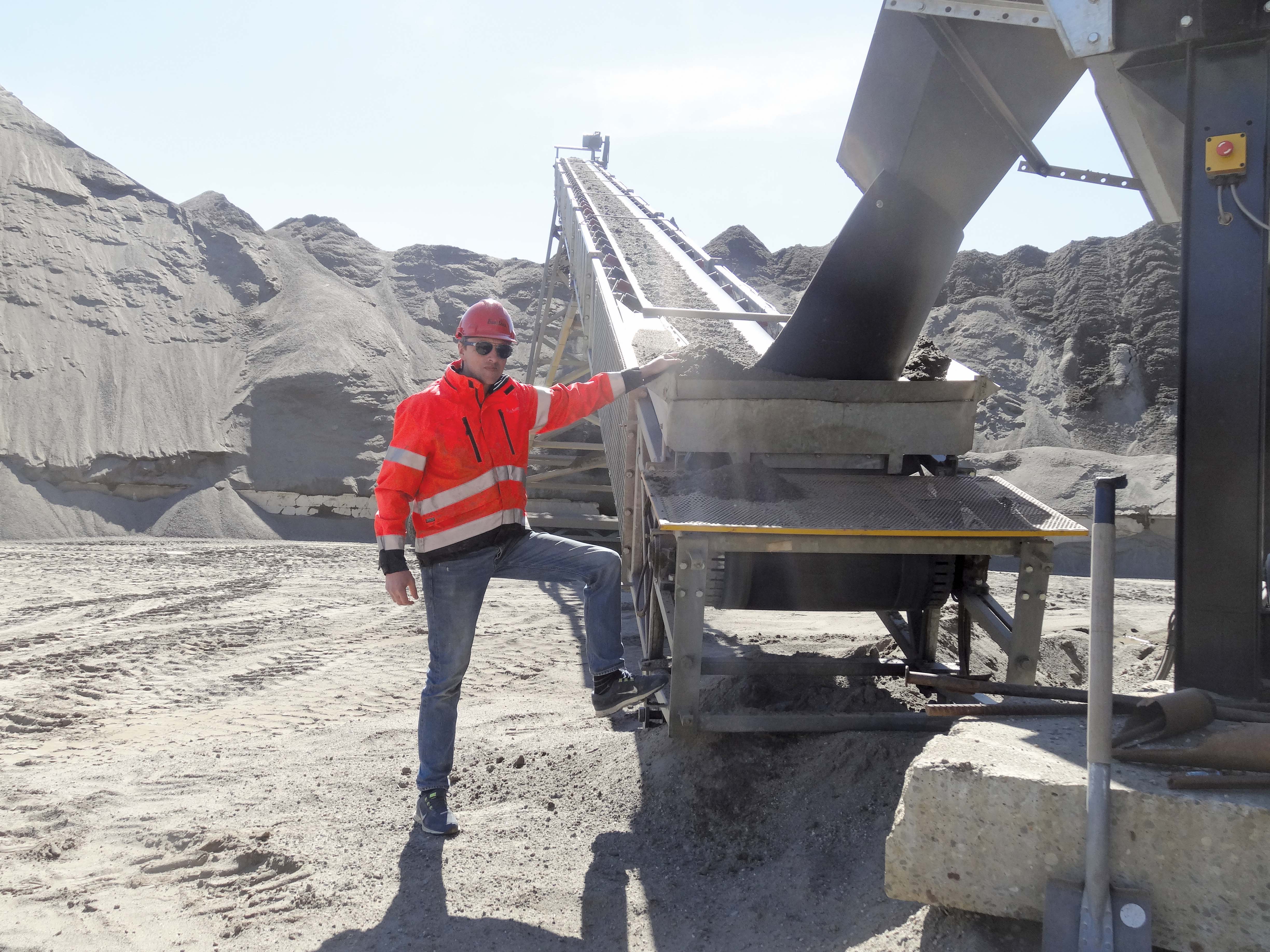
RSSA successful family-run quarrying business in Norway has increased its high-quality sand production capacity after investing in the latest Terex Washing Systems wash plant technology. Guy Woodford learns how the investment was secured thanks to a loyal, long-standing customer-dealer relationship.
Ole Haugum has known Terje Kristiansen, of Power System, the Oslo-based
The strong working relationship has seen Haugum, owner of Forset Grus, a quarrying company based in Tanem, near Trondheim, buy initially many
Sitting in his spacious office next to the family home on his 100hectare quarry site in Tanem, it’s obvious that Haugum is building another strong working relationship with Terje’s son, Geir Kristiansen, who has taken on the Power System dealer-customer relationship with Forset Grus from his father, now in his late 70s.
“Everything in life is about relationships, how you relate to people,” says Haugum.
“Whenever we have needed them [Power System] they have been there for us.” Geir Kristiansen added: “Forset Grus has bought a lot of our machinery over the years. Ole is doing a really good job and other customers in this area can see that he’s buying from us. It’s helped bring in new business.”
Having been impressed with the Terex Washing Systems Finesmaster (FM) 120BW Bucket Wheel wash plant, with 16 x 5 dewatering screen, over the previous six years, processing around 130tonnes/hour of 0-8mm sand for concrete and asphalt customers, and keen to increase his production capacity to meet customers’ demands, last summer Haugum bought an FM 200BW Bucket Wheel wash plant.
Holding a handful of the end grade sand that has recently come off the FM 200BW wash plant’s conveyor belt, Haugum says: “I’m impressed by the quality of material. It’s a very good machine.”
The FM 200BW wash plant is consistently delivering high quality 0-8mm concrete and asphalt application sand despite the varying quality of the initial feed material. Also crucially, there is zero wastage, as the silt produced in the materials’ washing process gets reused in the topsoil Forset Grus cleans and sells.
A static sand recovery unit on one chassis, the FM 200BW has a double bucket wheel, centrifugal slurry pump, twin hydro-cyclones, a collection tank, and, for Forset Grus, has been fitted with a 20 x 6 dewatering screen. It can produce one or two grades of sand, and is designed to work in conjunction with other Terex Washing Systems plant equipment. Capable of producing up to 200tonnes/hour of top quality washed final grade material, the wash plant model has a collapsible bucket wheel tank for easy transport, and offers quick set up time, low maintenance, reduced pump and cyclone wear, and lower running costs.
Terex Washing Systems says the FM 200BW delivers maximum recovery of material above 75µm (200 mesh); removes silt, slimes and clays below 75µm (200 mesh); removes water following dewatering operation to 10–15% of residual water content; and offers a major reduction in saleable material discharging to the pond, reducing pond maintenance and saving money.
Forset Grus’s Tanem quarry produces around 200,000tonnes/year of sand for major Norwegian companies like Unicon, whose concrete products are sold all over Norway and beyond, and national highway construction and maintenance firms like
Earlier in Aggregates Business Europe’s visit to his quarry business, Haugum had explained how his final sand product had to meet the high standard of material demanded by the Norwegian transport authorities – to NS-EN 13043 for asphalt; and to NS-EN 12620 for concrete.
“Everything is very strict. The cold climate means that there has to be tough control of asphalt standard as the frosts can damage roads unless you use the right materials. The authorities come and do tests and we also have our own materials testing laboratory, so that we know our standards are high. It also means we don’t have to send off material samples for testing elsewhere, which can take too long to get the results back.”
WASH PLANTS
1 x Terex Washing Systems Finesmaster FM 200BW
CRAWLER EXCAVATORS
1 x
1 x Volvo CE EC290
1 x Volvo CE EC220
1 x Volvo CE EC88
WHEELED LOADERS
2 x Volvo CE L150F
2 x Volvo CE L120G
1 x Volvo CE L150G
1 x Volvo CE L120H
CRAWLER DOZERS
1 x
1 x Komatsu D65 (2007 model)
CRUSHERS
1 x Sandvik UJ440 65 with a 2-deck screen
1 x
1 x
1 x Sandvik UH320 (Mobile Crushing & Screening Unit)
SCREENS
1 x Powerscreen 1700 Chieftain
1 x Powerscreen 1800 Chieftain
1 x
Haugum says that the growth and continuing success of his Tanem quarry is due to his use of wash plants over the last two decades, as the Norges geologiske undersøkelse (The Geological Survey of Norway - NGU) had said back in the mid-1990s that its aggregates were not, with dry screening alone, of a high enough quality to process due to their excess clay and topsoil.
The quarrying entrepreneur is also quick to praise the quality of his locally sourced workforce, including Edward Husby, the Tanem quarry site manager, who has been with Forset Grus for three years.
“Here, you learn something new every day,” says Husby, taking a short break from the day’s material loading work. Of Terex Washing Systems’ FM 200BW wash plant, he adds: “It has much more capacity. We’re now processing 180tonnes of sand an hour, a lot more than before.”
As well as operating a successful sand quarrying business, Forset Grus also recycles around 10-15,000tonnes/year of concrete and asphalt, and cleans and sells around 30-40,000m³ of topsoil.
However, it’s the location of Haugum’s quarry business that is equally as important to the diversity of products he can offer existing and new customers.
“As we are close to Trondheim and its port, our transport and shipping costs are lower. This is a big advantage,” he explains.
Haugum says there is around 20 years of life left in his Tanem quarry. He is keen to quarry on more of his site but says he has been prohibited from doing so by local authorities due to concerns over noise, dust and other issues expressed to them by residents living nearby.
However, he is keen to take advantage of Norwegian mineral processing laws introduced in 2010 that has seen DIRMIN designate mineral-rich but as yet undeveloped green-field land for quarrying, rather than new housing. “It’s a clever idea. Cities need all the minerals- based materials they can get, and it gives businesses like mine opportunities to grow.” RSS