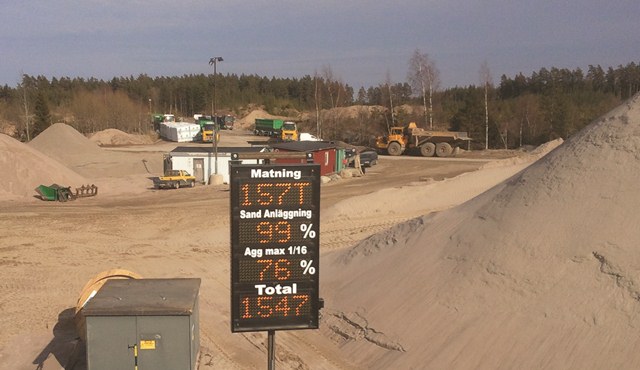
Working closely with leading Swedish operator Jehander, CDE had to ensure it had a full understanding of the project requirements, which included a digital feature that allowed it to optimise productivity.
With one of the largest pit operations in the capital Stockholm, producing sand, gravel, crushed rock and soil, Jehander ultimately wanted a mechanism to monitor the throughput levels of sand and aggregate being produced to allow them to achieve maximum productivity.
Subsequently, CDE developed a controlled automation system which integrates fully with the operation of the plant itself and is used to set the tonnes per rate on sand and aggregate, in turn highlighting the need to increase the feed material if and where necessary.
For Jehander, overall production improvements is said to have amounted to approximately 15%.
The controlled automation system allows visibility of production for the operator while allowing for raw material planning in terms of management to plan and supply the right mix of raw material to the plant.
The system is said to effectively display tonnes/hour of material to the washing plant as highlighted on the top row of a digital display board. The actual tonne/hour of sand and aggregate is also set individually on the HMI, indicating that the operator ideally should maintain the figure at 100% in order to fully maximise the washing plant operating tonnage.
The digital display also features a mechanism that will allow the user to monitor the overall actual tonnage of material that has been fed through the washing plant over a certain time period which can be reset at the end of the day or week.
“Essentially, what this means is that when a plant is running and the sand level is for example at 60% with the aggregate running at 100%, this will highlight to the operator that finer raw material is required for feeding into the hopper in order to maximise overall plant productivity. The hopper will either increase or decrease speed to maintain the optimum level of 100% on aggregate and sand,” says CDE.