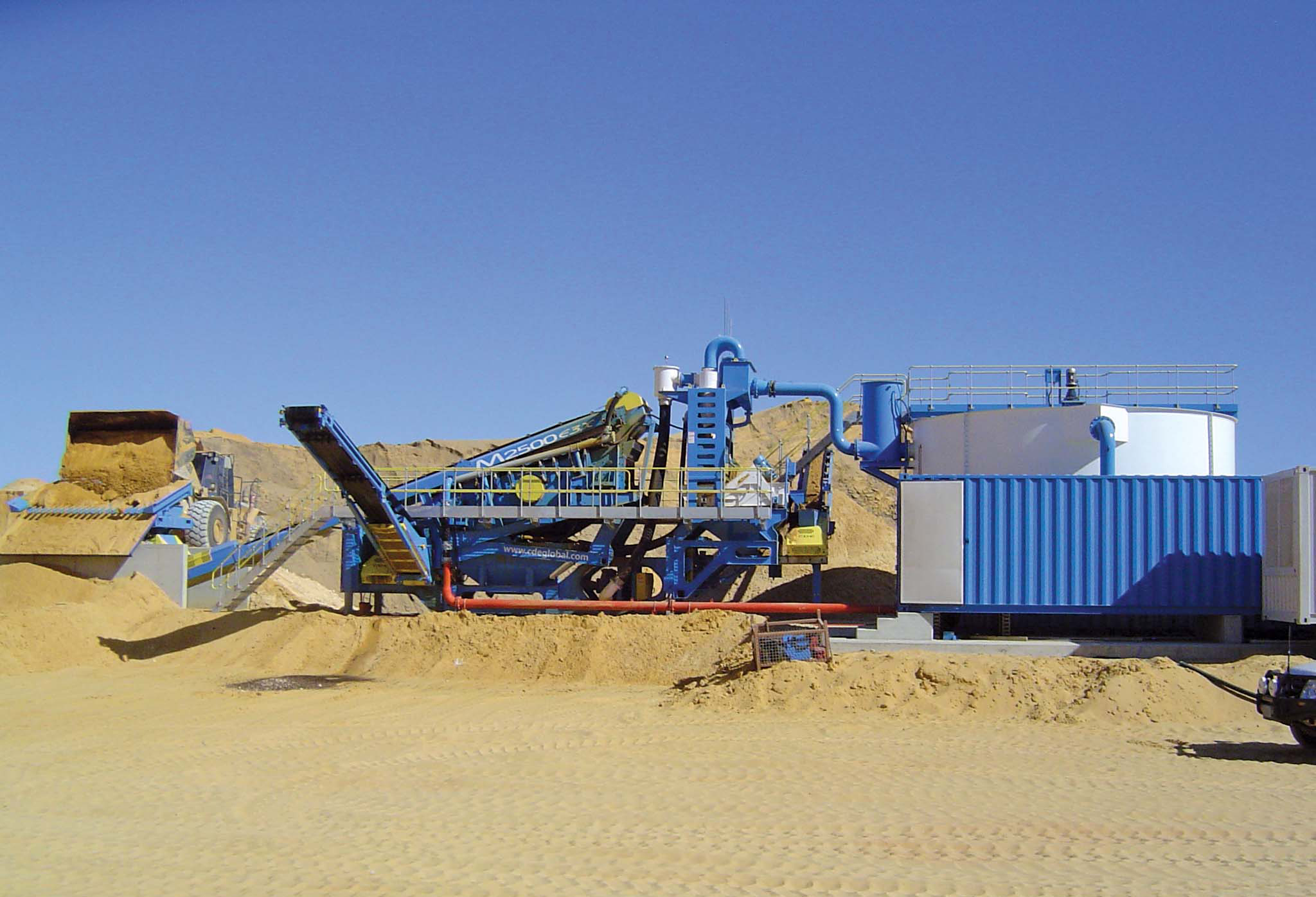
Family-owned Australian company WA Limestone has become one of the biggest suppliers of road construction materials and armour rock for breakwater construction and marine infrastructure in Western Australia.
The company, which has been operating for over 40 years, has quarries strategically located all over the Perth and north-west area, and its sand and gravel plant, now in its fourth year of operation, produced 1 million tonnes of concrete sand and gravel in the first three years. It supplies 30 different types of raw materials.
Since its installation in 2011 at its Perth site. WA Limestone says it has had no requirement to purchase any parts or service repairs other than routine plant maintenance which in itself has generated substantial cost savings while ensuring the optimum capacity at a rate of 200tonnes/hour.
After visiting bauma 2010, the company decided to replace its existing equipment in order to produce more consistent sand and gravel products for its own concrete plants with the aim of supplying material to construction markets throughout Perth. As a result, it invested in an M2500 mobile washing plant and an AquaCycle thickener from materials washing specialists
The ability of the plant to run effectively is primarily due to the durability of its design, according to Sean Kerr, engineering manager at CDE Global.
“The use of the highest quality polyurethane screen decks within the ProGrade P2-75 rinsing screen maximises plant life and offers the highest level of resistance to abrasion during the aggregate screening process,” says Kerr.
He highlights the discharge position from the M2500 feed conveyor, which ensures that material is delivered to the very back of the screen, maximising the available screening area.
He says that the easily replaceable modular polyurethane screen panels also reduce the time required for plant maintenance thus increasing the plants’ productivity.
The spraybar assembly on the ProGrade P2-75 rinsing screen is mounted independently of the screen box which in turn eliminates vibration and extends the life of the plant. The ProGrade also features a Rosta tensioned drive unit for increased belt life and efficiency, and as belts are held in constant tension they are not subjected to any shocks as the ProGrade screen rotates, also resulting in increased plant life and reduced maintenance costs.
Design features within the integrated EvoWash are also said to be proven to eliminate wear such as the rubber lined feed box which maximises the screening area on the dewatering screen and minimises the impact of material directly onto the screen deck, increasing operational life.
Rubber lined pipework ensures maximum wear resistance to minimise the lifetime cost of ownership. The discharge chute and cyclone of the EvoWash are also rubber lined to prevent abrasion of material on steel to offer superior wear resistance, says Kerr.
The focus for CDE in Australia is on the development of business in the sand and gravel and crushed rock sectors as well as the growing construction and demolition (C & D) waste recycling market through the introduction of the EvoWash sand washing plant and the M2500 mobile washing plant which “offers feeding, screening, sand washing and stockpiling on one single compact portable chassis.”
Steven Bella-Dona, director of WA Limestone, says: “Since our investment in the sand and gravel plant from CDE Global in 2010, we have been extremely pleased with the performance of the plant and its capability to process large volumes of material effectively.”
Terry Ashby, regional director for CDE Global, says: “Our sand and gravel washing systems have been employed by many of the leading construction materials companies in the world to improve efficiency of their operation and add value to their final sand and aggregate products and this is certainly also the case for WA Limestone.
“The efficiency improvements that the M2500 in particular has offered is evident in this case, particularly given the volume of material which has been processed through the plant and the company’s savings on parts and maintenance over the three-year period.”