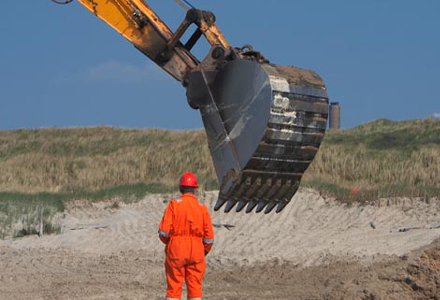
Operating or walking close to moving machines presents quarry workers with a greater risk of accidents. ABE looks at technology aimed to protect the workforce
Quarrying equipment is by nature large and heavy but this presents some major risks to people working in the quarry. For machine operators, just accessing and exiting the cab can be dangerous, plus there is the risk of overturning while manoeuvring around the site. There is also the issue of visibility and ensuring the safety of quarry workers when they are not working within the relative safety of a machine cab.
In recent years machine manufacturers have responded to the industries' needs and a number of new features have been added to minimise the accident risk. Nonetheless, too many of these remain as optional extras rather than standard fitment and until legislation enforces minimum standards, it is up to the industry to demand them as common practice.
The UK's
Access and egress
Climbing in and out of the machine at the start and end of a shift has been identified as one of the biggest cause of accidents with a high risk of trips, slips or falls. Vertical ladders with a large reach to the first step used to be a standard design for access, but many manufacturers are developing inclined steps with textured surfaces and guard rails to ease access.
Daily maintenance is an important task to ensure productivity and again machine design has helped to lower the risk of accidents from this activity. Many daily maintenance points are now co-located at ground level and where an operator has to climb onto the body of the machine, guard rails are now becoming common place.
Manoeuvring
Once in the cab, the health of the operator is further protected in newer machines with air filters to remove dust, noise suppression and isolation from potentially harmful vibrations with hi-tech seats and cab mounts. Visibility of many machines has been improved with lower profile body work and larger glass panels in the cab. However, to maintain this view it is important that machines are cleaned on a regular basis.
Reversing alarms have long been standard in many countries but there are still some areas in Europe that do not use them, putting workers walking across the site at risk of a machine strike. Although training of all quarry workers in safe working on a live site is essential and they should be aware of their surroundings, audible warnings should be considered essential protection.
Some quarry operators are beginning to fit rear view cameras and obstruction alarms into their machines. These give the equipment operator a much more informed view about the hazards - stationary and moving - that surround their machine.
While many quarry operators cannot currently afford to invest in new fleets with the latest safety designs, rear-view cameras, obstruction alarms and audible reversing alarms can be retro-fitted for a minimal cost. Retro-fitted into older machines can help to ensure that safety advantages can be applied across the quarry operator's equipment fleet and ensure minimum safety standards.
Responsibility
Many quarry operators have set themselves the target of achieving zero lost time accidents and, while this does require a step-change in behaviour on site, it is important to remember the impact of machines on safety. Investment in safety features helps to protect the workforce and will contribute to achieving targets but with many operators reducing capital investment, it is important to focus on the safety features of a machine rather than just the purchase price to ensure machine safety continues to improve.