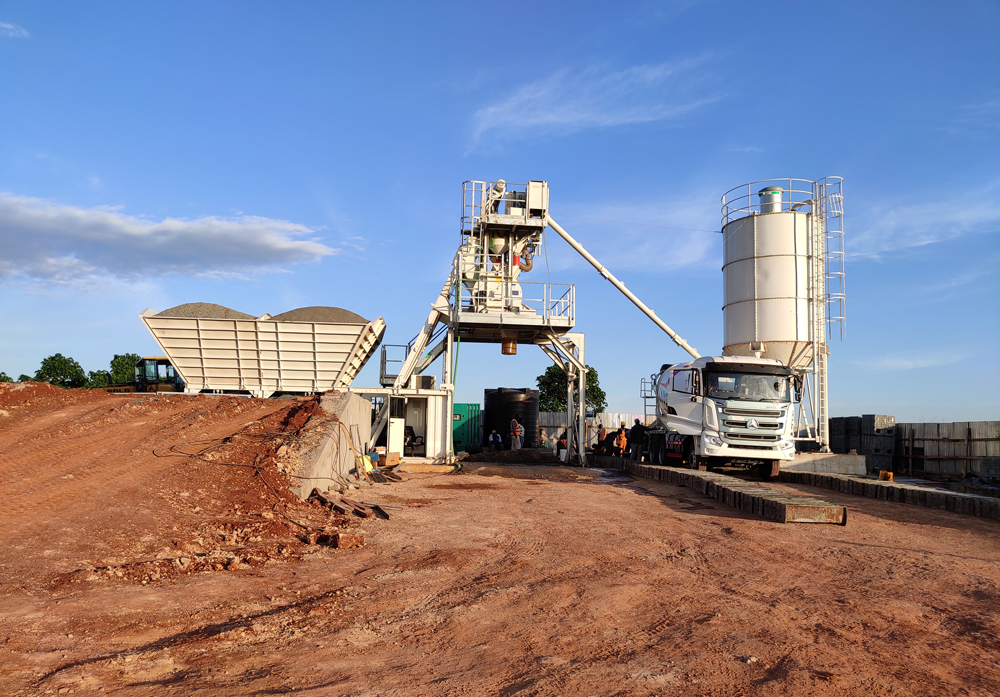
An Ammann concrete-mixing plant is helping Jilk Construction fill a key niche in the growing Kenyan market.
Nairobi-based Jilk recently purchased a CBT 60 SL Elba concrete-mixing plant, which is compact and easy to relocate between projects. Despite its compact dimensions, the plant has the production output to support large projects and the result is a mobile plant with high production potential.
Jilk has played a key role in public institution development, upgrading of infrastructure, commercial and residential building construction, project management design and supervision.
“We are in the process of obtaining the bigger projects in Nairobi and other parts of Kenya, and will use this plant on those jobsites,” said Sammy Maina, director of Jilk. The CBT 60 has a production output of 60m3 per hour.
“Normally in Kenya, 60 cubic metres is considered a larger capacity, and the most common hourly output is 30 to 45 cubic metres,” Maina said. “Our aim is to get the large projects to utilise this plant’s capacity.”
Several options provide the flexibility needed to develop varied concrete types to supply mix to outside customers as well. “We also will be using the plant for selling commercial concrete,” Maina said. “The plant has all the options necessary for commercial selling in targeted areas, such as additives, silica and cement.”
Commenting on what in general is new in concrete construction processes Volker Kies, director of concrete plants sales at Ammann, says that high- and ultra-high performance concretes are finding their way into processes.
“This enables the production of high-quality and freely designable concrete components,” he adds. “The design of buildings can thus be more efficient and filigree.”
In terms of how Ammann’s equipment fits into these trends, Kies says that high- and ultra-high performance concretes require high-performance mixers. “The single and twin shaft mixers from Ammann Elba are ideally suited for these applications and have already proven themselves many times in this field of application,” says Kies.
“With special options on the mechanical side as well as on the side of the control system, we can achieve very short mixing times that are no longer than in the production of standard concretes.”
Asked what green initiatives there are in concrete construction and how this ‘ancient’ material is changing to meet today's requirements, Kies says that two points should be emphasised.
“On the one hand is the goal of conserving resources,” he says. “More and more recycled materials are used for mineral aggregates.
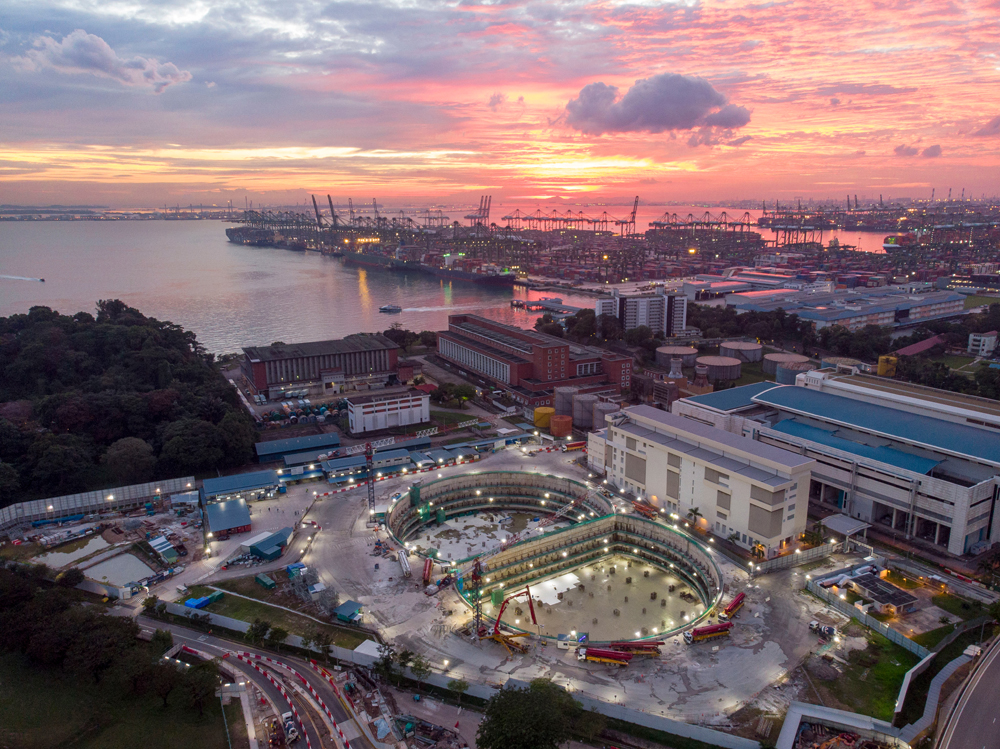
“On the other hand, we are constantly working on optimising the energy consumption of our plants. The use of frequency converters for large drives reduces the current peaks when starting up.”
Regarding what the future holds, Kies says Ammann’s opinion is that the development of modern concretes is not finished yet. “New solutions in the field of mixing and control technology must be found,” he adds. “As a plant manufacturer with our own team of experienced development engineers we will answer this task accordingly.”
Alternative fuel is the focal point of an engineering and procurement order that Turkish cement producer Bursa Çimento placed last year for the supply of a fully integrated clinker line from Denmark-based FLSmidth. The clinker line ranges from a crusher to the clinker cooler, and Bursa Çimento says it is expecting to harvest significant sustainability and productivity gains.
Situated in north-western Turkey, work at Bursa’s local site is under way with production from the new line set to start at the end of 2022. The order includes, among other equipment, FLSmidth’s HOTDISC Combustion Device, which will help increase the substitution rate to 86% - claimed to be the highest in Turkey.
“The modernisation of our Bursa site is a strategic investment, providing us with a more competitive cost base,” said Osman Nemli, general manager at Bursa Çimento. “But just as important is the entire upgrade which focuses on reducing emissions and power consumption. In this way, we are proactively mitigating future possible environmental regulation.”
In a separate move FLSmidth has also launched the latest version of its advanced process control solution, ECS/ProcessExpert V8.5 software, which now includes the ability to integrate new AI (artificial intelligence)-cognitive technologies and functions.
As one practical example of AI at work, the ECS/ProcessExpert V8.5 software facilitates predictive modelling of process data signals that are either unreliable or unavailable – such as real-time clinker quality measurements or O2/NOX measurements at the kiln inlet. These are then used to create a more accurate model and controller of the actual process conditions. FLSmidth says this provides benefits including better ability to maintain optimal setpoints and faster response to conditions that may result in undesirable situations.
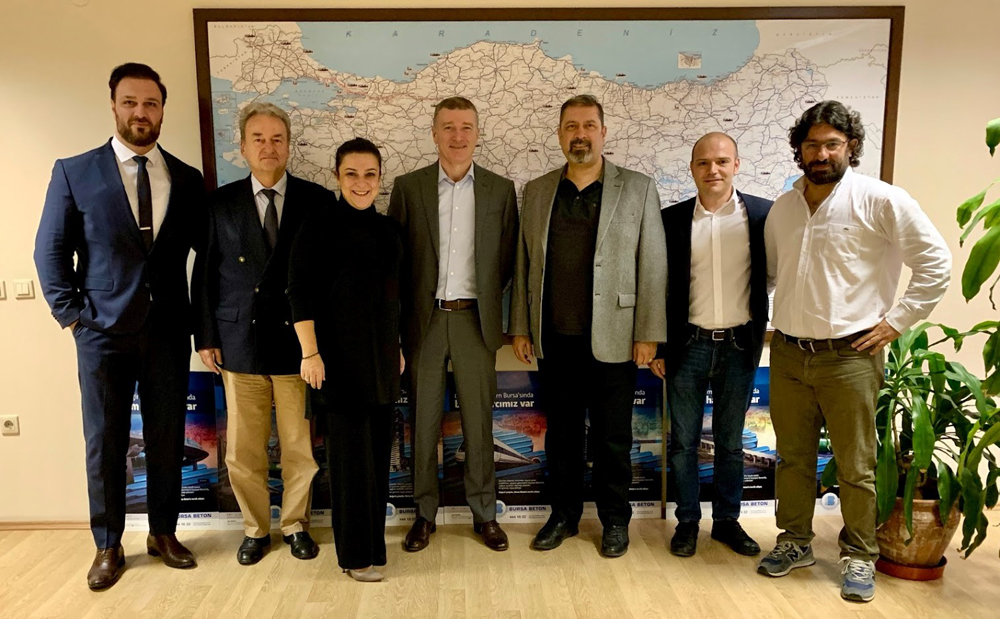
“AI is opening the door to create new solutions that efficiently offer more value,” said Javier Pigazo Merino, FLSmidth technical product line manager. “We are excited by the possibilities this brings to improve further the intelligence of our process control solutions, which is a big part of our commitment to make cement plants smarter, more productive and increasingly sustainable.”
Concrete-solutions provider Pan-United has achieved Singapore's largest two continuous ready-mix concrete pours in casting the raft foundation for a development project in the Labrador area of the island city-state.
The group's subsidiary, Pan-United Concrete, set a national record when it poured 18,916m3 for 57 hours non-stop from 31 October to 2 November 2020. This first pour was followed by a second pour of 18,342m3 of concrete in a shorter time of 42 hours non-stop, from 27 to 29 November 2020, to complete the raft foundation.
The mixer truck convoys delivered one truckload of concrete non-stop every 60 seconds. The total concrete volume of the two pours, at 37,258 m3, is equivalent to filling 14 Olympic-sized swimming pools. The previous record of 18,000m3 was in March 2015 for the Marina One raft foundation.
Ready-mixed concrete is produced just in time and typically has a brief two-hour workable lifespan. Pan-United designed a special concrete that remained workable for six hours to ensure the layers bonded integrally to form a solid raft.
The complex logistics planning for the production, delivery and casting of the raft foundation stretched over several months in close collaboration with Hyundai Engineering & Construction, the main contractor of the development.
Ken Loh, chief operating officer of Pan-United, said: "We are thankful to Hyundai for taking all the measures necessary to ensure safe distancing and to greatly reduce any health risks to the teams handling the massive pours. Pan-United also used our contactless processes such as e-delivery orders, e-concrete sampling, e-sign-offs, and our customer portal to minimise physical interaction at the worksite.”
Rapid International recently supplied UK ready-mix concrete company Eco Readymix with a new R3000 3.0m3 Rapid pan concrete mixer.
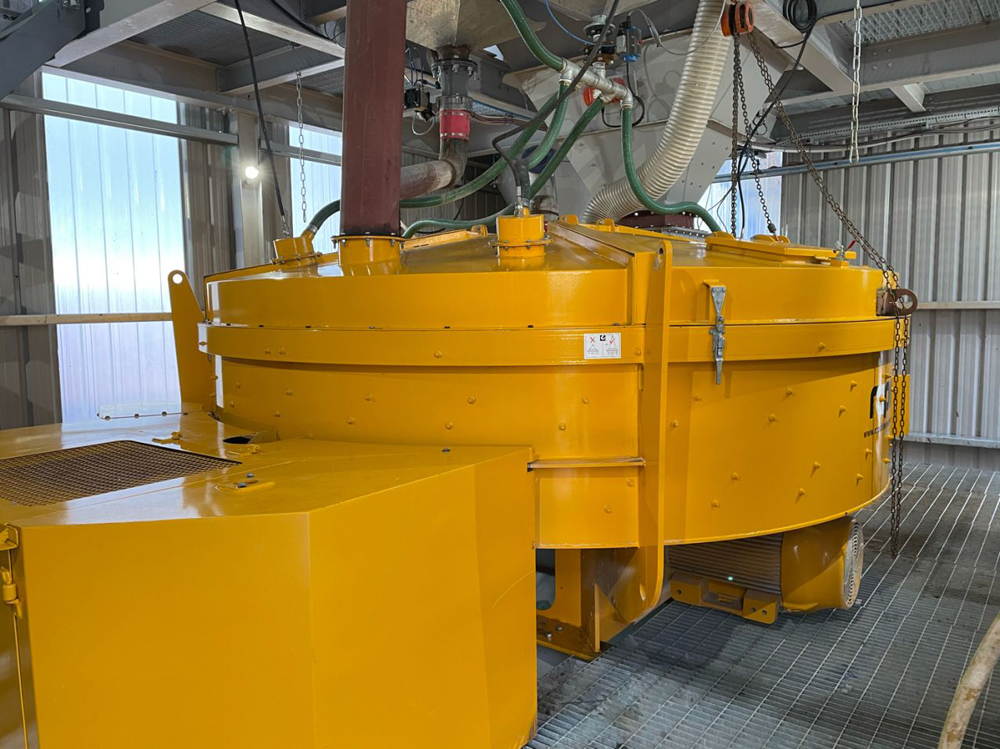
The mixer from Craigavon, Northern Ireland-based Rapid International forms an integral part of Eco Readymix’s new batching plant at its Ellesmere Port site and will produce circa 70,000m3 of material annually.
Trading for over three decades, Eco Readymix supplies eco-friendly, ready-mix concrete, mortar and floor screed to a wide range of customers, including leading construction groups. The company’s two depots in Wrexham and Ellesmere Port serve customers across north Wales and north-west England.
After experiencing an upsurge in demand and having been satisfied with the performance of its existing R1500 1.5m3 Rapid pan mixer, Eco Readymix approached Rapid to supply and install a new mixer, offering greater output levels and flexibility.
The new R3000 3.0m3 Rapid pan mixer, outputs 3m3 per batch and provides double batching, which Eco Readymix MD Gary Billington says is a big benefit for his company to increase its truck turnarounds whilst loading.
The Rapid pan mixer has been specifically designed with the ready-mix industry in mind, offering high outputs and fast discharge time. The pan’s mixing arms are designed to ensure all materials are kept in constant motion, in every direction, providing a thoroughly homogenised mix.