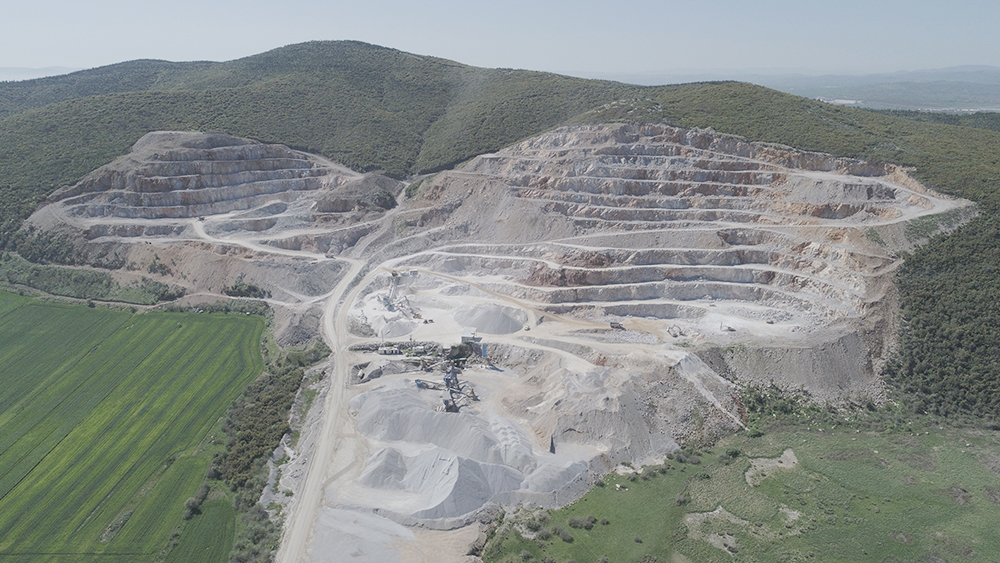
Turkey’s quarrying and aggregates sector is a large contributor to the country’s economic growth, social development and sustainability efforts. According to 2020 data, 67% of mining/quarrying production in Turkey consists of cement and construction raw materials. The local aggregates (cement feed and construction raw materials) demand was around 485 million tonnes in 2020, according to the Turkey Mining Industry Development Report (2020).
Data from AGUB (the aggregates producers’ association of Turkey) shows that 270 million tonnes of total production is used as crushed stone, sand, and gravel. Most aggregates in Turkey come from hard rock quarries (250 million tonnes), others are sand and gravel deposits (19.9 million tonnes) and marine aggregates (0.1 million tonnes). Aggregates-producing companies in Turkey are mostly SMEs operating in cities or nearby areas.
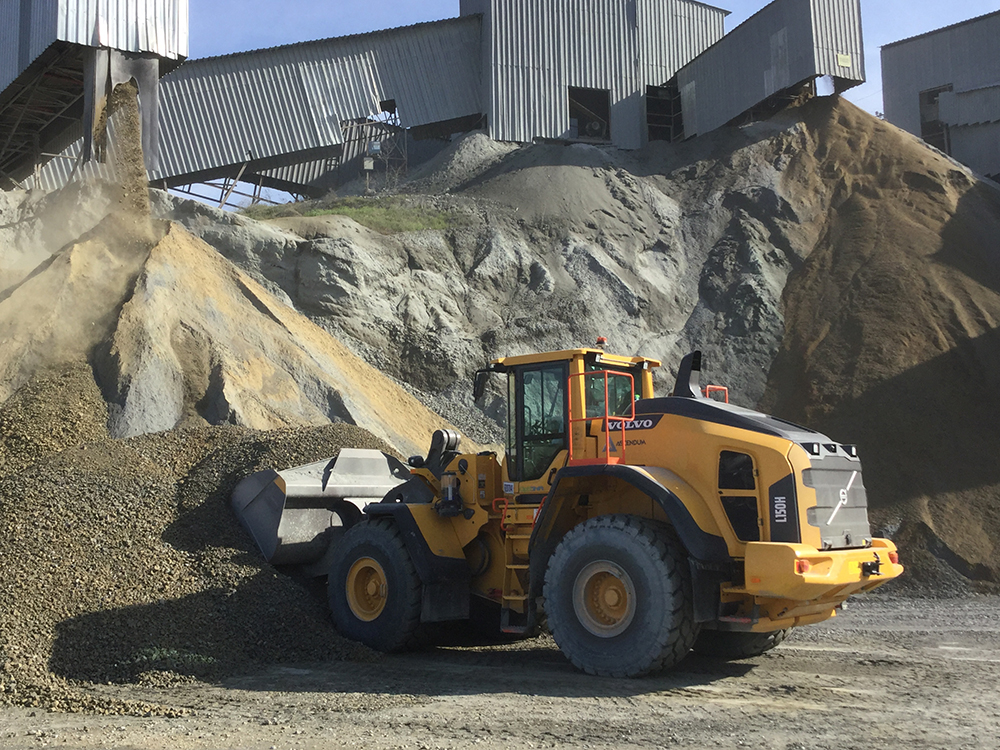
The Turkish aggregates sector comprises 1,155 companies (mostly SMEs) operating at 1,265 sites, with more than 12,500 employees, according to AGUB. The average aggregate demand (cement feed and construction raw materials) in Turkey is 5.77 tonnes per capita per year.
The aggregates industry faces a number of risks and threats to its continued healthy development that need to be addressed, according to Atiye Tugˇrul, honorary member of AGUB.
She says that one important factor for the sector is the sustainability of aggregates production in relation to mineral resources.
“Generally, sand and gravel deposits are being depleted or extraction is not allowed in some areas,” she adds. “Conflicts due to land use for quarrying are common all over megacities and the need for long-term planning is a pressing social, economic and political issue.”
Turkish capital Istanbul has a population of more than 11 million and is one of 33 global megacities (those with at least 10 million people), according to the United Nations.
Tugˇrul says that it is necessary to reduce the level of surplus materials: “The focus should be on zero-waste production in the aggregate industry. The transportation cost of aggregates from quarry to customer is increasing in Turkey, due to permit procedures and lack of aggregate resources within or in the vicinity of the megacities.”
There is a need for aggregates and crushed stone especially for residential construction projects in the country, according to Gökhan Kenar, commercial manager for the Middle East, Turkey & Cuba markets at Volvo Construction Equipment.
“Turkey is in an earthquake-prone zone and urban transformation projects have been ongoing for the last decade – demolishing old buildings and rebuilding them,” says Kenar. “The aggregates market has doubled within the last few years but the financial environment is turbulent so anything can happen. Nevertheless, we expect the increase in residential construction to drive some growth.”
Quarries in the Turkish market process a variety of hard and soft feed material. This means there is demand for all types of crushing and screening equipment depending on the makeup of the material and its intended end use, according to Dogˇan Özel of Northern Ireland-based wet processing equipment manufacturer CDE
“Most of the materials processors operating crushers are left with a significant volume of crusher fines and this material requires washing, or wet processing with technology like that which CDE designs and manufactures, to maximise its quality,” says Özel, who is business development manager for Turkey at CDE.
“The most commonly used fractions are 0-5mm, 5-12mm and 12-22 mm. 0-5 mm sand is typically washed in compact washing system which combines washing and dewatering in a single unit.”
The ongoing major risk of earthquakes in Turkey means that aggregates quality is a very important issue, according to AGUB’s Tugˇrul. This became even more important after the 7.4-magnitude earthquake on 17 August 1999 in Izmit, close to Istanbul, and other major recent earthquakes in different cities.
“Turkey has many old and big cities such as Istanbul, Izmir and Adana with many buildings constructed a long time ago,” says Tugˇrul. “Unfortunately, the quality of construction materials is far from the acceptable limits, and construction practices were applied poorly in these buildings. These factors are the main reasons for the damage and collapse of thousands of buildings in the big earthquakes. There are many projects and applications related to urban transformation in our country.”
Turkey is a country rich in aggregates-resource potential due to its geological characteristics. Therefore, Tugˇrul says there was no need for secondary and manufactured aggregates production with construction-demolition or quarry wastes in the process until about ten years ago.
She adds, however, that there are legislative deficiencies regarding the production and use of construction-demolition waste.
“The Turkish aggregate sector, especially producing in metropolitan areas or close to these areas, is today faced with not only a shortage of raw materials of expected quality but also a shortage of permits and long-term planning,” Tugˇrul says. “Businesses face more difficulties than ever before to manage all their bureaucratic requirements. Permitting procedures are very complex and lengthy. Limited access to available resources is getting more difficult day by day.”
Another important issue for the Turkish aggregates sector is the difficulty in evaluating the country’s potential in terms of aggregates exports, due to a shortage of ports and railways suitable for moving bulk cargo.
However, public authorities, AGUB, Building Materials Manufacturers' Federation (YUF), THBB (Turkish Ready Mixed Concrete Association), TURKCIMENTO (Turkish Cement Manufacturers’ Association), academics, exporters and other relevant institutions and organisations have increased their work on these issues, as well as in the process of harmonisation with the Paris Agreement international treaty on climate change.
In terms of the effects of COVID-19 on Turkey’s aggregates sector, Kenar of Volvo CE says that there was a very short period of slowdown in business at the start of the pandemic.
“This affected the aggregates business the same as other businesses, but the recovery has been quick,” says Kenar. “In general, during the whole pandemic period, business in Turkey was affected briefly in the beginning but then it has continued. It has not been affected as much as in some other markets.”
He adds that there are some major railway and road infrastructure projects that are having a positive influence on the demand for aggregates, but that Volvo CE expects the main growth driver going forward to be residential construction projects.
There have been many megaprojects completed in Turkey over the past 20 years, including the new Istanbul Airport; Yavuz Sultan Selim Bridge over the Bosphorus strait; Osman Gazi Bridge on Marmara Sea; Çanakkale Bridge over the Dardanelles; the Marmaray and Avrasya tunnels underneath the Marmara Sea, which connects Europe and Asia; and thousands of kilometres of roads across Anatolia.
Özel of CDE comments: “These are all multi-billion-euro projects which have been driving demand for sand and aggregates – and Turkey is still eager to enhance its infrastructure; from mega hospitals to urban transformation projects for large cities like Istanbul, subway projects in densely populated urban centres, the Istanbul Finance Center and the Kuzey Marmara Otoyolu motorway and its connecting roads.
“Istanbul is the only city in the world which has ten subway-line projects under construction at the same time. It has 265km of metro lines which will be extended to 450km in total after all active projects are completed.”
Özel adds that another megaproject, the US$15bn Kanal Istanbul scheme, is planned to be completed in 2027. It will see the development of an artificial channel connecting the Black Sea to the Marmara Sea.
Tugˇrul says the safeguarding of aggregates resources is one of the important aspects of sustainable development in Turkey, and that there is a need for national, regional, and local policies for aggregates.
“Due to increased pressure on land use in the big cities such as Istanbul, aggregate resources are under the threat of limitation,” she says. “On the other hand, new quarry sites often take several years to develop, and therefore strategic planning and new site development must stay ahead of actual growth.”
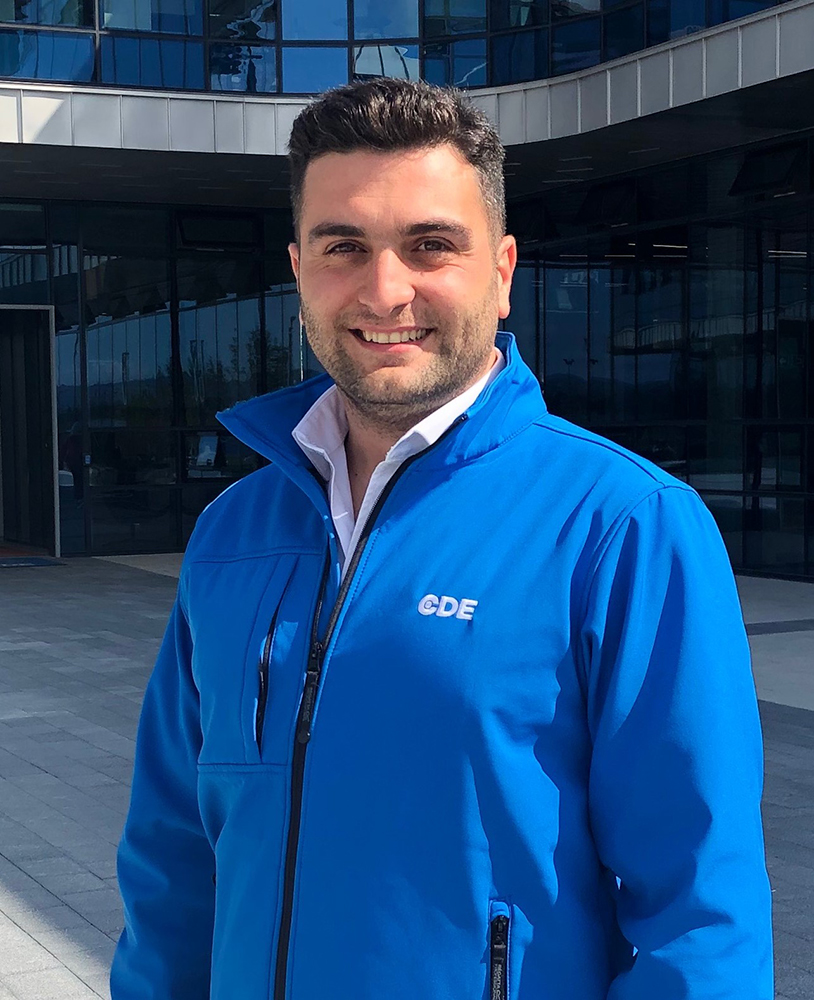
She says that it is also increasingly difficult to get permits for new aggregates sites or expand existing sites due to community resistance in some urban and suburban areas. This means that planning aggregates supply and sustainable resource management is essential, especially for megacities.
“Planning requires consideration of expected demand, aggregates resources, and constraints,” says Tugˇrul. “In addition, the current policy, legal and regulatory framework and its effectiveness, and many other variables should be considered. Regions should improve their aggregates planning processes, integrate planning for primary and secondary (manufactured) aggregates to increase resource efficiency, and raise communication among stakeholders, such as competent authorities, industry, and civil society with respect to aggregates management, planning and supply.”
Among the current challenges that the Turkish quarrying sector faces, Tugˇrul says most of the aggregates are bulky and heavy and difficult to transport efficiently. This means that shipping costs can quickly exceed production costs, and so the market for aggregates tends to be very localised around quarry sites.
In regions that do not possess commercially viable aggregates resources, materials are mainly transported by truck, with negligible amounts being transported by rail or ships.
“Due to the relatively high transportation costs inherent in the business, aggregate producers operate in a highly competitive industry within local markets,” says Tugˇrul. “Each type of aggregate is sold in competition with producers of different types of aggregates, as well as the same type of aggregate. Significant competition could lead to lower prices. Therefore, access to resources within the market is vital.”
As with other markets, Turkish quarry operators have an ever-growing need to take the environmental impact of their operations into account.
Tugˇrul says that in regions with many aggregates quarries in metropolitan areas, environmental and social problems are increasing day by day. She has played a central part in an innovative and proactive recent project to address this issue. Under the leadership of the Republic of Turkey Ministry of Energy and Natural Resources, the Istanbul Governorship and Istanbul Metropolitan Municipality have implemented the Cebeci Mining Area Project, which combined 16 quarries in the Sultangazi district of Istanbul that were causing environmental, social and mine safety problems.
The project was prepared by the Istanbul University-Cerrahpas¸a engineering faculty team, under the coordination of Tugˇrul, who says it is the first application in Turkey for urban areas that are on the way to becoming sustainable smart cities of the future.
She adds: “It covers many integrated applications (resource sustainability, resource planning, safe mine design, integration of aggregate quarries into the city, ensure urban security, energy efficiency, transportation, low carbon emissions, protection of water resources, reducing environmental impacts, co-production, evaluation of wastes, industrial symbiosis etc.) that can be an example for our country and world aggregate production activities.”
The aggregates production capacity in the Sultangazi district is planned at 24 million tonnes per year.
Commenting on current demand trends for quarry materials in Turkey, Kenar says there is a particular need for aggregates and crushed stone in residential construction projects.
He adds that Turkish quarry operators are looking for reliable equipment with high production and low fuel consumption. “Another important factor for quarry operators in Turkey is the quality of aftermarket support to ensure high machine availability and profitability,” Kenar says. “Our dealer in Turkey Ascendum Makina has an equally strong reputation for delivering superior service thanks to its wide network and highly competent staff.”
Looking at forthcoming trends in the Turkish market, Kenar says that, along with a continuing higher demand for aggregates related to residential construction projects, customers are looking for the best possible efficiency from their operations, so the company expects to see more operator training and site simulations taking place.
A survey of European construction contractors published by financial institution ING in February 2022 found that Turkey's issuance of new housing permits has been volatile in 2020 and in the first half of 2021. In the third quarter of 2021, it remained stable at a relatively higher level. However, this is far below that of 2017 before the Turkish exchange rate crisis which resulted in a big rise in construction costs and consequently a sharp drop in building activity in 2019.
“In addition, the next risk for Turkey is the primary concern at the moment of high inflation caused, in part, by the devaluation of the lira,” ING said.
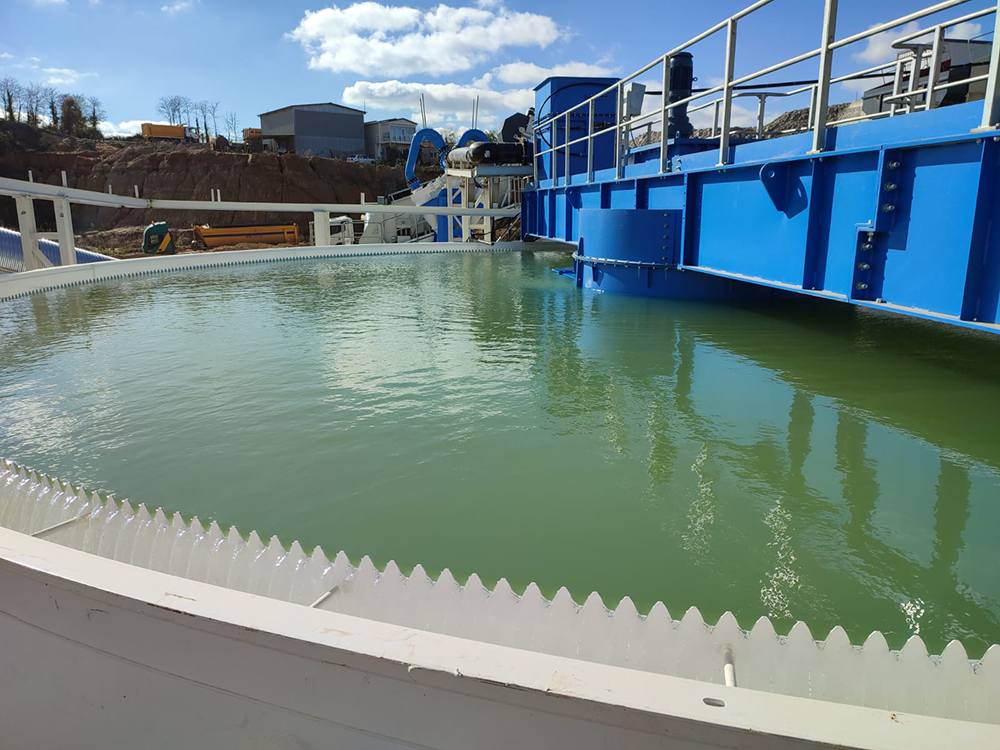
It adds that this high inflation could have particular ramifications for the Turkish construction sector this year. In November 2021, Turkish construction turnover soared by more than 50% year-on-year, mainly due to high inflation. Volume growth was consequently a lot lower.
“Demand for new construction is hindered by these high prices and we, therefore, diminished our growth expectations compared to our September forecast,” ING comments. “Still, there will be some low growth left for this year and next but output volumes won’t reach levels seen before the Turkish financial crisis.”
European construction association CECE’s annual report for 2022 stated that Turkey continued its recovery in 2021 from the catastrophic levels of decline seen in 2018/19, and saw the highest levels of construction growth across the European market regions.
CECE adds that construction equipment sales in Turkey went up by 63% last year thanks to deferred demand. Export value for the sector between January and November 2021 rose to US$1.598m, a growth of 23.6% from 2020.
Looking at the outlook for 2022, CECE states: “Even though making a prediction is still not easy because of the fluctuation in exchange rate, a size change between +10% / -10% is predicted in the Turkish construction equipment market for 2022.”
The Turkish economy faces ongoing challenges with the value of the lira nearly halving against the US dollar in 2021. Inflation in the country reached a 20-year high of more than 61% in March this year.
This has had inevitable implications for the country’s construction and materials sectors. In March the Turkish Statistical Institute reported that sector confidence in the construction industry fell to a level of 81 from 82.7. Any reading below 100 reflects pessimism.
Titan Cement Group says the current situation remains “challenging” in Turkey, exacerbated by the geopolitical turbulence on the Black Sea with Russia’s invasion of Ukraine.
“The outlook for the construction sector is highly dependent on the fortunes of the economy which remains under stress,” the manufacturer added.