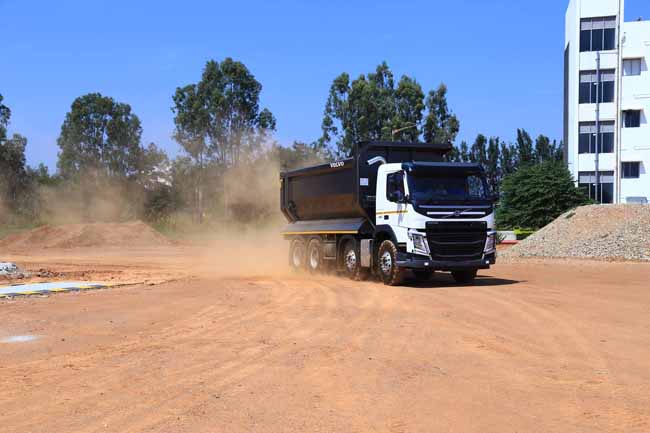
The Indian aggregates market is in fine health, creating a wealth of exciting commercial opportunities for suppliers and quarrying machine equipment manufacturers. Partha Pratim Basistha reports.
The Indian aggregates market continues to remain buoyant, as witnessed during the past three years. Robust demand stems from new bituminous and concrete road projects, ongoing railway infrastructure expansion and the construction of greenfield airports, all requiring colossal volumes of ballast.
The infrastructure growth story in India has created a surge in demand for mobile and tracked crushing and screening units, excavators, backhoe loaders, wheeled loaders and rigid dump trucks (RDTs). According to industry estimates, the size of the Indian excavator market is expected to be close to 25,000 units in 2018. Demand for 3tonne class wheeled loaders, predominantly used in quarry sites in India, is up by 30%, while 5-tonne class model demand is up 60% in 2018 compared to 2017.
Sales of RDTs have also been rising and manufacturers continue to launch newer hauler products, primarily for hauling granular sub-base materials, processed minerals and overburden. Sales of RDTs are expected to be close to 80,000 units in 2018, compared to 65,000 units last year. The market trend indicates a transition to higher capacity trucks, from 16tonnes to 25tonnes, and to 8x4 axle trucks with 31tonne capacities over 6x4 axle trucks offering up to 25tonne payloads. This transition has been noticeable during the past two years.
A key reason behind rising loader and hauler demand is due to pent-up demand, as contractors and equipment rental agencies held back from updating their fleets due to the reduction in infrastructure sector projects between 2011 and 2015.
Growing demand for crushing and screening equipment is driven by renewed high government-infrastructure spending coupled with the need to obtain higher capacity plants and machinery. There is a particularly strong demand for up to 300tonnes/hour mobile and skid mounted crushers and up to 250tonnes/hour tracked plants. Due to quicker setup times, tracked plants have been finding growing usage in infrastructure projects in India, as they can be set close to the actual work site for producing the granular sub-base materials.
Another very interesting emerging demand trend is value-based demand. Indian crushing and screening, extraction, loading and haulage equipment owners engaged in the mineral processing business are now increasingly looking for solutions that not only deliver exact levels of rated productivity, but also score highly on lowering operating costs. This is fuelled by contractors’ desire to complete infrastructure projects early, triggering bonus completion clauses.
Abhijeet Pai, president of Puzzolana Machinery Fabricators, a major South India-based crushing and screening plant manufacturer, said: “Flexibility, faster setup times, and, most vitally, low cost of productivity per tonne are the new major demand trends. This is also being increasingly characterised by demand for larger-sized skid and mobile plant to crush granular sub-base materials. We have recently introduced a 400tonnes/hour crusher of -22mm products utilising single line operation. We have also come up with a PCC 33150 up to 500tonnes/hour cone crusher for secondary applications.”
For delivering higher production rates and longer service life in jaw crushers, Puzzolana Machinery Fabricators has introduced an extended grizzly bar section for removal of -75mm material from the feed. The firm’s jaw crushers also feature a new anti-clogging mechanism, new design jaw plates and a higher grade of manganese steel castings. To avoid blockages in bigger size jaw crusher plants, Puzzolana has introduced a rock breaker with extended boom design for breaking oversize boulders.
Pai added: “Based on the requirements of crushed aggregates with high cubicity, dovetailed with high productivity and low cost per tonne, we have improvised the rock-on-rock design in our vertical shaft impactors (VSI). Heavy-duty bearing cartridge design has been made in the impactors, resulting towards increment in tip speed. Further, for reduced power consumption in our mobile and skid design plant, we have improvised the automation in operation and monitoring of vital parameters in the main equipment models like jaw, cone and VSI and screens. The initiative has also gone towards plant optimisation and improvement in productivity. Our diesel electric track crushers are highly fuel efficient compared to competition offerings.”
Pai continued: “We have optimised the design and configuration of plant as the need for finer -20mm aggregates and manufactured sand is rising. This will ensure best power utilisation and cost/tonne of production.”
Enabling faster setup and dismantling, Puzzolana has been carrying out improvisation on standardisation of structures, chute and conveyors. Pai said: “Standardisation of skid design will enable faster erection with minimum civil works and easy dismantling.”
Puzzolana manufactures standard stationary/skid plant handling -40mm aggregates and capable of producing up to 1,000tonnes/hour of final grade material. The company also recently introduced 250tonnes/hour, three-stage track plant. The crawler units are working for the greenfield Navi Mumbai airport project in western India. They have also been supplied to municipal projects for recycling of demolition materials.
Another South India-based, Indian crushing and screening solutions manufacturing major, Propel Industries, has set up a new plant for production of tracked crushers, close to its existing facility producing stationary plant. The new facility is fully equipped with fabrication including plasma cutting machines for cutting steel, computerised numerical controls machining units, a paint shop and testing facilities. It will be producing TMC Q 250/ TMC-C 250 tracked 200-320 cone crushers, powered by
“Our new track plant will be targeted at road contractors and commercial aggregates producers. The dual-powered diesel electric plant score over other competition offerings where the engine drives the hydraulics and the hydraulics powers the machines. In our new simplified tracked solutions, the generators would directly drive the motors, thus making power transfer more efficient. This would make the machines more fuel efficient and reduce maintenance and overall deliver higher productivity,” said V. Senthil Kumar, CEO of Propel Industries. Propel has launched its new PFS 955, PFS 1161, PFS 1365 and PFS 1680 feeder screens, that can take feed sizes between 560-750-900mm and 1200mm. The new solution is a combination of feeder and grizzly screen.
GR Infraprojects, a leading Indian road and general infrastructure contractor, has recently added a new
GR Infraprojects has its own crushers producing around 15-20,000tonnes/day of aggregates at its varied projects. The construction firm has six direct and exclusive sub-contractors for four crushing and screening plants, with some, according to Agarwal, having clocked up around 10,000 hours of operation.
GR Infraprojects is the first and new owner of a Terex FM 120 Conexus plant – a modular sand classification, dewatering and water recovery unit from Terex’s new Hosur facility near Bangalore in South India.
Acquisition of wet and dry process solutions for producing manufactured sand is a new trend in the Indian crushing and screening industry. Rising restrictions on the mining of river sand is helping fuel demand for manufactured sand. According to industry estimates, almost 50% of demand for manufactured sand is coming from the road and general infrastructure sector. Nuclear plants due to be built in India will require an estimated 12million tonnes of sand.
Puzzolana is marketing its standard sander and vertical shaft impactor (VSI) plant which operates on a floating shaft principle. The sander can be installed in the crushing plant as a standalone unit to produce sand. The manufacturer is also promoting its dry and wet classification solutions to separate fines generated during production of sand.
Propel Industries is providing standard VSI and jaw-cone and fine-cone configuration Sandmaster plant. It is also promoting its wet Hydrocyclone and air classifier systems (dry process). Senthil Kumar, the company’s managing director, said: “In the Sandmaster, the cone crusher can be converted for producing manufactured sand by simply changing the concave mantle. This flexibility is a unique benefit as it enables plant operators to get optimum results.”
Demand for higher capacity crushing and screening plant and supporting equipment is also raising the level of fleet and plant lifecycle support services offered by original equipment manufacturers.
Rajib Lochan Datta, head – service operations & officer on special duty to directors at Caterpillar’s India dealership, Gainwell Commosales, said: “Equipment owners are increasingly looking to rationalise the high levels of capital costs they are presently incurring. This is due to the growing advanced machine attributes and higher levels of instalment liabilities, owing to the rising loan borrowing costs from banks and non-banking financial institutions in India. To offset these factors, different equipment manufacturers are looking to make their pre- and after-sales product support services competitive. This is becoming a major trend in the increasingly competitive Indian construction equipment market.” The India dealership of Caterpillar since June 2016, Gainwell Commosales is also the new Caterpillar dealer for Eastern, North-Eastern and Northern Nepal and Bhutan.
Though demand should continue to remain firm for crushing, screening and plant support equipment, volatility in oil prices, sharp rupee depreciation and rising borrowing costs by the Central Reserve Bank of India, due to tightening monetary policy, are some of the factors that may create aberrations in demand. India’s GDP (gross domestic product) growth for 2019-20 has been pegged at 7.3% as compared to 7.4% in 2018.
Jaideep Shekhar, managing director of Terex India, said: “There remains a higher pressure on production costs. This is due to rising costs of steel and also other consumables. Further pressure is also due to the depreciating rupee as almost 20% of the components are imported including programme logic control units, hydraulics and engines.”
To neutralise the impact of rising production costs, crushing and screening equipment manufacturers such as Terex India are looking to incorporate efficiency in production.