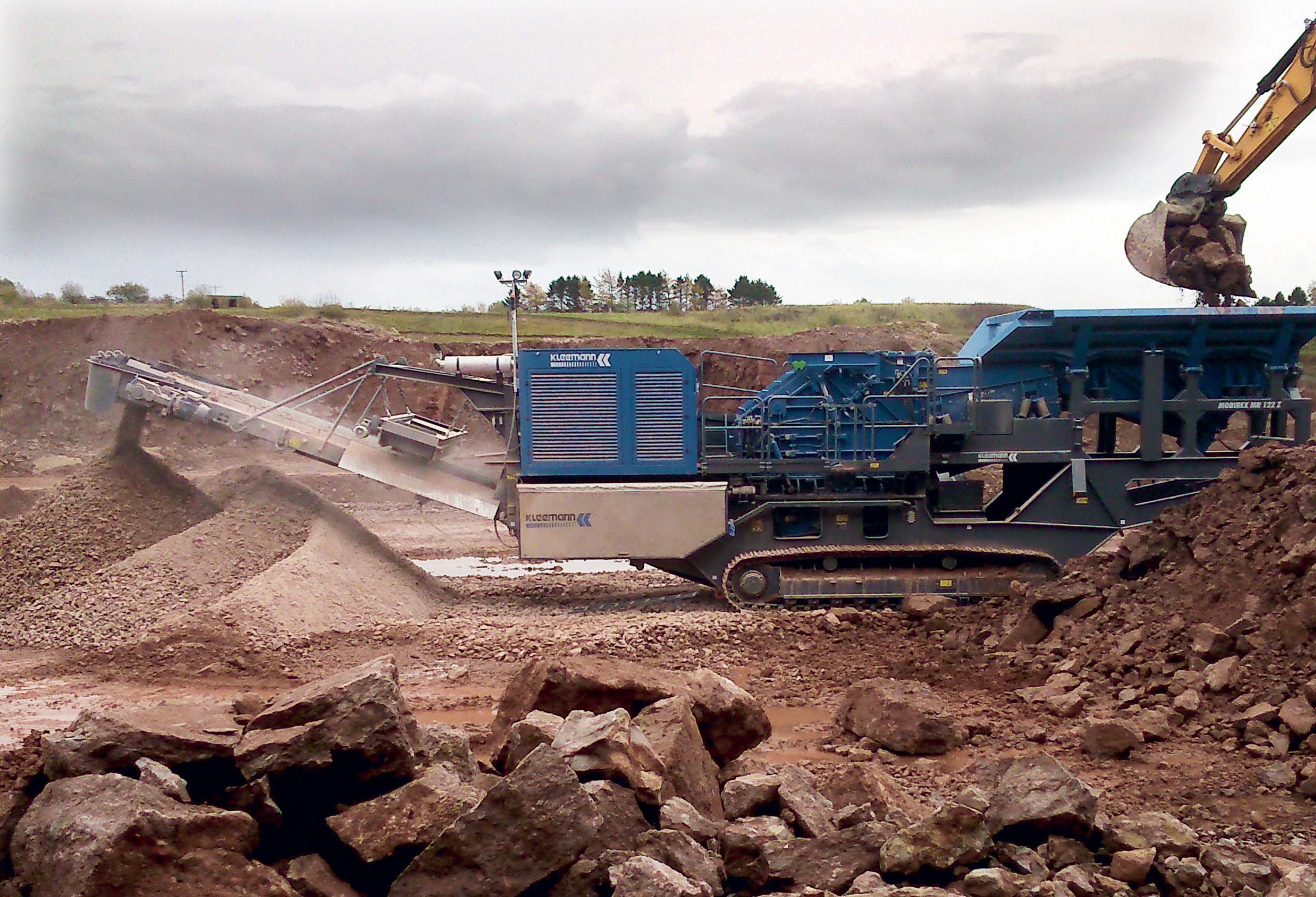
With a MOBIREX MR 122 Z impact crusher from Kleemann, the Scottish quarry operator Grange Quarry has recently strengthened its fleet of machines.
Founded in 2000, Grange Quarry is now one of the largest manufacturers of high-quality aggregates and ready-mixed concrete in the south of Scotland and the north of England.
For Grange Quarry, the MOBIREX MR 122 Z impact crusher is not the first plant that it has acquired from
““Since 2012, we have been working successfully with a mobile MOBICAT MC 110 Z jaw crusher and we are really impressed with the quality of the crushed end product,” says Stuart Dodd, owner and managing director.
The mobile plant is used to crush whinstone at Grange Quarry, Lockerbie, for road construction with a maximum feed size of 600mm to 125mm at an output of around 200tonnes of crushed material per hour.
Since 2012, Grange Quarry has also been developing Kelhead Quarry near Annan. At this site, a plant from Kleemann is used to process the stone.
The new MR 122 Z impact crusher has been in use since October 2013 and crushes limestone breccia of 600mm that is produced by the blasting to a final grain of 60mm. With an output of around 220tonnes/hour, the crushed stone is mainly used as concrete aggregate and to produce a high quality crushed rock sand.
The crusher, with its 250kW electric drive, which is supplied by a 364kW diesel engine, crushes heavily reinforced concrete just as easily as limestone blocks. This means that the MR 122 Z crushing plant is also ideal for concrete recycling.
“Another advantage is that the standard vibrating discharge chute under the crusher reduces wear on the crusher discharge conveyor and thus significantly increases the operational safety of the plant,” says Kleemann.
The high level of reliability is said to be one of the decisive factors in Stuart Dodd again investing in a plant from Kleemann. But he is also impressed by the crusher technology and the quality of the granulation.
“The crushed stone has an outstanding cubicity,” says Dodd.
In addition, the entirely electrical drives ensures the economical operation of the plant. Experiences in the Kelhead Quarry are said to underline this.
“The MR 122 Z consumes around 35litres of diesel per hour compared to our previous impact crusher of the same size using 60litres per hour. This means that we can keep costs under control and also do something for the environment.”
Maintenance of the plant was also an important point to consider for the quarry operator.
The Kleemann plants have easily accessible maintenance points, and service is provided by the Wirtgen Group. Grange Quarry’s maintenance needs are taken care of by the Wirtgen Limited subsidiary, which has its headquarters in Lincoln, eastern England, and which is responsible for sales and after-sales service for Kleemann crushers in Great Britain.