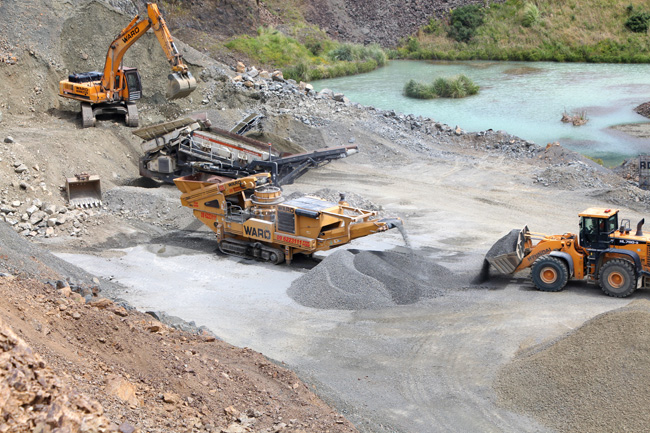
Trimble showcased its state-of-the-art Connected Quarry solution at the recent bauma 2019 exhibition in Munich, Germany (8-14 April). A key element of the solution is the company’s LOADRITE LR360 connected loader scales for quarry loadout.
Speaking to Aggregates Business during bauma 2019, Jérome Thomas,
“As well as the loader, the LR360 system can also be added on to a dump truck – for further payload weighing analysis,” said Thomas. “We can also create a geofencing capability at the quarry, so users can find out how many tonnes of a particular pit material source has been loaded and how much of it has been taken to a stockpile or the primary crusher. It can track all a truck’s movements, including how much time a truck is spending in a loading area, how much time it is taking to load, how much time it is travelling. This helps operation teams find out whether they have any machine efficiency issues.”
Thomas said that he was working with a customer who had installed Trimble’s complete Connected Quarry system on their site. “They had been using an old 45-tonne excavator and were thinking about purchasing a 75-tonne excavator. We’ve managed to show them through Connected Quarry that their excavator is loading 60% of its work time. When it’s loading, it’s loading an average of 370 tonnes of material an hour. So, we said ‘Is it worth investing in a 75-tonne machine?’ The customer is instead going to invest in a new 50-tonne machine which will perform better for them. This shows how our solutions can help with identifying both the correct loader or truck sizing for a job site and how a customer can go about maximising productivity.”
Despite being long-established in the mining sector in South Africa and other countries, the LR360 system is said by Thomas to have been adopted by aggregates quarry operators over the past two years. “We are attracting a lot of customers in Europe. In France, for example, we have 12 quarries using it. For a small site, you can do away with the gate house and the weighbridge as the LR360 scale can be legal for trade. It also helps on big quarry sites which have 500 to 600 truck loads a day and you don’t want trucks idling while they wait to receive material from a stockpile. The LR360 gives you faster turnaround of trucks by offering a clear visibility of what’s happening.”
Another key part of Trimble’s Connected Quarry offer is its InsightHQ quarry management portal for web browsers and mobile devices. It shows near real-time productivity, availability and performance dashboards and reports for extraction, processing and load-out. To view changes over time, users can adjust reports to suit either the shift, day, week, month or year.
Thomas said the fastest adopters of the Connected Quarry offer have tended to be mid-sized quarry operators, due to their ability to make quicker investment decisions than larger businesses containing a bigger executive management structure.
Trimble is also looking to increase the number of quarry operators using its Groundworks drilling system. The system is said to pay for itself in just four months by drilling to exactly the depth you need, reducing overdrilling and prolonging the life of drill bits and hammers. Groundworks is also said to drill evenly spaced holes and angles, creating an even blasting pattern that delivers better surfaces and improved rock fragmentation, leading to reduced hauling costs.
Trimble Groundworks is also said to increase site safety as users can see machine blind spots and warn the operator when he’s working where he shouldn’t be. The system also reduces time and money spent on site surveying.
“We are looking closely about who we need to be targeting for this system as quite a few quarries sub-contract their drilling and blasting work,” explained Thomas.
Already proving a hit with many civil engineering contractors and construction companies globally, Trimble Stratus is Trimble’s drone data processing system that Thomas believes can also benefit quarry operators. Its software can help quarry managers use drones to map, measure and share accurate information about their worksites and machine assets. This may include calculations of aggregates stockpile inventory, proof-of-site topography changes, haul-road berm monitoring and quarry mineral reserves assessment. With Stratus, Thomas explains, users can make quicker decisions, avoid mistakes and grow profits by always having the right information to hand.
“To create Trimble Stratus, we have partnered with an Australian [drone data and analytics technology] company called Propeller,” explained Thomas. “It’s having a phased introduction and our distributors are currently being trained in its capabilities. It has huge potential for quarry operators. A good sales guy calls in with a big new aggregates order and can accurately be told the timescale with which it can be met, and which sites can provide the material. If the new big order is going to become a regular order, Trimble Stratus can help the firm in question properly plan how it can be met.”