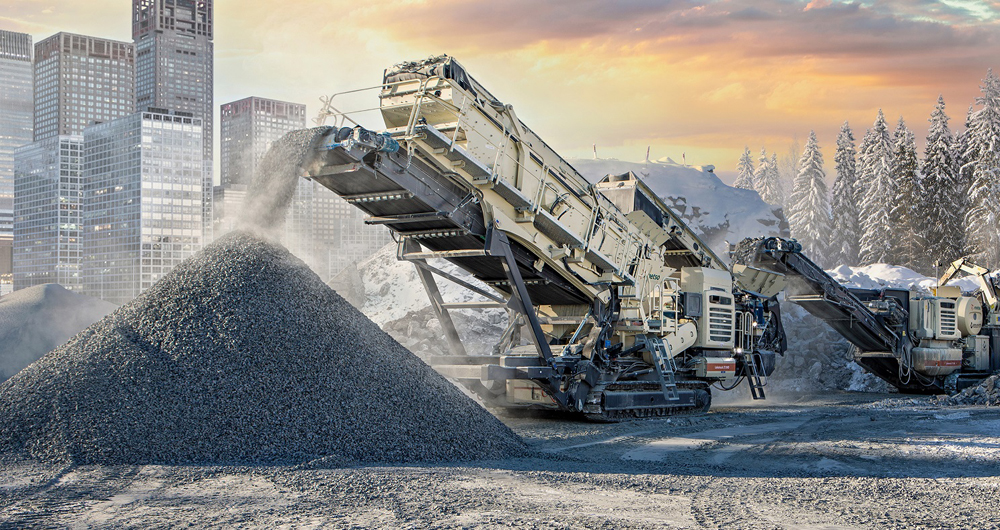
Metso Outotec’s new Lokotrack e-Power range brings the diesel-electric Lokotrack mobile crushing and screening units into one distinctive offering. The range includes 15 crushers and six screens, making it the market’s broadest portfolio of hybrid mobile crushing and screening equipment.
“We introduced the first Lokotrack E-models already 35 years ago, so we are one of the pioneers in this field,” says Kimmo Anttila, vice president, Lokotrack solutions at Metso Outotec. “During the past couple of years, the demand for hybrid solutions has really taken off as environmental regulations have become increasingly stringent in more countries. In fact, sales of the Lokotrack E-models have doubled in five years, and we expect the trend to accelerate.”
The Lokotrack e-Power range is an important factor in realising the goals of Metso Outotec’s Planet Positive initiative. With Planet Positive, Metso Outotec is committed to limiting global warming to 1.5°C. Aggregate crushing is very energy-intensive; thanks to the development actions to lower fuel consumption, the annual CO2 emissions of the Lokotrack equipment are 20,000 tonnes lower today compared to the situation before 2010.
“Lokotrack design principles are simple: optimise the operating costs, capacity, and end-product quality of the customer application. We give consideration to the total fuel consumption, including the engine and driveline technologies, but also to other factors, such as the unit transportation weight and the engine stand-by function,” Anttila explains.
“Additionally, we have reduced the hydraulic oil and lubricant volumes by more than half to further ease the environmental burden. Based on our data, a Lokotrack unit uses as much as 80% fewer oils compared to our previous models and compared to many other brands on the market. Naturally, the hybrid driveline reduces the need for oils and lubricants even further.”
He concludes: “A diesel and hybrid offering complete each other; in remote locations where the power grid is not available, a diesel driveline is still the only viable solution. We are investing heavily in the development of sustainable technologies. Lokotrack is robust, energy-efficient, and highly mobile – and it meets the versatile needs of customers today and tomorrow.”
Powerscreen’s electrification strategy now includes an exciting new concept for the future of crushing and screening—the Eco-Warrior battery-powered screener.
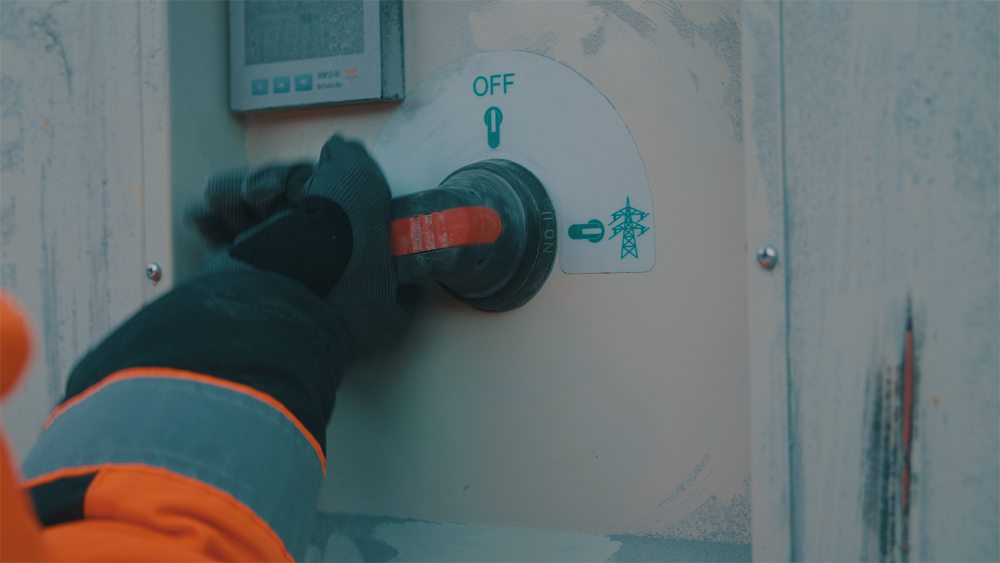
Neil Robinson, Powerscreen product and applications manager, said: “Some may view this topic as a recent trend, but for Powerscreen, decarbonisation is multi-faceted and has always been at our core. The Powerscreen mobile concept has always contributed towards decreasing the carbon footprint per tonne of material produced. This is done by reducing unnecessary material handling of hauling and loading material to static plants in aggregate production or in the ability to recycle and reuse material at point of use, for example, in roadbuilding projects where sub-base material is produced in situ. Using stockpiling conveyors as part of a track mobile set-up is another perfect example of how to cut out unnecessary double handling, reducing fuel consumption and therefore carbon production.”
Powerscreen has evolved its product range to reduce environmental impact by making its crushing and screening equipment as fuel-efficient as possible, using direct drive systems for its crushing range and improving engine capabilities and driveline design for its screening range.
Robinson explained: “Direct drive systems are proven to be 13-18% more fuel-efficient when compared with hydrostatic, resulting in significantly less carbon emissions, while improvements to our screening range have reduced engine speeds from 2,200rpm to 1,800rpm, which not only means cleaner engines with less emissions but also reduced fuel usage and therefore carbon produced. For example, a typical mid-size screener running at 1,000 hours per year has a fuel usage reduction of approximately 450 litres, which equates to 1.2 tonnes less of carbon produced annually.”
Another important tool for fuel efficiency is Powerscreen Pulse, in-depth machine telematics that help customers see how and where their machines are being operated, understand fuel consumption and carry out fault-finding activities to ensure optimised performance.
“Powerscreen was the first mobile crushing and screening manufacturer to offer in-depth machine telematics with the launch of Powerscreen Pulse in 2013,” continued Robinson. “In the early days, it generated a large volume of data, but now our system has been refined to deliver actionable information with customised reports and suggested actions for more fuel-efficient operation.”
Electrification is currently a key focus of the Powerscreen decarbonisation strategy. The Powerscreen Hybrid range, designed to give customers alternative energy options to operate their range of crushing, screening and conveying equipment, has been dramatically enhanced to include more fully electric crushers and screeners and models powered by innovative combinations of diesel and electricity. These options enable customers to choose which fuel to use, depending on cost, location and availability, and are of particular benefit to customers who operate in an area where electricity is more cost effective than diesel fuel, where diesel engine noise is unwanted or on sites where electricity is the preferred energy source.
Robinson added: “Customers using Powerscreen Hybrid units powered off the grid have been able to reduce on-site carbon emissions by 57% per tonne of material produced. While our hybrid customers have traditionally been in environmentally conscious countries and states, where legislation or financial incentives are more focused on green energy, we are witnessing a significant uptake in non-traditional locations, as customers prepare to comply with increased government drives for carbon neutrality.”
Working closely with automotive technology and using top-of-the-range, hyper-efficient drives and intelligent control systems, Powerscreen’s Eco-Warrior battery-powered screener has been designed to deliver on the powerful screening action that the Terex brand’s machines are famous for while being a self-charging or plug-in model that features a simple, quiet engine with no after-treatment requirements. The required engine size has been cut in half compared with the diesel-hydraulic unit, and the battery pack can mean emission-free running or give a power boost.
Robinson said: “To the best of our knowledge, this is the first battery-powered screener in the world and has been clocking up testing hours since it was built in 2019. It still delivers on the powerful screening action that Powerscreen machines are famous for, and we are now exploring taking it from concept to mainstream.”
Concluding, he added: “This isn’t a publicity stunt; the drive for decarbonisation is real, with the UK and other governments ruling that carbon emissions have to be reduced by 80% by 2050. It’s critical that we dramatically reduce our carbon footprint, and Powerscreen has many solutions available today in support of this. However, we’re not stopping there—we’re taking it to the next level, continuing to be the pioneers in adopting technology that supports the industry in meeting the requirements of government decarbonisation laws—this is the future.”
Sandvik jaw crushers are now delivered to quarrying, mining and construction sector customers with everything for plug-and-play installation.
“We deliver our jaw crushers with everything a customer needs for plug-and-play primary crushing operations,” says Mats Dahlberg, vice president lifecycle service, stationary crushing and screening. “It’s just to choose what extra components they require. There’s also a wide range of jaw plates that can be mixed and reversed to ensure optimal, versatile crushing.”
Sandvik says safety and sustainability are the global off-highway equipment giant’s priorities. A company spokesperson said: “We use the highest quality materials and parts in our equipment, while including lifting tools, guarding retraction and a modular maintenance platform for safe operation and maintenance. All Sandvik jaw crushers are built for the circular economy, meaning the complete machine – all the metal and rubber seals can be recycled.”
All new Sandvik jaw crushers are available with the Sandvik Reliability and Protection package, said to always keep customers in control of costs and efficiency.
“To continue as a leading global supplier, we now include everything our customers need for a fast start-up and reliable operations. Together with easy and safe maintenance, our jaw crushers increase productivity, offer true reliability and excellent availability,” says Martin Johansson, product manager, Sandvik jaw crushers.
Sandvik jaw crushers can be delivered with complete infrastructure including feed hopper, feed hopper interface, drive and subframe with v-belt guard and motor bracket, an innovative guarding retraction arrangement and toggle plate stop.
With the launch of the new MOBICAT MC 110(i) EVO2, Kleemann presents a mobile jaw crushing plant of the new generation. The further development of the tried-and-tested predecessor plant is said to offer users groundbreaking technologies for optimising all areas of a typical workday.
In designing the new jaw crusher, Kleemann says it concentrated on the requirements of demolition and building companies, contractor crushers and quarry operators. With an hourly output of up to 400 tonnes per hour, the new mobile jaw crusher meets the requirements in the medium output range. It delivers an impressive performance in a wide variety of quarry and recycling applications, emphasising effective coarse crushing.
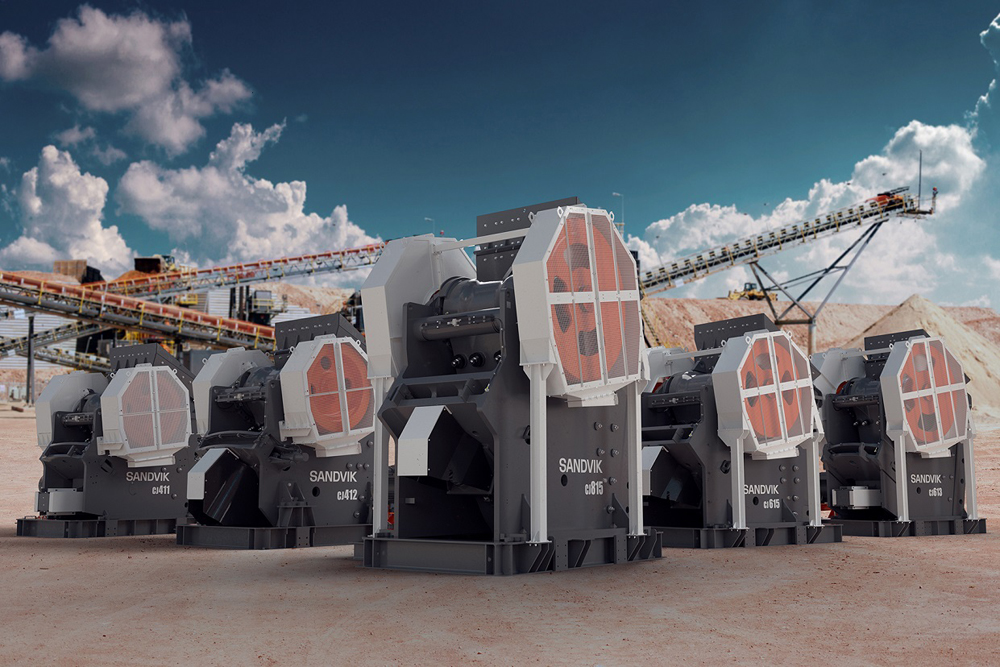
The development engineers at Kleemann’s main Göppingen, Germany factory wanted the MOBICAT MC 110 (i) EVO2 to give customers optimum transportability and a fast start-up. The model’s transport height was reduced by 20cm compared to its predecessor to 3.40m. Relocation is now possible with simplified transport utilising semi low-loaders. The start-up procedure itself takes only around 10 minutes and includes set-up times for flaps, belts and feed hopper.
A special highlight of the MOBICAT MC 110(i) EVO2 is a new effective two-stage overload system. It effectively prevents blockages and material bridging that can lead to unwanted downtimes. If uncrushable material enters the crushing process, the CSS (closed side setting) opens two times faster than with the predecessor plant or, as an option, even up to 40 times faster. This increases the availability and thus the overall output.
With the further development of SPECTIVE, Kleemann says it has set standards for user interfaces in the sector even higher. This digital operating concept has an intuitive structure and revolutionises plant operation with its extensive features. The 12-inch touch panel offers optimised user guidance and visualisation. Furthermore, new components such as a radio remote control and a small radio remote control have been integrated into the SPECTIVE world. The new digital solution SPECTIVE CONNECT sends all-important plant data to the smartphone.
In the new MOBICAT MC 110(i) EVO2, Kleemann has integrated a series of new technologies and improvements. The CFS (continuous feed system) guarantees continued crusher utilisation for daily outputs up to 10% higher. The independent double-deck prescreen effectively separates fines before they reach the crushing process. This increases the total plant throughput and is gentle, for example, on downstream cone crushers in the second crushing stage. Improved feed behaviour is guaranteed on the one hand by the extra-long articulated crusher jaw, whereas a flattened transition to the crushing chamber makes an optimum material flow possible. The accessibility for fast, safe and convenient maintenance has also been optimised.
With its innovative technical solutions, Kleemann concentrates on energy efficiency in all its new and further developments. The company’s improved diesel-direct drive concept can be seen in the MOBICAT MC 110(i) EVO2’s economical use of fuel, minimising operating costs. The plant’s output-dependent fan guarantees an increased cooling capacity, works when required and reduces fuel consumption. With its forward-looking, innovative technologies, Kleemann says it prioritises sustainability and lower customer operating costs.