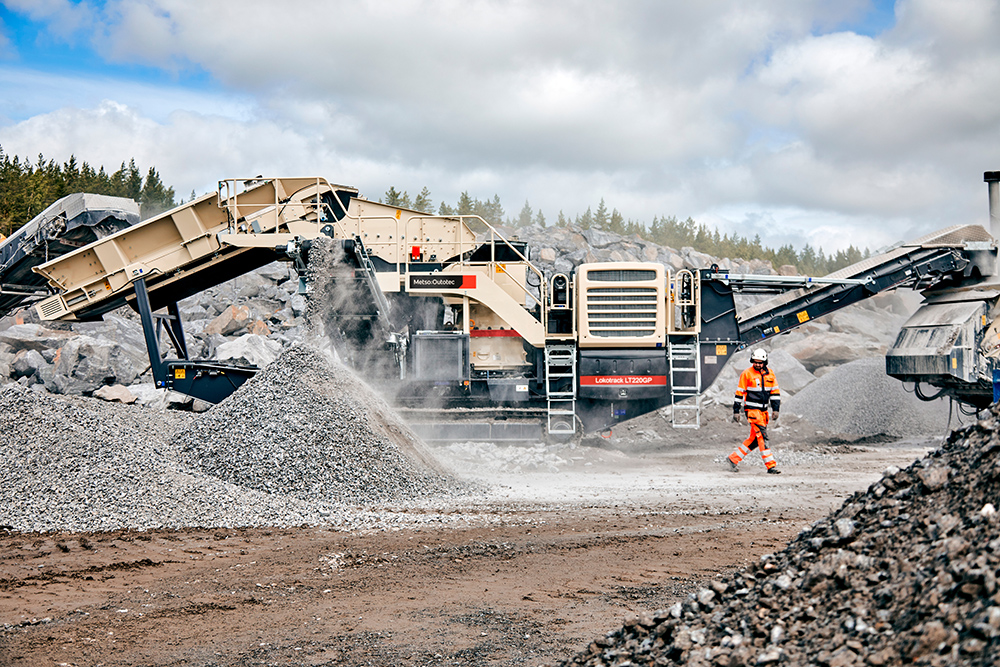
Metso Outotec is developing a full range of electrically driven track-mounted crushers and screens in response to what it says is a growing demand for sustainable plant solutions.
The Finnish manufacturer adds that its new Lokotrack range will be built on an innovative platform that it has been developing since 2020 with a total R&D investment of €20m. The development work will primarily occur at Metso Outotec’s technology centre in Tampere.
The platform concept has now been developed, and Metso Outotec is currently entering the design phase of the first new products. The new Lokotrack range will be transformational for the whole aggregates industry of mobile crushing and screening. It will also significantly contribute to Metso Outotec’s Planet Positive strategy and commitment to reaching the 1.5OC climate target.
“The next generation Lokotrack range will address the needs of our crushing and screening customers by providing new easy-to-use diesel-electric equipment,” says Renaud Lapointe, senior vice president at Metso Outotec’s aggregates business area. “The possibility to run track-mounted machines from an integrated genset or connect to an external power source lowers operational costs and allows access to renewable energy for our customers,” he continues.
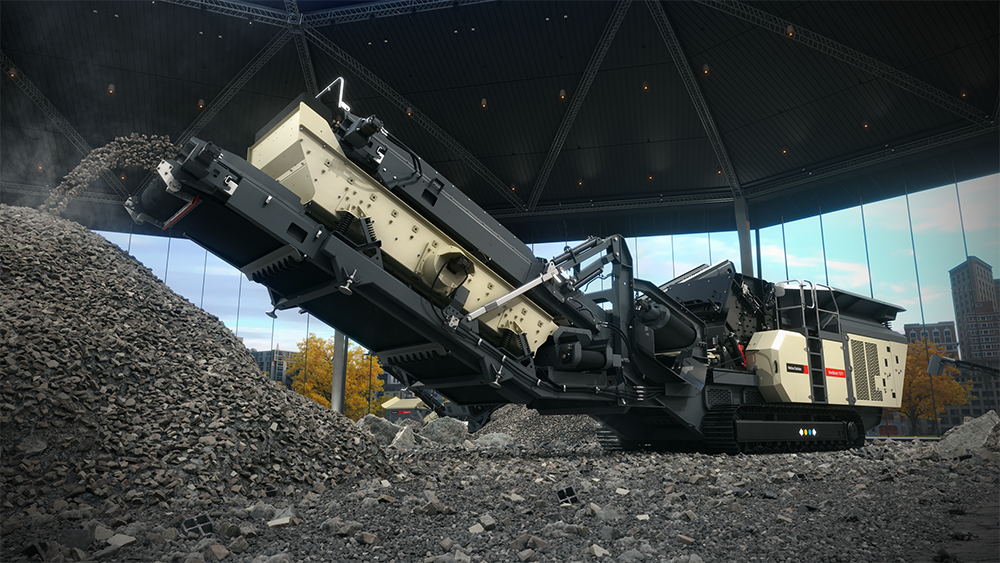
The new unique platform will enable a faster and more agile way to develop products and reduce the number of components. “Using one common architecture throughout the range allows scalable solutions that can be seamlessly combined and adapted for different applications and capacities,” says Jarmo Vuorenpää, director, new Lokotrack offering, aggregates business area at Metso Outotec. “Harmonised design together with advanced digital solutions enables our global service network to support the customers throughout the entire equipment lifecycle.”
The concept of track-mounted crushers and screens was developed in Finland in 1985 to minimise the cost and energy use. The idea has grown significantly during the last 35 years, with thousands of units manufactured and sold globally every year. Lokotrack has made it possible to provide on-site mobility close to the processed raw materials, lowering transport and hauling costs and emissions.
In a separate move, Metso Outotec has added a new impact crusher to its Nordtrack mobile crushing and screening range, targeting especially smaller-sized applications and jobsites in the construction- and demolition-waste-recycling segment.
The Nordtrack I1011 mobile impactor has compact dimensions and a powerful, high-performance crusher, ideally suited for contractors and rental work. Equipped with a large hanging screen, it combines high crushing capacity with calibrated end-product accuracy.
The versatile Nordtrack I1011 crusher is suitable for working in different jobsites from rock crushing to concrete- and demolition-waste-recycling. It is transported on a standard trailer, making it cost-effective and quick to move between sites. Metso says that, thanks to its agility, moving the equipment in tight places inside the jobsites is easy. The company adds that, with its service support and global inventory of parts such as different blow bar options, Nordtrack I1011 is a dependable choice for contractors and as a rental machine.
“We have listened to the feedback from our customers and are happy to offer this newest addition to our Nordtrack range. The launch of Nordtrack I908S was very successful, and consequently we have been asked for a bigger mobile impactor unit,” says Vesa Tuloisela, who heads the Nordtrack product offering at Metso Outotec. “The I1011 has a more powerful crusher and engine, resulting in a capacity as high as 300 tph. As a mobile crusher it also is well suited for the recycling of demolition and concrete waste, or reclaimed asphalt,” he continues.
In April, Metso Outotec signed an agreement to acquire Tesab Engineering, a Northern Ireland-based company offering mobile crushing equipment for aggregates applications, including quarrying, recycling, asphalt and concrete.
Tesab's turnover in 2021 was around €30m, and the company has more than 60 employees, primarily in Europe. The value of the deal has not been disclosed. Metso Outotec says that the deal, scheduled to close in the second quarter of 2022, will have no material impact on its financials.
Tesab's product portfolio includes mobile jaw, impact and cone crushers, mobile screens, scalpers and stackers. Metso Outotec says the acquisition will complement its current offering in the mobile crushing and screening markets. Tesab will continue as an independent brand within Metso Outotec and manage its distribution network.
Cone crushers are an integral part of any comminution process – but how do you know if your process requires a live shaft or fixed shaft model? This question has been addressed by Mark Utecht, director of the comminution technology group at crushing and screening equipment manufacturer Weir Minerals.
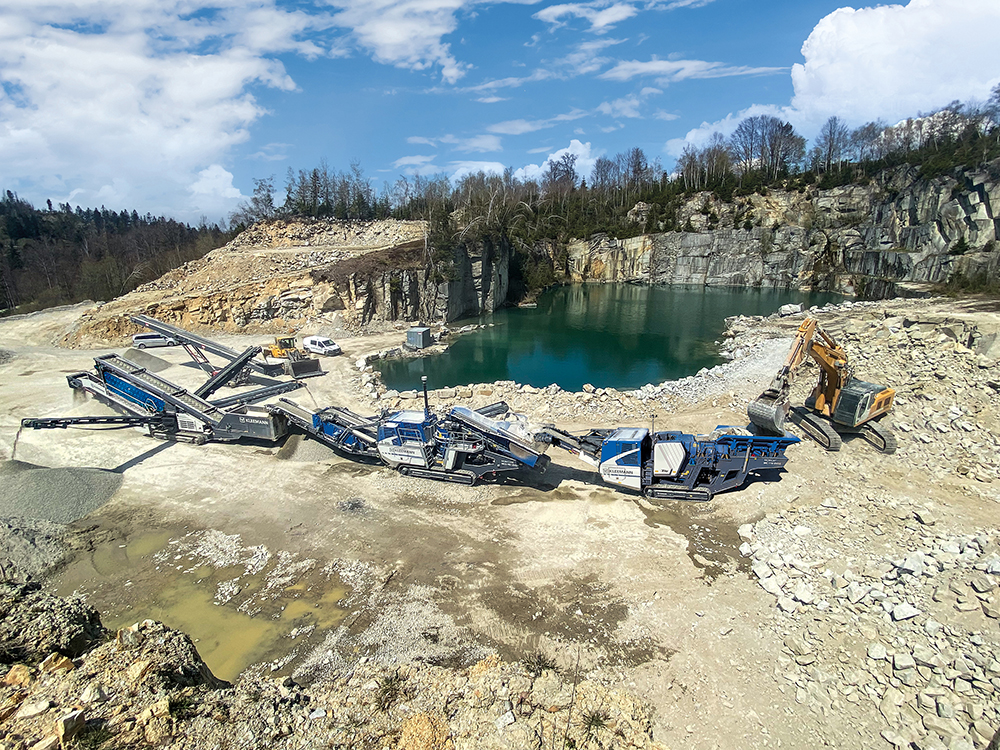
Utecht says that cone crushers - such as Weir’s Trio TC live shaft and Trio TP fixed shaft models - offer robust reduction for medium- or above-hardness feed material and are suitable for secondary, tertiary or, if the application requires: quaternary crushing stages. “These compression crushers are highly effective in typical mining applications and when processing ballast,” Utecht adds.
Inside the crushing chamber, a moving cone (the head) compresses rocks against each other and the edge of the concave bowl. This reduces multiple-sized particles at once and minimises wear.
The concave shape of the bowl ensures rocks will be crushed several times before they exit the crusher, as the volumetric space between the head and bowl gradually narrows towards the bottom of the crushing chamber.
“The primary difference between our two ranges of Trio cone crushers, the TC and TP, is the rotating parts,” Utecht explains. “The Trio TC crusher’s classic live, or moving shaft, design sees the entire shaft rotate eccentrically along with the head. While in a Trio TP crusher’s design, the shaft is fixed in the mainframe while the head rotates eccentrically. The TP’s design allows it to rotate faster and facilitates more interparticle crushing than the TC series.”
He states that Weir personnel are often asked: “Which cone crusher is better?”, adding that the answer is not as straightforward as it may seem, with factors such as the application and operating conditions determining the correct choice.
In the Trio TC cone crusher, both the shaft and head are moved in unison eccentrically during operation. Utecht says this proven design can be traced back to the original cone crushers invented in the 1920s, and a century of optimisation later, it’s one of the most reliable crushers in operation today.
“Although we always recommend all cone crushers are choke fed, the TC series’ straightforward design makes it ideal for use in applications where feed conditions are unreliable,” he says. “It has a slower rotation and a smaller throw (the space between the head and the bowl) compared to fixed shaft designs. It is also less susceptible to wear from intermittent feeds which leave the crushing chamber filled below capacity.”
Utecht says that Trio TC series cone crushers are based on a proven design and feature modern, easy-to-use control systems. He adds that their suitability for sub-standard feed conditions doesn’t mean these are sub-standard cone crushers.
“Following months of operational and design upgrades, our Trio TC is a fully automated live shaft crusher, engineered to deliver maximum efficiency,” says Utecht. “It features state-of-the-art crushing technology with modern lubrication, power systems and optimised hydraulics. Every element has been considered in the design, from the gearing, to the motion of the shaft and eccentricity of the rotation.”
The Trio TP fixed shaft (or pedestal) cone crusher can utilise substantially more horsepower, with a bigger eccentric throw and a higher pivot point to deliver throughput as high as 1,000m/tph. The TP series is also said to benefit from higher percentages of interparticle crushing which enables it to produce a finer product curve compared to TC-style crushers.
The fixed shaft is more compact than live shaft designs, which Utecht says makes it ideal for mobile applications or plants with limited clearance.
“The easily adjustable closed side setting (CSS) makes it easier for operators to adapt to changing ore bodies, or for aggregate producers to achieve their preferred product,” he adds. “Our Trio TP series cone crusher naturally creates a cubical shaped end-product that can remove the need for further crushing and shaping.”
The flexible Trio TP series is available in short-head and standard configurations offering 260-900hp, and is ideal for any project which facilitates choke-fed crushing.
Utecht concludes: “Using data from applications throughout mining and aggregates, Weir Minerals can support you throughout the entire process of cone crusher selection, installation, optimisation, and maintenance, from locations in more than 70 countries around the world.”
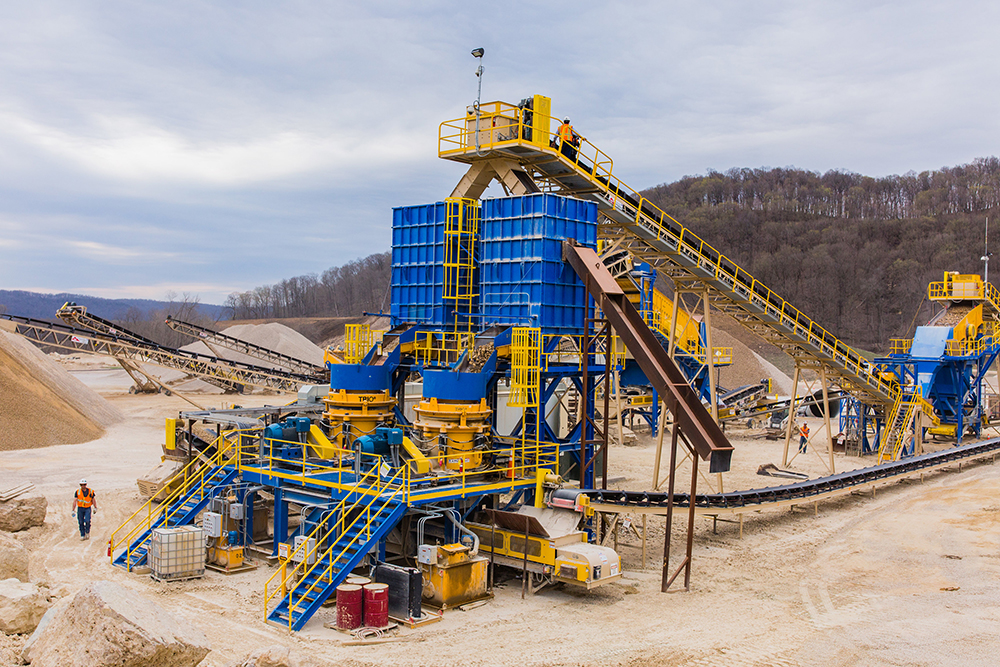
Wirtgen-owned Kleemann says two machines in its latest EVO2 generation of crushers are perfectly tuned to one another for line coupling in natural-stone-crushing applications.
The MOBICAT MC 110(i) EVO2 jaw crusher and the MOBICONE MCO 90(i) EVO2 cone crusher were developed with a focus on output, efficiency and flexibility. The mobile plants are frequently used together in the first and second crushing stage and pay off, in particular, due to the joint output level and simple line linking.
Kleemann adds that the two crushing plants in the latest EVO2 generation are harmonised with one another with regard to the transport points of the material, and the output also matches: the jaw crusher has the exact amount of power to perfectly utilise the cone crusher in the second crushing stage. The correct filling level of a cone crusher is particularly important to produce the highest grain quality with a minimum of wear. The MC 110 EVO2 can adjust its crushing gap fully hydraulically by up to 180mm. The MCO 90 EVO2, on the other hand, can cover a gap range of 6-45mm with its new crushing tools. Depending on the feed material, a downstream screening plant can be used to produce concrete or asphalt grain sizes in a single operation.
The crushing plant of both plants is optimised automatically by the feed control CFS (continuous feed system) so that material is always conveyed with maximum efficiency through the machines. At the same time, the filling level of the crushing chambers is monitored. When the filling level reaches a height that can be defined in advance, the material feed of the machine is adjusted.
Kleemann says this system forms the perfect basis for the line coupling of an interlinked plant train. The optionally available probes at the crusher discharge conveyor and/or fine grain conveyor of the upstream machine monitor the filling level of the feeding unit of the respective upstream machine.
For safety reasons, the crushing and screening plants are connected to each other by a cable. If an emergency stop button is pressed on the plant train in the event of an emergency, all machines are safely stopped.
Finnish crusher and screener bucket maker ALLU has launched the new Transformer DC Series for the Chinese market. ALLU says it commenced its new Chinese manufacturing plan in 2021, after listening to the needs of customers. The manufacturer adds that it was clear it needed a local facility to grow and support Chinese customers. The company says that investing in a local manufacturing facility has enabled it to make products tailored to the local market requirements.
ALLU operations director for China Pierre Bujes says: “Introducing the new DC Series, which ALLU has tailored just for the Chinese market will strengthen our support to our customers and operational presence, to help grow the region whilst being competitive in the local market.”
The ALLU Transformer DC Series parts are designed to be reliable screening attachments for a variety of screening, crushing, mixing, and aerating applications. All models are equipped with two hydraulic motors for maximum processing power. The attachments have reinforced sides, making the bucket robust and durable even in demanding environments and with demanding materials.
The main areas of application for the Transformer DC Series are: waste material handling & processing; compost mixing and aerating; pipeline backfilling/padding; stabilising clay; cable backfill; environmental remediation; and soil & gravel screening.
The Transformer DC Series offers two different blade options, TS blades and X-blades. The TS blades are suited for applications that require screening, separation, and aeration. They rotate between the screening combs, and the final fragment size is 25-50mm.
Swedish manufacturer Sandvik is introducing Endurance packages to help its mobile crusher customers maximise their plant uptime.
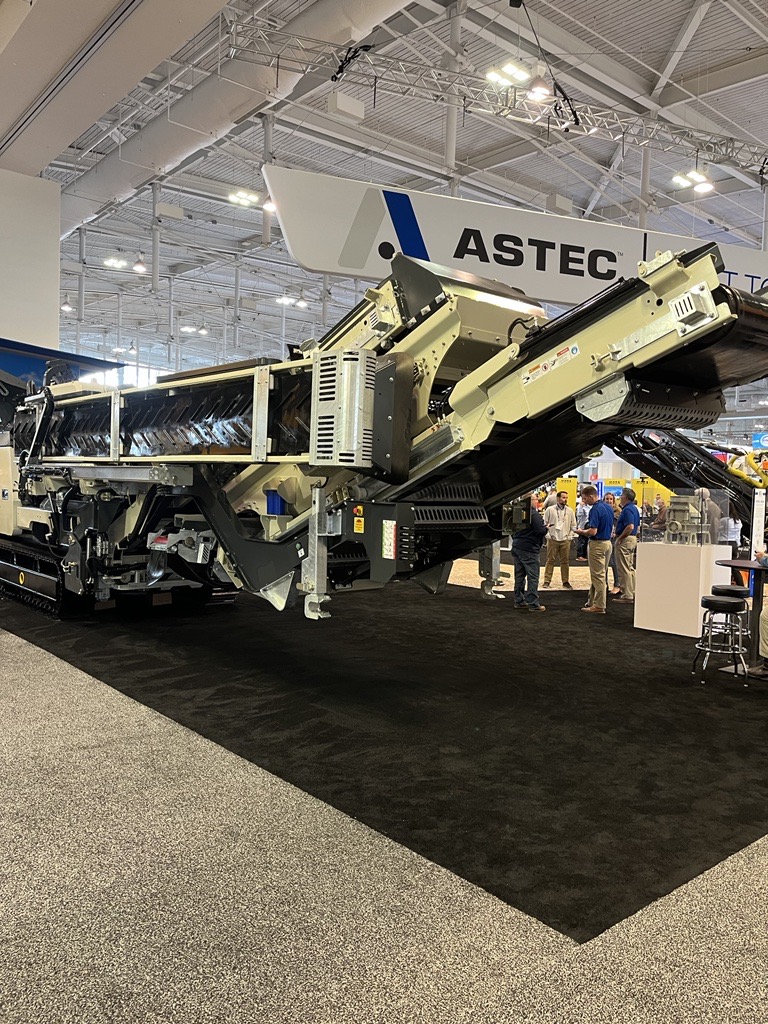
The packages are configurable and can be tailored to meet specific customer needs and requirements. They provide all the necessary parts should the unexpected occur, allowing customers to replace these immediately, maximising plant uptime. They are said to be the perfect solution for sites working long hours (high utilisation) and/or remote locations, where availability and support are essential to customer operations.
The packages range from standard maintenance to major component ‘exchanges’, allowing customers to choose the package best suited to their operational needs. Sandvik’s maintenance, repair and overhaul package strategy can meet varying customer demands and caters for all quarry, mining, and demolition and recycling applications.
SBM Mineral Processing plans to launch a redesigned version of its REMAX 600 impact crusher at this year’s bauma exhibition in Munich (October 24–30).
The Austria-based manufacturer says the new machine will set new standards in the up to 600 t/h power class, helped by compact transport dimensions and a machine weight of around 60 tonnes.
SBM adds that the REMAX 600 is an ‘intelligent crusher’ utilising the all-electric SBM drive system and process automation technology. High-grade sensors in the machine automatically monitor feed material and final products, record the load conditions of crusher and conveyors, and optimise all separation processes including overbelt magnetic separators and wind sifter.
US-based Astec’s new Ranger J20 tracked jaw crusher was on show at the co-located World of Asphalt/AGG1 exhibitions (29-31 March) in Nashville, Tennessee.
The compact unit is aimed at customers such as rental firms and is designed for versatility, mobility and ease of transport. It is suitable for customers wanting a crusher that can be used in comparatively small urban spaces. Designed to be mobile and easy to transport, the machine can be made ready for use within a short period of its arrival onsite. Power comes from a Cat C4.4 diesel rated at 129kW, which meets the Tier 4 Final/Stage V emissions requirements.
The machine is available in closed-circuit and open-circuit variants and can be used to feed into other plants if required.