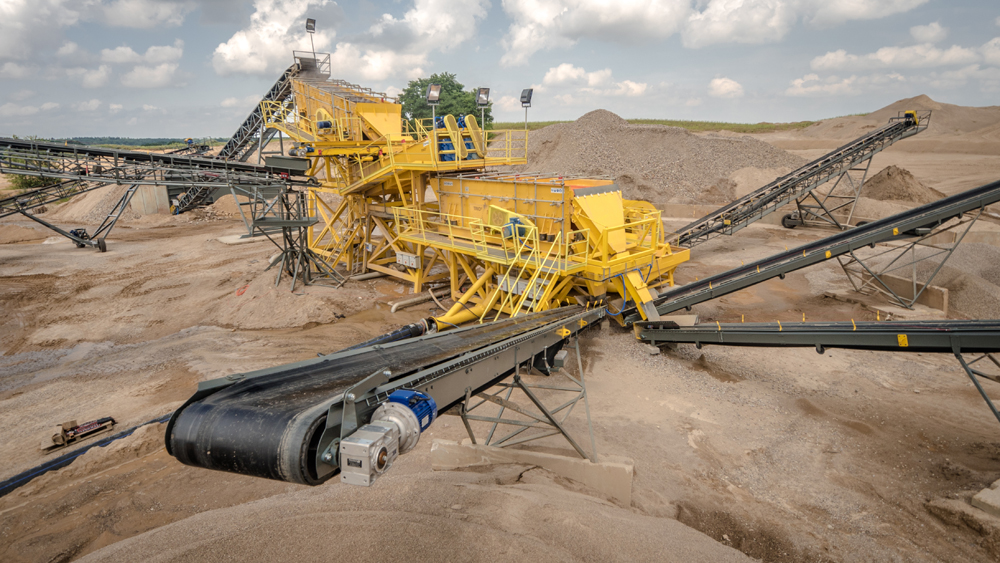
The servicing and spares strategy for crushing and screening equipment is critical in terms of its success and reliability. Crushers are designed to ingest and break some of the most abrasive materials on earth – to the detriment of their internal wear parts. Engineered to operate on the front line, they perform within some of the harshest environments.
“When we sell processing equipment to mines and quarries, we often find it is classified as ‘mission-critical’ – meaning the failure of this machine can stop the production of the entire site,” says Scott Campbell, comminution sales manager, UK at Weir Minerals.
He adds that the availability of high-quality wear parts can be the difference between the success and failure of an entire project. Campbell highlights some key points for consideration when designing a spares and wears strategy.
Firstly, the combination of materials used in crushing parts plays a critical role in their success or failure when installed.
Manganese is a favoured alloy for those operating cone and jaw crushers due to the material’s work-hardening properties. As rocks meet the outer layer of the manganese its exterior toughens, while its interior remains soft. This combination of toughening exterior and flexible interior means the part is harder to wear down during typical operations and can navigate higher impact blows.
The second point Campbell highlights is that the shape of the jaw crusher wear parts often determines if the jaw die will experience equal or unequal wear throughout the plate, impacting the overall efficiency of the crusher.
The mould, which also includes the tooth profile, must be designed for the application and the material that is being crushed.
The tooth pattern must be designed to properly grip the chosen feed, enabling the crusher to process the material as efficiently as possible. This is a fine balance as the die must offer enough wear material to ensure the maximum life of the part, while keeping weight to a minimum and safeguarding against excessive wear material, which reduces the overall capacity or closed side setting of the crusher.
The shape of the valleys between each tooth must be carefully considered. If the shape is not suited to the application, rocks can become lodged, clogging the die and putting the crusher under undue stress during operation.
In addition to evaluating the customer’s application, the team at Weir Minerals and ESCO can examine their worn parts and recommend different jaw features and customisations which could increase wear-life, boost production, ensure even wear or alter the product size. These wear parts will be designed using the old part’s successes and failures and be made specifically for the customer.
The third point Campbell sets out is unlocking the crusher’s capabilities.
“Customers are often surprised when they find their crusher has untapped potential,” he says. “Take the Weir Trio TV series vertical shaft impact crusher (VSI) for instance - a popular crusher when creating manufactured sand.
“The VSI is fed from the top, and the material is guided into a high-speed rotor. It is then accelerated, application-dependent to 45-75m/s, and discharged into an ‘impact zone’. In here it is broken along its natural fracture lines as it comes into contact with other feed material rebounding from the walls of the chamber or anvils installed inside the crusher.”
Campbell says that customers of the Trio TV series are always surprised during discussions regarding the product’s flexibility. By simply switching the wear-part combinations, he says this crusher can easily interchange between three different crushing chamber configurations:
- Steel on Steel (SOS) effective when crushing larger non-abrasive materials, in secondary and tertiary crushing applications.
- Rock on Rock (ROR) useful when crushing abrasive materials, in tertiary and quaternary applications where additional fines are desired.
- Rock on Steel (ROS) configurations are recommended when crushing low abrasive materials, in tertiary and quaternary applications where a higher rotor speed is necessary to produce additional fines.
“Speak with your original equipment manufacturer and better understand the capabilities of your product,” says Campbell. “Often by switching configurations, existing equipment can be repurposed to offer a pathway to creating a completely new income stream for your site.”
The fourth factor is time, which Campbell says is the easiest factor to understand and the one which most struggle to optimise.
“At Weir Minerals we’ve noticed an increasing trend where some cone crusher operators choose to replace mantle and cone liners at different times – often because one is wearing faster than the other,” he says. “We realise that operators must ensure they are using each part to its full potential, however our recommendation is simple; work with your supplier to re-evaluate your process and identify parts which wear at the same rate – or find someone who can.”
Mantle and cone liners must be changed at the same time – Campbell says it is the only way to ensure the parts match upon commissioning and reduce the risk of part failure, while keeping servicing stoppages to a minimum.
The successful timing of servicing windows is crucial. “Think about a Formula One race team for example, strategising their tyre and fuel stops – too early and you have not maximised your part’s potential, too late and you put your equipment at risk,” says Campbell.
He adds that it is very important to understand the limitations of the part while monitoring wear rates. Operators should work with their supplier, take the time to understand all factors at play and reap the rewards when they are able to fully optimise their maintenance schedule.
Scott says that the final factor is to partner with a company you can count on.
“At Weir Minerals we realise that maintaining the reliability of operations is of key importance to our customers,” he says. “All Weir Minerals equipment is fully supported by our unmatched global service centre network – operating in 70+ countries around the world.”
In an interesting crushing and screening market development, Terex Materials Processing (MP) has acquired fellow Irish company MDS International (MDS), a manufacturer of heavy-duty and recycling trommels, apron feeders and conveyor systems, based in Co. Monaghan.
MDS was founded in 1995 by Liam and Una Murray with the aim of designing and developing engineering solutions for industry.
Materials processing equipment company Terex MP says that, over the past 25 years, MDS has built a highly skilled work force along with global distribution partners, and has a valued reputation for innovation, offering bespoke solutions to serve client needs with equipment that can withstand the harshest of environments.
The acquisition, details of which have not been disclosed, supports Terex MP’s growth strategy to expand its offering in the crushing and screening and environmental industries, with products that complement the existing portfolio.
Terex MP says that MDS produces heavy-duty trommels that will enable it to expand into areas it does not currently serve. Terex MP adds that it expects strong commercial synergies from the deal, as several of its distributors already carry the MDS line, while others will be new to Terex, offering the potential to develop new channel partner relationships.
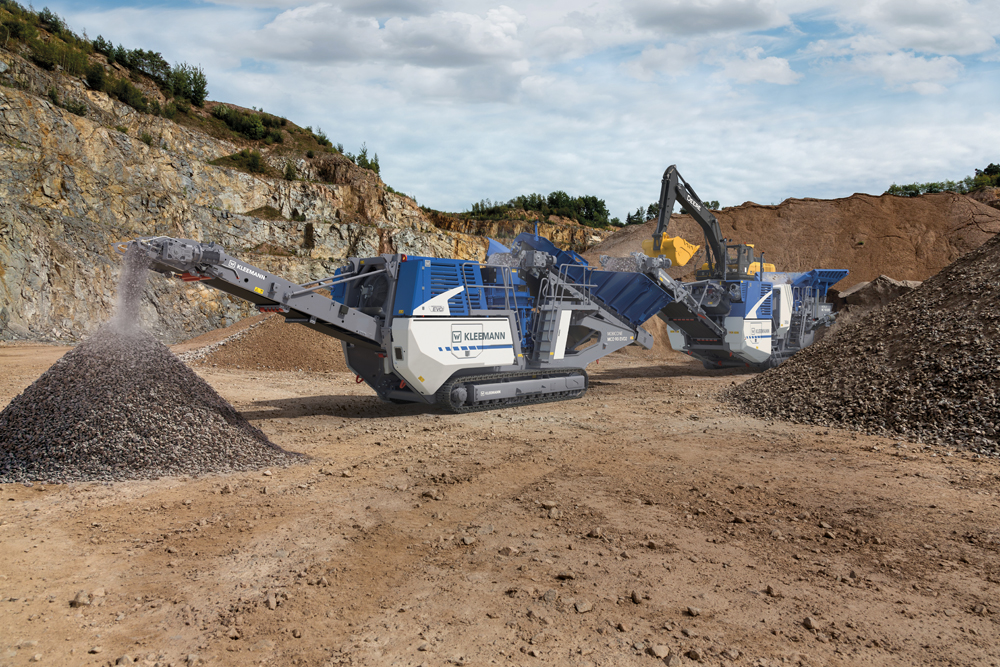
MDS’ 34,000 square foot facility will be the first Terex location in the Republic of Ireland, which the company says diversifies its footprint and provides access to a new labour pool.
The facility is within a short driving distance of the Terex Dungannon and Omagh sites, providing ready access to Terex MP’s Northern Irish team and enabling close coordination with the resources at these facilities.
The MDS facility and its team members will be led by Conor Hegarty, general manager and business line director. Previously, Hegarty was international sales director for Terex Ecotec.
Terex MP says his commercial background and product knowledge will be a huge asset as he takes leadership responsibility for MDS.
MDS will remain a standalone brand along with Terex MP’s crushing and screening businesses including Powerscreen, Terex Finlay and EvoQuip.
Terex MP says it will build on the momentum of MDS International’s long-standing reputation, continuing to develop the brand, its product portfolio and its distribution channels.
Pat Brian, vice president, mobile crushing and screening at Terex MP, commented:
“The addition of MDS to our portfolio of businesses will bolster our growth and improve our product offering. The business has been well managed, is on a terrific growth trajectory, and its heavy-duty trommels address a gap in our own product lines while also having a lot of synergy with what we already manufacture and distribute.”
Liam Murray, co-founder of MDS International, said: “MDS will now have the global resources of Terex to develop and grow it to new levels; I feel this is the right move for our business and team. This sale will also bring new levels of support to customers and dealers worldwide.”
The September-October 2021 issues of Aggregates Business Europe/International will include an in-depth interview with Conor Hegarty.
Komatsu Europe’s new BR380JG-3 mobile jaw crusher is powered by a Komatsu EU Stage V emissions-compliant diesel engine. Furthermore, to meet Komatsu’s commitment to a cleaner environment and increasing demands from customers to reduce CO2 emissions, the BR380JG-3 comes with an innovative CO2 offsetting scheme applied to every plant sold in Europe.
“The new BR380JG-3 is Komatsu’s first diesel-powered machine in Europe with net-zero CO2 emissions,” says Vince Porteous, product manager at Komatsu Europe. “Komatsu believes that solving environmental, social and governance (ESG) issues are key to the future. By combining Komatsu technology with the assistance of biology, we, as a manufacturer of construction and mining equipment and as a member of society, can deliver on our commitment to our customers and to the planet.”
The BR380JG-3’s operating weight ranges from 33.5 to 35.31 tonnes, with the plant’s maximum crushing capacity of 240 tonnes per hour. The fuel-efficient EU Stage V Komatsu engine has a power output of 159kW @ 2050rpm.
The latest Komtrax telematics, and the Komatsu Care maintenance programme for customers, offer top fleet management and support, protect the machine against misuse and guarantee maximum efficiency and uptime.
Building on the reputation of the BR380JG-1, the net-zero C02 emissions BR380JG-3 incorporates a new two-axis type deck vibrator, which enables a smooth continuous flow of material to the highly efficient two-stage grizzly separator bars.
The semi-automatic feeding system incorporates crusher overload detection and automatic feed control to enable consistent and efficient production.
The machine has a 1,065mm x 550m jaw opening with tapered side plates. The automatic jaw setting feature is user-friendly and makes it easy for a customer to crush at a high volume to the desired discharge material size.
With its generous crushing capacity and 1,050mm-wide main conveyor with a top speed of 120m/min, an up to 37-tonne stockpile can be achieved before any machine movement is required.
The BR380JG-3 also has the option of a side muck conveyor and magnetic separator, which provide additional versatility.
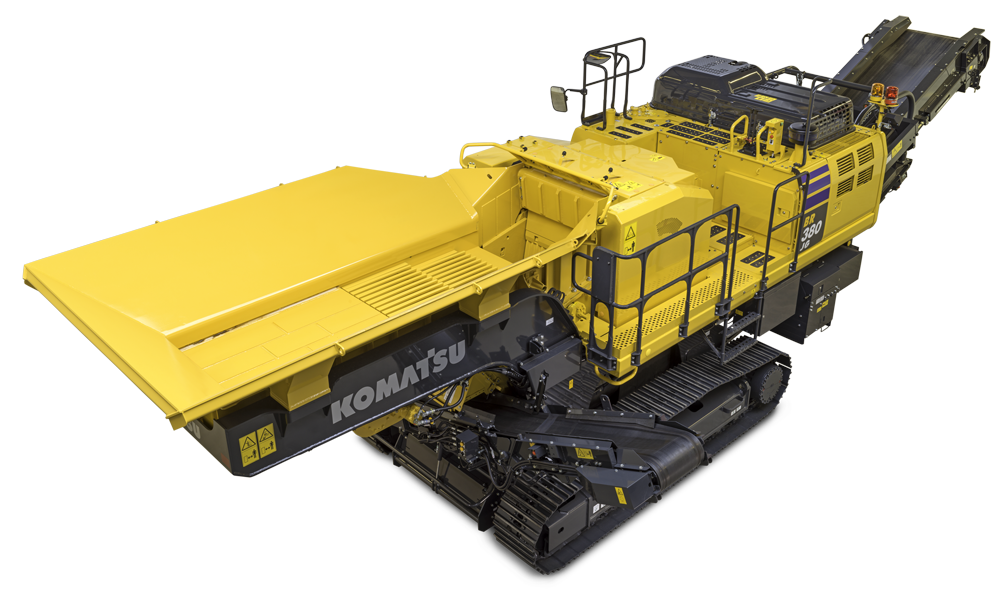
An easy one-touch start-and-stop function makes it quick and simple to operate the machine. The addition of the standard radio remote control allows operators to multitask and increase their efficiency.
The high-resolution monitor panel, available in 27 languages, provides real-time machine condition information, fuel consumption information and ECO guidance.
The BR380JG-3’s enhanced safety features include a foldable ground-level maintenance access step, allowing safe, easy access while retaining a transport width of 2,870mm. The machine also provides new guardrails and safety harness anchor points.
The machine incorporates Komatsu’s telematics system Komtrax, which provides machine performance reports, and engine after-treatment system health and maintenance reports, all provided through 4G mobile communication.
With its new mobile cone crusher MOBICONE MCO 90(i) EVO2, Kleemann says it has created the perfect supplement to the jaw crushing plant MOBICAT MC 110(i) EVO2. The innovative cone crusher is designed to provide high economy, intelligent control engineering and top product quality. Kleemann says the robust MOBICONE MCO 90(i) EVO2 offers quarrying and contracting companies decisive quality advantages on a typical workday.
“During daily work in medium-hard to hard stone – mainly in the 2nd or 3rd crushing stage – cone crushers often work close to their load limits,” the manufacturer states. “With a maximum feed capacity of up to 270 t/h, the new cone crusher MCO 90(i) EVO2 demonstrates its strengths and guarantees more operational reliability and high plant availability.”
Kleemann adds that simple transportability with frequently changing job sites and the wide application range also provide convincing arguments for using the MOBICONE MCO 90(i) EVO2.
The operation of crushing plants is becoming more and more sophisticated, according to Kleemann. Therefore, for its brand-new crushing plants in the EVO2 generation, the manufacturer developed an intelligent control concept that is designed to considerably simplify operation.
The SPECTIVE operating concept has an intuitive structure and is claimed to revolutionise plant operation with its extensive features. The 12” touch panel has been optimised with regard to user guidance and visualisation. In addition, new components such as a large and small radio remote control have been integrated into the SPECTIVE offering. The new digital solution SPECTIVE CONNECT sends all important plant data to the smartphone. Kleemann says this means less downtime, higher productivity and more revenue.
The MOBICONE MCO 90(i) EVO2 is designed for a high crushing capacity. With its crushing tools, the cone crusher covers a wide gap range of 6-45mm, allowing it to be used flexibly. The improved crushing tools with geometries optimised for the respective application, contribute both to the material quality as well as the plant output. All crushing gap widths are set conveniently via the radio remote control, and this does not require further conversion work.