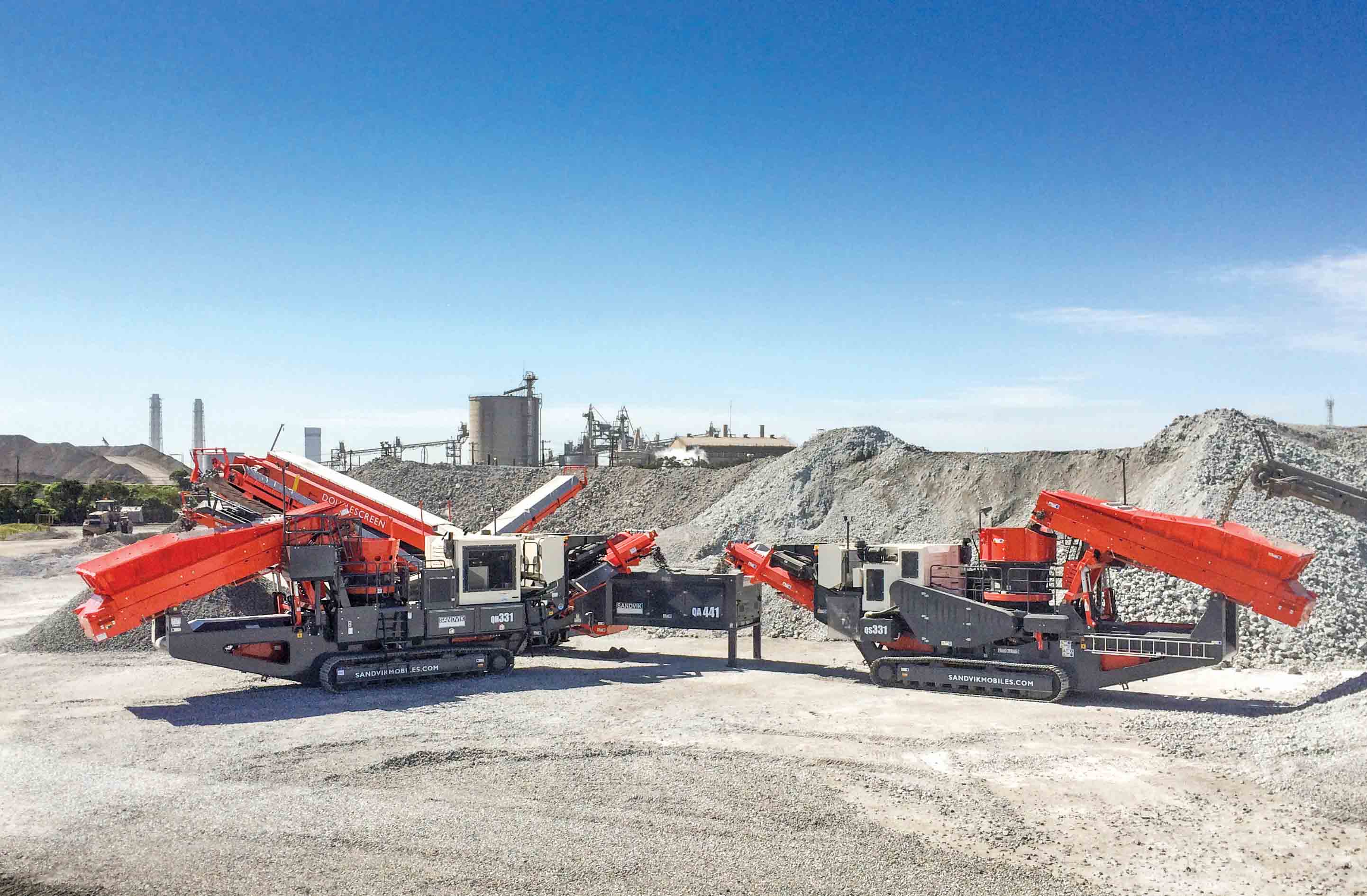
Equipment from Sandvik is helping Japanese company Tetsugen produce aggregates for use in road construction and concrete foundations, Patrick Smith reports.
Japan’s Tetsugen Corporation, which has its headquarters in the central Tokyo district of Chiyoda, has recently acquired two mobile cone crushers and a Doublescreen screening plant from
Originally focusing on coke production after its founding in 1939, the company has developed into one of the leading companies for slag recycling and utilisation in Japan.
The three Sandvik machines, which produce a variety of aggregates, were selected for their “high performance, reliability and low running costs,” along with a direct link to Sandvik’s Global Support Centre, which has assisted in providing aftermarket back-up in Japan.
The decision to acquire the Sandvik equipment was concluded as part of an agreement following a visit to the manufacturing plant in Ballygawley, Northern Ireland, in the summer of 2015.
The delegation from Tetsugen was accompanied by a representative from Imagiire, Sandvik Mobile Crushers and Screens dealer in Japan. Shigehiro Kimura, sales manager for Sandvik in Japan, was also present to ensure a personal approach to finding the right solution for Tetsugen’s production requirements.
This relationship also provided assurance that interruptions to production would be kept to an absolute minimum. It also meant that any natural wear and tear experienced through prolonged and regular use can be quickly identified and components can be rapidly replaced with genuine Sandvik Spare and Wear Parts. Aftermarket service provided in Japan is also able to assist if any unexpected interferences occur during processing.
When recycling slag material, Tetsugen must produce a number of different and precise aggregate sizes because the end product is employed by construction and steel companies for road construction and use in concrete foundations.
The company presently utilises a Sandvik QS331 gyratory cone crusher; a QH331 Hydrocone crusher, and a QA441 Doublescreen.
The large slag feed size of 400mm is accommodated by one of its jaw crushers, and this is then fed directly into the QS331, which features the high performance Sandvik CS430 gyratory cone that is easily able to accept feed sizes up to 340mm.
The material is then processed by the QH331 cone crusher with Sandvik’s Hydrocone technology.
The QA441 Doublescreen provides the sized aggregates required. The 0-40mm and 0-25mm are used in road construction, while the 5-20mm aggregates are used in concrete foundations.
Sandvik’s patented Doublescreen technology has two independently adjustable screen boxes which allow for precision while screening, resulting in high-quality products for Tetsugen’s customers.
When performing together in normal conditions, the Sandvik trio provides for an output of approximately 250tonnes/hour, and this is helped by the QA441’s massive screening area.
According to Tetsugen’s on-site engineers, the most pleasing aspect of working with Sandvik’s machines is their “reliability, compact size and ease of operation in the field.”
In addition, the QH331 is noted to have performed exceptionally during slag processing operations thus far, in particular thanks to the automatic control of its cone crusher. This is aided by the machine’s signature level sensor located directly above the cone’s input, as well as by the system’s hydraulically-adjusted Hydrocone.
In acquiring the ensemble of machines, Tetsugen is said to have also taken into account the long term running costs necessary for its required production outputs. Into this equation come fuel costs and the expense of replacing and repairing parts and components.
Apart from possessing a direct drive system for optimised fuel efficiency, the QH331 also incorporates the Constant Liner Performance, that enables the extended life of chamber liners. This feature is said to reduce replacement costs and greatly reduce periods of downtime.
A distinct challenge when processing slag is the presence of metal and other ferrous materials so metal detectors and overband magnets are optionally available for this purpose.
The calibre of material output by the machines is of the utmost importance when considering its final purpose, and this is especially critical for aggregates destined for use in concrete foundations, says Sandvik.
Thanks to its low permeability and increased resistance to corrosion, concrete involving recycled slag is often used in Japan for coastal construction and bridges which are exposed to saline environments.