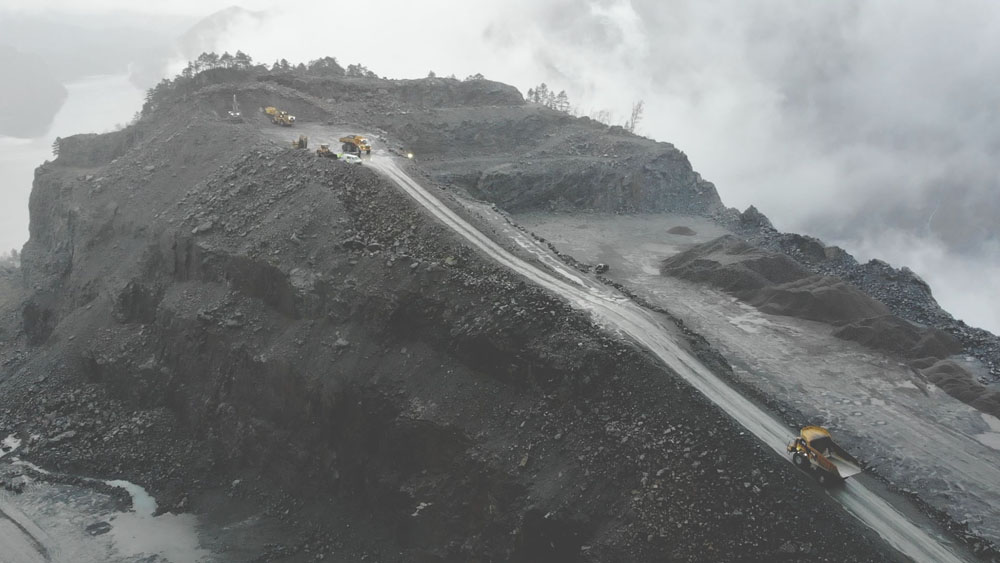
“This is a milestone for Steer. With this contract, we are taking a giant step from our first contract in 2009 which involved clearing a large artillery range in the Norwegian mountains,” says Steer CEO Pål Ligård.
Steer chairman Ketil Solvik Olsen adds: “We can now utilise our technology with a customer within an industry with a lot of potential. This is very exciting!”
The project with Romarheim is innovative on several levels. Previously, Steer’s remote-controlled construction equipment had primarily been used in projects where health and safety had been the main concern. Projects have included the clearing artillery ranges, and where the geographical conditions were challenging and dangerous. The key focus of the Romarheim project has changed to utilise the technology for a more efficient and cost-effective autonomous operation.
The contract involves work in a stone quarry in Osterfjord, north of Bergen. The plan is to load up autonomous trucks with stones, and these trucks will then follow a set route out of the quarry and dump the stones into a shaft leading down to a crushing plant. From there, the stones will then be transported by boat to both domestic and international markets.
“As you can understand, these are quite repetitive tasks, and this is a perfectly sized project to test our autonomous solution even further. In addition, Romarheim is a very forward-thinking customer who is excited to be part of this innovation project,”, says Steer co-founder Njål Arne Gjermundshaug. “We are able to develop our product through a clearly defined long term project.”
The plan is that the driver of the wheeled loader that is loading stones onto the fleet of trucks will also be able to oversee and direct the trucks using an iPad from his seat in the cabin.
“At the start of the project, we will place drivers in the remote-controlled trucks as a precaution to ensure that the technology is working correctly and meeting expectations,” says Gjermundshaug. The project is due to start in spring 2021. Steer is currently performing testing with miniature trucks in Oslo. “This is to test the technology, so it’s meeting the expectations we have for precision, safety, usability and operation time,” explains Gjermundshaug.
For Romarheim, this project is also about realising an idea they have had even before the company was established in 2011. “Our focus has always been to be open to new ways of streamlining mass transport by automating some of the processes involved,” explains Kåre Romarheim. With automation, we aim to improve consistency and remove hazardous and dangerous tasks for our employees, reducing the risk of injuries. The expectation is that this will also increase efficiency and reduce the operational and maintenance costs of the equipment.
After Steer issued a press release about the launch of its remote technology for industry, Romarheim contacted Steer, and they soon started the process of developing a solution together. As both Romarheim and its stone quarry customer DC Eikefet Aggregates were also keen on the idea, this helped speed up the project’s delivery. “We were excited to do this pilot project. Our customer was also keen to look at measures to increase efficiency and improve health and safety for its employees.
“This is our first major delivery of autonomous dump trucks in a global market, and we see a large potential,” says Ligård.
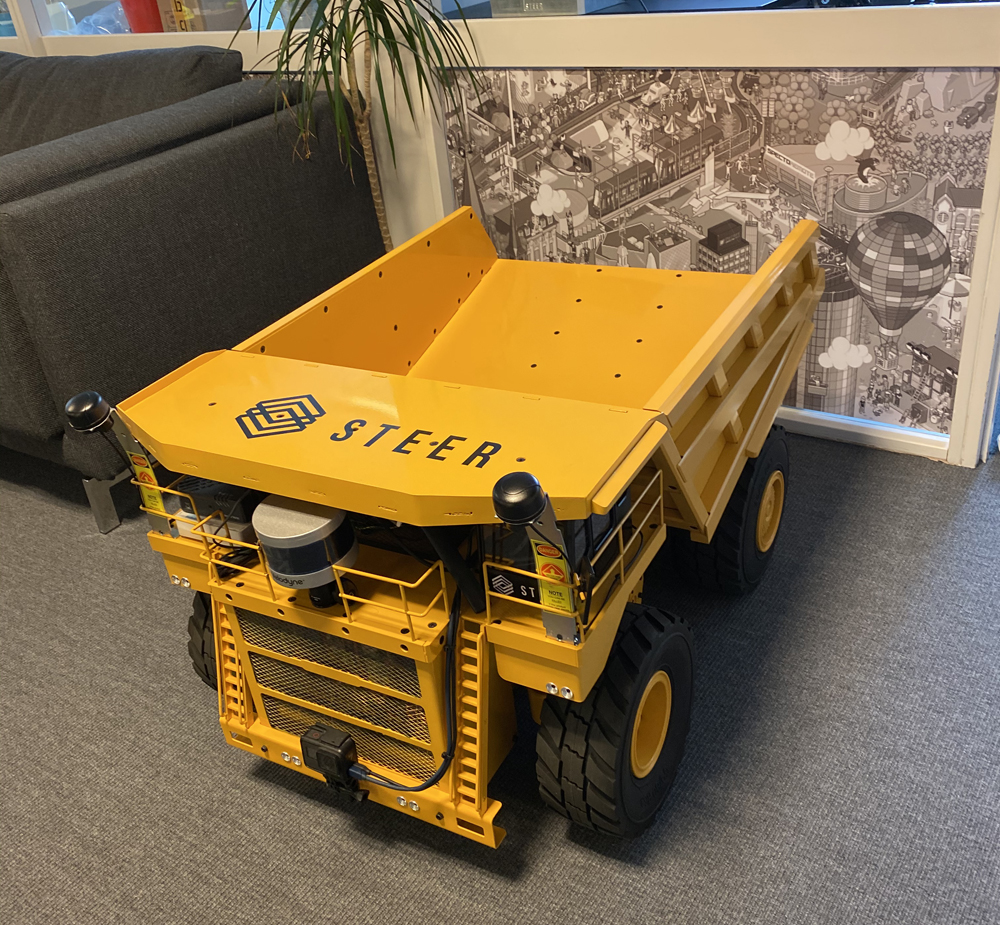
Due to a significant increase in the interest in Steer’s technology, they are now in the process of expanding the workforce and the organisation. In addition, the company have received NOK 2 million [€190,600] in grants from the public innovation body Innovation Norway. Steer can now focus on developing technology with both the domestic and international market in mind. “We believe the market is substantial, especially in North-America and Australia,” says Olsen.
The launch of Steer on the international market was delayed due to the COVID-19 pandemic. An ongoing project at an oil refinery in the USA had to be postponed, but despite the pandemic, Steer has experienced an increase of interest from potential new international customers.
Olsen continues: “This is not the type of technology that you purchase online with a home delivery two days later. Our solutions need to be properly integrated with the customer’s existing technology; safety is the highest priority. Our experts would normally travel to the customer to oversee the integration. With the travel limitations we experienced in 2020, we have not been able to do this as initially planned. At the same time, by focusing on domestic projects, we have had a great opportunity to establish a partnership with Romarheim. They have so far been a dream partner for us as they are a serious, down to earth and trustworthy partner. This may be beneficial for both of us.”