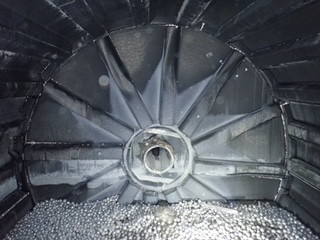
Due to a substantial increase in demand for their product and to increase the overall throughput of the site, JHP wanted to increase the output of their ball mill, which was processing a mixture of coarse and fine silica. The incumbent rubber mill liners were only lasting between six and nine months and contributed to a 25% drop in output after just six months in operation.
Weir Minerals mill lining specialists, renowned for their expertise in mill lining systems and wear materials, conducted extensive testing and modelling scenarios to evaluate how optimising the ball mill charge volume and trajectories would result in increased mill throughput.
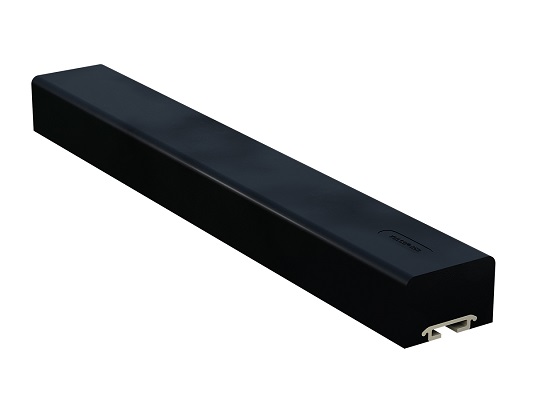
Using state-of-the-art simulation technology and decades of expert knowledge, Weir Minerals specialists designed a customised mill lining system with Vulco R63 rubber mill liners. The custom-engineered shell liner design ensured correct lifter face-angle to facilitate optimum performance while also increasing the service life of the Vulco mill liners. To complete the ball mill overhaul, Weir Minerals experts also recommended increasing the charge height, significantly improving the grinding process.
The custom-designed solution resulted in increased production and increased mill availability at JHP. The Vulco R63 mill liners improved wear life by up to 200%, from six to 18 months, more than halving the reline time and associated maintenance costs. As a result of the ball mill overhaul -designed and executed by Weir Minerals experts in partnership with JHP, the throughput was increased by up to 44%.
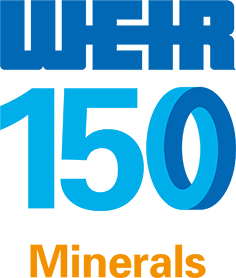
The innovative designs of Vulco mill liners are tailored specifically for every customer and are manufactured to the highest industry standards for autogenous (AG) and semi-autogenous (SAG) mills, primary, secondary, and re-grind ball and rod mills. The inherent characteristics of elasticity, high tensile strength and corrosion resistance found in the Vulco elastomer compounds position them as the preferred mill lining material over steel in many applications.