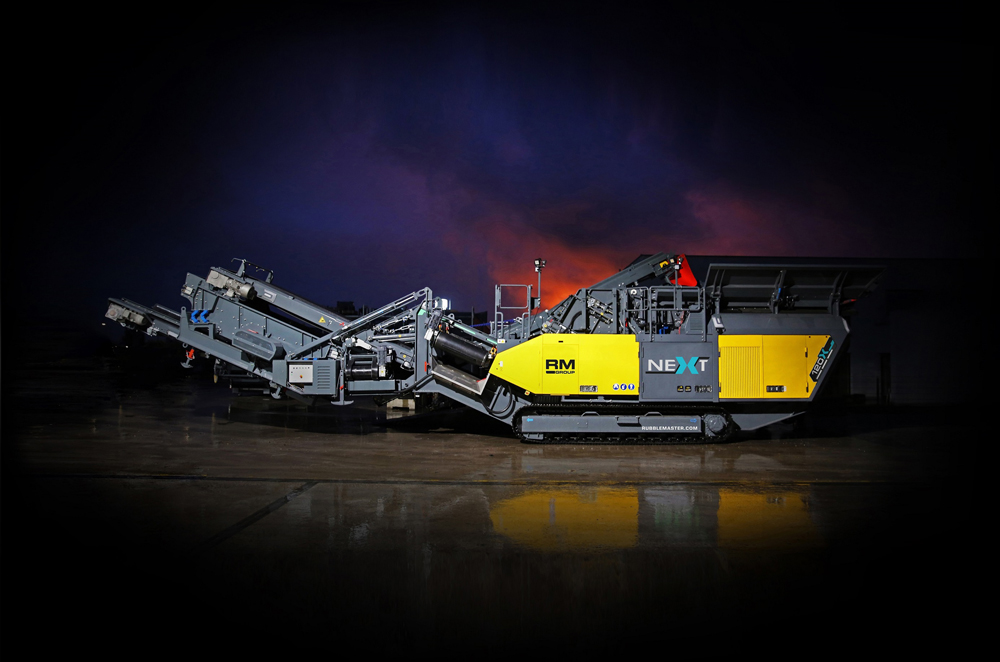
The debut RM NEXT crusher follows on from a prototype RM NEXT machine showcased at bauma in Munich, Germany in April 2019. The RM NEXT-based RM 120X crusher will be followed by an RM NEXT-based screen in 2021.
"With this philosophy, we are once again setting standards in user-friendliness," says Gerald Hanisch, founder and owner of Rubble Master, enthusiastically. As the first NEXT philosophy crusher, the RM 120X combines enhanced safety with maximum performance and flexibility. However, the company remains true its proven service and intuitive GO! operation concept, which it continues to expand.
In a nutshell, RM NEXT focusses on four points. Extended service is one of them, which includes both the standard five-year warranty - an industry first - and the annual service.
Simplicity is ensured despite the additional features, equipment options and configurations that have been developed based on customer requirements. "Operating a RM 120X still involves only a few buttons. The built-in screen is only used to display information and has no sub-menus. We have received valuable input for this operating concept from our customers around the world, and the controls and display meet the specifications on job sites 100%," says Hanisch.
The RM Group has always been one of the pioneers in terms of safety in the past. Gerald Hanisch's vision has now become a reality. With RM NEXT and the comprehensive operator-machine interface, the operator no longer has to enter the danger zone while operating the machine and can see light signals indicating both the status and current workload of the crusher from the excavator cab.
An additional focus was on the optimisation of material throughput. Here, the world market leader implements job-specific crushing equipment for the respective material and real-time analysis. This reduces running costs and increases turnover. The optimisation starts with the machine configuration, which is why five main application cases have been developed with the necessary equipment options. Also, the performance indicator on the machine and the RM GO! SMART can be used to detect and implement any potential improvement immediately.
"When we started developing RM NEXT, we always had our entire product range in mind. In future, an important role will be played by networking different products in operation at the same job site. However, we can only make this happen if all the products work according to the same philosophy," explains Hanisch. That is why intensive work is currently underway to network RM machines that work together. This will mean that the throughput of the screen can be adjusted in future to match the utilisation of the crusher. Machines downstream from the crusher can also stop automatically if the crusher is currently not processing any material. These optimisations are designed to increase efficiency and save running costs.