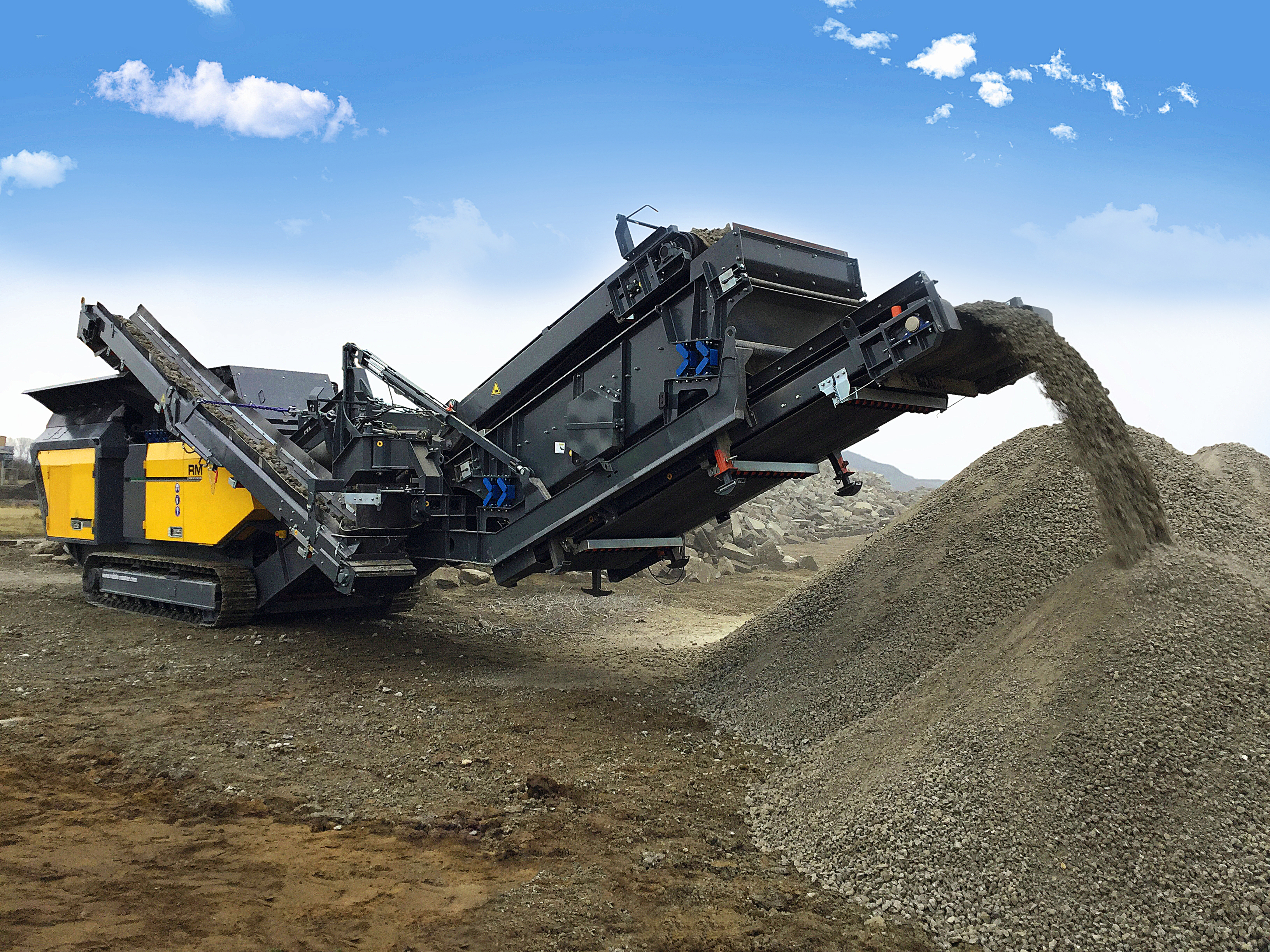
Able to recycle and process materials on site, Rubble Master’s John Deere-powered impact crushers are said to bring instant return to small and medium-sized recycling contractors. They offer great weight to size ratio and excellent throughput capacity. The patented GO! principle, built into every unit, is said to emphasise easy set up and intuitive operation.
The RM 100GO! track-mounted impact crusher handles up to 250tonnes/hour, crushing construction and demolition (C&D) waste, concrete, asphalt, glass, coal, natural rock, and even reinforced concrete for production of high quality construction materials.
With the RM 120GO! track-mounted impact crusher Rubble Master strengthens its foothold in the mining industry. Weighing only 35tonnes, it can reduce up to 350tonnes of demolition waste to tiny pieces in just one hour. Impact plates enable the operator to switch between recycling and natural stone applications quickly, increasing productivity and flexibility.
For both units, customers have a choice of a John Deere Tier 3/Stage III A or Final Tier 4/Stage IV PowerTech E 9.0L engine. “The dynamics of a crusher require a good engine response to maintain a constant speed at highly fluctuating load. These engines have proven reliable in the toughest of applications,” says Heinz Jank, research & development manager of Rubble Master.
Both Rubble Master and John Deere Power Systems are pioneers in their fields. While processing hard stone usually requires a jaw or cone crusher, Rubble Master has developed impact crushers that can handle the job – and, in certain applications, do the work of two other crushers.
John Deere Power Systems pioneered advanced emission technologies for Tier 3/Stage IIIA, and built its Final Tier 4/Stage IV on these proven technologies. The company is ready to lead customers seamlessly through the upcoming Stage V transition, thanks to its considerable DPF experience. John Deere brings remarkable expertise in application integration, while a wide product offering gives OEMs more options to match power and performance to exact machine requirements.
The two companies have a long history of successful collaboration. Local John Deere engine distributor Hamilton AG has worked with Rubble Master to successfully integrate John Deere engines in the company’s impact crushers since 2005.
“As long-term supplier to Rubble Master, we appreciate the opportunity to support its innovations. We are pleased our technologies help Rubble Master to strengthen its position in the market, and its end-customers to build successful businesses,” said Florent Goujon, Area Manager of John Deere Power Systems.