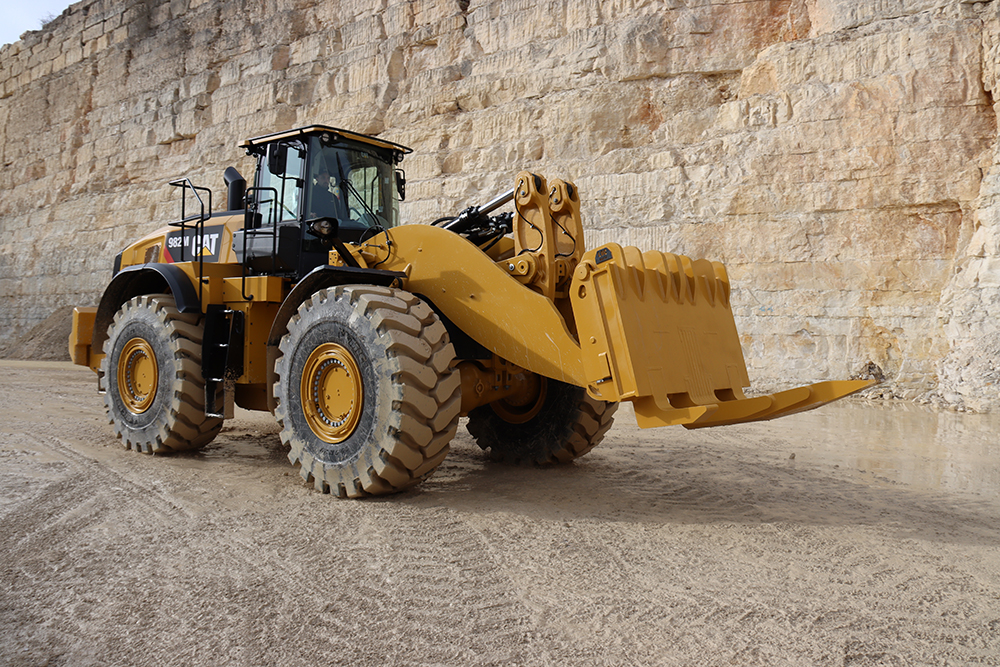
All or nothing. If you enter a new business, you either make it right and invest all your energy in order to establish yourself in the market, or you may as well leave it. Back in 2015, when SH-Jura Steinbruch took over the Jura quarry site in Altmühl valley, Bavaria, southern Germany, not even Josef Seizmeir, the company’s CEO, would have dreamt that the business would grow so rapidly.
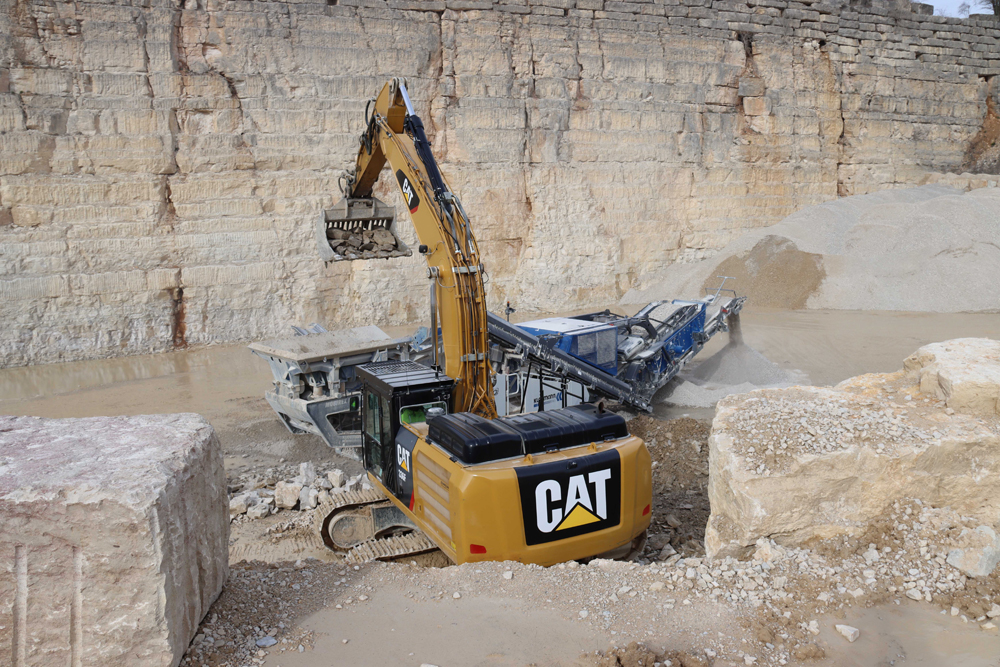
Originally, the plan was for the gravel and material extracted from the quarry to mainly supply SH-Jura Steinbruch’s own construction sites. But other construction companies in the region started to request material from the quarry, and at a much higher rate than Seizmeir had anticipated.
Initially, Seizmeir had planned on an annual production of 100,000 tonnes growing to a demand of 150,000 tonnes in 2019, which was the then capacity of the Jura quarry operation. Consequently, new investments were needed to cater for growing material demand.
“In the beginning the basic idea was to extract and use our own deposit for our construction projects but then we received more requests for grit and gravel because of the level of construction activity especially around the Munich metropolitan area, Ingolstadt and Nuremberg. It is not easy to obtain an extracting licence for gravel and, as such, our building materials produced in the Altmühltal region are in demand. There is an urgent need to provide sufficient [extracting] licences and to simplify the approval process,” explains Seizmeir.
Another reason for the growing demand for SH-Jura Steinbruch’s building materials is the customer focus and flexibility of the company.
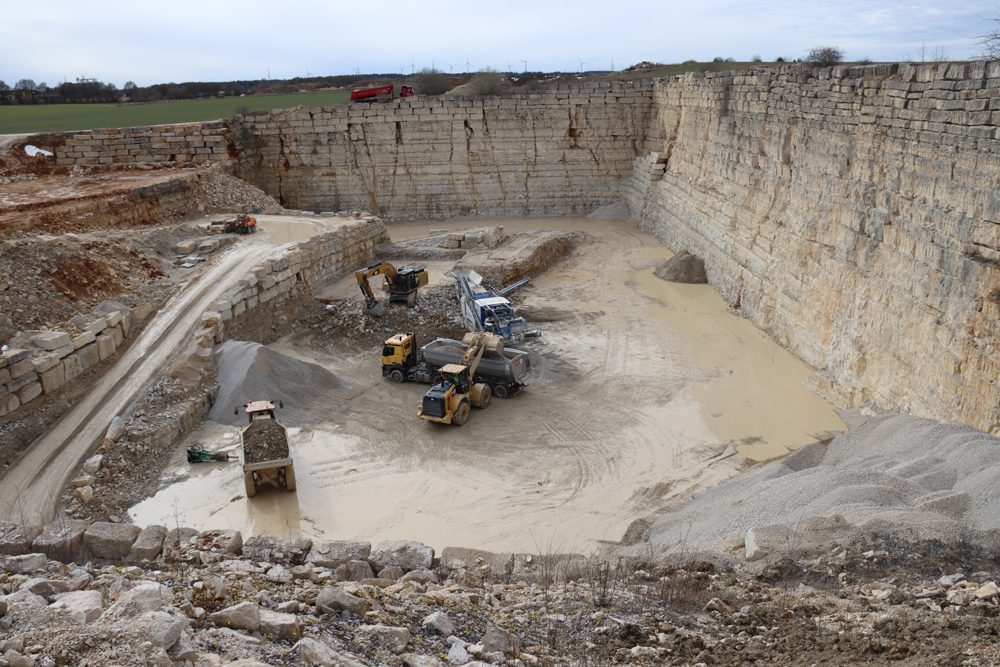
“The customers know that we are not rigid and bureaucratic. Our opening hours include Friday afternoons and Saturday,” says civil engineer Josef Seizmeir junior, who has worked with the company for three years and is now co-partner in his father’s company, working as its construction manager.
The former agricultural building adjacent to SH-Jura Steinbruch’s Jura quarry was acquired so that extraction could expand further. With it, came 1.5 hectares, increasing the site’s surface area to more than 80,000m².
In the quarry, a Cat 336F LN crawler excavator with a hydraulic hammer is responsible for oversize material management and providing material to the crusher. In the yard, a Cat 962M wheeled loader with a 3.8m³ bucket loads the delivery trucks. More recently, a Cat 982M has reinforced the fleet as a primary production machine working at the extraction points.
“With the purchase of the Cat 982M, the company is moving into a new league, in terms of machine size and technology, keeping in mind that the company started as a gardening and landscaping company, using compact equipment,” said Jürgen Karremann, sales director for Bavaria, responsible for the Zeppelin branch in Munich, the main supplier of construction machinery to SH-Jura Steinbruch and other Seizmeir Group companies.
One hundred and fifty million years of the earth’s history has left its mark on the Altmühltal region. The presence of fossils like ammonites testify that a sea once covered this part of the world. The Jurassic limestone deposits have formed in layers which vary in thickness.
In order to extract the limestone slabs from the face, SH-Jura Steinbruch’s Jury quarry operation relies on the superior power of the new Cat 982M, equipped with a ripper tooth. The ripper tooth penetrates underneath the layers and then breaks them out. For that special application, the Cat 982M has been fitted with an additional counterweight.
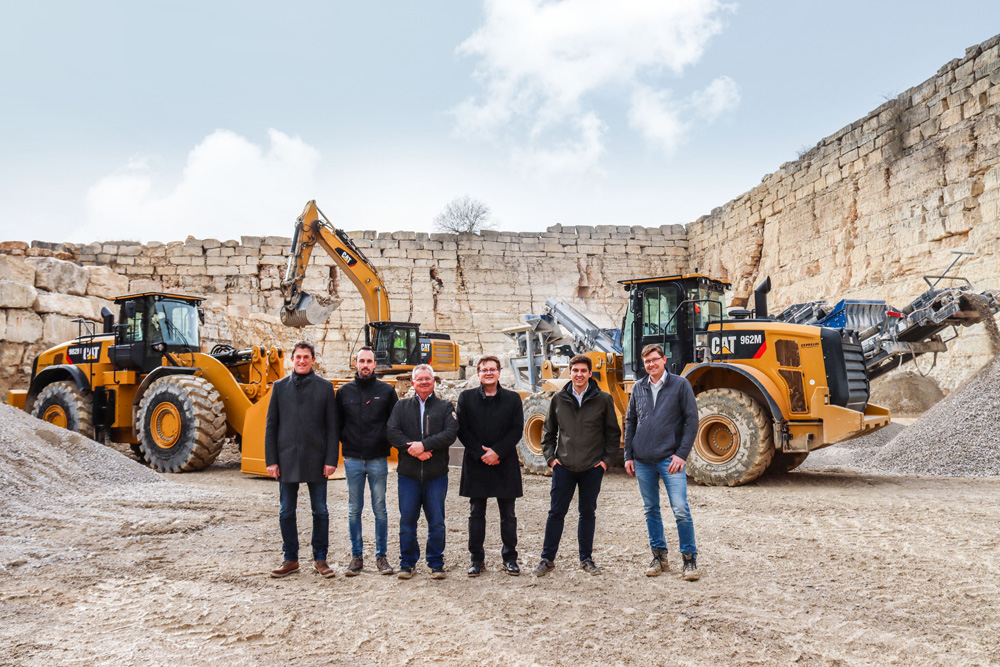
“Quarrying must change so that we can produce differently. In the future, we want to extract from the face blocks, we want to sell them as raw blocks without being processed,” explains Stefan Hausmann, authorised officer of the Seizmeir Group. “Some of the material is too good for grit and gravel and more suitable for better-sized blocks,” adds Josef Seizmeir. “We want to utilise as much as possible of the deposits and minimise waste.”
This explains why the 35-tonne Cat wheeled loader with a ripper tooth was chosen to break each layer. “With the Cat 982M we can reduce the number of blasts and therefore reduce noise emissions in the extraction process,” explains Seizmeir.
In the extraction process, the wheeled loader loosens the stone on the face with the ripper tooth, creating up to 10m³ blocks weighing up to 27 tonnes. After the blocks have been extracted, the Cat 982M is fitted with forks instead of a ripper tooth to carry and load. Josef Seizmeir points out the versatility of the wheeled loader, given its use in breaking, block carrying, overburden removal and cleaning up a deposit. “With that new wheeled loader, we could increase flexibility, so that if any of the other wheeled loaders fail, the Cat 982M can be used to load trucks.”