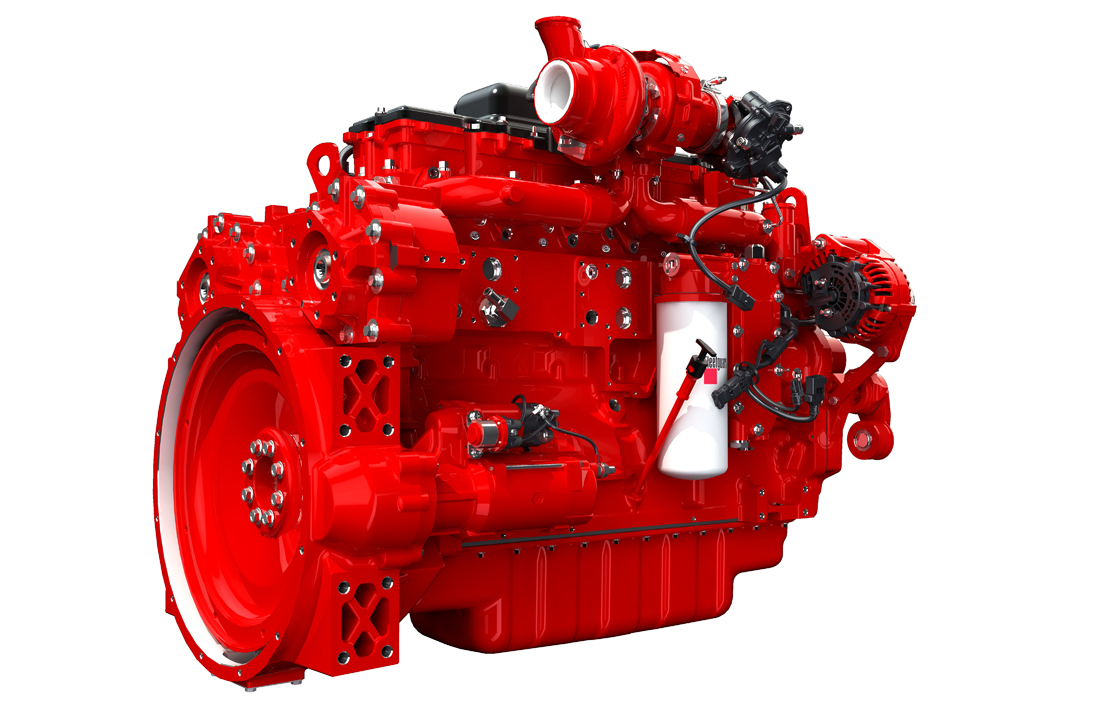
Cummins is among major off-highway engine manufacturers looking for quarrying and heavy construction equipment demand to return to a healthy level as large parts of the world begin to emerge from COVID-19-triggered lockdown.
The US-headquartered company has continued to produce its wide engine range at a reduced capacity since the near total global introduction of lockdowns in the first quarter of 2020. It includes the production of its quarrying-suited 3.8-12-litre, 75-382kW, EGR- (exhaust gas recirculation) free EU Stage V Performance Series power units.
“In the UK, our Darlington and Daventry factories were producing at around 50% when social distancing and lockdown came in. The plant management teams have done a fantastic job in working out how we can keep employees safe, working at a 2m distance from each other, and keep engines moving through the production line. They also modified shift times, so we didn’t have lots of people entering and leaving site at the same time,” said Steve Nendick, Cummins marketing communications director. Certain customers like Komatsu, DAF Trucks and JCB closed down temporarily, so the number of engines needed was reduced, and we were able to keep other OEMs (original equipment manufacturers) up and running through this tough time.”
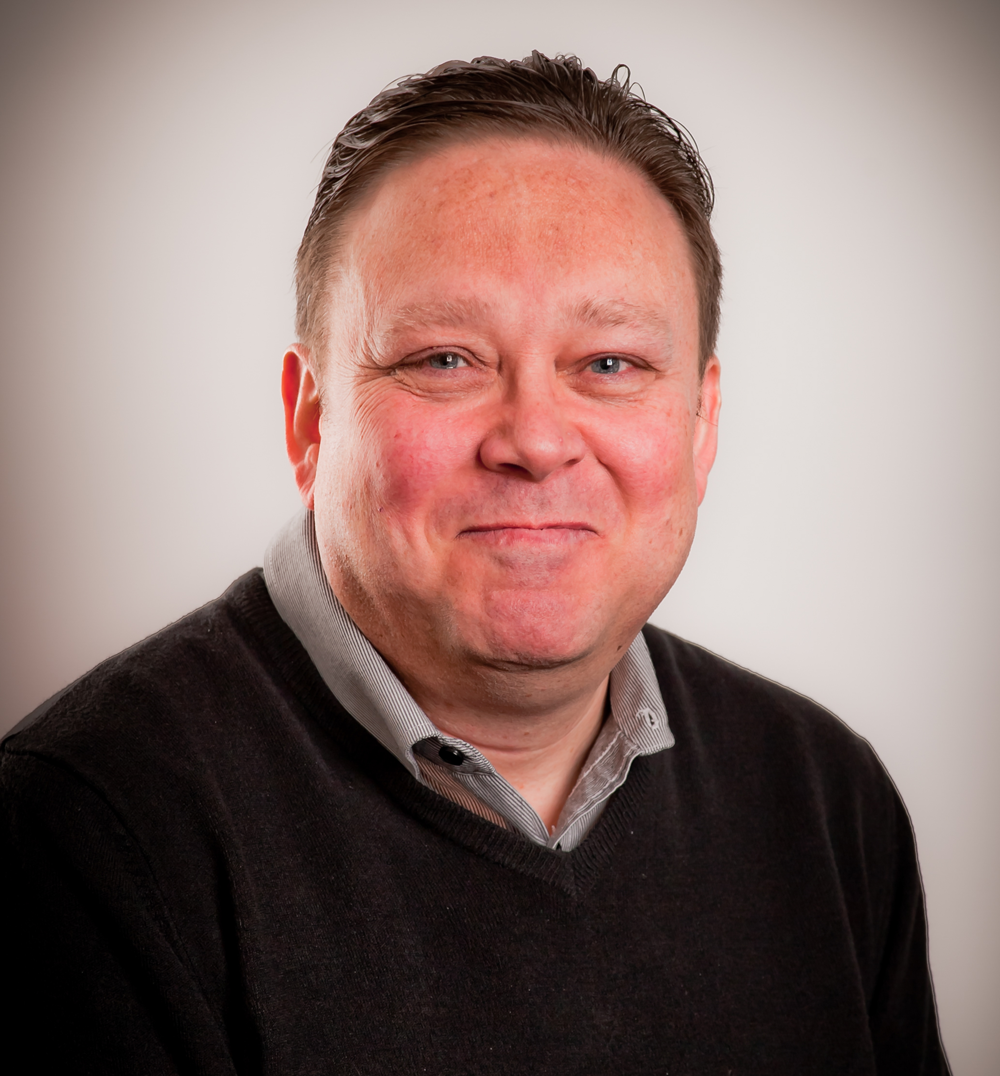
Speaking to Aggregates Business in late May 2020, Nendick says the Darlington and Daventry sites are now back up to at least 80% production capacity. “Things are going well in the UK, and our production in China is pretty much at 100%. The Dongfeng Cummins (Xiangyang City, Hubei Province) plant achieved record monthly production in April. In India, everything was shut down by the government, and is now restarting. In the US, most of our plants are back up and running now.
“Now that production is building back up, the next challenge for the industry is around supply chain. Suppliers are struggling or have shut down because of the crisis, and our team are working through the best ways to manage them.”
Cummins says its B6.7 and L9 Performance Series power units will now feature new engine power take-off (PTO) capabilities to support key applications such as crushers, screeners and cranes.
Launched at Hillhead 2018, Cummins’ power units are available from 75–503kW, delivered as a complete and ready-made package. This comprises an engine, exhaust after-treatment system, radiator and cooling system, plus auxiliaries such as mounting feet, hoses and an air cleaner. Crucially, Nendick notes that more than 60% of the content is pre-approved, making the machine integration process simpler and quicker.
“Our Performance Series power units offer a flexible drop-in solution for manufacturers. Because we were able to remove the EGR and push up the power, we’ve got excellent power density, particularly on the 3.8, 4.5 and 6.7-litre models.”
Such high machine capability, stresses Nendick, makes the Performance Series power units well suited to hard-working applications such as crushing, screening and pumping.
Examples of installations to date include the L9 power units powering Anaconda’s new J12 tracked jaw crusher, and I12 tracked impact crusher. The B6.7 version is available with Bandit in their Intimidator 20XP tree chipper plus NLB Corp’s water-jetting systems.
“When we developed the Stage V Performance Series engines, we dual-certified them to Tier 4 Final for the US. That was one of the real benefits that Anaconda saw. It meant they could take the engine and package and build the same machine, whichever region it was destined for. From a production flexibility and capability perspective, they got a really good solution.”
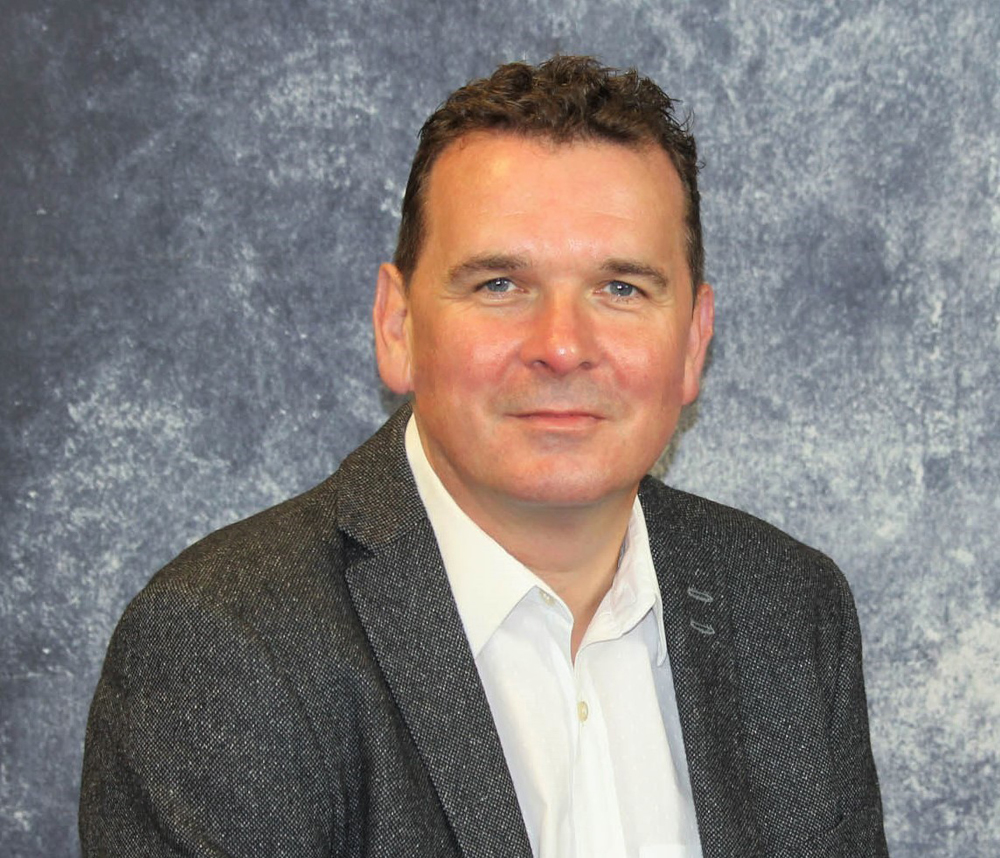
Nendick explains that to increase the flexibility and capability of the Performance Series power units even further, Cummins is integrating new single and dual rear-engine power take-offs (REPTO). These complement its standard PTO capability used for items such as hydraulic pumps. Cummins is also making these available on the base engines without the pack.
As an example, fitted with the dual REPTO, the L9 will have a total drive capability of 560Nm. This will make the engine capable of driving additional pumping capability through SAE B two and four bolt mounts. Integrated into the flywheel housing, the dual REPTO is compact and has a minimal impact on engine packaging. The added weight is approximately 100kg.
“For equipment manufacturers, they have the ability to efficiently drive more from the engine without the need for additional aftermarket systems. This would support the driving of hydraulic pumps for all sorts of machine functions from steering systems to fans, etc. It will reduce installation costs and complexity for a more integrated solution,” says Nendick. “I think the Performance Series power units plus the addition of REPTO, puts us in the driving seat to increase our business in the crushing and screening sector.”
John Deere Power Systems (JDPS) will begin full production later this year of its new CONEXPO/CON-AGG 2020 exhibition-showcased JDPS 13.6-litre diesel engine (300kW to 510kW). The engine is said by Martin Ryley, JDPS worldwide business development manager, to be well suited to large crushers involved in quarrying applications.
Peak torque for the new 13.6-litre unit is 3050Nm with a series turbocharger, an 11% increase over previous models. With a single turbo, the peak torque rating is 2510Nm. The new diesel has up to a 6% fluid economy advantage, while heat rejection reduction is over 20%.
The JDPS 13.6-litre engine was built with a “clean-sheet” design, offering new levels of performance, serviceability and integration — all key characteristics for OEM customers. This design process — which now includes a DPF- (diesel particulate filter) free solution for Tier 4 Final variable and constant speed markets, in addition to the dual-certified solution for Tier 4 Final/EU Stage 5 markets — was driven specifically by customer requirements.
“We leveraged and optimised our proven technologies developed over the years to best address market and customer needs in heavy-duty applications. This ensured the final product would deliver increased performance and overall value to our OEM customers and end users,” says David Hoffman, director of worldwide marketing, sales and customer support at JDPS.
JDPS and its distributors are now accepting orders for the 13.6-litre engine.
Speaking to Aggregates Business, Ryley said JDPS is also developing an 18-litre, 500kW-plus engine for large quarry plant. The engine is earmarked to be available at some stage in 2022.
The new 18-litre model will move the top end of the JDPS power range to over 650kW. The engine, which will be JDPS’s biggest ever, will be built at the company’s Engine Works facility in Waterloo, Iowa, US. The launch of the unit will be timed, says Ryley, to coincide with construction and quarrying equipment makers’ product development plans.
Ryley says JDPS engines are ideal for quarrying applications due to their robustness and John Deere-proven high performance and reliability. The company has a wide range of engines for quarry plant, and Ryley stresses that this is an important part of the company’s business. JDPS engines are used in quarrying plant manufactured by a number of major global players such as Terex and Rubble Master. Both variable speed engines for industrial applications such as quarrying crushers and screeners, and constant speed engines for generator driven screeners, are available from JDPS.
Ryley notes that JDPS has consistently used high-quality diesel particulate filters (DPF) to meet off-highway engine emissions regulations as they’ve evolved over the years. The company, he says, is very proud of its record in this area. “We started with DPF in 2011. Not many of our competitors did. We have used that experience in hundreds of applications to make it work in even the most challenging of conditions. We’re very confident in our DPF solutions.
“We also have a strong focus on fluid consumption – optimising the mix of diesel exhaust fluid (DEF/AdBlue) and diesel to get the lowest machine running cost for operators.”
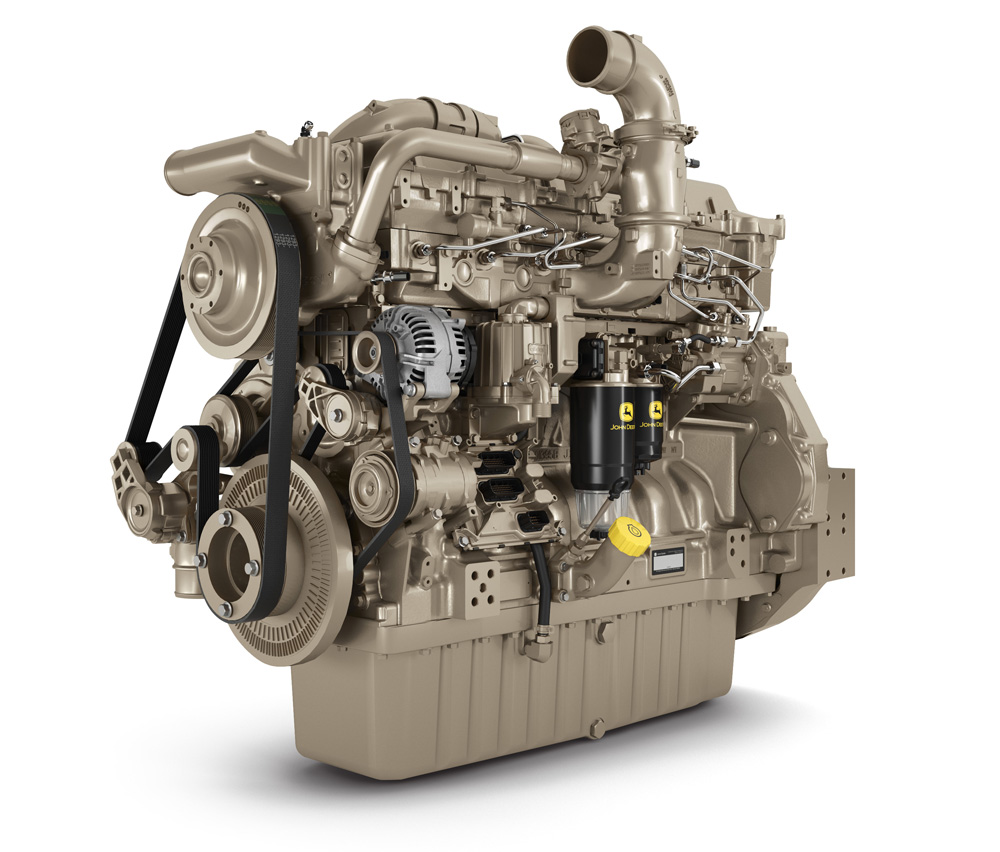
Ryley says that JDPS is looking to bring out an engine predictive maintenance solution/s in the next couple of years. “It’s what’s next – putting more engine data and control over maintenance into customers’ hands. John Deere is already developing predictive maintenance solutions for its machines, and we’ll apply that to our engines.
“Preventing machine breakdown is absolutely vital when it comes to quarrying. If one piece of equipment goes down, the whole production chain goes down, and it becomes very expensive.”
Ryley adds that the firm was also investing heavily in electrification - to meet the growing demand for fully electric and diesel electric drives for quarry and general construction plant and vehicles. “The benefits of electrification are enormous: it creates opportunities for much higher operation efficiency, much higher productivity, lower fuel consumption, and to downsize engines required on some machines.
“For a number of years now, John Deere has had a diesel-electric hybrid wheeled loader [the 944K] on the market. It’s an indication of where we see the market going.”
FPT Industrial, the global powertrain brand of CNH Industrial, has acquired Potenza Technology, a company specialising in the design and development of electric and hybrid powertrain systems.
The March 2020-announced acquisition represents another step in FPT Industrial’s path towards electrification, one of the pillars of its multi-power strategy.
“Sustainable powertrain technology is of increasing global focus and concern. Here at CNH Industrial we are committed to delivering solutions, which not only reduce emissions and enhance productivity but which deliver future-proof technology for the long term,” said Hubertus Mühlhäuser, chief executive officer, CNH Industrial. “This, our latest acquisition, is further testament to this.”
“FPT Industrial is acknowledged as a leader in alternative propulsion systems. The acquisition of Potenza Technology will further enhance our brand’s accelerating development of sustainable electric powertrains across a range of operating segments,” said Annalisa Stupenengo, president Powertrain, CNH Industrial.
Potenza Technology, based in Coventry, England, has been at the forefront of electric powertrain technology since 1999. The company has specific expertise in functional safety, battery management systems for traction battery packs, and electrical and electronic systems design and development.
Major global off-highway machine engines player Perkins has appointed Onnyx as its authorised distributor for Algeria.
A family-owned business, Onnyx has 18 years of experience with Perkins engines as a second-level dealer (DPA) since 2002.
Headquartered in the UK with an operations branch in Algiers, Onnyx has already established a strong 21-person team focused on engine and parts sales and the delivery of 24/7 technical service support to Perkins-powered customers.
“I’m excited to be working with Onnyx, which, through its former role as a second-level dealer, has a proven reputation for delivering customer service and quality,” said Jaz Gill, vice president of global sales, marketing, service and parts at Perkins. “I’m confident this highly experienced team will provide the consistent service our customers in Algeria expect and deserve.”
“This is more than a collaboration,” noted Khaled Terai, country manager at Onnyx. “Becoming a Perkins distributor opens many more opportunities for us. With the best-in-class range of engines, the largest genuine spare parts stock in Algeria, premium product support and the best service team in territory provided by Perkins-certified engineers, we always target excellence to deliver the best customer experience. This is our commitment and promise.”