Cemex updates its brand as part of an ongoing evolution
Cemex has unveiled an updated brand in line with its ongoing evolution to help the world reach the next frontier of sustainable living by becoming a more agile, innovative, and approachable company.
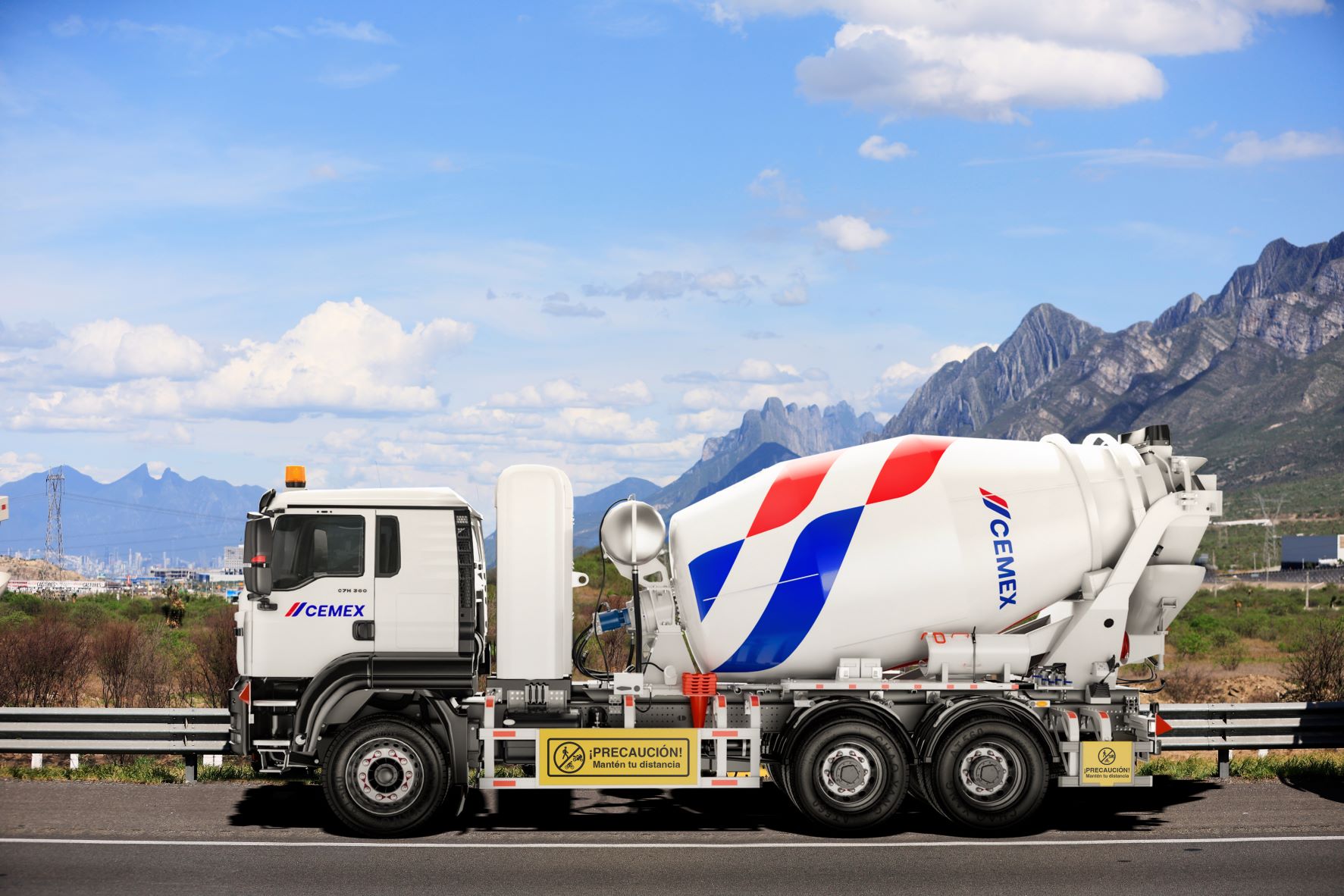
Hauling opportunities from Franco-Italian rail link
The Turin–Lyon high-speed railway is one of the projects providing major opportunities for hauler manufacturers in Europe, involving extensive earth-moving and construction.
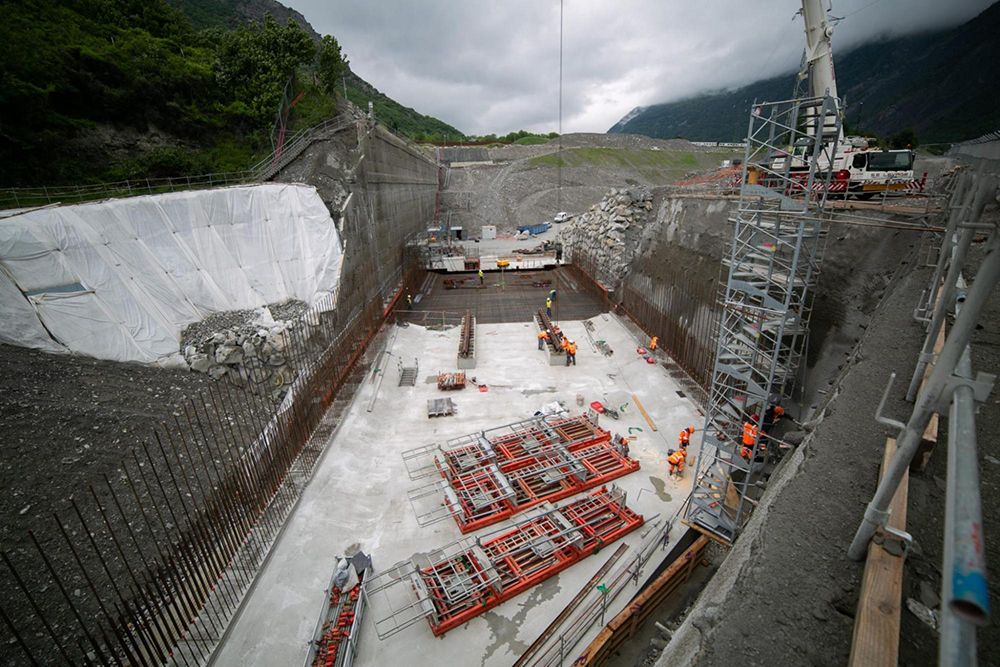
Over 139,000 attendees at biggest-ever CONEXPO/CON-AGG exhibition
After five jam-packed days of innovative product launches, major company announcements, enlightening education sessions and countless networking opportunities, CONEXPO-CON/AGG & IFPE 2023 have come to a close, but not before taking the construction industry to the next level.

Smiley Monroe Zip Clip turning downtime into dollars
Smiley Monroe is turning more and more US mobile materials processing downtime into dollars as demand rises for its high-quality Zip Clip replacement conveyor belting.

Holcim's ECOPact Low-Carbon Concrete wins CONEXPO-CON/AGG & IFPE 2023 award
Holcim's ECOPact Low-Carbon Concrete has been selected as the CONEXPO-CON/AGG Next Level Awards Contractors' Choice in the inaugural awards program at CONEXPO-CON/AGG and IFPE 2023.
The Next Level Awards celebrate exhibiting companies pushing the boundaries and developing next-level products, technologies and services designed to advance the construction industry.
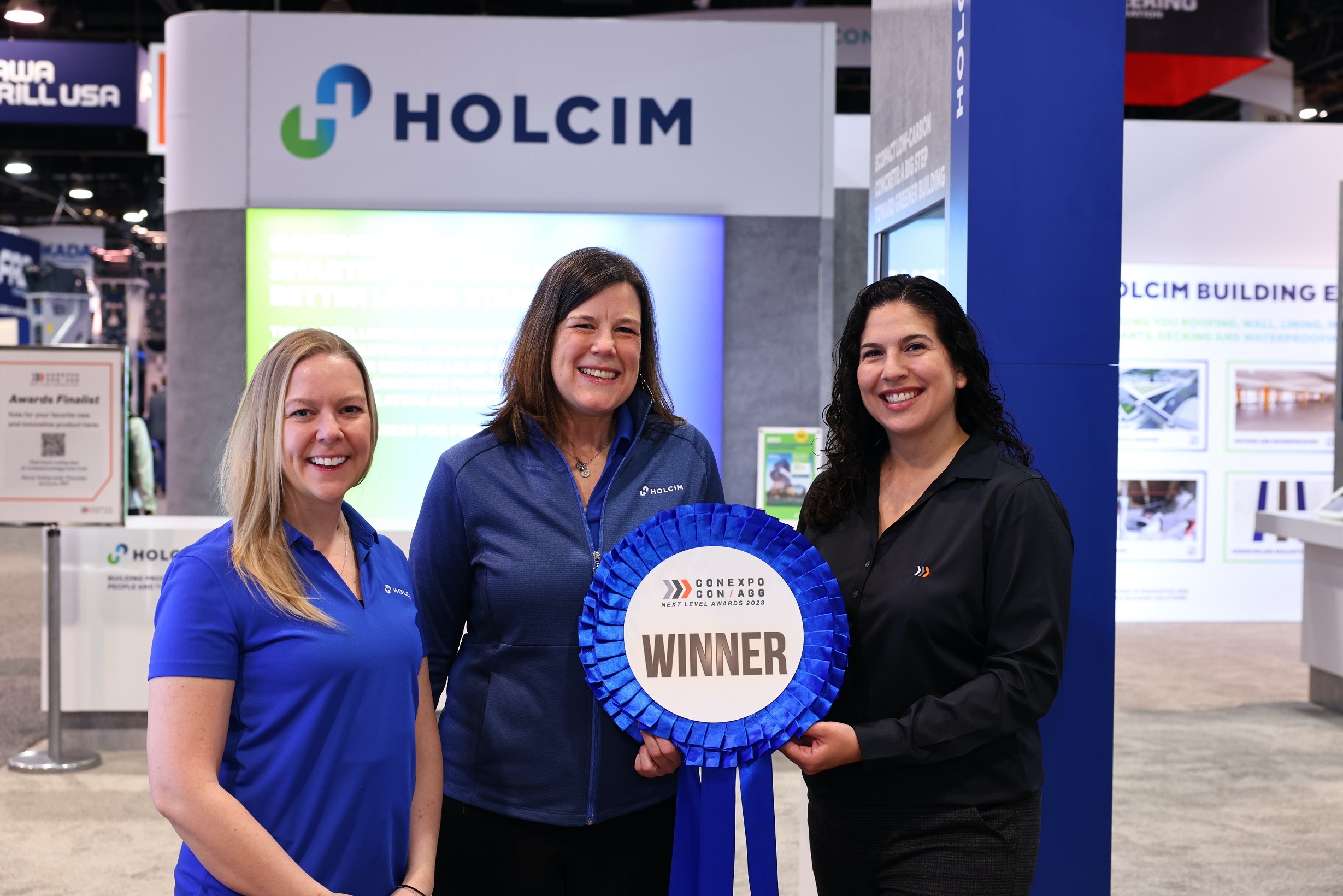
The future is looking greener and cleaner at CONEXPO-CON/AGG 2023
Turn dirt into dollars. Join our expert editors as they review CONEXPO-CON/AGG 2023 … a show full of great new ideas for recycling, alternative fuels, safety, and revolutionary power systems.
Read more on our CONEXPO-CON/AGG 2023 Daily News website
Simex cold planer gives 80 inches of pure paving power
Cummins goes fuel agnostic as it heads for destination zero
Cummins is future-proofing its internal combustion engine options developing a “common base range” of power units that can be adapted to run on natural gas, hydrogen, or diesel by making a few simple alterations...
Rokbak RA30 & RA40 ADTS are a big US hit
“Rokbak is seeing huge demand for its RA30 and RA40 articulated haulers in the US,” says Robert Franklin, Rokbak’s director of sales – Americas. “The US is leading articulated hauler demand globally with huge infrastructure spend. There is a lot of construction activity at the moment around house and road building, so we are keen to meet with customers and discuss how the RA30 and RA40 can help with these projects.”
The 28.9tonne maximum payload RA30’s new transmission and high-performance 276kW engine improve fuel efficiency, operator comfort and, with 1880Nm maximum torque, delivers power when operators need it. The new transmission retardation system is combined with exhaust brakes and fully enclosed oil-cooled multidisc brakes to cut operating costs and increase safety and stability. The RA30’s drivetrain is also said to be perfectly balanced to provide excellent performance and productivity in all hauling conditions.
Ground-level test points, a fully tilting cab and an electronically raised hood, make the RA30’s servicing quick and easy – maximising uptime.
Furthermore, Rokbak’s bespoke Haul Track system gives RA30 hauler operators more visibility and control of their machines, with live data viewable on desktop computers or mobile devices. This allows companies to protect their investment even when not on-site.
The 38tonne maximum payload, 331kW high-performance engine equipped RA40 is a heavy-duty articulated hauler said to make light work of large-scale quarry, mine, and construction jobs, offering high capacity and claimed high performance in the toughest conditions.
The RA40 benefits from the same transmission retardation system, fully adaptable drivetrain, easy maintenance, and Haul Track system as its smaller RA30 sibling. The RA40’s planetary gear transmission is said to deliver smooth, efficient gear shifting, cutting fuel costs and increasing operator comfort – even under the most challenging conditions.
With sustainability in mind, the Rokbak event booth materials are all recycled or reusable. Two 40ft customised shipping containers, adorned in the recognisable Rokbak aesthetic, will be used for meeting rooms and product information displays. Following the event, these will be shipped back to Motherwell, Scotland, for reuse at future events.
Booth Festival Lot F8926
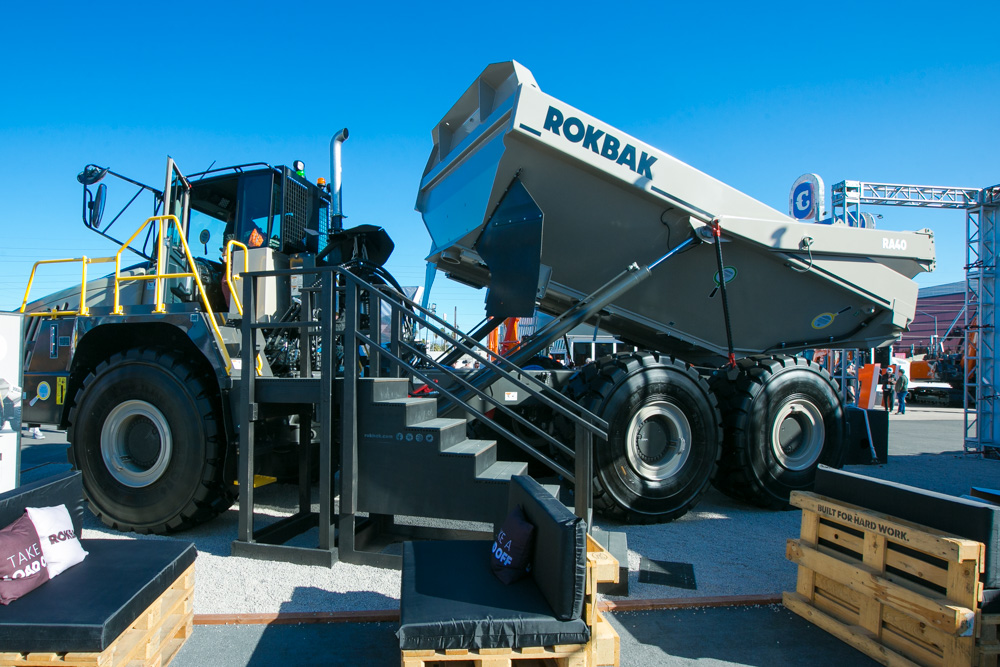
CAMS debuts APR 1000-2S concrete and asphalt recycling shredder in North America
The Italy-headquartered company has had a presence in the North American market for 18-months through its CAMS America operation. The APR 1000-2S was launched in Europe in 2019.
The APR 1000-2S is a hybrid diesel-electric machine that combines the features of two shredders, one iron separator and a screening unit in a single tracked machine. CAMS says it is the perfect solution to recycle slabs and milled asphalt with low fuel consumption, running costs and environmental impact.
The machine incorporates three shredding stages plus a screening unit in one machine. It has the ability to handle steel chunks (including toolholders, manhole covers and steel bars)
The APR 1000-2S features a patented hydraulic pusher system, output weighing system, remote service, and can be transported with one standard size truck.
Features include built-in specific crushing programmes depending on the type of material, the capability to process wet materials, low dust and acoustic emissions, and the ability to provide electrical power on-site.
Booth C32848/C32649
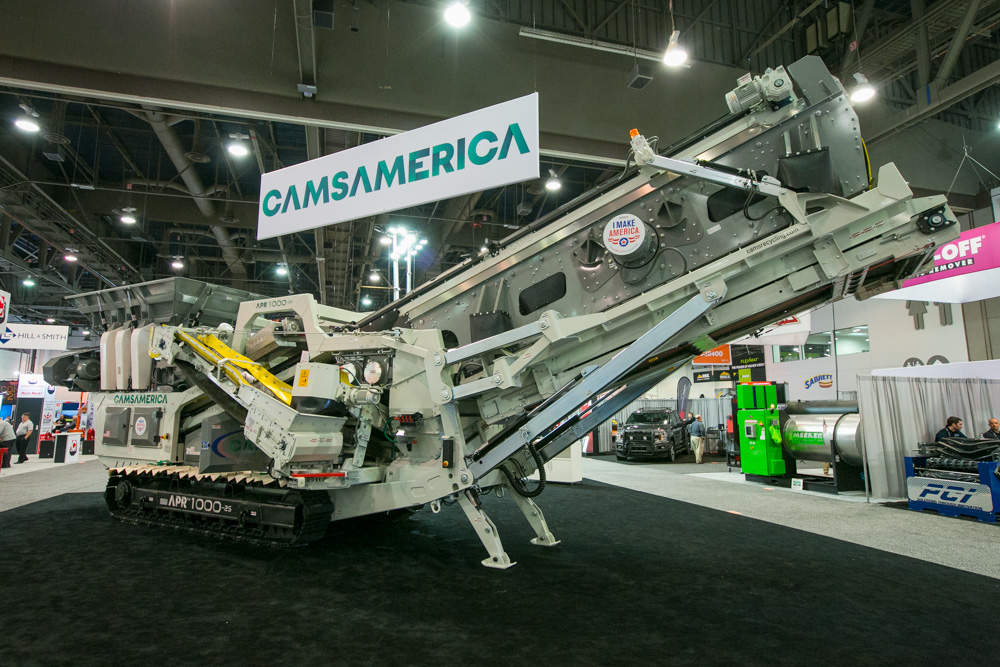
SBM have big hopes for AI-inclusive REMAX 600 after first ten orders
Extensive sensor technology, including cameras, records and evaluates the REMAX 600’s feed material as well as intermediate and end products. In real-time, those values reach centralised digital labs at SBM, where they are further analysed. Necessary adjustments are then made on the ‘digital twin’ of the working machine and re-transmitted directly to the REMAX 600 in the field.
Known as ‘Crusher 4.0’ and developed together with the University of Leoben, the REMAX 600 was presented at the bauma Munich exhibition in October 2022. Large-scale field tests of a REMAX 600 are currently being carried out at an Austrian quarry partner.
“We have made three REMAX 600 plants so far. The first has already done 1500 hours of testing with an Austrian quarry customer. All has been good so far on testing,” said Erwin Schneller, SBM managing director. “The first sold machine will be delivered to a customer this year, with the others being delivered by mid next year.”
Another big machine for SBM is the JAWMAX 400 jaw crusher, said to feature one of the most advanced diesel-electric drive concepts on the market. A combination of a fuel-efficient onboard diesel and a performance-tuned generator powers the plant’s materials processing.
SBM’s mobile plant range comprises 12 track-mounted JAWMAX jaw crushers and REMAX impact crushers, capable of 250 – 800tph production. The plant range shares the same innovative drive concept, with fewer hydraulics ensuring less risk of failure, lower maintenance and parts inventory costs, and thus higher availability, says SBM. Overall savings from running the plants can, says the OEM, be 40% to 75%.
SBM sees the US as a major growth market. Schneller said very good discussions are taking place with a number of potential dealer partners in different parts of America. “I think there is the potential for us to sell 50 machines a year in the US,” he added.
Booth Outdoor Silver Lot 1-2 S-5600
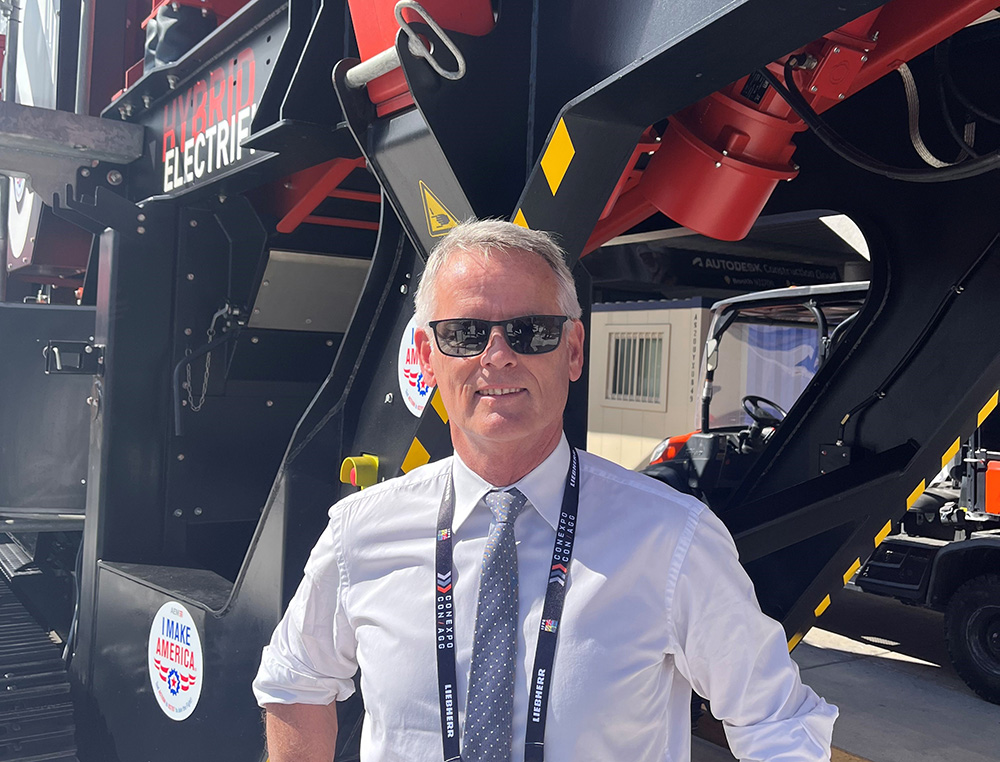
Astec keen to help US asphalt plant customers comply with new greenhouse gas reduction legislation
Astec CEO and president Jaco van der Merwe has stressed the importance of helping American asphalt plant customers comply with new US greenhouse gas reduction legislation.

Holcim acquires HM Factory to enter precast market in Poland
Holcim acquires HM Factory, a provider of precast concrete solutions with net sales of CHF 18 million.
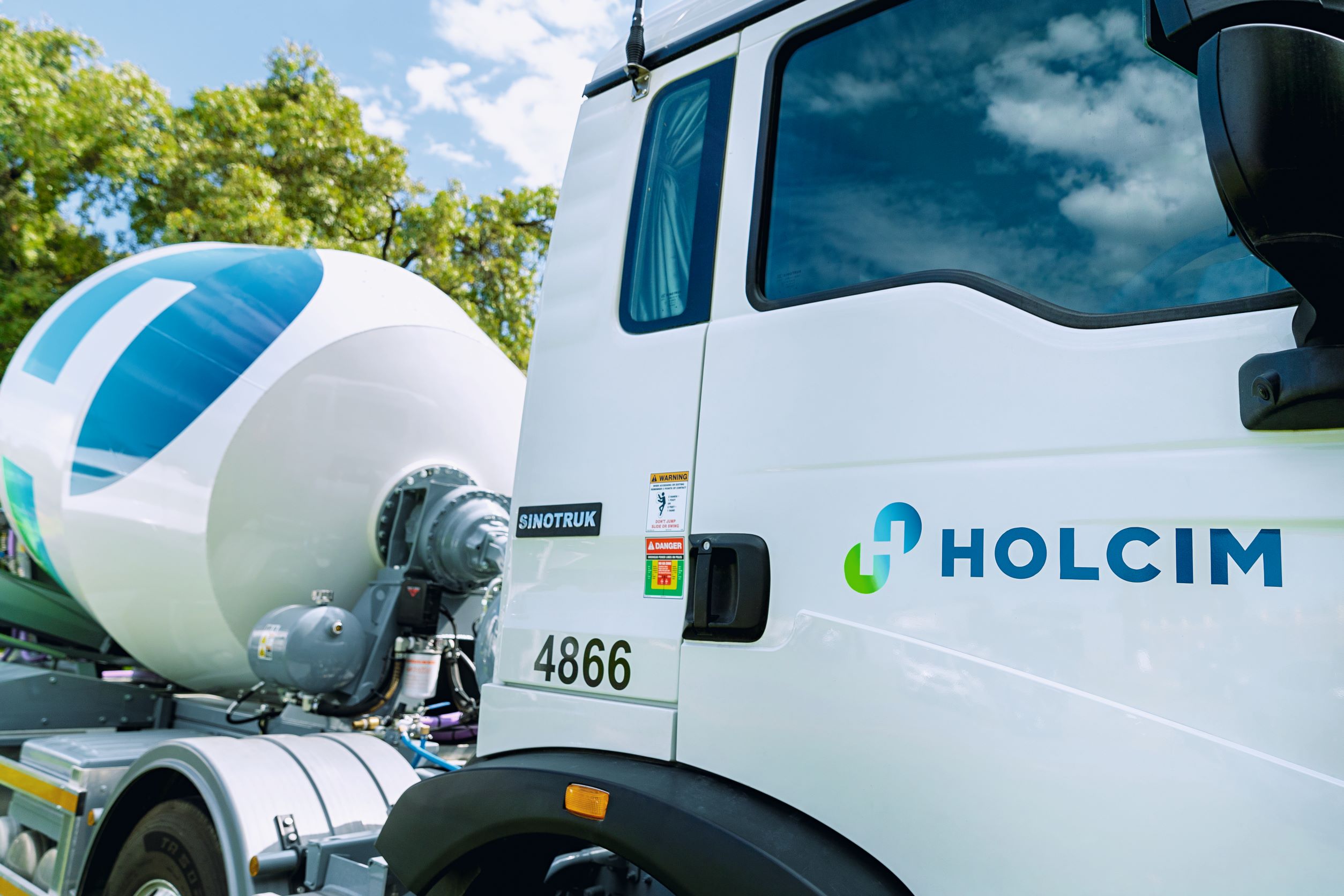
Epiroc accelerates the transformation as its autonomous drills reach milestone
Epiroc, a leading productivity and sustainability partner for the mining, quarrying and infrastructure industries, continues accelerating its customers' transformation toward lower emissions, strengthened safety, and higher productivity. The Swedish company's autonomous drill rigs have now achieved another milestone by successfully drilling the equivalent length of more than one round worldwide.
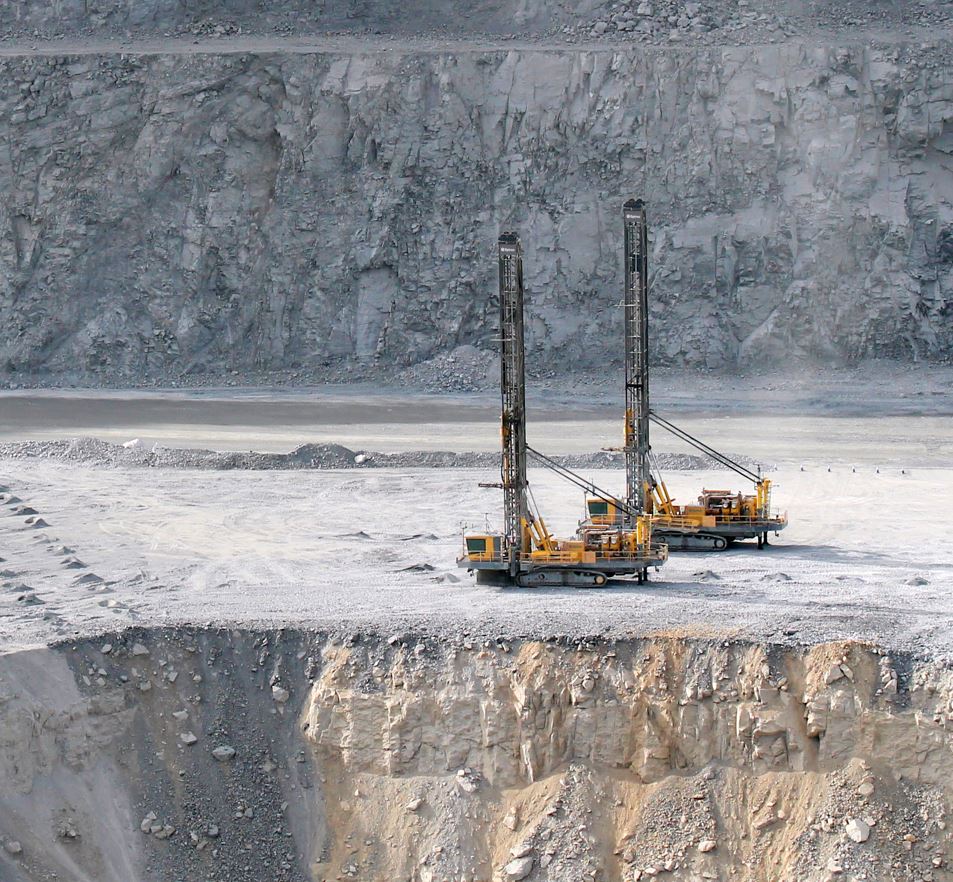
Soaring prices concern for stakeholders
After the huge disruption of COVID-19, the construction industry and aggregates demand have recovered in the Philippines, Vietnam, and Thailand
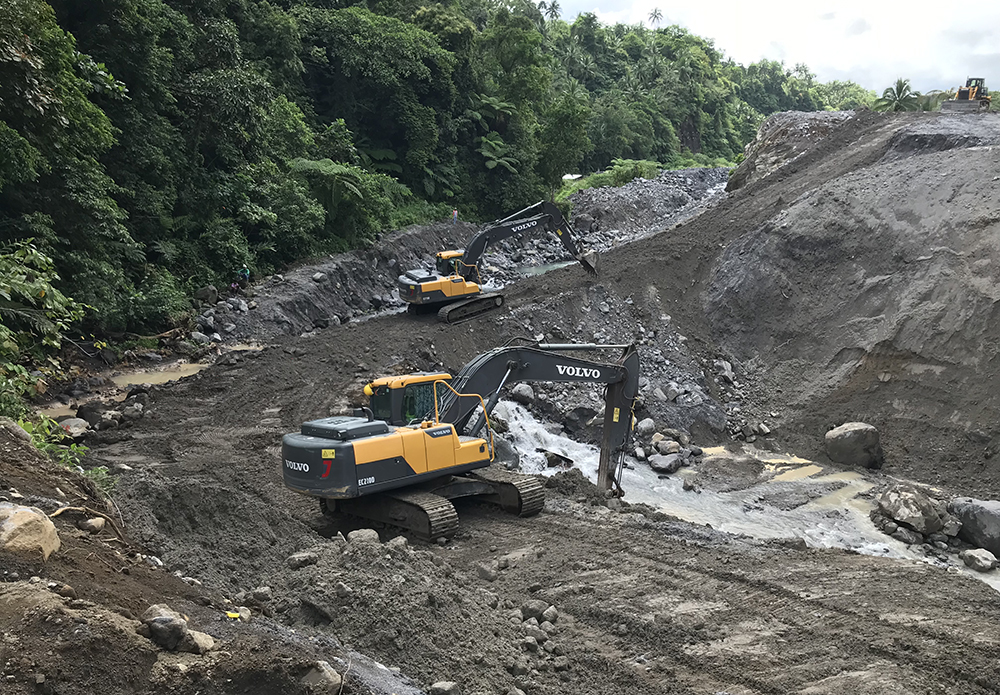
Bobcat unveils new RogueX autonomous concept machine and ‘world’s first’ all-electric skid-steer loader
The launch of the S7X follows the 2022 release of the Bobcat T7X all-electric compact track loader. Bobcat says it plans to commercialise the prototype S7X.
The next-generation RogueX is purely a concept machine, with no plans currently for commercialising it. The machine is designed to explore the capabilities of electric power, autonomous operation and dual lift-arm geometry.
Doosan Bobcat North America president Mike Balweber said of the new machines: “We have launched more models in the last five years than in the previous 50 years of the company’s existence.”
Like the T7X, the S7X is all-electric, and is powered by a 60.5kWh, lithium-ion battery. It features electric drive motors and utilises ball screw actuators for lift and tilt functions.
Bobcat says that, together, the battery and electrical powertrain generate incredible performance characteristics, with instantaneous torque that is as much as three times greater than traditional loaders. The powerful loader is designed to balance sustainability and performance with zero emissions and is equipped to outperform its diesel-powered equivalent.
The S7X skid-steer loader is designed to offer operators a smooth and comfortable experience with minimal vibration and nearly silent operation. The S7X can operate for up to 8 hours on a single charge depending on the application, giving most operators more than a full day’s work when breaks and downtime are considered. A full charge takes approximately 10 hours.
“As the inventor of the original skid-steer loader, we are excited to take the machine that created the industry and reinvent it all over again,” said Joel Honeyman, Doosan Bobcat VP of global innovation.
“The S7X is an incredible product with real-world application that can support operators on environmentally sensitive sites, in noise-restricted areas and for indoor operation.”
While most closely resembling a track loader, the RogueX machine was built as a research and development project, and as a proving ground to advance the Bobcat innovation roadmap, evaluate customer perceptions and test the limits of machine functionality.
“RogueX was concepted with consideration for the worksite of the future and how a customer’s needs may evolve — with a focus on ease of use, remote operations, autonomous functionality, sustainable operations and features that allow operators to accomplish more with one machine,” said Honeyman.
As jobsites change and operators turn to remote operation, Bobcat took its concept further by fully eliminating an operator station. The machine is designed to explore the idea of operating where humans cannot go, to tackle more work in more places than ever from a remote position.
By building the loader without a cab and using advanced kinematics, RogueX features next-generation functionality including both vertical-path and radial-path lift capabilities in one machine. The machine produces zero emissions as it features a lithium-ion battery, electric drive system and no hydraulics. “After our successful development of building an all-electric loader [the Bobcat T7X], we wanted to think bigger, broader and take a leap far into the future,” said Matt Sagaser, director of innovation accelerated at Bobcat.
“RogueX sets a framework for what is possible, and our team is just getting started on what is next.” RogueX is in the early research and development stage at Bobcat.
Booth W41544
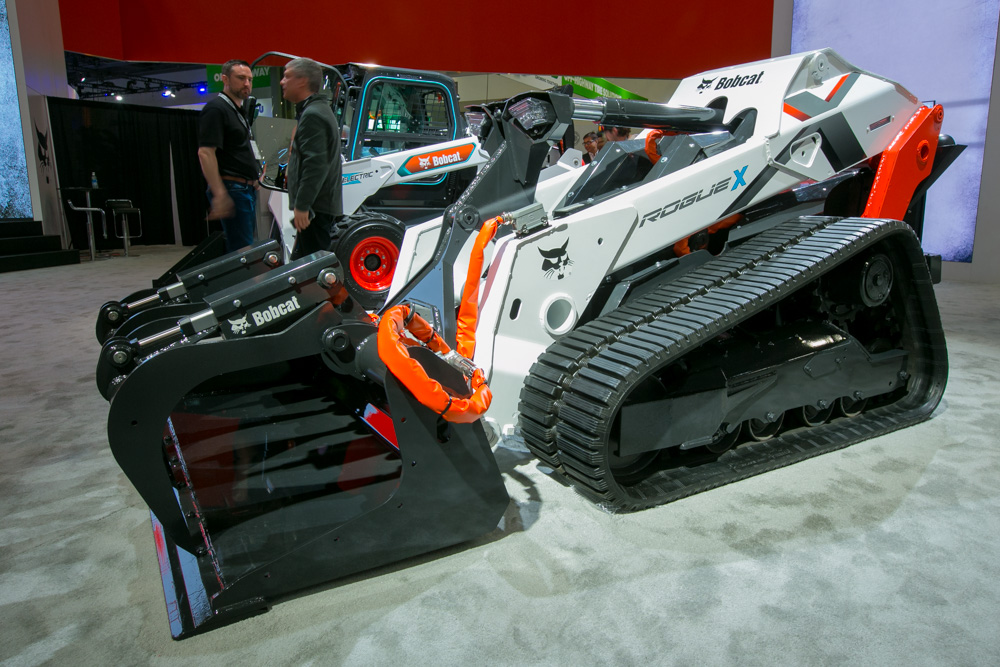
CDE’s AggMax 253SR scrubbing and attrition system
At its launch, Ko Shiozaki, Kubota manager for sales promotions in the engine division, said that the V3307 provides power assistance during peak performance, using electric power to compensate for high loads instantaneously.
For some applications, high load is required for only a fraction of the total work time. The engine’s 10kW electric motor-assist function allows customers to match those high load demands and select an engine with an output power tailored to the low and medium load regions of frequent use.
The engine has a straightforward design with three main components: a DC converter, a lithium-ion battery, and a motor generator attached to the existing engine model.
The hybrid system is controlled by the engine control unit (ECU). This is made possible by rewriting the software in the existing ECU, available only to Kubota engines, according to the manufacturer. No additional ECU is required for hybrid control.
The engine is equipped with a 48V motor generator, providing high torque with quick response – boosting overall work efficiency. At low speeds, the motor provides up to 70Nm of torque assistance.
Designed for applications that demand an immediate response to instantaneous peak overloads within the typical machine duty cycle, the power assist Micro-Hybrid system supports the engine by delivering an additional electrical power boost of up to 10kW.
An instantly available torque curve offers efficiency boosts at the most crucial time, while recuperating and recharging its battery pack when not initiated, says Kubota, adding that these innovations push the boundaries in areas of fuel efficiency, power density and adaptability.
Booth South Hall Level 2, S84415
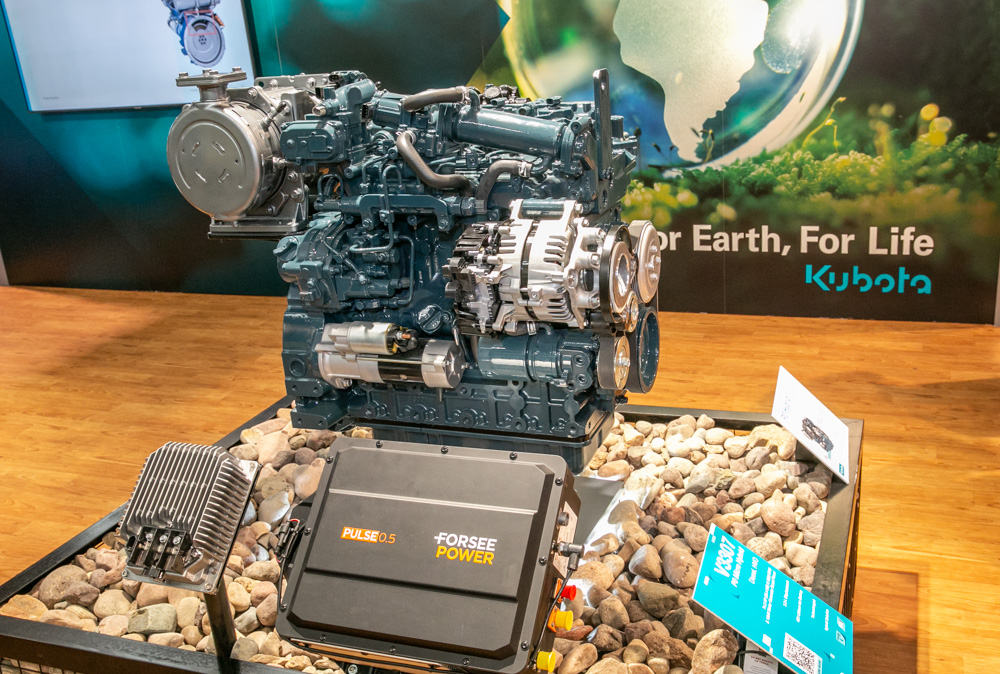
CDE looking to turn more North American dirt into dollars
With 30 years of experience providing optimised, proven solutions to customers worldwide, Cookstown, Northern Ireland-headquartered CDE’s technologies have successfully diverted more than 100 million tonnes of CD&E waste from landfills, while turning construction, demolition and excavation (CD&E) materials into high-specification outputs.
The company’s AggMax scrubbing and attrition system, its Counter Flow Classification Unit (CFCU) for density separation and the EvoWash sand classification and dewatering system are among its proven plant solutions.
“We all understand that the depletion of natural aggregates is happening at a rate that is pretty scary. CDE has proven solutions that will slow that consumption of materials,” said Darren Eastwood, business development director at CDE.
“We’ve been proving our solutions for the past 20 years, and in the last number of years have brought them to the US and Canadian market. The recycling of inert and contaminated construction, demolition and excavation wastes can make a big difference to the construction industry across those countries, easing the pressure on landfills. It also eases the pressure on the trucking industry, which is often having to shift materials over long distances into cities. Most importantly, it eases the pressure on existing quarries and the valuable precious material that they have. We can also keep required material as close to the demand centre as possible.”
Eastwood said CDE’s two latest US recycling customer plants have gone live in California and Pennsylvania. The California plant is the first CDE sale in the Golden State. It will treat and process a variety of construction and demolition wastes. “This will make a big difference to the circular economy there. It will produce dependable recycled products for surrounding cities while doing away with the need for excessive long-distance trucked materials supply. It will also have a big impact in lowering the cost per tonne of production and in the gas trucks need to use.
“The Pennsylvania facility is a stone’s throw from a city centre. It will be producing C33 [product] and a range of aggregates.”
Booth C30269 (Central Halls 3-5)
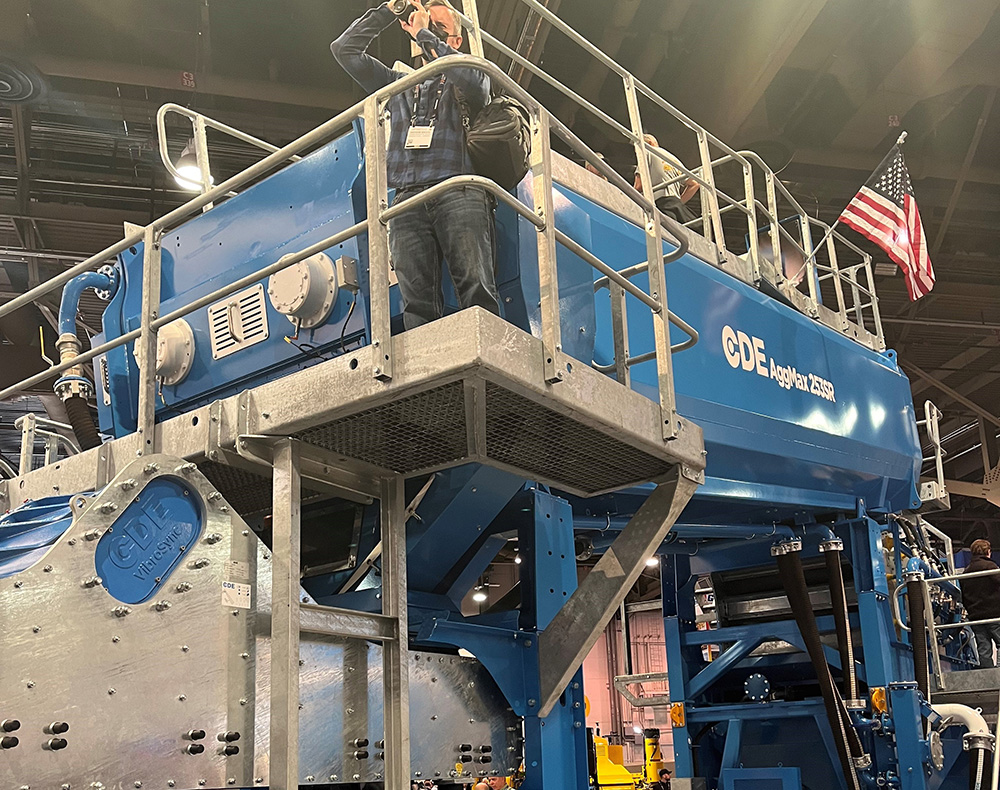
Keestrack unveils B7H hydraulic jaw crusher for US market and tough rock conditions
The 70-tonne B7H hydraulic jaw crusher has a 30-tonne jaw and is adapted from Keestrack’s existing B7 electric jaw crusher which was launched in 2018.
It has a vibrating feeder with 2-step grizzly of 2,200mm x 1,080mm (LxW) and a bottom deck in wire mesh of 1,450mm x 870mm (LxW) to optimise crushing results and to reduce wear.
The feed size of the material is up to 700mm, the feed opening is 1,200mm x 830mm and the outlet adjustment CSS is min.-max. 75mm–250mm.
The jaw crusher is equipped with the patented NSS, non-stop system, which protects the crusher from uncrushable feed and resets the CSS automatic during operations.
Keestrack sales director Frederik Hoogendoorn says the mobile crushing and screening equipment company is a pioneer in electric quarrying and mining machinery, having launched its first electric machine in 2006.
He adds that 90% of Keestrack machines are available in three versions: hydraulic, electric, and zero-emissions plug-in.
“A focus on sustainability is at the core of our company as this is the origin of our business,” Hoogendoorn said.
“Producing and recycling valuable raw materials is what mobile crushing and screening is all about, and our efforts are definitely having a positive impact on the ecological footprint.”
“As these heavy duty industries need very powerful drive systems, Keestrack kept on searching for alternative drive systems,” Hoogendoorn explains.
“From load sensing hydraulics to e-drives to Zero drives, (Keestrack offers) equipment with no combustion engines on board but only electric motors. This request is also a pull from mostly the North European market. This way we want to protect the planet and save money at the same time.”
He adds that 80% of US customers currently ask for hybrid machines and only 20% electric, but that this is changing with all-electric units becoming more common in the US market every year.
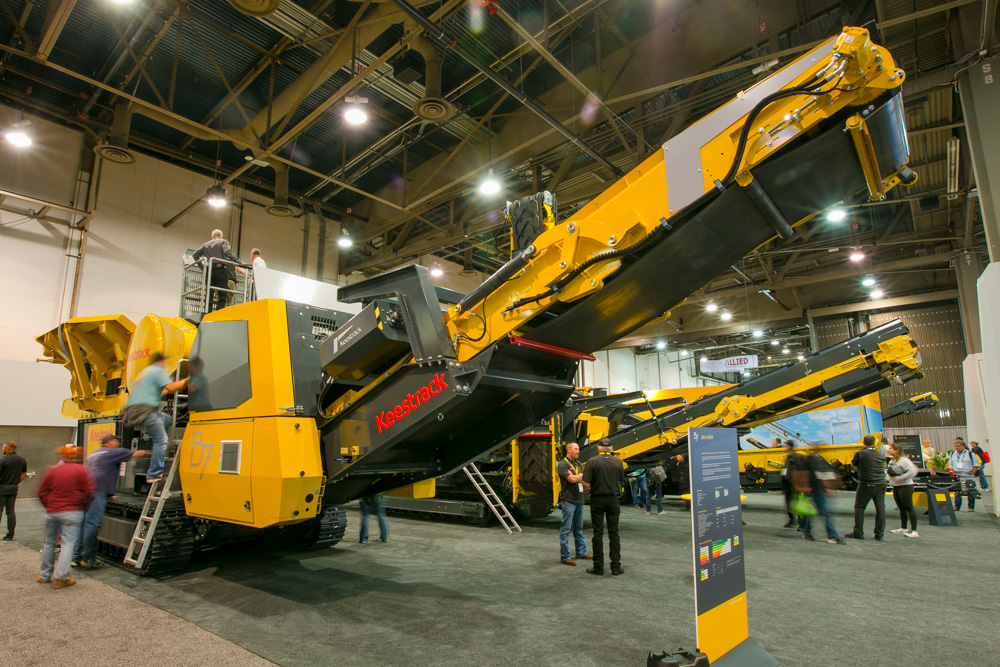
Matec plans new factory for its massive new Twin Freccia Rossa filter press
The new factory is in Mulazzo, in the Italian region of Massa-Carrara, North Tuscany. It will be the sole production facility for the 50-metre long, 600 tonnes per hour Twin Freccia Rossa.
The filter press is designed to combine the efficiency of two machines into a single product, offering faster sludge feeding and cake discharge time.
Matec Industries marketing manager Tatiana Bini said the company is taking on 60-70 new employees to work at the new factory in its offices and workshop.
"We are opening the new factory as we have had a lot of new orders and need to increase production," she added.
Italy-based Matec will now have three manufacturing bases. In addition to the new factory, Matec recently acquired the Alfa Pompe factory in Verona and has a manufacturing facility for small and medium machines at its headquarters in the town of Massa which is also in the Massa-Carrara province.
The Twin Freccia Rossa was first unveiled at the bauma trade show in Munich, Germany in 2022.
Booth C22929
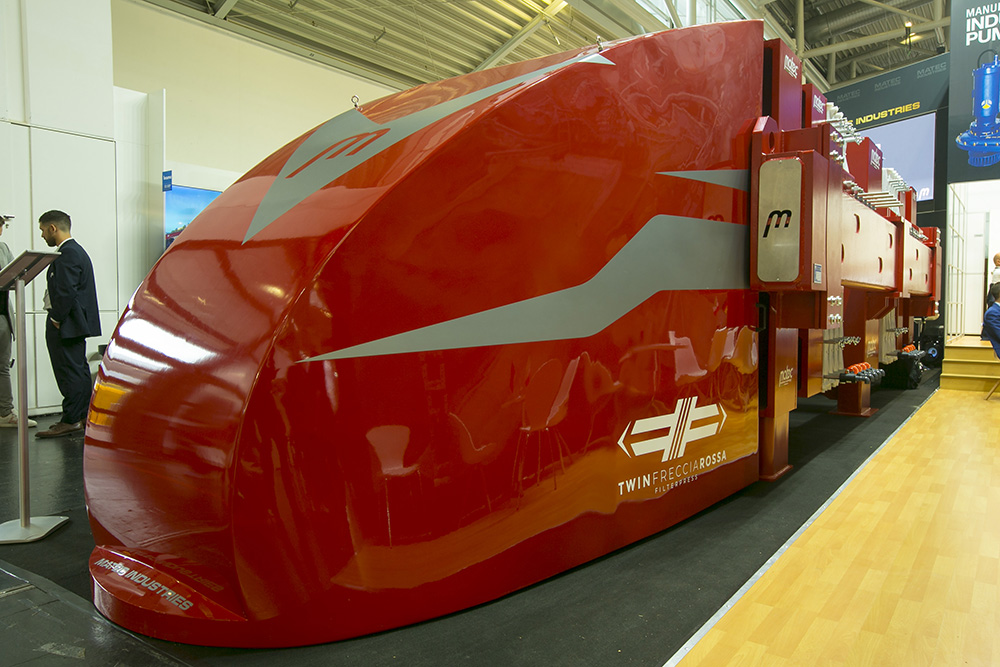