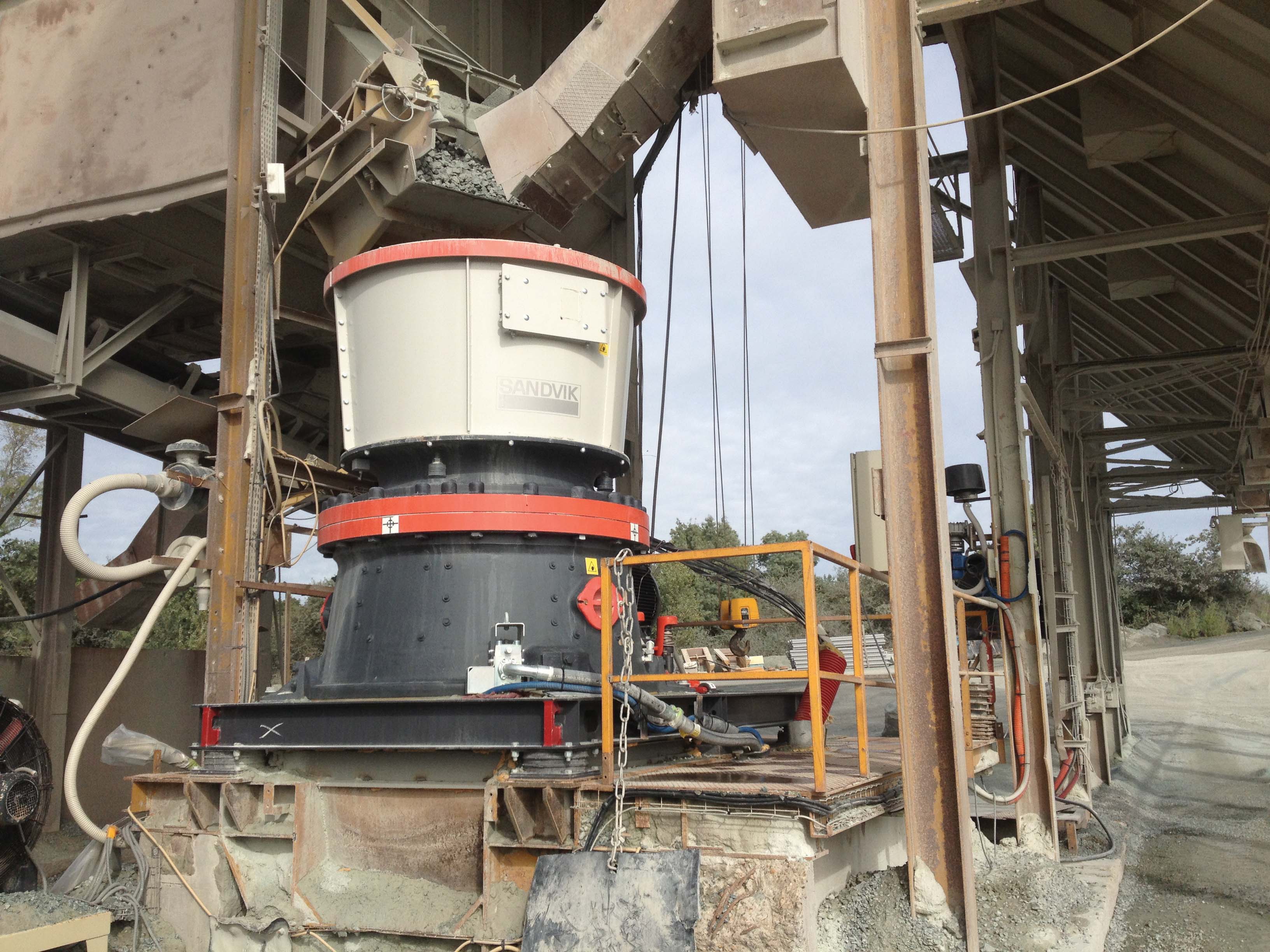
A new CH550 cone crusher from Sandvik Construction is helping the NIVET TPPL quarry produce a 0-10mm aggregate for use in road construction and civil engineering projects.
Part of the famous NIVET Group of quarrying and construction companies located in the west of France, the TPPL quarry is now able to provide customers with the aggregates they require, and deliver the material when it is needed. Furthermore the quarry has also reported direct operational benefits from the what are said to be the special attributes of the CH550.
The TPPL quarry in Beaulieu-sur-Layon has developed a reputation for providing high quality aggregate which is ideally suited for use in road construction, as well as general civil engineering work. However the contractors who use the material require a 0-10 mm product and NIVET TPPL thus required a crusher that would be able to consistently produce material to this specification.
The difficulties are due to the hard nature of the rock found at the quarry: spilite, a magmatic rock with the same geological structure as basalt and one of the hardest found in France.
The quarry’s solution was the new CH550 from
The new crusher was developed in response to customer demands, building on the foundation of the Hydrocone concept. It was developed to deliver exceptional rates of productivity and efficiency, as the CH550 crusher has the ability to be configured for either secondary or tertiary crusher applications.
It also has a wide performance range, and with its patented design, the CH550 provides NIVET TPPL with adaptability and flexibility as a tertiary crusher used for the production of the high quality aggregates.
In order to minimise negative environmental impact, and to produce safer working conditions, the CH550 also comes with no plastic backing, and is electrically powered.
Whether electrically or diesel powered, the motor on the CH550 provides a high energy efficiency classification, resulting in less power consumption, says Sandvik Construction.
“This means that non-electrically powered CH550s minimise CO2 emissions, and when compared to earlier models the features found on the crusher enable it to reduce emissions by approximately 30tonnes each year. This is equivalent to the annual emissions of six people, and as well as savings on operating power, total power consumption is reduced during the crushers working lifetime. Furthermore, quieter operation of the CH550 has enabled the NIVET TPPL quarry to benefit from reduced noise emissions thereby providing additional benefits to the workforce and the locality,” says the company.
In addition to improving its environmental standards efficiency, and enhancing operational flexibility, most importantly of all, the use of the Sandvik CH550 has enabled the 100-person NIVET TPPL operation to now be able to produce the 0-10mm product its customers require.
This is essential to the NIVET Group as a whole as the company has become an increasingly influential player in the west of France, with the group now employing over 700 people in a variety of sites throughout the region. Thus it was vital to the group’s reputation and business position that customer requirements were satisfied, with the products being produced as accurately and efficiently as possible.
The CH550 is able to be set to produce a -10mm product (which is then screened to produce a variety of sizes depending on the specific customer application) and then effectively be left to crush all day. This means that the production process is uninterrupted, thereby lowering the cost per tonne of material produced, and enabling the workforce to concentrate on its main tasks without having to worry about the cone crusher.