Epiroc toasts record quarterly revenues & profit
Epiroc, the Swedish global market manufacturer of drill rigs and hydraulic breakers for the quarrying and mining industries, is celebrating record quarterly revenues and profit.
Q3 orders received, excluding Russia, increased to SEK 13,324mn (SEK 11,493mn), an organic increase of 5%. Revenues increased 28% to SEK 12,802mn (SEK 9 966mn), an increase of 12% organically. Meanwhile, adjusted quarterly profit increased 31% to SEK 3,064mn (SEK 2,331mn).
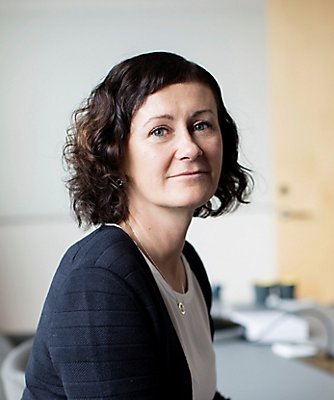
Lintec & Linnhoff Concrete CEO reflects on a legendary career in the concrete plant business
R. Sakthi, CEO of Lintec & Linnhoff Concrete, knows more than most about the concrete industry, having dedicated decades of his career to it. He says spotting the potential for high-quality manufacturing in Asia and harnessing the benefits of automation have helped establish the Eurotec brand in the global market.
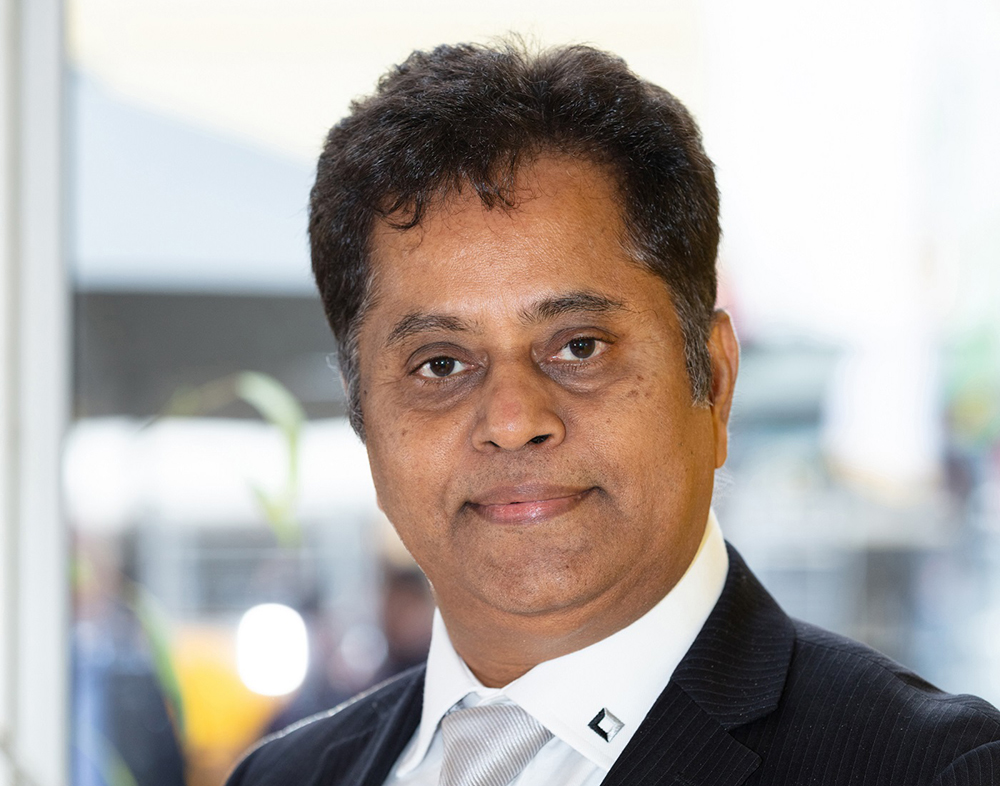
Hoffmann agrees carbon-free cement contract with O.T.E.
Hoffmann Green Cement Technologies, which designs and distributes clinker-free cement, has signed a three-year commercial partnership with O.T.E, a player in the digital, civil and industrial engineering sectors, for the supply of clinker-free and low energy cement H-EVA SOL.
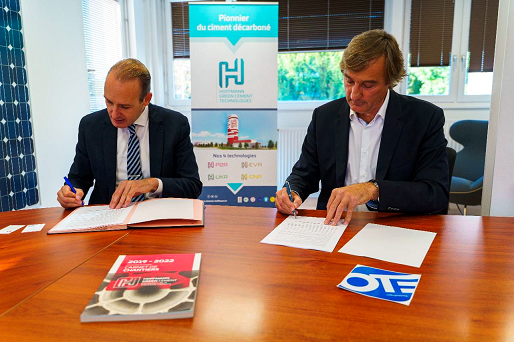
McCloskey launches new 'powerhouse' J4 jaw crusher
The crushers are particularly suited to aggregates, construction and demolition recycling, and site preparation.
The crushing and screening equipment manufacturer says the J4 builds on the robust features of its existing product range, with a line-up of features aimed at boosting productivity and offering enhanced durability across applications.
Designed to withstand the toughest conditions, the J4 delivers high production due to its jaw chamber design and enhanced material flow, the company says. The large 1060mm x 700mm jaw opening accommodates large feed sizes, contributing to higher production in material processing.
The material path is improved with the 1064mm x 4247mm grizzly pan feeder under the hopper that allows for better sizing of material with a variety of mesh options. Options of either a short pan feeder to suit the pre-screen or a double-deck grizzly pre-screen are available, ensuring suitability and better sizing of material based on the application.
McCloskey says the J4 delivers effective stockpiling, with wide main and side conveyors for enhanced material flow. The angle-adjustable 1200mm-wide ToughFlex main conveyor features a 3.912m-high stockpile and, with quick release and ground level access, the belt is designed to be easy to maintain and service.
ToughFlex is constructed with a special weave of two fabric plies and an additional binder warp (without the need for steel wire) resulting in reduced belt weight. The plies are reinforced to resist puncturing and are protected with heavy-duty, wear-resistant top and bottom covers.
McCloskey says that portability has not been compromised with the J4, despite its powerful capabilities. Mobility on-site and between sites continues to be a feature, with remote control tracks to move and position the crusher and maximise efficiency.
The company adds that technology has been a key factor in the development of the J4, with a DSE control panel for the highest operational performance and reliability providing push-button control of the jaw, track and feeder functions. The crusher is fitted with a telematics modem for the new 365SiteConnex programme, a connectivity solution for accurate monitoring of McCloskey products.
365SiteConnex is based on the latest communication technologies to collect, analyse and deliver information on the crushers, screeners and stackers.
“The J4 continues the momentum for our jaw-crushing product range, as we continue to develop new products that meet the evolving needs of our customers across industries,” said Toni Laaksonen, senior vice president, McCloskey International.
“As a company that is involved in the handling and processing of the Earth’s resources, we also have our sights set on sustainability. Our next commitment to an environmentally responsible strategy will be the introduction of our electric crushers, scheduled to be available in 2023.”
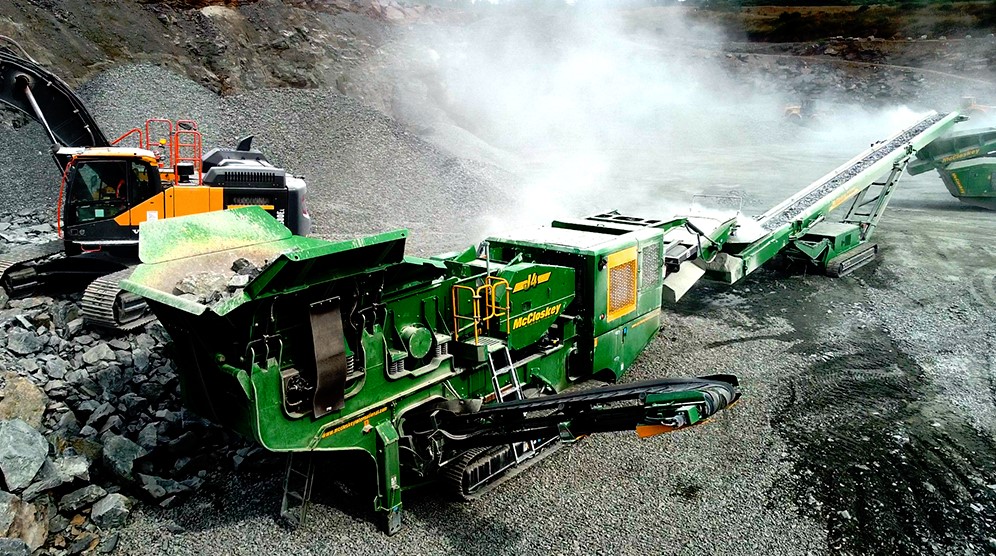
Hannes Norrgren takes over as new Volvo Penta president
He will take up the former position from 1 November, replacing Giorgio Paris who will retire after a 25-year career at the company.
Norrgren has worked within the industry for more than 20 years. He has a long track record at Volvo Penta, having previously held various positions including vice president for industrial sales and marketing in Europe. For the past three years, he has served as CEO at Humphree, a fast-growing Swedish marine technology provider of which Volvo Penta is the major shareholder.
“I am delighted that Hannes is returning to the Volvo Penta team,” said Heléne Mellquist, president of Volvo Penta. “He brings extensive knowledge about building business relationships with customers which, in combination with a strong commercial focus and mindset, will be key in leading the Industrial Business Unit on our transformation journey.”
Norrgren commented: “To be able to lead one of the industry’s top brands in times of disruptive change is an exciting challenge. What we will do over the coming years in relation to our transformation towards sustainable power solutions will define the next era of Volvo Penta Industrial.
“It will take courage, teamwork and entrepreneurship to succeed, all of which are values that are close to my heart and management approach.”
Mellquist added: “I would like to thank Giorgio for his engagement and commitment to our company. He will be truly missed, but we wish him a happy and relaxing future with family and friends.”
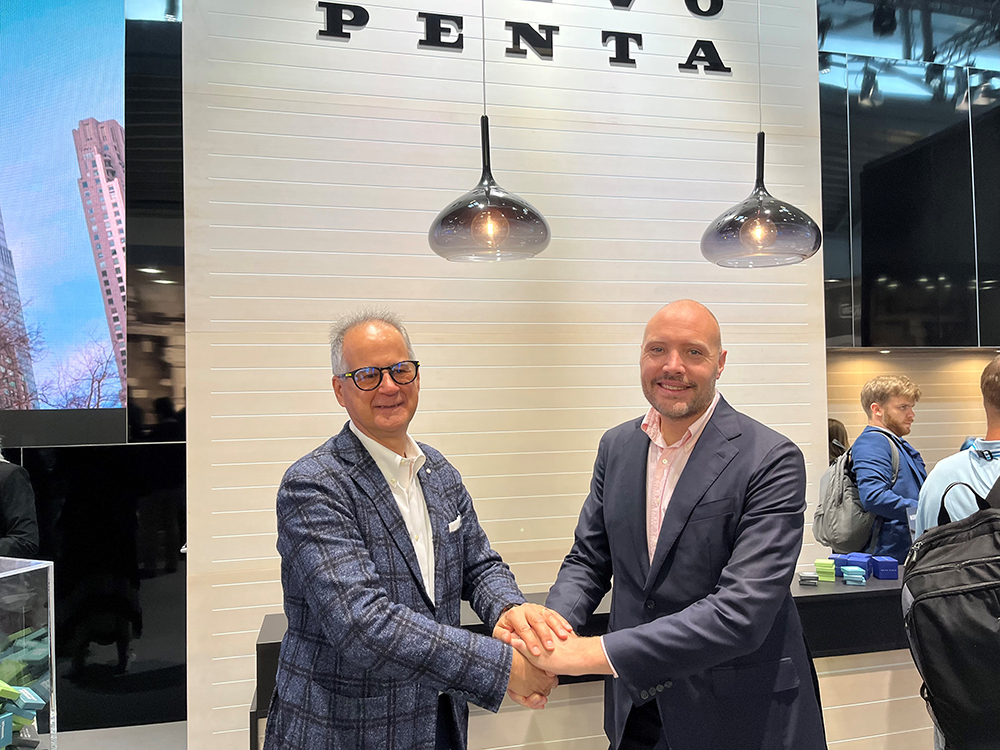
CIFA launches new K42E electric concrete pump
The K42E is equipped with a 30amp hour cell battery pack that powers two Rexroth electric motors. The first drives the hydraulic pump to move the boom and open the outriggers, while the second drives the pumping unit, in a closed circuit and at maximum capacity of 160m³/hour at 80bar.
The charging process is quick and easy, says the company, with the integrated battery charger compatible with the 220V system. The boom extends up to 42m and consists of five sections, with the last two made from carbon fibre.
“If the job requires higher performance than the batteries can provide, the new Energya pump can be connected directly to an electrical outlet on site,” explains Davide Cipolla, CIFA’s CEO. “The system will then cut out the batteries and power the electric motors directly from the power source. A 40m power cable is included.”
This, he adds, means that the pump continues to operate with the truck’s diesel engine switched off, thus eliminating emissions and noise. If there is no electrical supply on site, an emergency system allows end-users to connect the K42E to the truck’s power take-offs and use the engine to complete the work, then close the boom and outriggers.
“The aim is to eliminate CO2 and noise emissions throughout the supply chain, from transport to laying of the concrete, by expanding the possibilities of using high-performance vehicles in areas where noise pollution and CO2 emissions are prohibited,” adds Cipolla. “The special feature of the Energya K42E pump is that the battery allows it to always operate in full electric mode.”
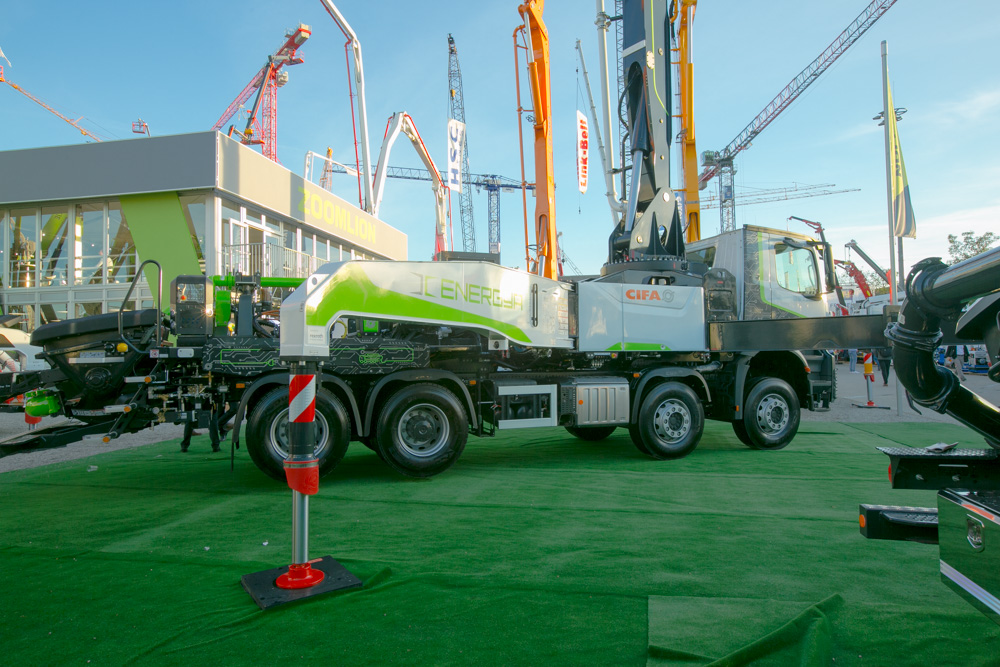
Orica successfully trials WebGen 200 tech at Blair Athol
Building on the success of over 4,000 WebGen 100 blasts worldwide, Orica’s WebGen 200 technology continues its successful entry into the high-volume surface mining market.
WebGen technology provides for groups of in-hole primers to be wirelessly initiated by a firing command that communicates through hundreds of metres of rock, water, and air. This completely removes constraints often imposed by the requirement of a physical connection to each primer in a blast and, importantly, allows us to remove people from harm’s way.
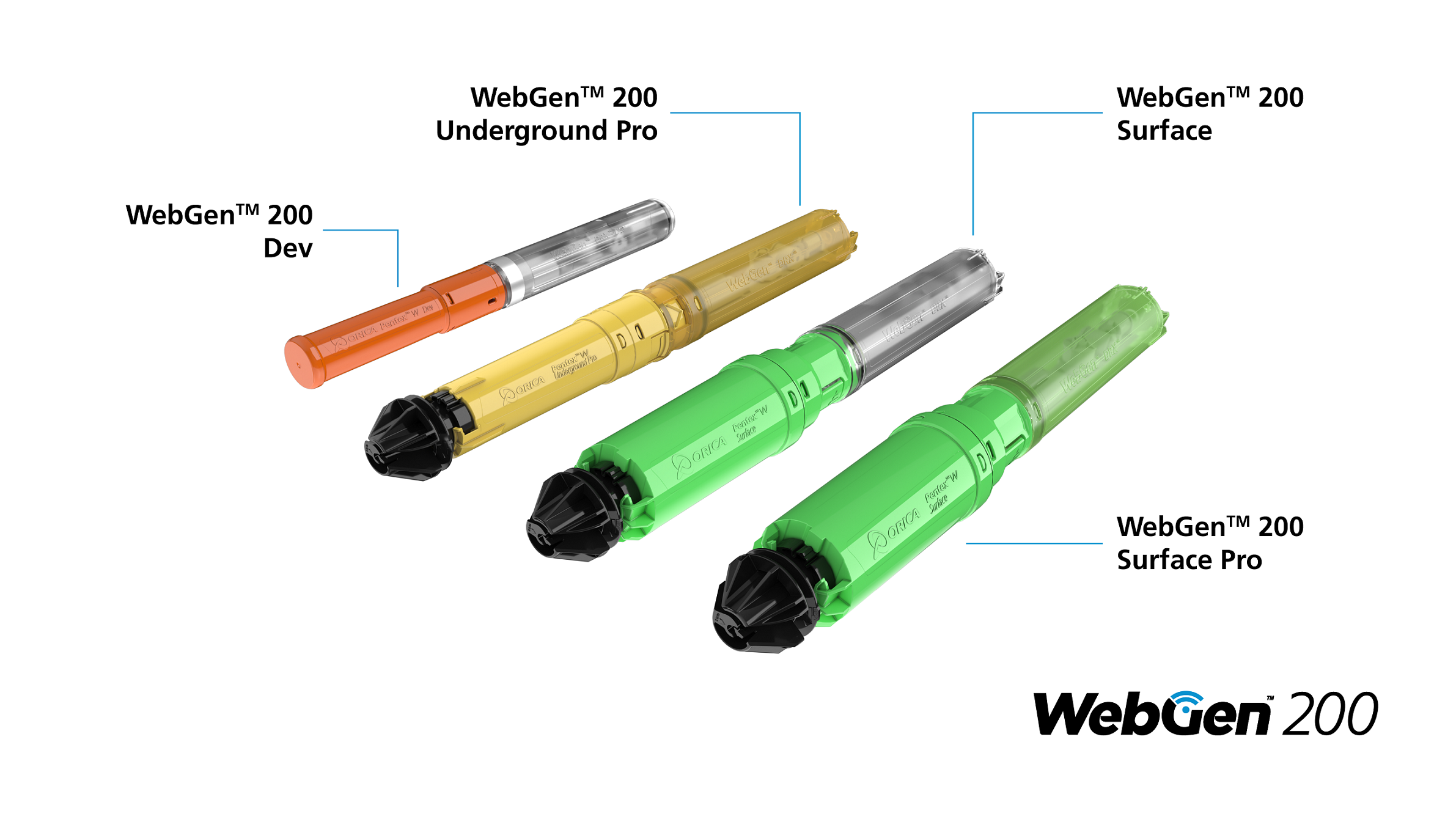
Tarmac supervisor leads the way with prestigious award nomination
Tarmac's rising star Shahid Zaman has been shortlisted in the top 10 Future Leaders category at the prestigious 2022 Ethnicity Awards.
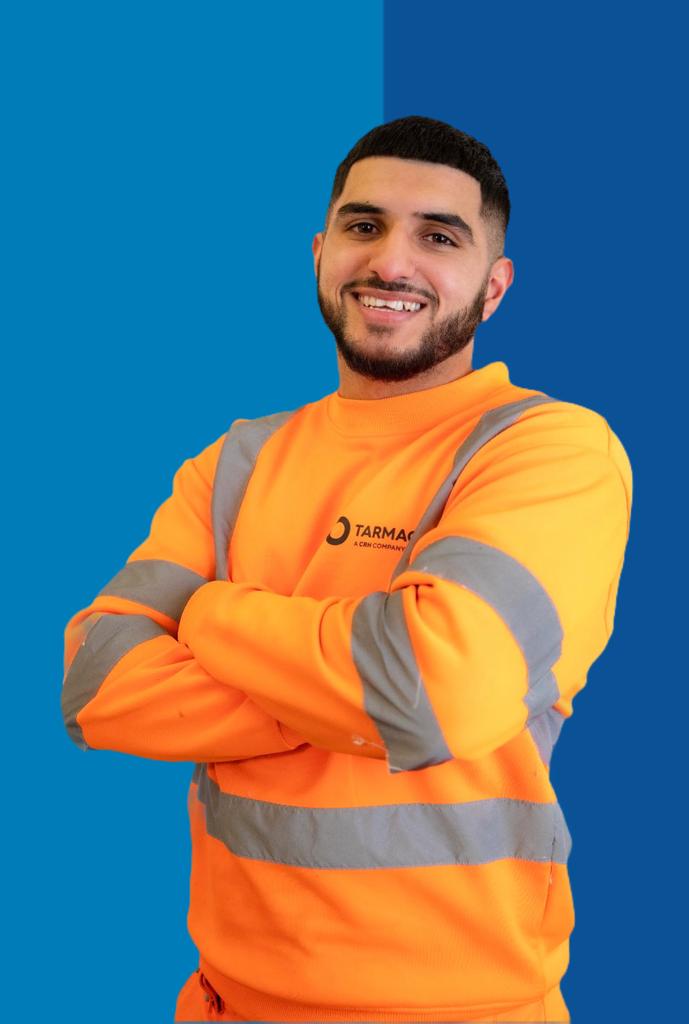
Electrifying! Komatsu’s Proterra-powered PC210E excavator
Since January 2021, Komatsu and US-based Proterra have been jointly developing electric medium-sized hydraulic excavators and have been conducting Proof of Concept tests on advanced research machines at customers' construction sites.
The PC210E is scheduled to be introduced to the Japanese and European markets in financial year 2023.
Komatsu notes that hydraulic excavators are the most versatile type of construction equipment, and the mid-size class is used in a wide range of jobsites and applications, mainly in earth excavation and loading operations, requiring power and durability to withstand heavy-load work.
The PC210E model is said by the manufacturer to optimise the entire body control system by capitalising on Komatsu’s proprietary coordinating technology.
It specifically integrates Proterra’s lithium-ion battery technology, which has a proven track record for use in heavy-duty and commercial vehicles deployed in various fields globally, combined with Komatsu’s components such as the hydraulic pump, controller, and electric motor for work equipment operation.
Komatsu has also developed a robust cage structure to provide additional protection onboard the vehicle for its battery packs.
As a result, the company has achieved digging performance and durability equivalent to those of engine-driven hydraulic excavators. In addition, the high energy levels in the excavator’s Proterra battery system enables operation for up to a claimed eight hours when fully charged.
The excavator’s electric power makes it possible to work comfortably in various work environments without worrying about noise and exhaust emissions and is expected to be used for work in urban areas and night-time construction work. The zero-engine vibration also helps reduce operator fatigue.
As global awareness of climate change accelerates, Komatsu has declared it plans to achieve carbon neutrality by 2050. In collaboration with its partners, the company is developing electric construction equipment to achieve zero exhaust gas emissions and a significant reduction in noise, with the vision of developing safe, highly productive, smart and clean workplaces of the future.
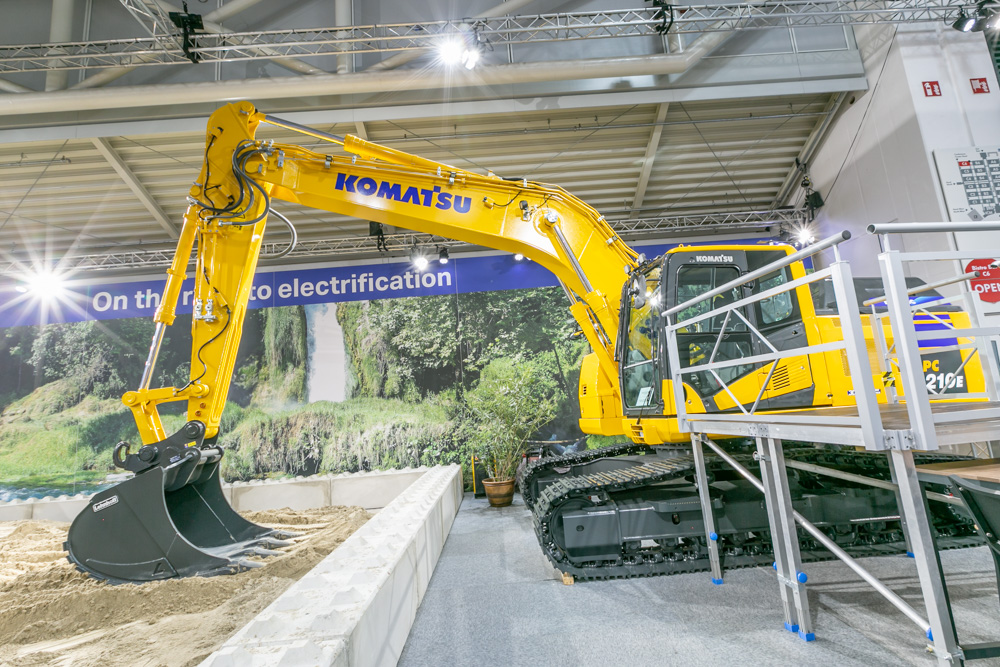
Kleemann’s electric-drive MOBIREX MR 130(i) PRO impact crusher
Local emission-free operation is said to be possible thanks to the model’s E-DRIVE diesel-electric drive with the option of external power supply.
Thanks to this external supply, the system can be operated without emissions. This ensures low energy consumption per tonne of end product. The electric drive also means that hydraulic oil is only required for setting and set-up functions. This minimises risk to the environment and further increases the system’s sustainability.
When the Mobirex MR 130(i) PRO is operated via the diesel unit, the performance and load-dependent fan is said to ensure efficient use of fuel and low noise emissions. The formation of dust is also said by Kleemann to be greatly reduced by water spraying at all relevant points, such as the crusher inlet, the discharge belts and the post-screening unit, as well as various belt covers.
The Kleemann PRO-Line system can process up to 600 t/h of material. The high output is made possible by the crushing unit with a heavy rotor and a 250kW drive in conjunction with efficient pre-screening. The Continuous Feed Systems’ (CFS) continuous feed control is said by Kleemann to ensure consistently high utilisation.
The company says it counters the increasing complexity of crushing plants with its intuitive operating concept Spective.
In addition to a large touch panel and two Spective radio remote controls - one of them for operating all relevant functions of the automatic mode from the comfort of the excavator - Kleemann also offers Spective Connect.
The digital solution simplifies the construction site digitisation of the Mobirex MR 130(i) PRO. Spective Connect transmits all important system data to the user's smartphone and simplifies reporting.
With the Mobirex MR 130(i) PRO, the proven, robust crushing unit with its two impact rockers and versatile blow bar options, as well as the 8.4m² optional double-decker post-screen, are said to ensure very good product quality.
Kleemann’s new impact crusher can produce and discharge two classified end sizes – without using an additional screening plan. The use of optional wind sifters is said by the German company to further increase end product quality.
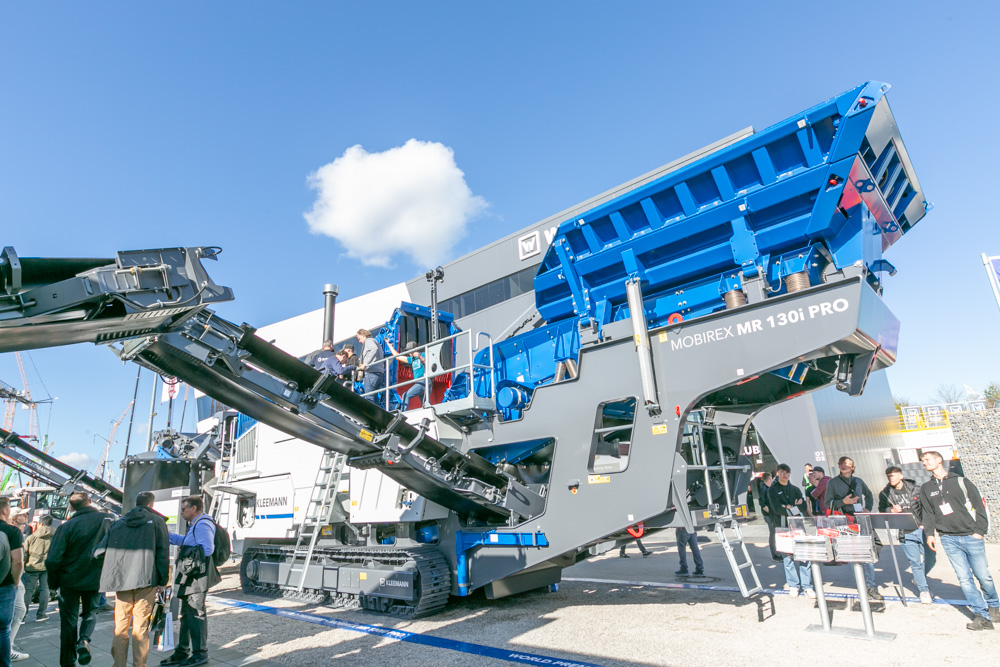
Bobcat expands electric range with launch of E19e mini excavator at bauma 2022
The 2-tonne battery-electric machine features the same profile, external dimensions and offers comparable performance as the popular diesel powered E19 mini excavator, more than 10,000 units of which have been sold globally.
According to Miroslav Konas, mini excavator product manager at Doosan Bobcat EMEA, with a width of just 98cm, the new E19e model is ideally suited for indoor applications where space is at a premium.
“The E19e is a perfect fit for applications such as indoor and outdoor demolition, landscaping and infrastructure activities,” he says, “as well as other tasks that necessitate night-time work or low noise levels. The machine, therefore, fits the bill for rental companies and contractors alike.”
Featuring a 3.5-hour battery capacity, the E19e comes with a super-fast charger, which allows for opportunity charging during work breaks, thus maximising uptime on site.
Doosan Bobcat CEO Scott Park says the launch of the E19e confirms Bobcat’s commitment to helping the industry meet its environmental, social and governance (ESG) targets: “The move toward a more sustainable construction industry is well underway with a clear roadmap ahead to deliver zero-emission equipment fit for the future.
“Battery-electric products form a major part of this ambition, and we remain at the forefront of the global rollout.”
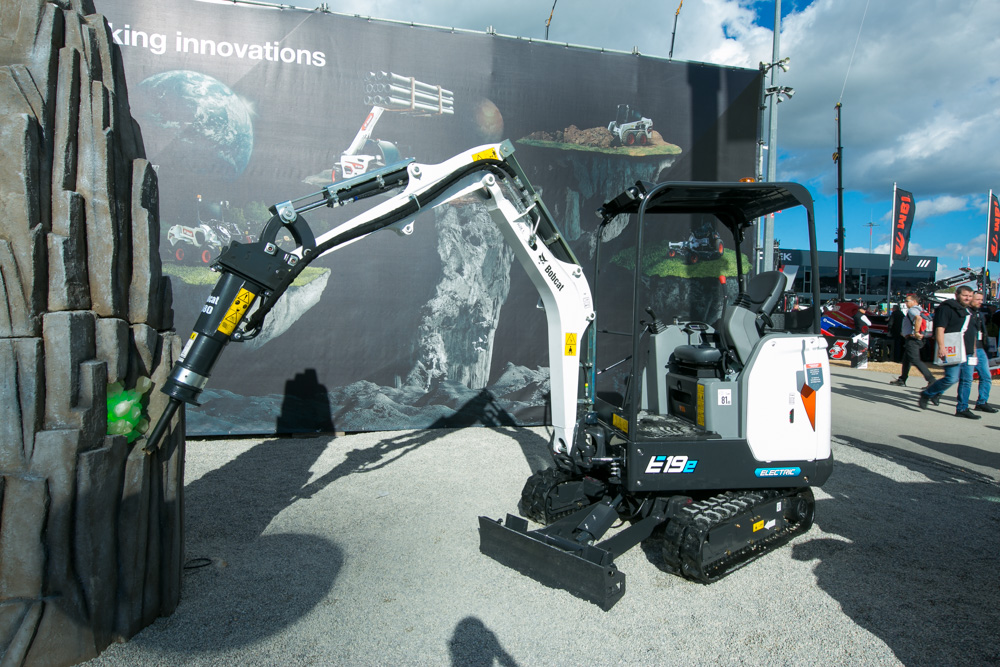
Epiroc demonstrates its first-ever tophammer battery-electric drill rig, the SmartROC T35 E
Based on Epiroc’s well-proven SmartROC T35 surface drill rig and drawing on the company’s experience in developing underground battery rigs, the SmartROC T35 E comes with a range of smart features, and is said to deliver high safety, reliability, and performance – in a quieter working environment.
"The fact that we are removing emissions from the drilling process is an important step towards a better environment,” says Hakan Aytekin, vice president marketing, Epiroc Surface division.
“This accomplishment shows that Epiroc has an important role to play in making our industry more sustainable.”
The SmartROC T35 E rig is equipped with both a battery and an electric cable, which improves flexibility considerably. Personnel can choose to drill with the most suitable alternative for the location. It also allows for quick and smooth transportation within and between sites.
The surface drill rig is fitted with the same type of well-proven batteries and sub-components as in the Epiroc underground battery solutions. This streamlines spare parts handling and service for customers with several different operations.
"SmartROC T35 E is a result of a successful collaboration between Epiroc and our customers,” says Ulf Gyllander, global product manager, Epiroc Surface division. “They have provided us with valuable input, making sure we will deliver a rig with optimised performance and flexibility.”
Epiroc’s battery-electric solutions are said by the company to be attracting strong interest from the market. The machines play a vital role in the firm’s ambitious sustainability goals for 2030, which include halving the CO₂ emissions in operations and from sold products.
In 2021, the goals were validated by the Science Backed Targets initiative as being in line with keeping global warming at a maximum 1.5°C, consistent with the goal of the Paris Climate Agreement.
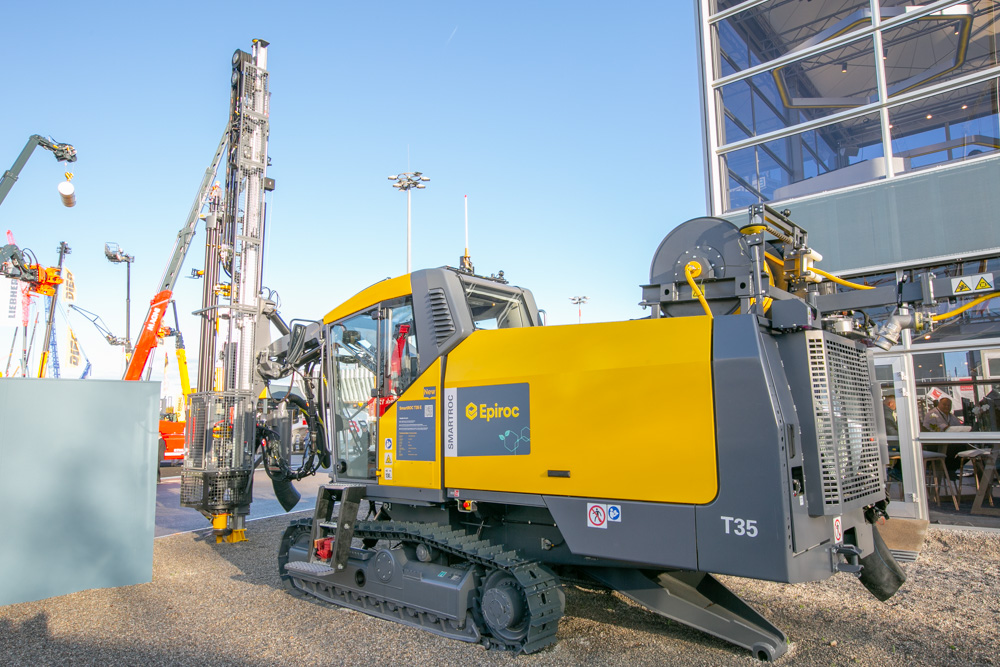
Powerscreen crushing it at bauma!
The Dungannon, Northern Ireland-based Terex brand, a major global supplier of mobile crushing, screening and conveying equipment to the quarrying, mining, construction and recycling sectors, has a strong relationship with German strategic partners, Kölsch and Christophel.
The Premiertrak 330 boasts a two-piece grizzly feeder which allows better material flow towards the chamber. User benefits include track mobility for a quick set-up time, and variable crusher speed that allows the operator to fine-tune the machine and maximise output.
The Powerscreen Chieftain 1700X is a mid-sized tracked mobile screen aimed at end-users requiring high volumes of finished products in applications including topsoil, coal, crushed stone, recycling, iron ore, sand and gravel.
User benefits include a quick set-up time, drop-down tail conveyor and the patented four-bearing screenbox with the ability to switch to a two-bearing setup in less than three hours, making the Chieftain 1700X one of the most versatile units of its size on the market, according to the company.
Commenting on Powerscreen’s relationship with distributors Kölsch and Christophel, Joe Cassidy, Powerscreen International sales director, said, “Both companies have been representing the Powerscreen brand for many years and offer an extremely professional service to end-users of our equipment across the country. We are strongly committed to the German market and look forward to continued success and growth in the region.”
Jürgen Kölsch is a family-run business with more than 20 years industry experience. It offers tailormade solutions in new machines, rental and used equipment to meet the needs of its customers. The company prides itself on aftermarket support and has an extensive service and parts offering that spans southern Germany.
For almost four decades, C. Christophel has been another family-owned business that German customers have relied on. As one of the largest dealers in the industry, the Lübeck company offers mobile equipment solutions for mining and recycling applications.
It counts on innovative solutions to achieve optimum results - whether at the quarry face or in the sand and gravel pit. At the same time, considering the shortage and protection of raw materials, recycling of minerals and organics is of great importance to its business.
"We rely on comprehensive and honest advice to enable our customers leading their projects to success,” company CEO Rüdiger Christophel said. “Our experience has shown that honesty and quality is key to getting the best results.”
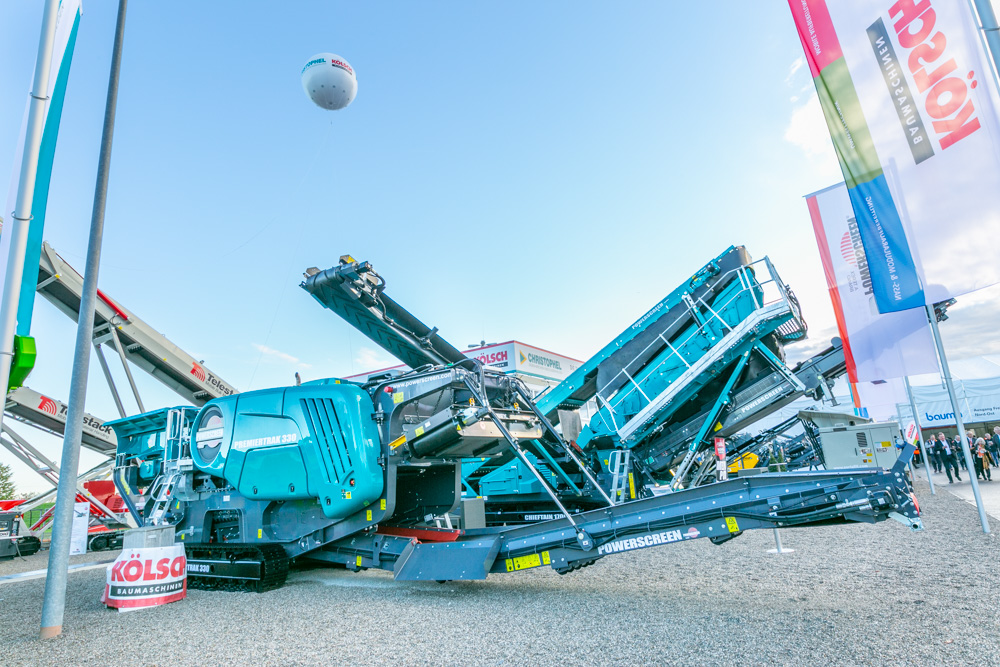
Magni moves the cab on RTH series to give better visibility
By moving the cab forwards, the operator has better vision when traveling on roads, as well as around construction sites. This also helps when positioning the vehicle’s stabilisers, especially in rough terrain.
Inside the cab, along with the latest Combi Touch Screen incorporating the Magni LLD – Load Live Diagram – the operator now has better knowledge of where the load is positioned.
There is also more glass in the cab to make visibility a key feature of the RTH series. And entry to the cab is easier thanks to a new positioning of the steps.
The new RTH series, including the 6.26, are used for many applications being able to take various accessories such as forks, winches and platforms and being equipped with 360° rotation.
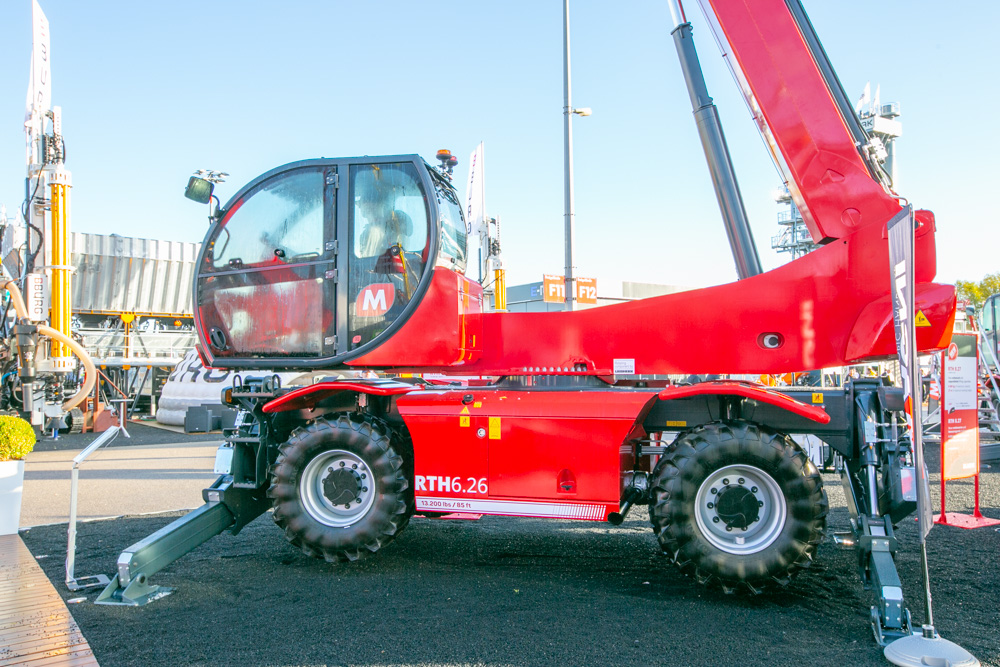
CDE focus on multiple benefits of premium waste recycling technology
The Northern Ireland-headquartered global provider of sand and aggregate wet processing solutions for the natural processing and waste recycling sectors, is highlighting the role of its technology in supporting the circular economy and zero-waste agenda.
As the construction sector continues to adjust to the restricted availability and high cost of raw materials, CDE is demonstrating the potential benefits of processing construction, demolition and excavation (CD&E) waste.
On 26 and 27 October, senior CDE figures are being joined by several of the company’s European customers for a series of round-table discussions on the future of recycling. Before that, as part of the bauma exhibitor forum on 24 October, Eunan Kelly, CDE's head of business development for North West Europe, delivered a lecture on Creating valuable in-spec products from CD&E waste.
Speaking ahead of his lecture, Kelly said, "In the current economic and social climate, with materials costs rising, resources depleting, and regulations calling for the adoption of sustainable solutions, we should look to the technology of today to produce the sustainable construction materials of tomorrow; how CDE's waste recycling solutions…can support the industry to transform CD&E waste into certified, in-spec sand and aggregates."
Earlier this year, a package of European Green Deal proposals was presented with a view to making sustainable products the norm within the EU internal market. The revised Construction Products Regulation (CPR) emphasises the value of construction to the EU as a key employer and economic contributor.
However, it also highlights the adverse impacts the sector has on the environment, as one generating some 30% of the EU's annual waste and contributing significantly to its domestic carbon footprint and emissions.
The construction industry is a major economic driver; in the EU alone, 25 million people are employed by five million companies, according to data from the revised CPR. So, when the Covid-19 crisis gripped economies and construction output fell to some of its lowest-ever levels, it was no surprise that robust recovery plans with a clear focus on investments in infrastructure were announced by nations around the world to stimulate renewed economic growth.
However, the cost of raw materials and their availability remains a deepening challenge for the sector.
Materials shortages and their rising costs are not entirely symptoms of the pandemic, but they have been exacerbated by it and have become more acute, CDE's business development manager for the DACH region, Christoph Baier, explains.
"Every day we continue to extract our fast-depleting natural resources to support rapid urbanisation and our modern, technological lifestyles. Essential to this is sand, the second most consumed natural resource after water and the most consumed solid material on earth."
In April, the UN Environment Programme (UNEP) published 10 recommendations to avert the impending sand crisis. It noted how the use of sand, gravel, crushed stone and aggregates has tripled in the last two decades, reaching an estimated 40-50 billion tonnes per year.
"This, in the context of projected increases in global populations and urban living," Baier continues, "demonstrates how demand will only rise, while resources will only deplete, unless we adopt long-term attitudinal, regulatory and technological change to ensure not only the sustainability of companies within the construction sector – and with it the livelihoods of those employed within it – but also the sustainability of the very planet.
"It's clear the consequences of a linear take, make and waste economy are catching up to us."
While Covid-19 economic recovery packages may help to stimulate growth, they must be conditional on building back greener and more sustainably, Baier adds.
"We can set out ambitious plans to build and grow, but we must ask ourselves how sustainable this is without a new approach to how we extract and manage the lifecycle of finite natural resources."
A circular approach is the only answer, Kelly agrees.
"It can be the means to equip us with the resources needed to supply a sector charged with a key role in the economic recovery while addressing our collective environmental footprint by reducing waste-to-landfill volumes and extending the lifespan of precious natural materials. All the while continuing to supply a resource-intense sector with the materials it requires; materials often trucked out of our urban centres, where they are needed most."
He says the technology needed to extract recycled sand and aggregate resources from CD&E waste that are equivalent to their virgin quarried counterparts is already in operation throughout Europe.
"Many businesses are already on this pathway," Kelly says, "and we will welcome many of them to join our upcoming round table discussions at bauma to share insights with the industry as we work to demonstrate that we can pursue commercial opportunities in a sustainable way."
CDE supports materials processors in realising the value locked in CD&E waste. Using innovative wet processing technologies that scrub material, float off lightweights (demolition debris) and classify end products, this waste stream can be repurposed to produce washed materials free of contaminants and suitable for use in high-value construction projects.
To date, CDE solutions have supported companies around the world to divert more than 100 million tonnes from landfill.
"These are far from 'alternative' materials," Kelly explains. "Many material processors utilising CDE technology are successfully producing CE- and BSI-certified concrete products, including competitive concrete for non-structural – but still high value – construction projects, with some applications successfully achieving beyond C45 spec."
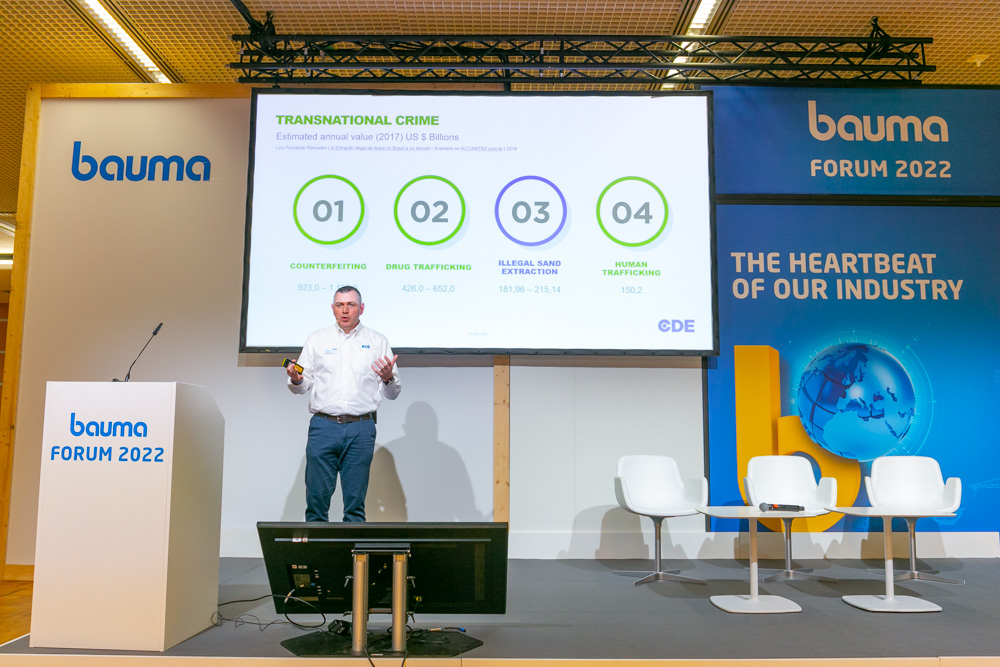
The CASE plant in Lecce celebrates 50 years in business
The CASE plant in Lecce, Italy, has celebrated 50 years in the off-highway equipment business. Celebrations began on Wednesday 28th September, with the planting of an olive tree, a symbol of the Salento region and of the company's roots in the area.
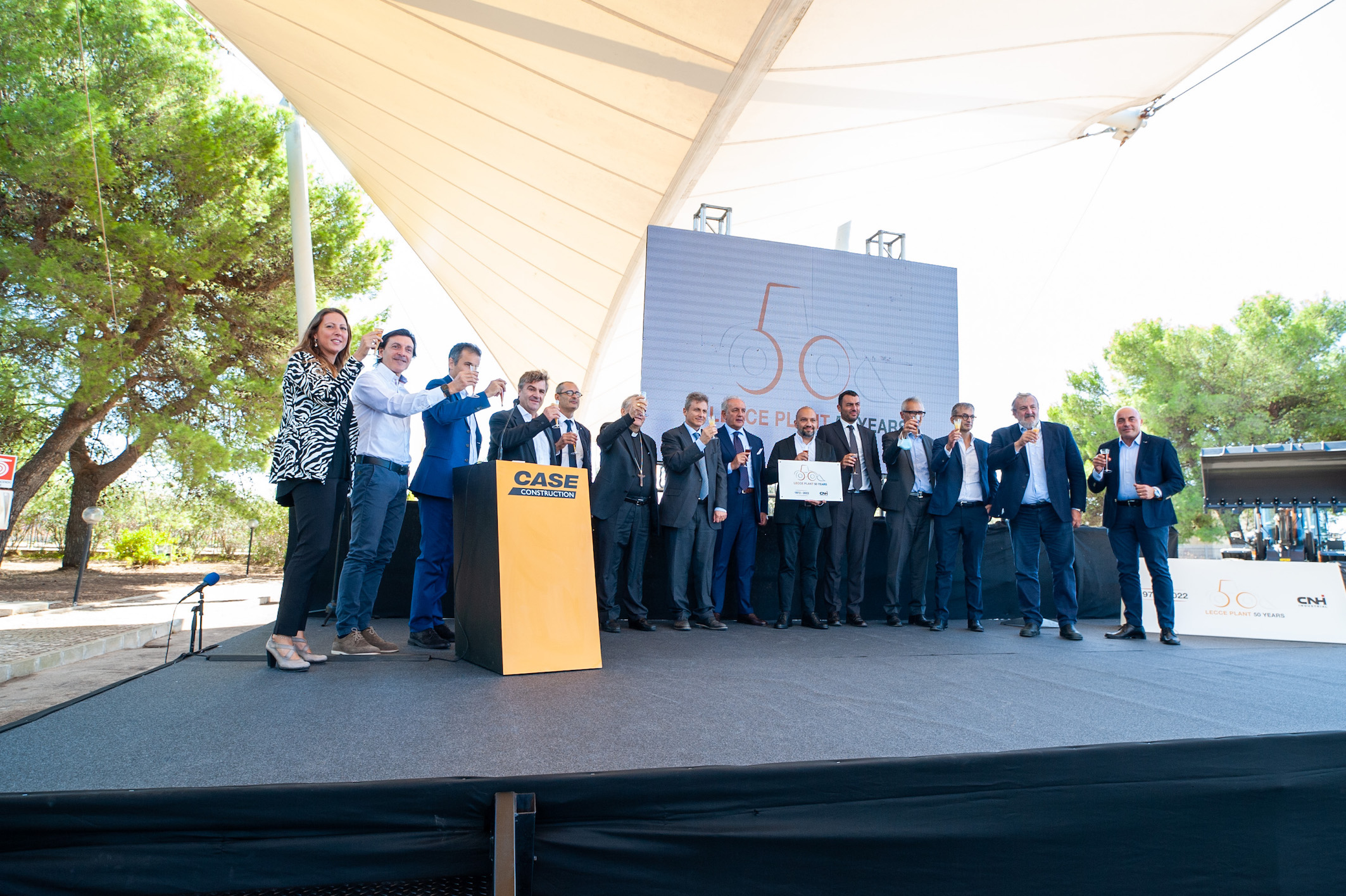
Wheeled and tracked duo prove just the job for Makapa in the Philippines
Makapa Corporation in the Philippines is operating a Sandvik UJ300 wheeled jaw crushing unit together with a tracked QA335 Doublescreen to process river gravel.
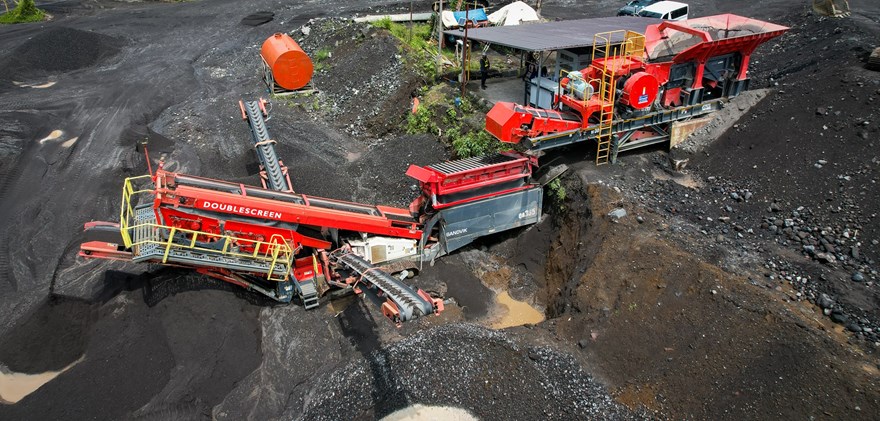
Continental unveils LD-Master L5 Traction construction tyre with integrated self-monitoring
Construction machines usually operate with heavy payloads and are exposed to a variety of harsh ground conditions, such as rock, gravel, or rubble. The LD-Master L5 Traction is specifically designed for loaders operating on abrasive surfaces and in face working jobs where high productivity and assured vehicle uptime are of most importance.
The reinforced 3* carcass is said to satisfy the highest load carrying capacity requirements, even under extensive production cycles. The L5 traction tread pattern protects the carcass and ensures smooth and safe operation on the construction site.
The solid tread block design always provides secure traction. The extra deep tread and sidewall protection are also said by Continental to make the tyre more robust and ensure long-term productivity.
To minimise idle time and ensure serviceability even under harsh conditions, the special tires fitted to construction machinery should be controlled as precisely as possible.
The LD-Master L5 Traction is fitted with an integrated tyre sensor, making monitoring possible in real time. The sensor monitors temperature and tyre pressure, said to assure the most efficient operation mode for a long tyre life.
In addition to the LD-Master L5 Traction, Continental is presenting its EM-Master E3/L3 as 65-series for construction/surface applications and a sneak preview for a new solid skid-steer tyre.
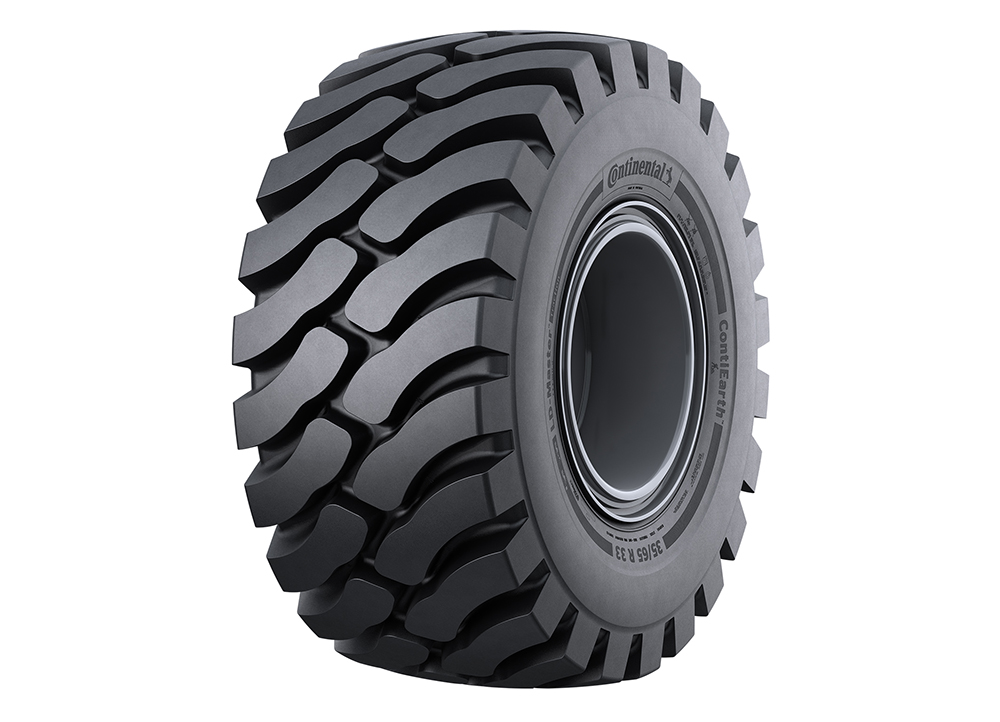