Recycled aggregates – new life to construction waste
The imperative need and the rising demand to give new life to construction waste is now more important than ever before. Legislations around the world are calling its member countries to recycle increasingly more construction and demolition waste. Re-using crushed concrete instead of natural rock and recycling metal saves both the environment and the constructor resources.
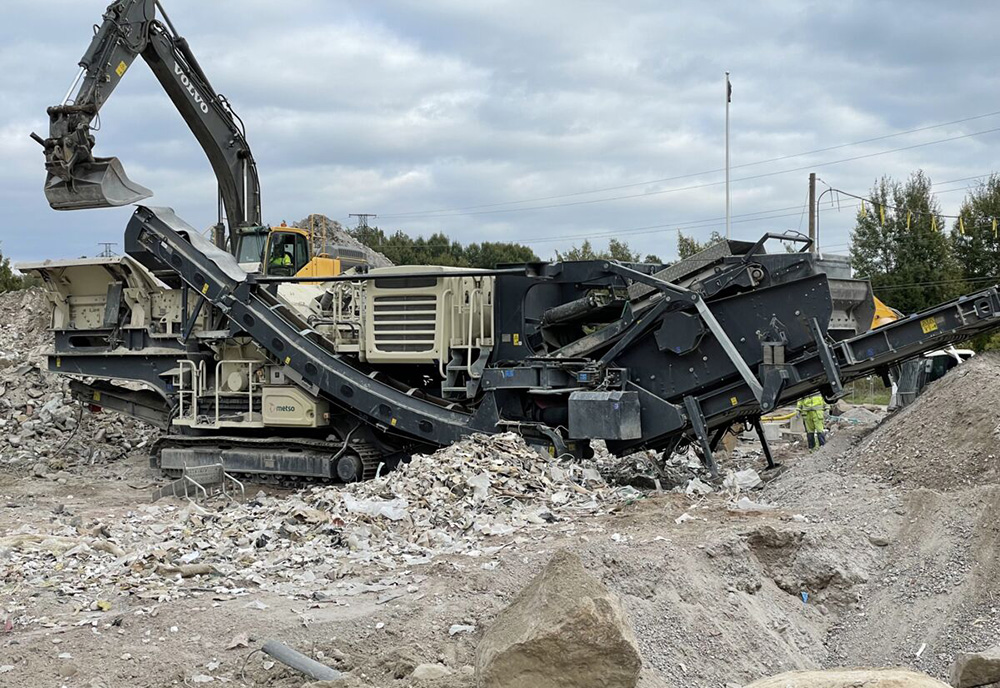
More volumes and cleaner grades in demolition and recycling business
Ahosen Palvelut trusts the new Metso Outotec’s Lokotrack® LT1213S mobile impactor crusher for crushing the waste of a demolished swimming hall in Kuopio, Finland. The machine is specially equipped for producing recycled aggregates with a wind sifter, a hydraulic magnetic separator and a belt weigh feeder. Added with a convenient remote monitoring system Ahosen Palvelut has been able to produce more volume and cleaner grades for the customers than before.
Nearly 500K visitors to vibrant bauma Munich 2022
bauma Munich, the world's biggest construction, quarrying, mining & recycling machinery exhibition, attracted more than 495,000 visitors from over 200 countries and around 3,200 exhibitors from 60 countries during the latest staging of the tri-annual event (24-30 October 2022).
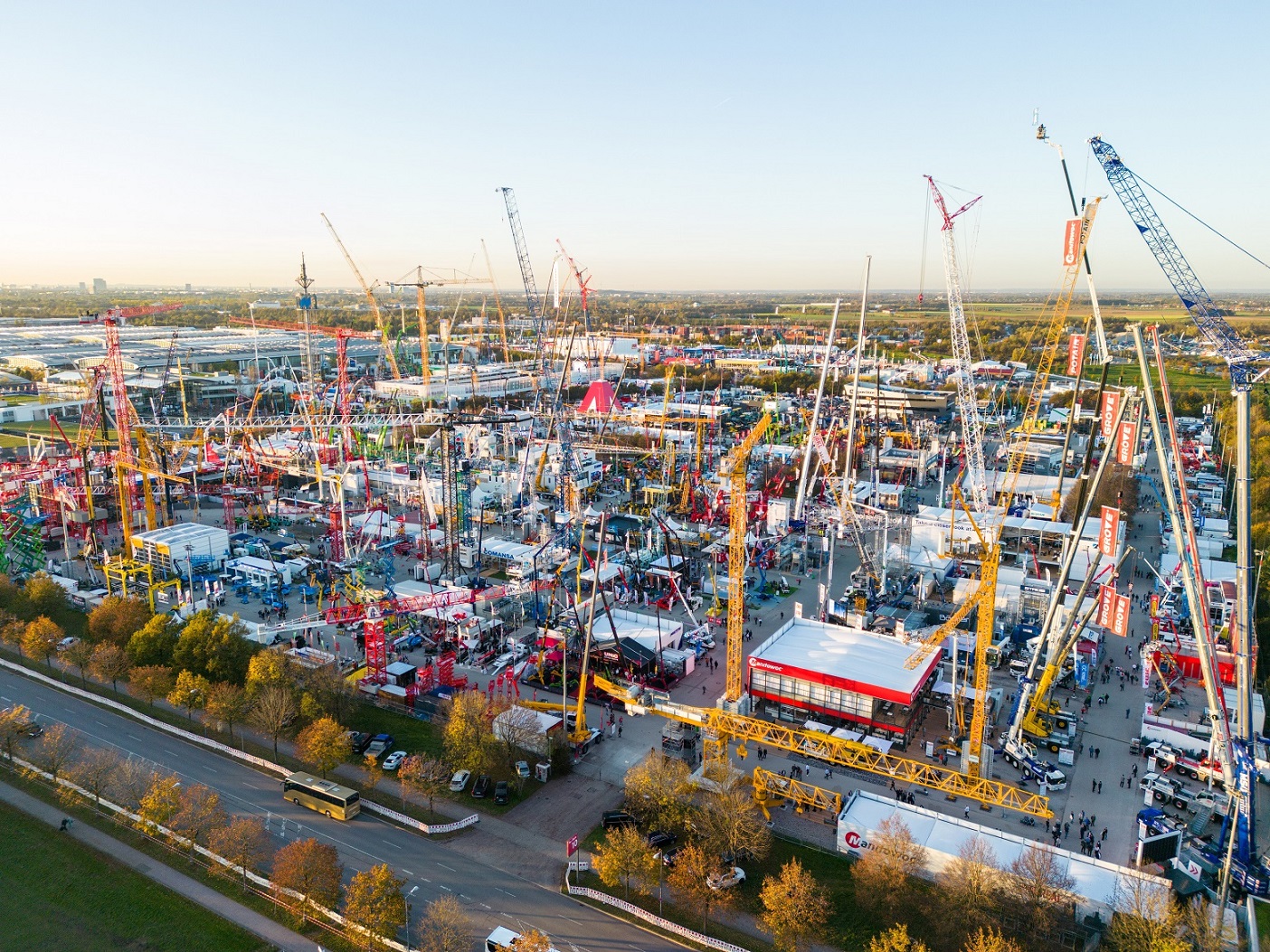
CEMEX reports 13% top-line growth driven by strong pricing
CEMEX has continued its solid top-line growth, with third-quarter net sales growing 13% to US$3.956bn.
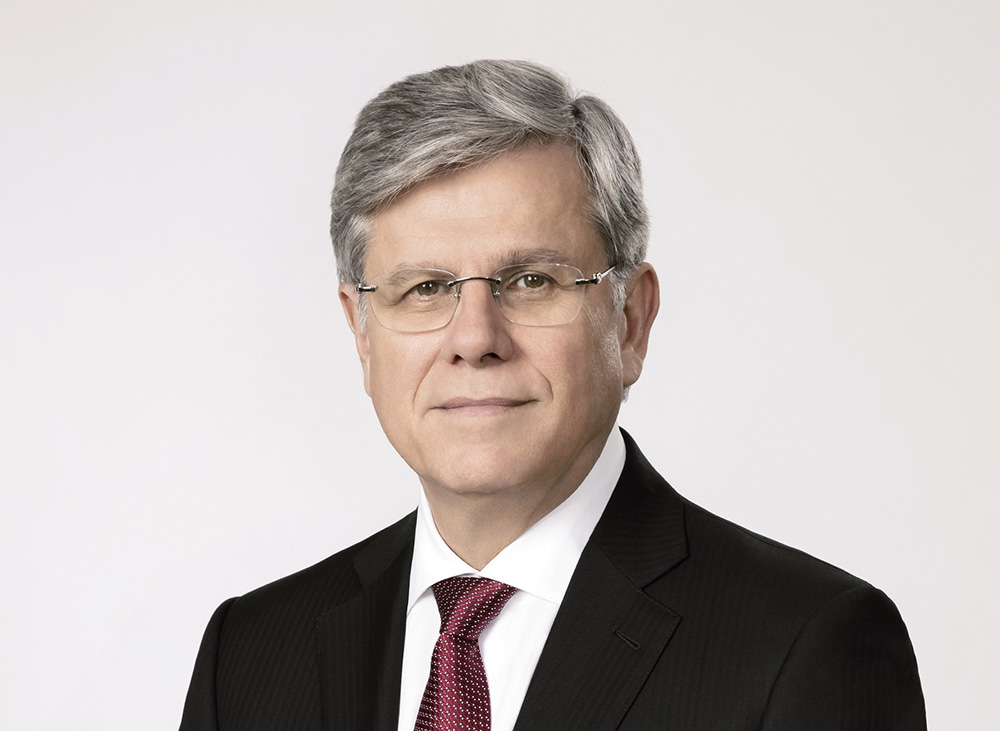
'Minerals Matter' aims to futureproof the quarrying & mineral products industry
A consortium of respected quarrying and mineral products industry organisations and employers has taken a key role in leading a major project to raise the sector's profile and inspire young people and adults to become the next generation of quarrying and mineral products professionals.
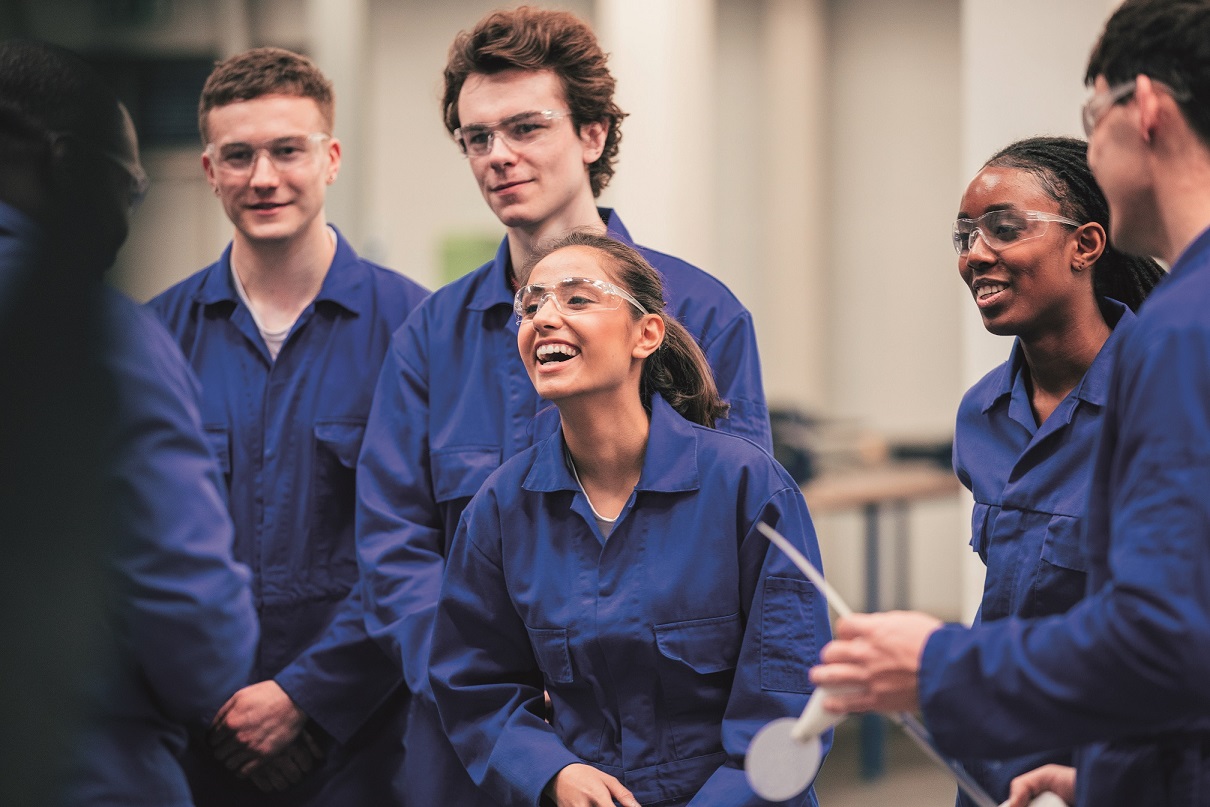
Heidelberg Materials strengthens CCUS work by signing Leilac global licence agreement
As part of the continued expansion of its broad portfolio of CCUS technologies, Heidelberg Materials has signed an indefinite global licence agreement with the technology company Leilac, a Calix subsidiary.
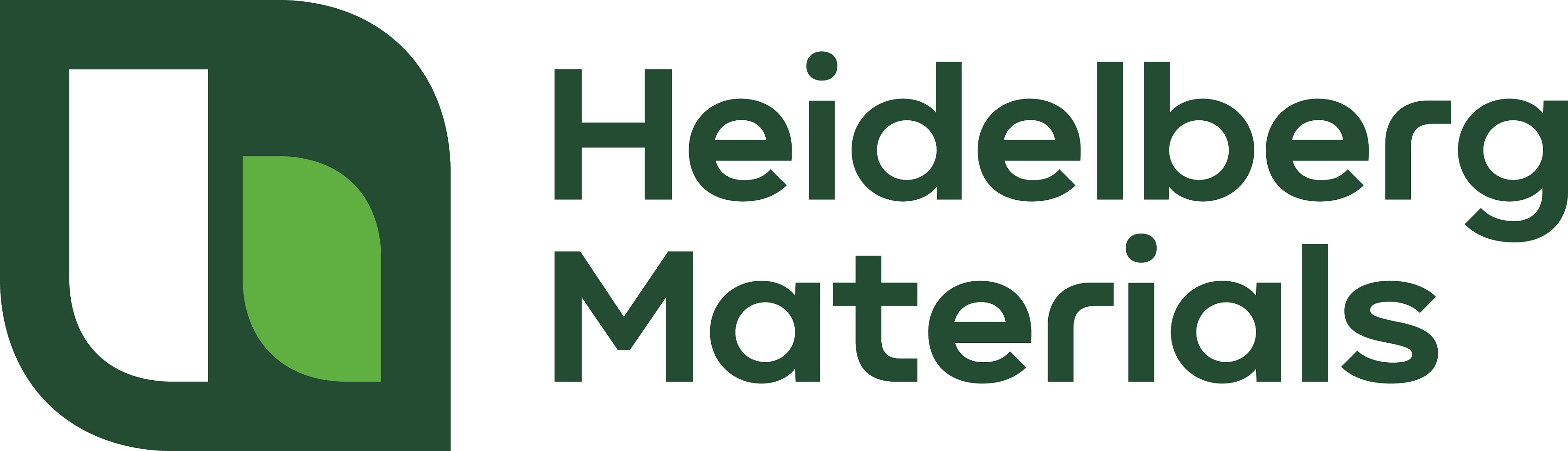
Excon defies bad weather to deliver for Indian customers
An extreme weather-hit Excon exhibition saw major off-highway original equipment manufacturers (OEMs) showcase their new and latest models for Indian customers, with a firm emphasis on reducing job-site operating costs
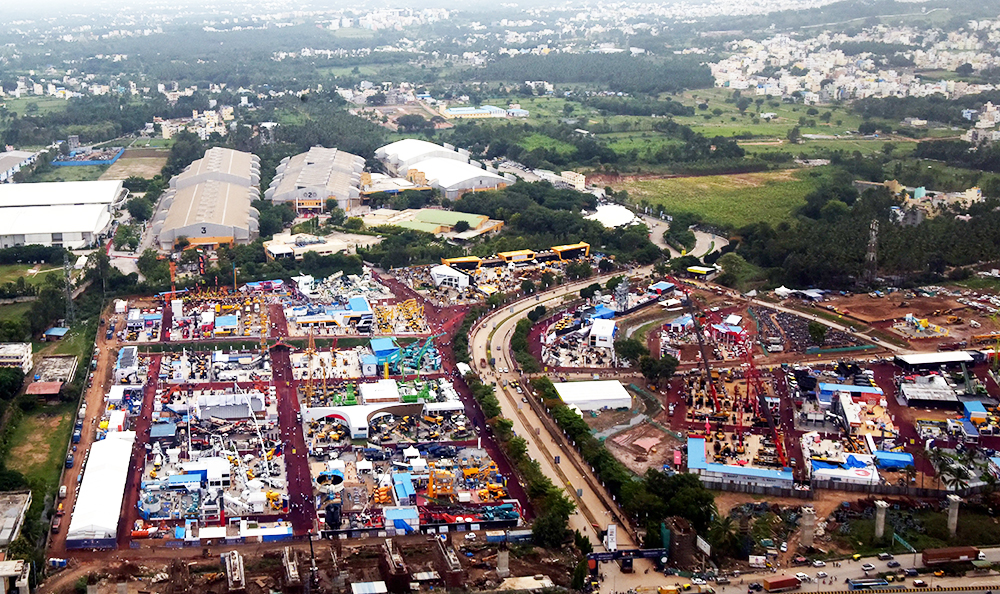
John Deere ploughs significant resources into electric future
To demonstrate strides made toward low- and near-zero carbon propulsion systems, the company is showcasing a suite of electric systems, including batteries, drives and converters.
A key talking point, explained Collin Krantz, John Deere Power Systems’ OEM implementation manager, is the Kreisel Battery Pack 63 (KBP63), which utilises Kreisel Electric’s patented immersion cooling technology for efficient thermal management.
This ensures that all cells are stressed equally, prolonging battery life while meeting high safety standards. The technology offers a low temperature spread of <1°C throughout the module, thus increasing service life and reliability.
“The modules in the battery pack are interchangeable, allowing the battery to serve multiple applications with just one platform solution,” said Krantz. “The same module is adaptable for use in the automotive and commercial vehicle, off-highway, transportation and marine markets. It can be connected in parallel as well as in series (400V or 800V). This offers high flexibility in combination with different possible installation positions.”
In addition, the company is showcasing a series of inverters based on a modular concept that supports single or dual configurations with a variety of other hardware options. The high-voltage, high-power, liquid-cooled modules are designed to work at maximum efficiency with complete monitoring capabilities.
The common control architecture enables advanced software features for control under all conditions and supports a variety of different motor types.
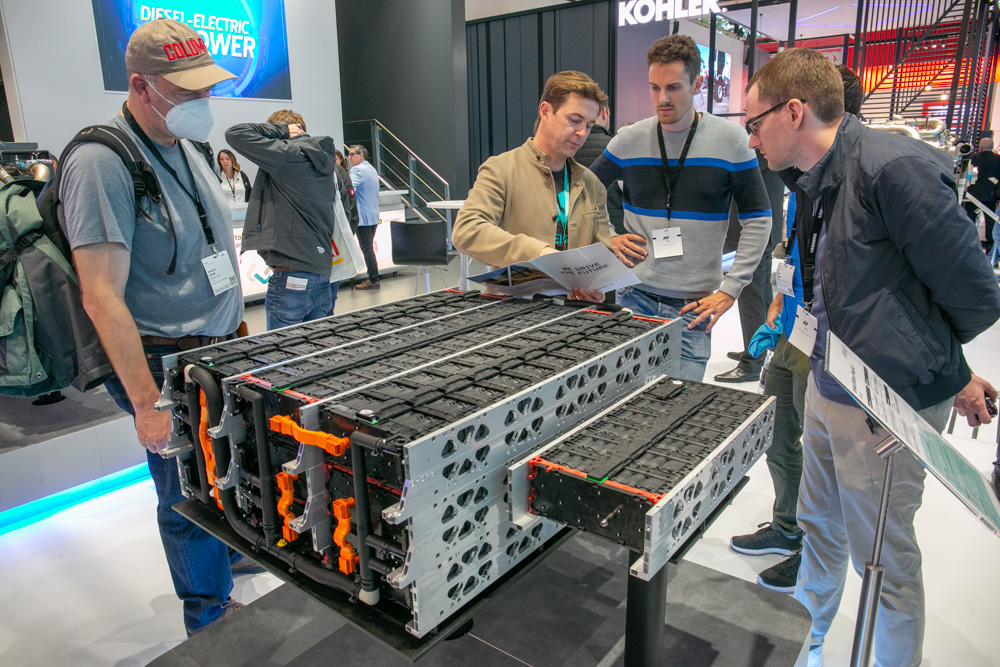
Kohler gears up for sustainable power growth in 150th year
The company has set out its new strategy toward a more sustainable future, revealing its long-term plan and next steps to transform the group from a power producer to an energy supplier.
The company says the unveiling of this new strategy comes at a momentous time for the engine industry.
Kohler’s strategy incorporates alternative fuels, electrification and hybridisation to reduce engine size or achieve zero emissions during operation, together with introducing hydrogen as a potential ‘green’ fuel.
The manufacturer recently acquired electric vehicle and hybrid applications company Curtis. Kohler says the acquisition expands and diversifies its product portfolio, leveraging Curtis’ expertise in electrification, and solidifying Kohler’s commitment to hybrid and electrified solutions.
Kohler’s road map toward electrification has 2025 as its first goal. The company says its vision is to develop sustainable and technically sound EV system solutions to increase the performance of internal combustion engines by placing full electric solutions alongside them.
Kohler is updating its K-HEM series hybrid unit for the combined electric and mechanical power solution. The range will move from the booster hybrid version, Kohler’s first hybrid alternative solution design that solves the problem of onerous after-treatment for intermittent cycles, to the versatile-hybrid version, which enables electric-only operation.
The new P2 option achieves zero-emissions through full-electric operation while keeping the diesel engine ready to step in to add mechanical power when needed or to recharge the battery.
The new hybrid option will be featured in CELA’s new application, the DT40, a ‘spider’ aerial platform with an electric track. The DT40 is already geared to be an electric machine, in that if the battery is fully charged, crawling can be done in electric. Arm movements can also be done in electric, as the hydraulic pump is assembled on the electric machine and the latter can function as either a generator or a motor.
Another cornerstone of Kohler’s strategy is the KSD engine, which has won both the Engine of the Year award from Diesel and the Engine of the Year under 175 hp award at the Diesel Progress Summit. The KSD is in the under-19kW category and features an electronically controlled indirect injection combustion system, as opposed to the standard mechanical indirect injection in this category.
Kohler says this offers advantages such as high low-end torque – 95Nm at 1000rpm for TC/TCA – and better performance at altitude. The KSD enables a low total cost of ownership due to its optimised fuel consumption, extended service intervals and simplified routine maintenance that requires only two tools.
Vincenzo Perrone, president of Kohler Engines, commented, “Kohler sees the future as a multi-energy landscape, with multiple technological solutions to meet future customer needs and requirements. We will continue to invest in engines and expand their production. We will improve engine efficiency, even in the smallest HP, and develop electronic controls on small engines.
“We will pursue the development of hydrogen solutions that have the same performance as diesel units, as well as natural gas and biogas engines. We will continue to bring to market hybrid modules.
“In summary, we are investing in a diversified energy future, in which a wide range of power options and multiple technologies will coexist for many years."
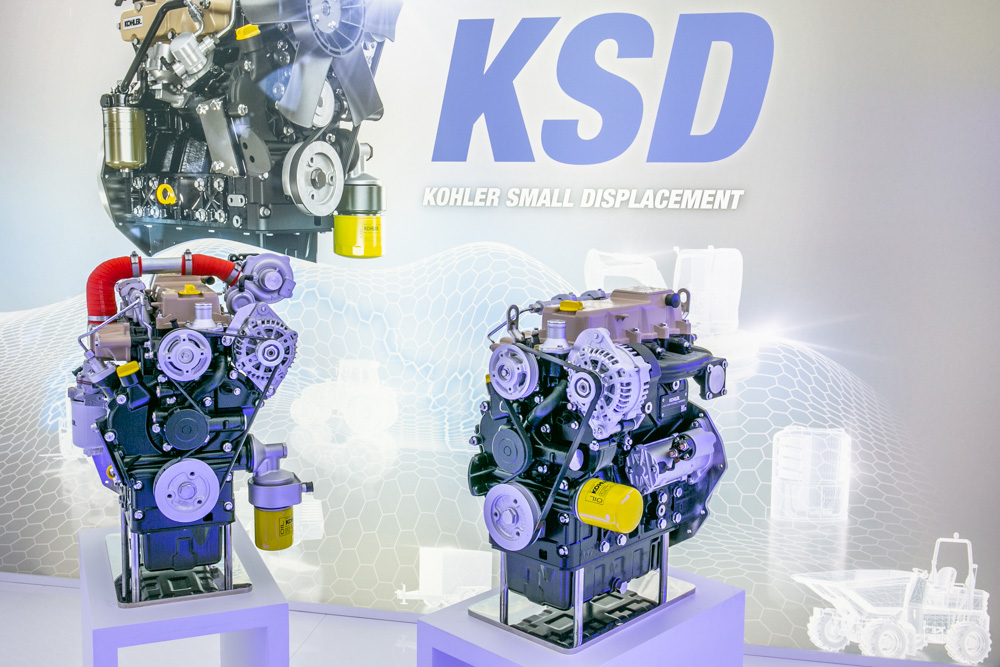
Electric concrete slipformer revolution from GOMACO
Keogh said that the battery will power the machine for eight hours when laying kerb in a straight line, although he added that this may drop to around six hours when working around curves due to the extra power needed for the steering system. Recharging the 48V DC lithium-ion battery pack takes around 8-10 hours from a conventional 220V supply, although a two-hour fast charger is an optional feature.
The first unit has been equipped with a Topcon machine control package, although Keogh said that customers can order technology from Leica Geosystems or Trimble if they prefer. He said that that the 3D machine control system is just for steering, as the level of the kerb being laid follows the level of the road.
The machine is operated using a radio remote control unit that features GOMACO’s proven G+ control system. Features include rotary-sensored slew drive steering on the front assembly for tight turning, smooth paving and ease of control.
The machine can pour a 610mm radius, has a paving speed of up to 12.2m/min and an auxiliary speed of 28.3m/min for site mobility. Different mold configurations are offered, allowing a 305mm wide by 356mm high section. The mold can be mounted on either side of the machine, while the hopper and mold are adjustable up to 381mm.
Leg elevation is controlled by three hydraulic cylinders, each with a stroke of 254mm as well as an additional 127mm of manual adjustment.
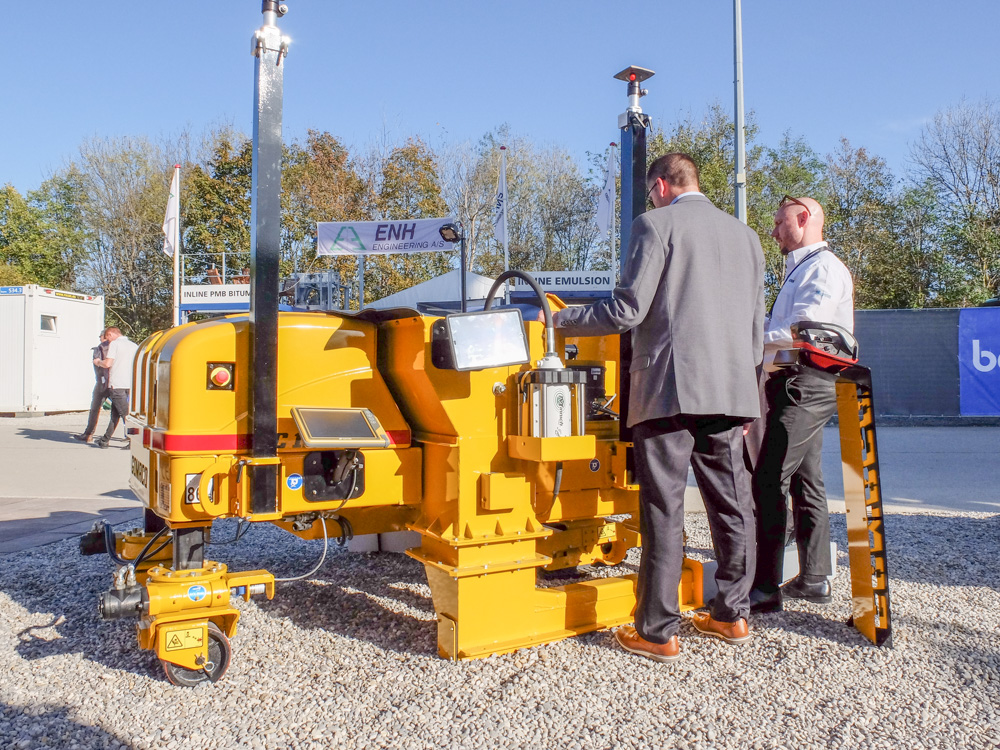
New tracked and wheeled asphalt pavers from Sumitomo
Power for the HA60 machines comes from a Yanmar diesel rated at 110kW, an increase from the 92kW of the Isuzu engine in the previous generation machines. The machines also benefit from sophisticated technology developed by Sumitomo, ensuring high work efficiency and low fuel consumption, while meeting the Stage V emission standards through the use of a selective catalytic reduction (SCR) system.
The improved heating system features flat-type heating plates. “We modified the design of the heating elements to increase efficiency,” said a spokesperson for the firm. “Before we used a round type, but now we use a flat-type heating element and you get more contact with the ground.” Heating times are also said to be around 50% quicker than before due to the new elements.
In addition, the heating generator has been changed from a belt drive to a direct motor drive, eliminating the need for daily belt adjustments.
Sumitomo’s innovative STV compaction system (strike-off, tamper, vibration) is said to ensure a high-quality, smooth surface. An automatic tamper speed setting function is now available on the DASH 11 generation machines. The machine retains the proven, novel screed design, which features overlapping hydraulic cylinders and allows wider extension than other machines in its size class. However, the firm says that the rigidity of the screed has been increased to make it stiffer and further boost paving quality. Both the wheeled and tracked variants offer screed widths from 2.3-6m using the hydraulic extension, although bolt-on extensions can be used if a wider setting is required.
The wheeled model now has a slightly shorter hopper, which helps manoeuvrability in tight locations, as well as allowing the machine to be loaded on a truck along with a small twin-drum roller for easy transport. Hopper capacity for the wheeled machine is 12tonnes, compared with 13tonnes for the tracked model.
Crew comfort levels have been improved and the new FRP canopy is raised and lowered hydraulically, while there are also side windshields to provide operator protection in bad weather, as well as LED lighting for night working. Site safety is improved by the installation of a field view monitor (FVM) package that allows the operator to see around the machine.
A new differential lock option helps to ensure traction when working on soft ground, while the brake steer system that was an option on the previous wheeled model is now a standard feature.
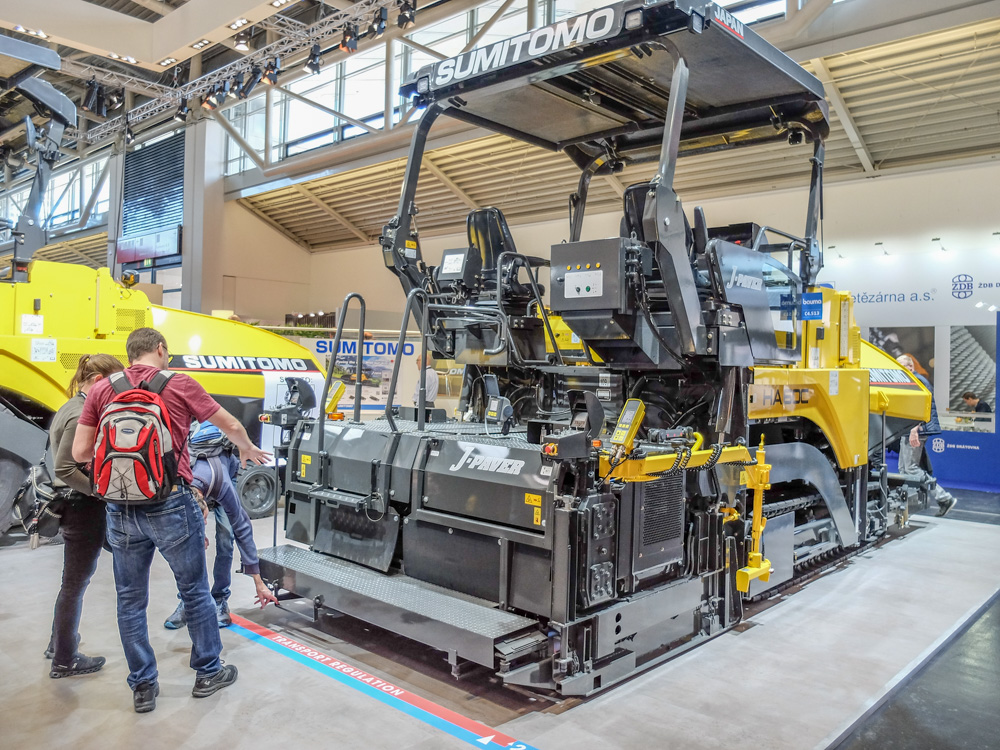
Holcim posts record Q3 trading figures
Building materials giant Holcim has posted new record Q3 sales of CHF 8.045bn (+16.3% like-for-like [LFL] -€8.115bn). The Switzerland-headquartered group also achieved its biggest-ever Q3 recurring EBIT of CHF 1.551m (+7.7% LFL - €1.564bn).
Based on the record-breaking third-quarter performance, Holcim's 2022 outlook has been upgraded to full-year net sales growth of at least 12% (LFL), with recurring EBIT forecast at mid-single digit growth (LFL).
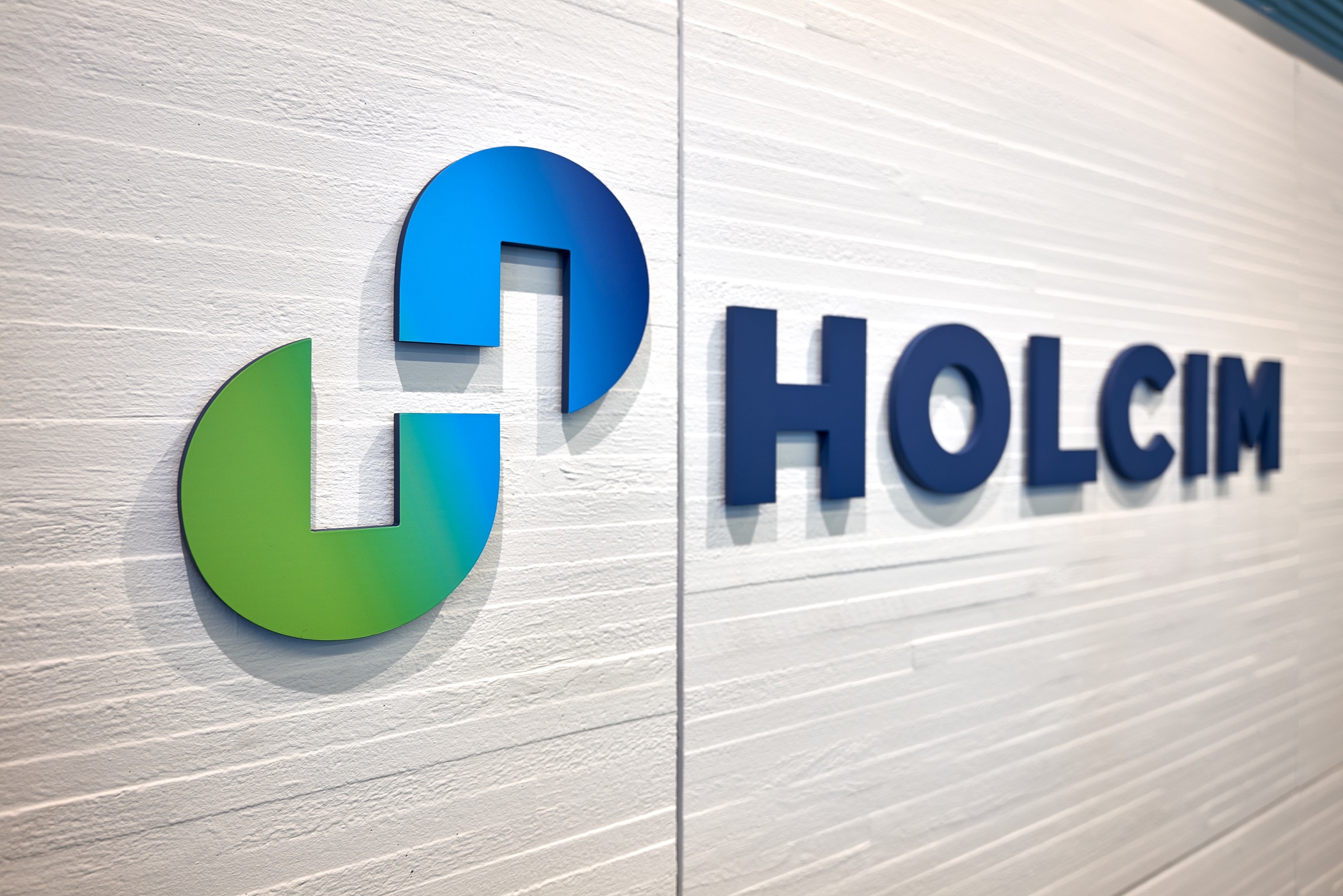
One of world's largest white cement makers shares strategies for cutting clinker & fossil fuel at CarbonZero 2022
Over 80% of the cement operation's carbon emissions are released during clinker production. 2030 is a crucial benchmark for the carbon neutrality journey: reducing the CO2 footprint while producing enough cement to meet demand will be challenging. Also, substituting fossil fuel with carbon-neutral fuel is the key to achieving the 2030 and 2050 targets.
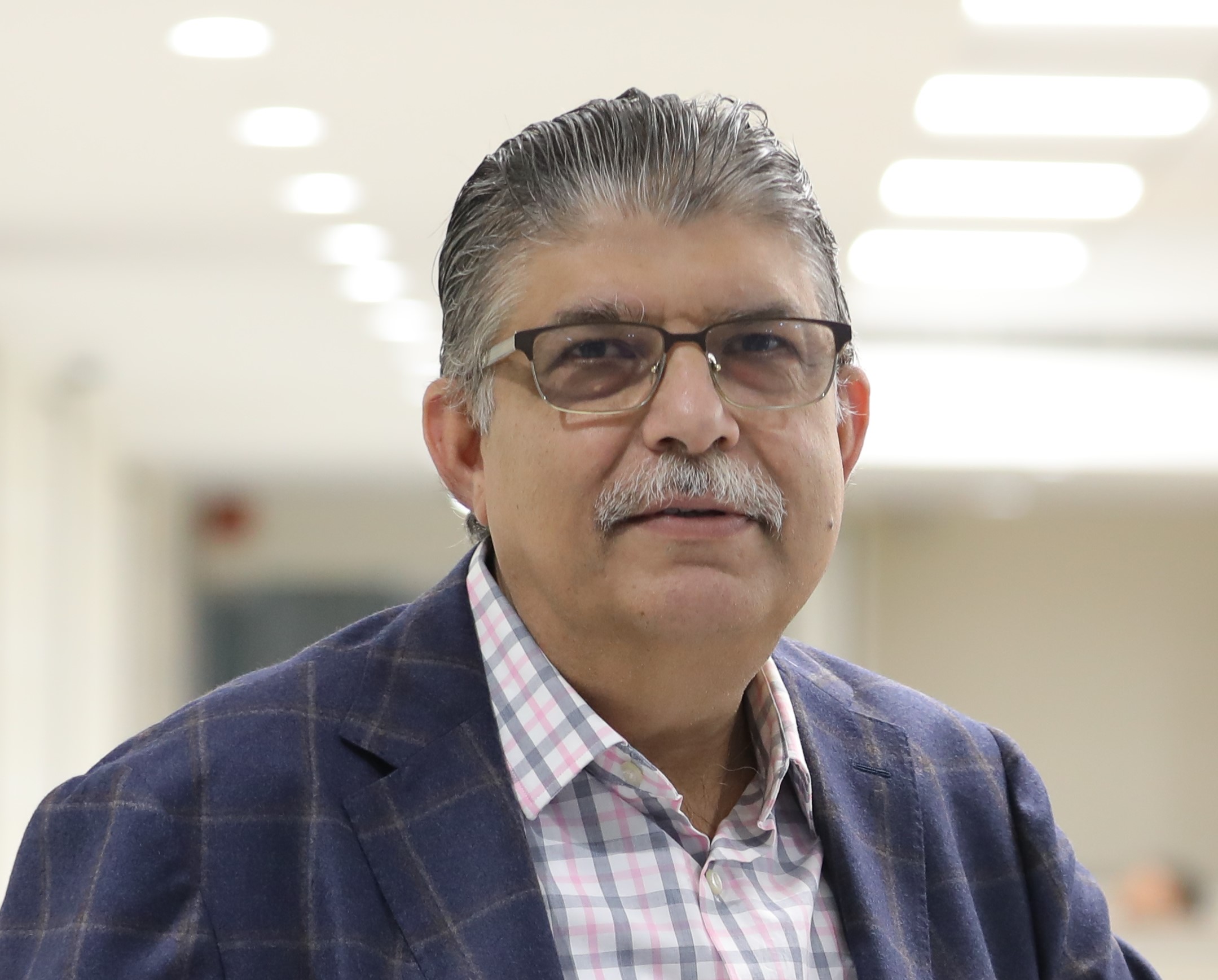
CEMEX supplies Vertua cement for bridge in Croatia
CEMEX has supplied 37,000 tonnes of cement for constructing the Pelješac Bridge, one of Croatia's most significant infrastructure projects in the past three decades. Nearly all the cement used in the project belonged to CEMEX's Vertua family of lower-carbon products.
The Pelješac Bridge spans a total of 2.4 kilometres and is an integral part of Croatia's transport system, connecting the southern region of Croatia with the rest of the country. For decades, crossing Croatia's territories by land required crossing its border with Bosnia and Herzegovina.
Matec presents ‘Twin Freccia Rossa’ prototype of world’s biggest filter press
The first full-production, 50m-long, up to 380-plate and 600 t/h machine is set to be snapped up by a Turkish iron ore mining customer. The Italian company says its innovative machine combines the efficiency of two machines into a single product with exceptional performance, offering faster sludge feeding and cake discharge time.
The patented ‘Twin Freccia Rossa’ is said to reduce customers’ operating costs and allows production to continue during maintenance times. Featuring a single conveyor belt, feeding point, silo decanter, supporting structure, homogeniser tank, high-pressure 10-16-21-30-bar technology, a protective shell for the oleodynamic unit and piston, and four-point cloth washing, the cutting-edge filter press can be equipped with 25 to 50mm standard or membrane plates.
“All our customers are asking us for two filter presses in one machine,” said Matec Industries CEO, Matteo Goich. “We started work on Twin Freccia Rossa around a year ago and the customer who will operate the first full-sized version of this new filter press already has one of our washing plants and six of our filter presses.”
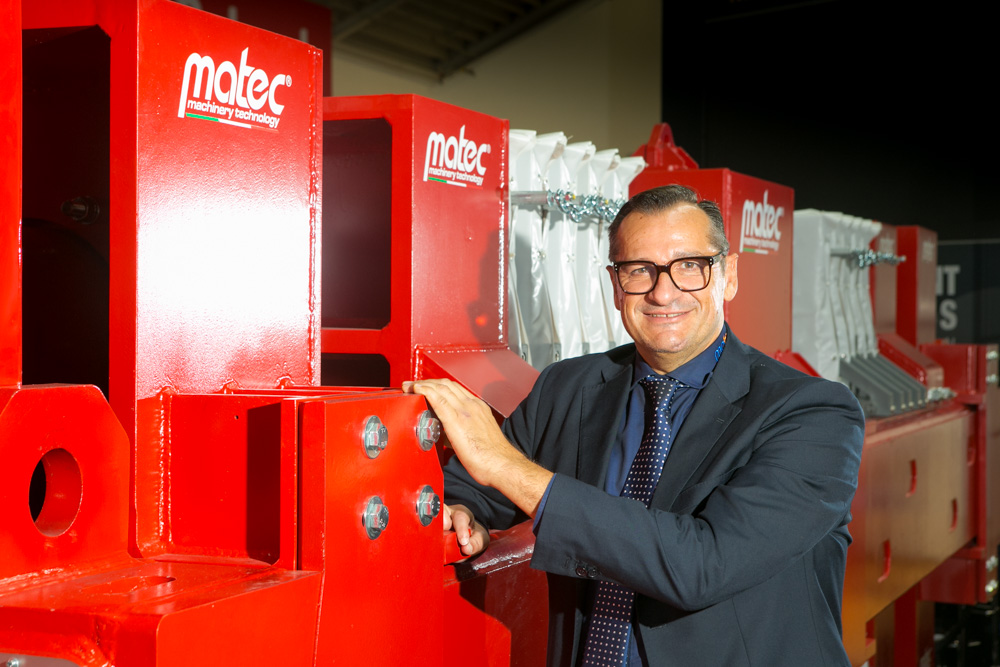
CIFA unveils fully automated shotcrete pump for underground construction
This is made possible by the inclusion of a laser scanning device on the machine, which allows the operator to take measurements of the tunnel before and after application, thus providing data about the average thickness of the layer of sprayed concrete being applied.
Davide Cipolla, CIFA’s CEO, explained that the new underground range is inspired by nature, which is why the models are named after animals with similar physical or behavioural characteristics. ‘Inspired by nature’, he says, refers to more than just the names of machines, it also describes the company’s goals and aspirations when designing the range.
“We aim to make these CIFA machines as eco-friendly as possible, respectful of the environment and people, and able to transform the notoriously unhealthy underground construction site into a sustainable eco-system,” he said.
Manufacturers of tunnelling machinery, he added, need to work together to create a sustainable construction site in what is a challenging environment – an enclosed space with poor ventilation.
“We need to design intelligent machines, harnessing data to increase efficiency, using electricity to cut emissions and technology to simplify the work of operators.
“The first step towards a sustainable business model is to create intelligent machines, designed to optimise the consumption of resources. This forms part of a holistic approach that examines the overall impact of every operation, and not just the performance of the individual machine.
All the data collected by Mamba can be used in the future to determine where to spray concrete and how much to apply at a time, creating a digital model of the tunnel in line with the Building Information Modelling (BIM) method.
In addition to Mamba, the range consists of several other shotcrete models (Elk, Dingo, Rhino and Mantis) and concrete mixers (Coguaro and Myria), in varying sizes and with different features in line with their applications. All the models can be customised to meet the needs of particular projects.
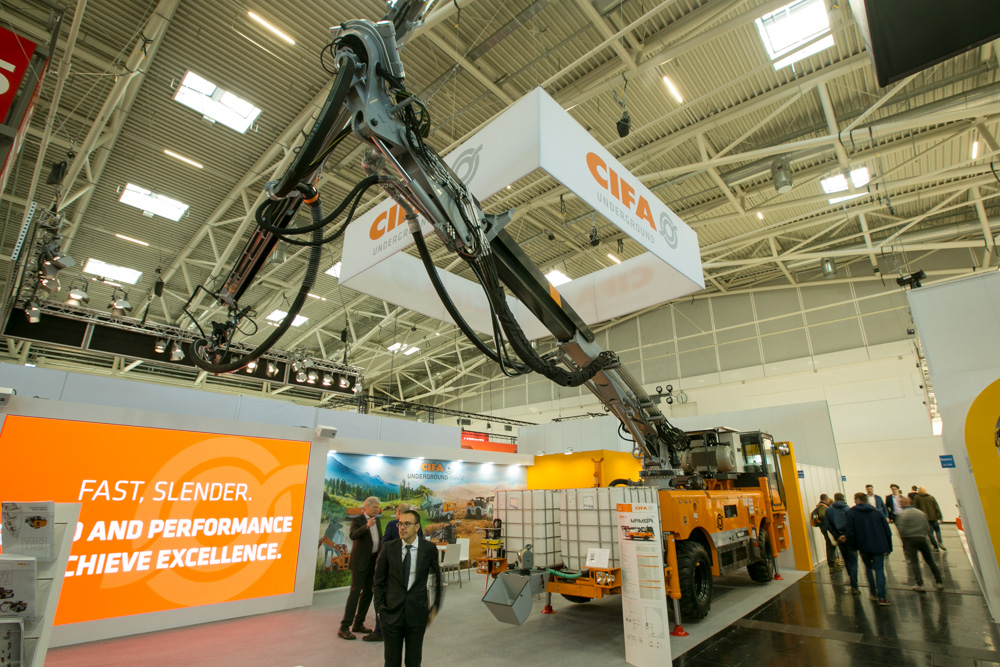
Piling rig control system from Trimble
The Trimble Groundworks package is a 3D machine control system said to improve efficiency and reduce downtime with stakeless navigation, productivity and quality monitoring, and office-to-field connectivity.
The integration of Trimble software in the office and Trimble Groundworks in the field can increase the efficiency and productivity of piling operations, wirelessly syncing data to reduce site visits and provide a single data source.
Trimble Groundworks allows operators to create an in-field design for piling and create piling reports. To reduce blind spots, administrators can set avoidance zones in the design file. With stakeless workflows, Trimble Groundworks is said to reduce the need for surveyors to be near the machine, making job sites safer.
For an ABI Mobilram-System or DELMAG drill rig, the option to install a Trimble Groundworks base kit provides mounting hardware, brackets and an integrated wiring harness. Having the system installed in the factory can reduce cost and complexity for the customer.
"Trimble enables our customers to map the entire construction process from planning to quality management. On construction sites, for example, the pile grid does not have to be measured in place," said Tobias Schmidt, head of control engineering electrics at ABI.
"A significant advantage of the Trimble Ready solution is the direct communication with the ABI control system, so that the sensor technology available on the machines can be integrated. The necessary mounting options on the machine are already prepared. This significantly reduces the costs required to equip a system from Trimble."
For the Junttan piling equipment, the technology is said to allow more efficient and safer working, along with stakeless workflows and 3D machine control. The system helps optimise productivity by allowing operations during the day or night. The 2D or 3D guidance technology allows accurate piling depth and direction, reducing driving time for each pile, cutting fuel consumption.
"Junttan strongly believes in the benefits of digitalisation in the piling construction field," said Karoliina Pesola, head of digital and measuring solutions, Junttan. "Trimble Groundworks connected to Junttan's machine control system PCD will provide a new dimension to our customers' piling experience."
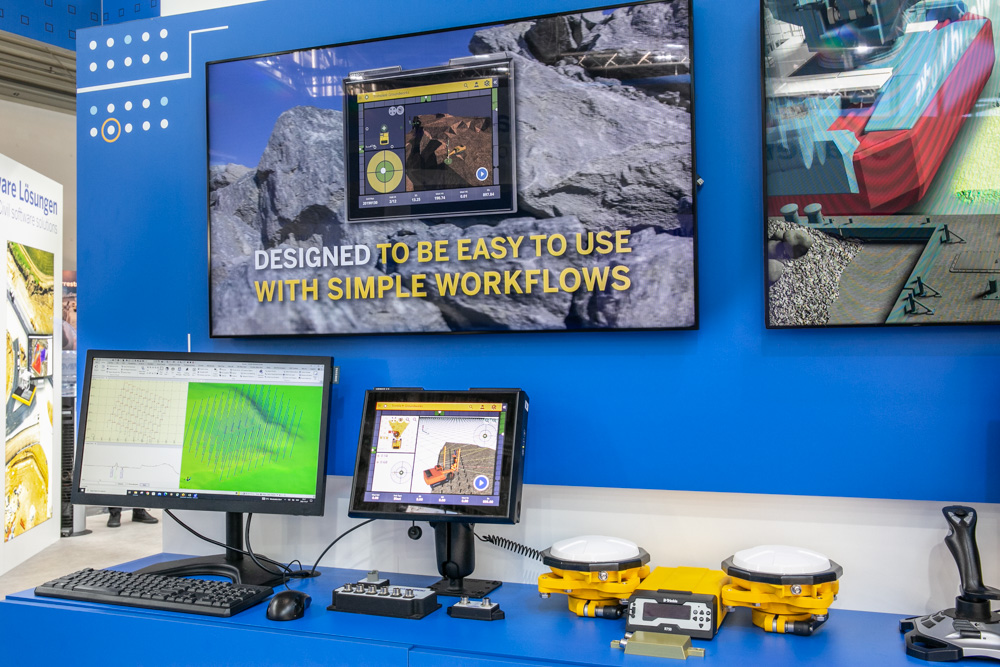
MB Crusher launches the mid-sized MB-HDS220 shafts screener bucket
The Italy-based manufacturer says the bucket is suitable for use with loaders and excavators for groundworks and agricultural applications.
Alessia Valerio, responsible for product growth & content at MB Crusher, said that the MB-HDS220 fills a gap in its MB-HDS shafts screener range, bringing the product line-up to six sizes.
The MB-HDS523 bucket, the biggest in the range, is suitable for quarrying applications.
Valerio said the company is seeing a lot of demand for its smaller buckets in Italy and the rest of Europe, while many customers in Asia and the US are moving towards the larger models.
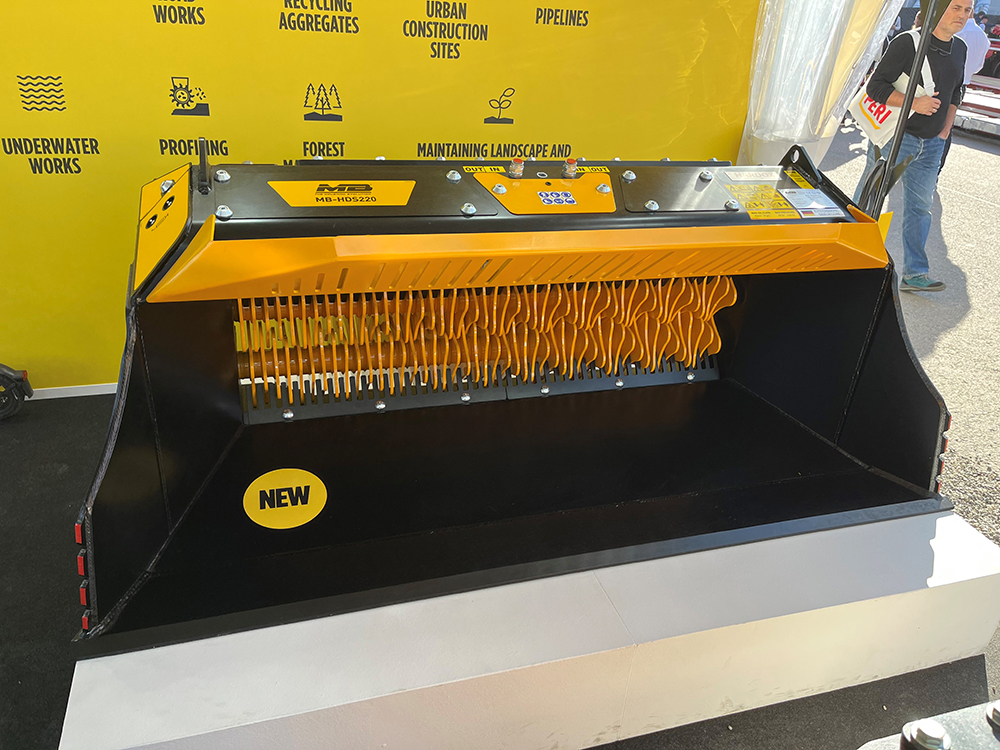